Article
Understanding Total Quality Management for Improved Business Performance
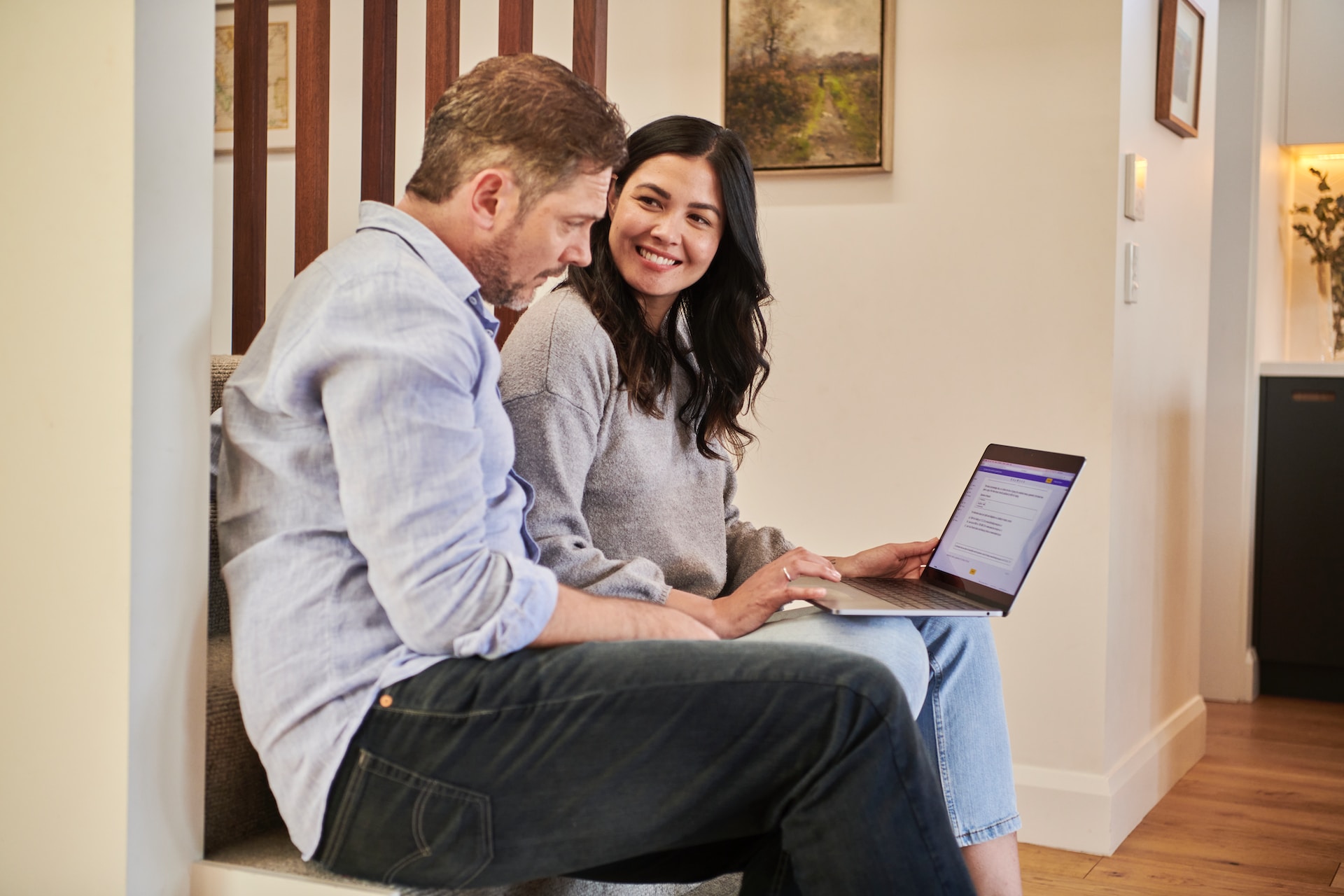
In today's highly competitive market, the success of a business hinges on its ability to deliver quality products and services consistently. This is where Total Quality Management (TQM) comes in. TQM is a management philosophy and approach designed to improve an organization's processes and systems to achieve higher levels of performance. In this article, we'll take a closer look at TQM and how it can help improve your business performance.
