Article
Adding By Subtraction: The Power Of Thinking And Working Lean
November 27, 2019
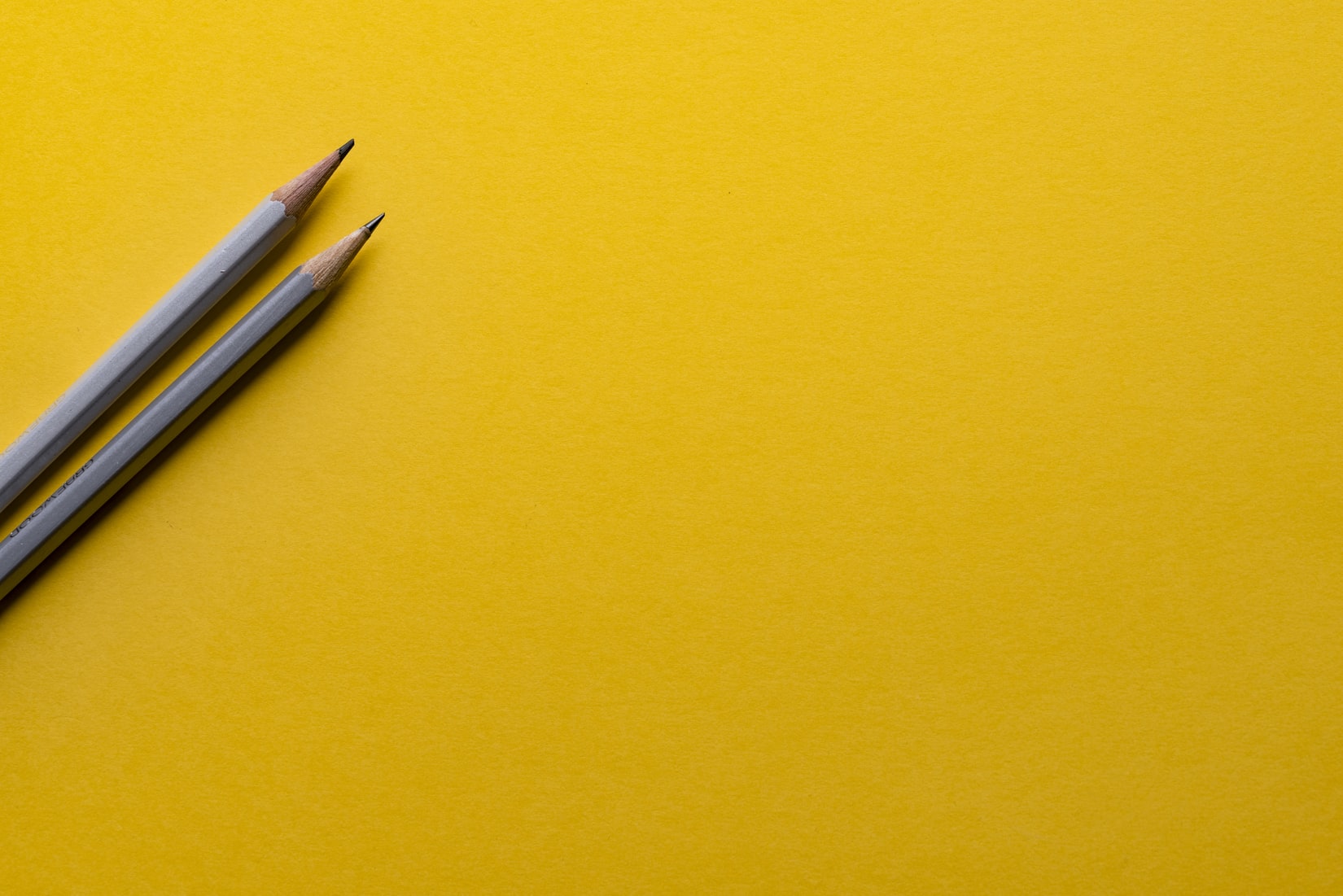
What would you do for the opportunity to describe your life and business in the following ways:
- An incredible life - check
- A life where things work - check
- A life where you have great days almost every day - check
- A life where everything just keeps getting better and better - check
- A life that feels like heaven on earth - check
If any or all of those prospects sound good to you, you just might be ready to join Paul Akers’ Lean revolution. The concept behind Lean working and thinking isn’t new, and seems breathtakingly simple on the surface.
But as Paul explains, getting to Lean takes ongoing effort, commitment, and discipline to create and sustain the systems and processes you’ll need to keep it simple - in life as well as in business.
Subscribe to Process Makes Perfect for free on: Apple Podcasts | Spotify | Google Podcasts
The most annoying phrase in the English language
This one may be up for interpretation depending on who you ask, but if you’re a process and systems oriented person in business (as well as in life), no response is more grating and demoralizing than “this is the way we’ve always done things.” But as Paul explains, changing the way things are done to make them simpler will ultimately pay exponential dividends down the line that will spill over into all areas of your company and personal life.