The Origins and Evolution of Total Quality Management
Total Quality Management (TQM) has come a long way since its inception in the late 19th and early 20th centuries. TQM was initially developed to identify and correct defects in products, but as manufacturing processes became more complex, new methods were needed to ensure quality and consistency across the entire organization.
Today, TQM is a comprehensive approach to quality management that involves all employees in the organization, from top management to frontline workers. It is a continuous improvement process that aims to meet or exceed customer expectations while reducing costs and increasing efficiency.
Early Quality Control Methods
The first quality control methods were developed in the manufacturing industry and focused on detecting and correcting defects in products through inspection and testing. However, this approach was reactive and did not address the root causes of defects.
In the 1920s, Walter Shewhart introduced the concept of statistical process control (SPC), which involved using statistical tools to monitor the quality of production processes and detect any variations or defects that might occur. This was a major step toward the development of TQM.
SPC enabled manufacturers to identify the root causes of defects and make changes to the production process to prevent them from occurring in the future. This approach was proactive and helped to improve the quality of products and reduce costs.
The Birth of Total Quality Management
The term Total Quality Management was first coined by Armand Feigenbaum in the 1950s. Feigenbaum emphasized the importance of quality at every stage of the production process, from design and development to delivery and after-sales support.
TQM was further developed in the 1970s and 1980s by quality gurus such as W. Edwards Deming, Joseph Juran, and Philip Crosby. These thought leaders emphasized the importance of customer satisfaction, continuous improvement, and employee involvement in the quality improvement process.
Key Contributors to TQM Development
Deming, Juran, and Crosby are considered the three pillars of TQM. Deming, an American statistician, emphasized the importance of continuous improvement and the involvement of every employee in the quality improvement process.
Juran, a Romanian engineer, introduced the concept of quality planning and emphasized the importance of data analysis and process improvement. He believed that quality should be built into the product or service from the beginning, rather than inspected out at the end.
Crosby, an American quality expert, introduced the concept of "zero defects" and emphasized the importance of prevention rather than detection of defects. He believed that quality should be the responsibility of every employee in the organization, not just the quality control department.
Together, these quality gurus helped to shape the modern approach to TQM, which emphasizes continuous improvement, customer satisfaction, and employee involvement in the quality improvement process.
Core Principles of Total Quality Management
Total Quality Management (TQM) is a management approach that aims to meet or exceed customer expectations by continuously improving products and services. TQM is based on a set of core principles that guide organizations towards achieving quality excellence. These principles include:
Customer Focus
Customer focus is the foundation of TQM. The ultimate goal of TQM is to meet or exceed customer expectations. This requires a deep understanding of customer needs and preferences. TQM emphasizes the importance of listening to customers, collecting feedback, and using customer insights to improve products and services. By focusing on the customer, organizations can deliver high-quality products and services that meet their needs and expectations.
For example, a restaurant that practices TQM would regularly collect feedback from customers to understand their preferences and improve the quality of their food and service. They may also conduct surveys to gather feedback on their menu, ambiance, and overall dining experience.
Continuous Improvement
Continuous improvement is at the heart of TQM. It involves identifying areas for improvement, setting goals, and taking actions to achieve those goals. This requires a willingness to challenge the status quo and continuously look for ways to improve. By continuously improving, organizations can enhance their products and services, reduce costs, and increase customer satisfaction.
For example, a manufacturing company that practices TQM would regularly review their production processes to identify areas for improvement. They may set goals to reduce waste, increase efficiency, and improve product quality. They would then take actions to achieve these goals, such as implementing new technologies or training employees on best practices.
Employee Empowerment
TQM recognizes the importance of empowering employees to take ownership of quality improvement. This involves providing employees with the tools, training, and support they need to become actively involved in the improvement process. It also requires creating a culture of trust, open communication, and teamwork.
Empowered employees are more likely to take initiative, identify problems, and suggest solutions. They are also more committed to the organization's goals and values. By empowering employees, organizations can tap into their creativity and expertise to drive continuous improvement.
Process Management
TQM emphasizes the importance of process management. This involves understanding the entire process, from start to finish, and identifying areas for improvement. It also requires the use of data and metrics to monitor and measure process performance.
Process management helps organizations identify inefficiencies, bottlenecks, and other issues that can impact quality and customer satisfaction. By optimizing processes, organizations can improve quality, reduce costs, and increase efficiency.
Fact-Based Decision Making
TQM is based on data-driven decision making. This involves collecting and analyzing data to identify trends, patterns, and opportunities for improvement. It also requires involving employees in the decision-making process and using a structured approach to problem-solving.
By using data to make decisions, organizations can avoid biases and make informed choices. Involving employees in the decision-making process also helps to build consensus and commitment to the chosen solution.
In conclusion, TQM is a customer-centric approach to management that emphasizes continuous improvement, employee empowerment, process management, and fact-based decision making. By adopting these principles, organizations can achieve quality excellence and meet or exceed customer expectations.
Implementing Total Quality Management in Your Business
Implementing Total Quality Management (TQM) is a process that involves a holistic approach that touches on all aspects of an organization. It is a management philosophy that aims to continuously improve the quality of products, services, and processes. The following are the key steps involved in implementing TQM:
Assessing Your Organization's Readiness
The first step in implementing TQM is to assess your organization's readiness for change. This involves identifying the strengths and weaknesses of your organization, and understanding the current state of your quality management processes. To assess your organization's readiness, you can conduct a SWOT analysis (Strengths, Weaknesses, Opportunities, and Threats). This will help you identify areas that need improvement and areas where your organization excels.
It is important to involve all stakeholders in the assessment process, including employees, customers, and suppliers. This will help you gain a comprehensive understanding of your organization's strengths and weaknesses.
Developing a TQM Implementation Plan
Once you have assessed your organization's readiness, the next step is to develop a TQM implementation plan. This plan should outline the goals, objectives, and key performance indicators for your TQM initiative. It should also identify the key stakeholders, resources, and timelines for the initiative.
The TQM implementation plan should be developed with the involvement of all stakeholders. This will help ensure that everyone is committed to the initiative and that the plan is realistic and achievable.
Training and Educating Employees
Employee education and training is a critical component of any TQM initiative. This involves providing employees with the tools, skills, and knowledge they need to become actively involved in the quality improvement process. It is important to provide ongoing training and education to ensure that employees are equipped with the latest knowledge and skills.
Training and education should not be limited to employees directly involved in the quality improvement process. All employees should be trained on the importance of quality and their role in achieving it. This will help create a culture of quality throughout the organization.
Establishing Metrics and Monitoring Progress
Measuring and monitoring progress is essential to the success of any TQM initiative. This involves establishing metrics and key performance indicators, and regularly tracking and analyzing performance data. It also requires ongoing communication and collaboration among all stakeholders.
The metrics and key performance indicators should be aligned with the goals and objectives of the TQM initiative. They should be measurable, relevant, and meaningful. Regular monitoring and analysis of performance data will help identify areas that need improvement and areas where the organization is excelling.
Communication and collaboration among all stakeholders are critical to the success of the TQM initiative. This will help ensure that everyone is working towards the same goals and that progress is being made.
In conclusion, implementing TQM requires a holistic approach that involves all aspects of the organization. The key steps involved in implementing TQM include assessing your organization's readiness, developing a TQM implementation plan, training and educating employees, and establishing metrics and monitoring progress. By following these steps, your organization can achieve continuous improvement in quality and achieve success in the long run.
Conclusion
In conclusion, Total Quality Management is a powerful approach to improving business performance. By focusing on customer needs, continuous improvement, employee empowerment, process management, and fact-based decision making, organizations can achieve higher levels of quality and performance that translate into increased customer satisfaction and profitability.
Implementing TQM requires a strategic and holistic approach that involves all aspects of the organization. By following the steps outlined in this article and using HTML formatting, you can begin your journey toward TQM and improved business performance.