What is lean thinking and how do you get there?
Simply put, lean thinking and working at its core is about implementing good processes where none exist, or overhauling bad ones to tackle the chaos and complexity that most people deal with on some level in life in general and business in particular. The concept of Lean culture introduces the beauty of simplifying how we do things on a daily basis, so that we have more time and things run more efficiently.
The key according to Paul is to start small, and get in the habit of working on it every day. Lean living and working basically boils down to recognizing the things that bug you, and setting out to fix them every day.
To get started, become one with the three s’s:
Sweep - clean out the top drawer, hang the hand towels closer to the sink, put the batteries and tools where they belong. Whatever sweeping looks like for you, this is where you identify what’s bugging you, what’s out of sorts, and what’s costing you time and money
Sort - this is where you organize and set the wheels in motion for the third s
Standardize - this is the process that you will adopt and repeat every day to transform your life and business from a cycle of raging five alarm fires, to a purring kitten in your lap or a soft summer breeze ruffling through your hair as you swing on a hammock on a summer afternoon (or whatever ease, efficiency, and joy personally looks like for you)
Additionally, Paul has outlined eight deadly sins or “areas of waste” that lower productivity and cripple many companies and their employees with inefficiencies:
- Over-production
- Over-processing
- Excess inventory
- Defects
- Transportation
- Wasted motion
- Waiting time
- Unused employee genius
Identify the problem and find the solution
As we’ve already learned, the best processes are constantly evolving and changing to keep up with an organization’s needs. Paul’s company holds a daily morning meaning where a good hour to 90 minutes are allocated to the “how” - a roadmap for how the team will approach the day’s work in order to get a handle on it before it begins.
The result? A seamless, productive, and efficient work day where the hours just seem to fly and the work is completed effortlessly. Instead of hiring people to “do” or “make” specific things, hire people that will improve the way you do things.
According to Paul,” a lean company has incentives built in because the efficiency creates the resources that are necessary to compensate people well and create a positive environment. Because our company is so lean, we can afford to pay people more, it’s an awesome environment, you’re working in a place where you never struggle, everyone values your creativity, you’re allowed to express yourself - the rewards are there and they’re automatic.”
By focusing on and highlighting the benefits of cutting waste and implementing lean thinking and workflows as an ongoing process, Paul helps other business owners and people from all walks of life adopt the Lean living ethos as a matter of course. Think of it as the antidote to procrastination - the more you do now, the less you’ll have to do later.
Lean thinking is not just a business formula; it’s a culture and way of life. By taking time to examine and simplify your processes so that they can be executed in fewer steps, you’ll ultimately add more time - and hopefully joy - to your work and life.
Similar Blog Posts
Article
Adding By Subtraction: The Power Of Thinking And Working Lean
November 27, 2019
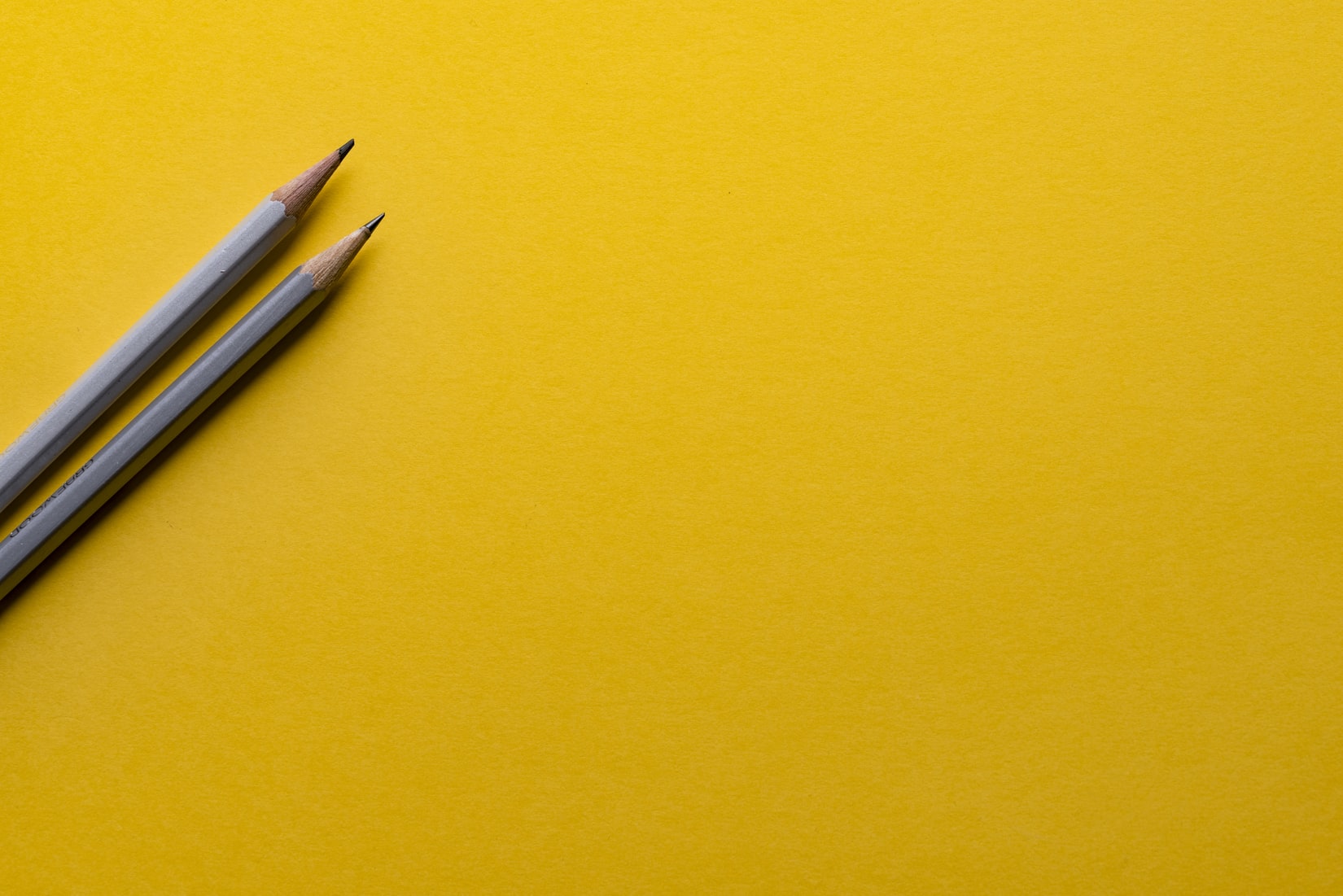
What would you do for the opportunity to describe your life and business in the following ways:
- An incredible life - check
- A life where things work - check
- A life where you have great days almost every day - check
- A life where everything just keeps getting better and better - check
- A life that feels like heaven on earth - check
If any or all of those prospects sound good to you, you just might be ready to join Paul Akers’ Lean revolution. The concept behind Lean working and thinking isn’t new, and seems breathtakingly simple on the surface.
But as Paul explains, getting to Lean takes ongoing effort, commitment, and discipline to create and sustain the systems and processes you’ll need to keep it simple - in life as well as in business.
Subscribe to Process Makes Perfect for free on: Apple Podcasts | Spotify | Google Podcasts
The most annoying phrase in the English language
This one may be up for interpretation depending on who you ask, but if you’re a process and systems oriented person in business (as well as in life), no response is more grating and demoralizing than “this is the way we’ve always done things.” But as Paul explains, changing the way things are done to make them simpler will ultimately pay exponential dividends down the line that will spill over into all areas of your company and personal life.
What is lean thinking and how do you get there?
Simply put, lean thinking and working at its core is about implementing good processes where none exist, or overhauling bad ones to tackle the chaos and complexity that most people deal with on some level in life in general and business in particular. The concept of Lean culture introduces the beauty of simplifying how we do things on a daily basis, so that we have more time and things run more efficiently.
The key according to Paul is to start small, and get in the habit of working on it every day. Lean living and working basically boils down to recognizing the things that bug you, and setting out to fix them every day.
To get started, become one with the three s’s:
Sweep - clean out the top drawer, hang the hand towels closer to the sink, put the batteries and tools where they belong. Whatever sweeping looks like for you, this is where you identify what’s bugging you, what’s out of sorts, and what’s costing you time and money
Sort - this is where you organize and set the wheels in motion for the third s
Standardize - this is the process that you will adopt and repeat every day to transform your life and business from a cycle of raging five alarm fires, to a purring kitten in your lap or a soft summer breeze ruffling through your hair as you swing on a hammock on a summer afternoon (or whatever ease, efficiency, and joy personally looks like for you)
Additionally, Paul has outlined eight deadly sins or “areas of waste” that lower productivity and cripple many companies and their employees with inefficiencies:
- Over-production
- Over-processing
- Excess inventory
- Defects
- Transportation
- Wasted motion
- Waiting time
- Unused employee genius
Identify the problem and find the solution
As we’ve already learned, the best processes are constantly evolving and changing to keep up with an organization’s needs. Paul’s company holds a daily morning meaning where a good hour to 90 minutes are allocated to the “how” - a roadmap for how the team will approach the day’s work in order to get a handle on it before it begins.
The result? A seamless, productive, and efficient work day where the hours just seem to fly and the work is completed effortlessly. Instead of hiring people to “do” or “make” specific things, hire people that will improve the way you do things.