Similar Blog Posts
Article
Understanding Total Quality Management for Improved Business Performance
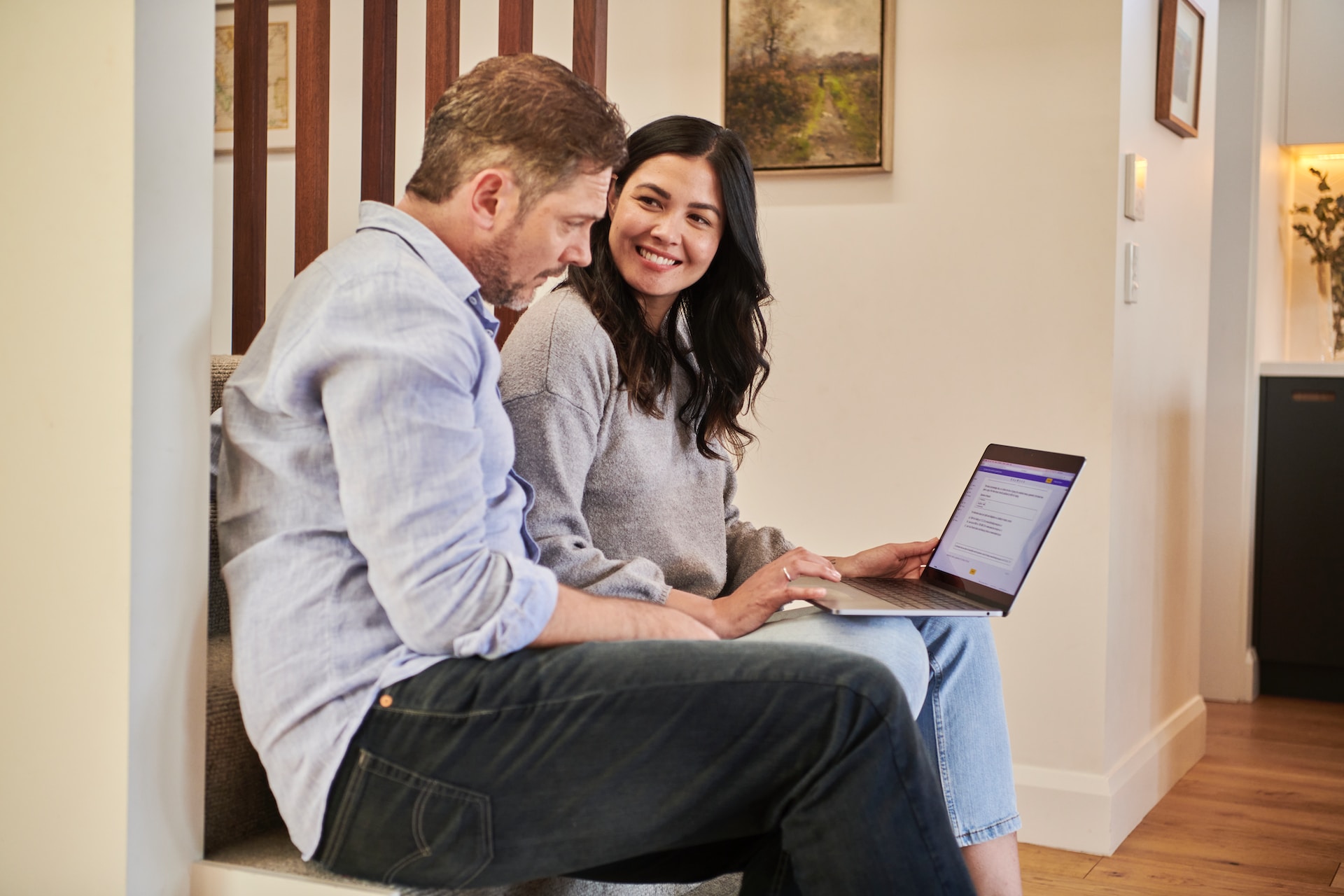
In today's highly competitive market, the success of a business hinges on its ability to deliver quality products and services consistently. This is where Total Quality Management (TQM) comes in. TQM is a management philosophy and approach designed to improve an organization's processes and systems to achieve higher levels of performance. In this article, we'll take a closer look at TQM and how it can help improve your business performance.