According to Paul,” a lean company has incentives built in because the efficiency creates the resources that are necessary to compensate people well and create a positive environment. Because our company is so lean, we can afford to pay people more, it’s an awesome environment, you’re working in a place where you never struggle, everyone values your creativity, you’re allowed to express yourself - the rewards are there and they’re automatic.”
By focusing on and highlighting the benefits of cutting waste and implementing lean thinking and workflows as an ongoing process, Paul helps other business owners and people from all walks of life adopt the Lean living ethos as a matter of course. Think of it as the antidote to procrastination - the more you do now, the less you’ll have to do later.
Lean thinking is not just a business formula; it’s a culture and way of life. By taking time to examine and simplify your processes so that they can be executed in fewer steps, you’ll ultimately add more time - and hopefully joy - to your work and life.
Article
Adding By Subtraction: The Power Of Thinking And Working Lean
November 27, 2019
•
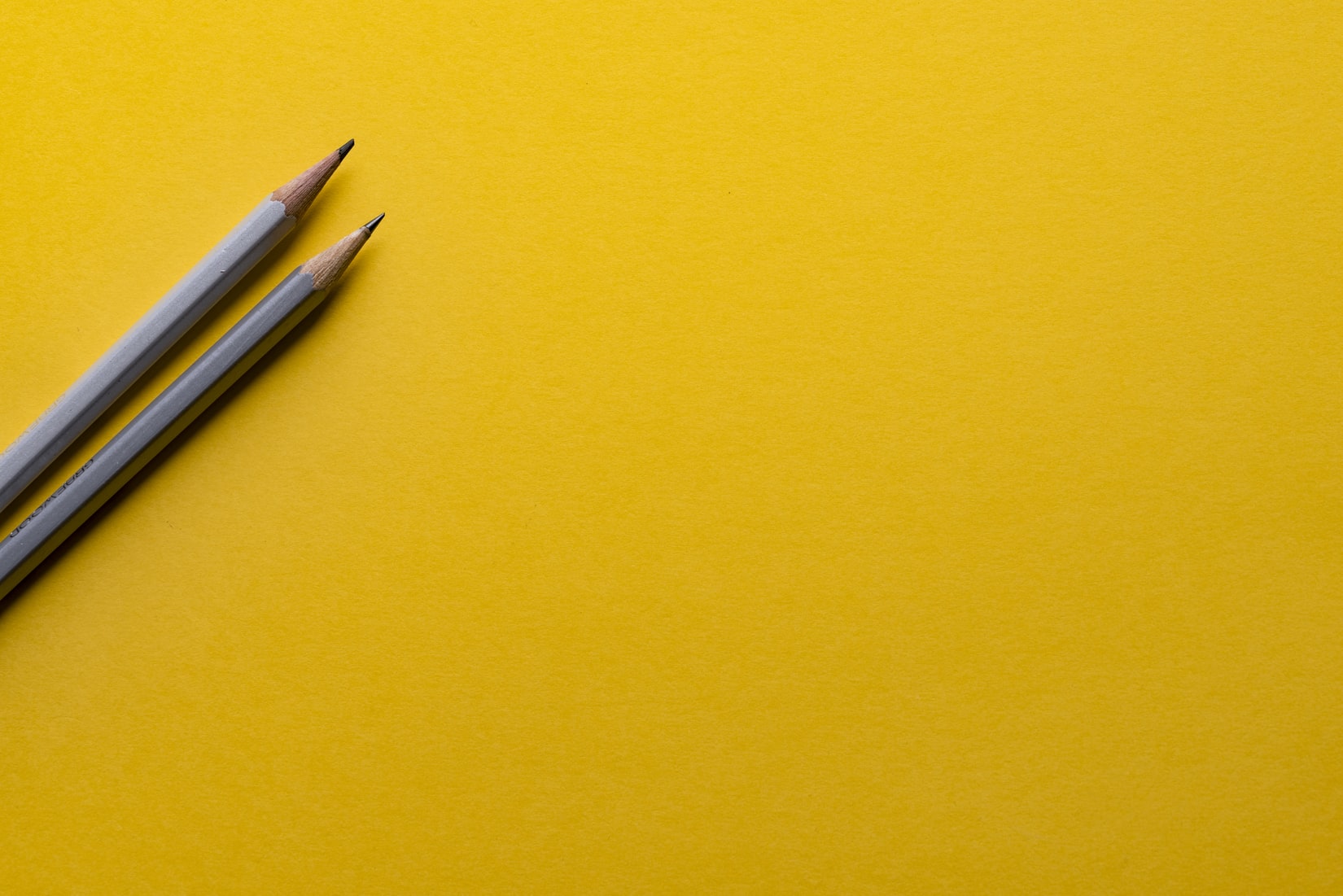