The Origins and Evolution of Total Quality Management
Total Quality Management (TQM) has come a long way since its inception in the late 19th and early 20th centuries. TQM was initially developed to identify and correct defects in products, but as manufacturing processes became more complex, new methods were needed to ensure quality and consistency across the entire organization.
Today, TQM is a comprehensive approach to quality management that involves all employees in the organization, from top management to frontline workers. It is a continuous improvement process that aims to meet or exceed customer expectations while reducing costs and increasing efficiency.
Early Quality Control Methods
The first quality control methods were developed in the manufacturing industry and focused on detecting and correcting defects in products through inspection and testing. However, this approach was reactive and did not address the root causes of defects.
In the 1920s, Walter Shewhart introduced the concept of statistical process control (SPC), which involved using statistical tools to monitor the quality of production processes and detect any variations or defects that might occur. This was a major step toward the development of TQM.
SPC enabled manufacturers to identify the root causes of defects and make changes to the production process to prevent them from occurring in the future. This approach was proactive and helped to improve the quality of products and reduce costs.
The Birth of Total Quality Management
The term Total Quality Management was first coined by Armand Feigenbaum in the 1950s. Feigenbaum emphasized the importance of quality at every stage of the production process, from design and development to delivery and after-sales support.
TQM was further developed in the 1970s and 1980s by quality gurus such as W. Edwards Deming, Joseph Juran, and Philip Crosby. These thought leaders emphasized the importance of customer satisfaction, continuous improvement, and employee involvement in the quality improvement process.
Key Contributors to TQM Development
Deming, Juran, and Crosby are considered the three pillars of TQM. Deming, an American statistician, emphasized the importance of continuous improvement and the involvement of every employee in the quality improvement process.
Juran, a Romanian engineer, introduced the concept of quality planning and emphasized the importance of data analysis and process improvement. He believed that quality should be built into the product or service from the beginning, rather than inspected out at the end.
Crosby, an American quality expert, introduced the concept of "zero defects" and emphasized the importance of prevention rather than detection of defects. He believed that quality should be the responsibility of every employee in the organization, not just the quality control department.
Together, these quality gurus helped to shape the modern approach to TQM, which emphasizes continuous improvement, customer satisfaction, and employee involvement in the quality improvement process.
Core Principles of Total Quality Management
Total Quality Management (TQM) is a management approach that aims to meet or exceed customer expectations by continuously improving products and services. TQM is based on a set of core principles that guide organizations towards achieving quality excellence. These principles include:
Customer Focus
Customer focus is the foundation of TQM. The ultimate goal of TQM is to meet or exceed customer expectations. This requires a deep understanding of customer needs and preferences. TQM emphasizes the importance of listening to customers, collecting feedback, and using customer insights to improve products and services. By focusing on the customer, organizations can deliver high-quality products and services that meet their needs and expectations.
For example, a restaurant that practices TQM would regularly collect feedback from customers to understand their preferences and improve the quality of their food and service. They may also conduct surveys to gather feedback on their menu, ambiance, and overall dining experience.
Continuous Improvement
Continuous improvement is at the heart of TQM. It involves identifying areas for improvement, setting goals, and taking actions to achieve those goals. This requires a willingness to challenge the status quo and continuously look for ways to improve. By continuously improving, organizations can enhance their products and services, reduce costs, and increase customer satisfaction.
For example, a manufacturing company that practices TQM would regularly review their production processes to identify areas for improvement. They may set goals to reduce waste, increase efficiency, and improve product quality. They would then take actions to achieve these goals, such as implementing new technologies or training employees on best practices.
Employee Empowerment
TQM recognizes the importance of empowering employees to take ownership of quality improvement. This involves providing employees with the tools, training, and support they need to become actively involved in the improvement process. It also requires creating a culture of trust, open communication, and teamwork.
Empowered employees are more likely to take initiative, identify problems, and suggest solutions. They are also more committed to the organization's goals and values. By empowering employees, organizations can tap into their creativity and expertise to drive continuous improvement.
Process Management
TQM emphasizes the importance of process management. This involves understanding the entire process, from start to finish, and identifying areas for improvement. It also requires the use of data and metrics to monitor and measure process performance.
Process management helps organizations identify inefficiencies, bottlenecks, and other issues that can impact quality and customer satisfaction. By optimizing processes, organizations can improve quality, reduce costs, and increase efficiency.
Fact-Based Decision Making
TQM is based on data-driven decision making. This involves collecting and analyzing data to identify trends, patterns, and opportunities for improvement. It also requires involving employees in the decision-making process and using a structured approach to problem-solving.
By using data to make decisions, organizations can avoid biases and make informed choices. Involving employees in the decision-making process also helps to build consensus and commitment to the chosen solution.
In conclusion, TQM is a customer-centric approach to management that emphasizes continuous improvement, employee empowerment, process management, and fact-based decision making. By adopting these principles, organizations can achieve quality excellence and meet or exceed customer expectations.
Implementing Total Quality Management in Your Business
Implementing Total Quality Management (TQM) is a process that involves a holistic approach that touches on all aspects of an organization. It is a management philosophy that aims to continuously improve the quality of products, services, and processes. The following are the key steps involved in implementing TQM:
Assessing Your Organization's Readiness
The first step in implementing TQM is to assess your organization's readiness for change. This involves identifying the strengths and weaknesses of your organization, and understanding the current state of your quality management processes. To assess your organization's readiness, you can conduct a SWOT analysis (Strengths, Weaknesses, Opportunities, and Threats). This will help you identify areas that need improvement and areas where your organization excels.
It is important to involve all stakeholders in the assessment process, including employees, customers, and suppliers. This will help you gain a comprehensive understanding of your organization's strengths and weaknesses.
Developing a TQM Implementation Plan
Once you have assessed your organization's readiness, the next step is to develop a TQM implementation plan. This plan should outline the goals, objectives, and key performance indicators for your TQM initiative. It should also identify the key stakeholders, resources, and timelines for the initiative.
The TQM implementation plan should be developed with the involvement of all stakeholders. This will help ensure that everyone is committed to the initiative and that the plan is realistic and achievable.
Training and Educating Employees
Employee education and training is a critical component of any TQM initiative. This involves providing employees with the tools, skills, and knowledge they need to become actively involved in the quality improvement process. It is important to provide ongoing training and education to ensure that employees are equipped with the latest knowledge and skills.
Training and education should not be limited to employees directly involved in the quality improvement process. All employees should be trained on the importance of quality and their role in achieving it. This will help create a culture of quality throughout the organization.
Establishing Metrics and Monitoring Progress
Measuring and monitoring progress is essential to the success of any TQM initiative. This involves establishing metrics and key performance indicators, and regularly tracking and analyzing performance data. It also requires ongoing communication and collaboration among all stakeholders.
The metrics and key performance indicators should be aligned with the goals and objectives of the TQM initiative. They should be measurable, relevant, and meaningful. Regular monitoring and analysis of performance data will help identify areas that need improvement and areas where the organization is excelling.
Communication and collaboration among all stakeholders are critical to the success of the TQM initiative. This will help ensure that everyone is working towards the same goals and that progress is being made.
In conclusion, implementing TQM requires a holistic approach that involves all aspects of the organization. The key steps involved in implementing TQM include assessing your organization's readiness, developing a TQM implementation plan, training and educating employees, and establishing metrics and monitoring progress. By following these steps, your organization can achieve continuous improvement in quality and achieve success in the long run.
Conclusion
In conclusion, Total Quality Management is a powerful approach to improving business performance. By focusing on customer needs, continuous improvement, employee empowerment, process management, and fact-based decision making, organizations can achieve higher levels of quality and performance that translate into increased customer satisfaction and profitability.
Implementing TQM requires a strategic and holistic approach that involves all aspects of the organization. By following the steps outlined in this article and using HTML formatting, you can begin your journey toward TQM and improved business performance.
Article
Understanding Total Quality Management for Improved Business Performance
•
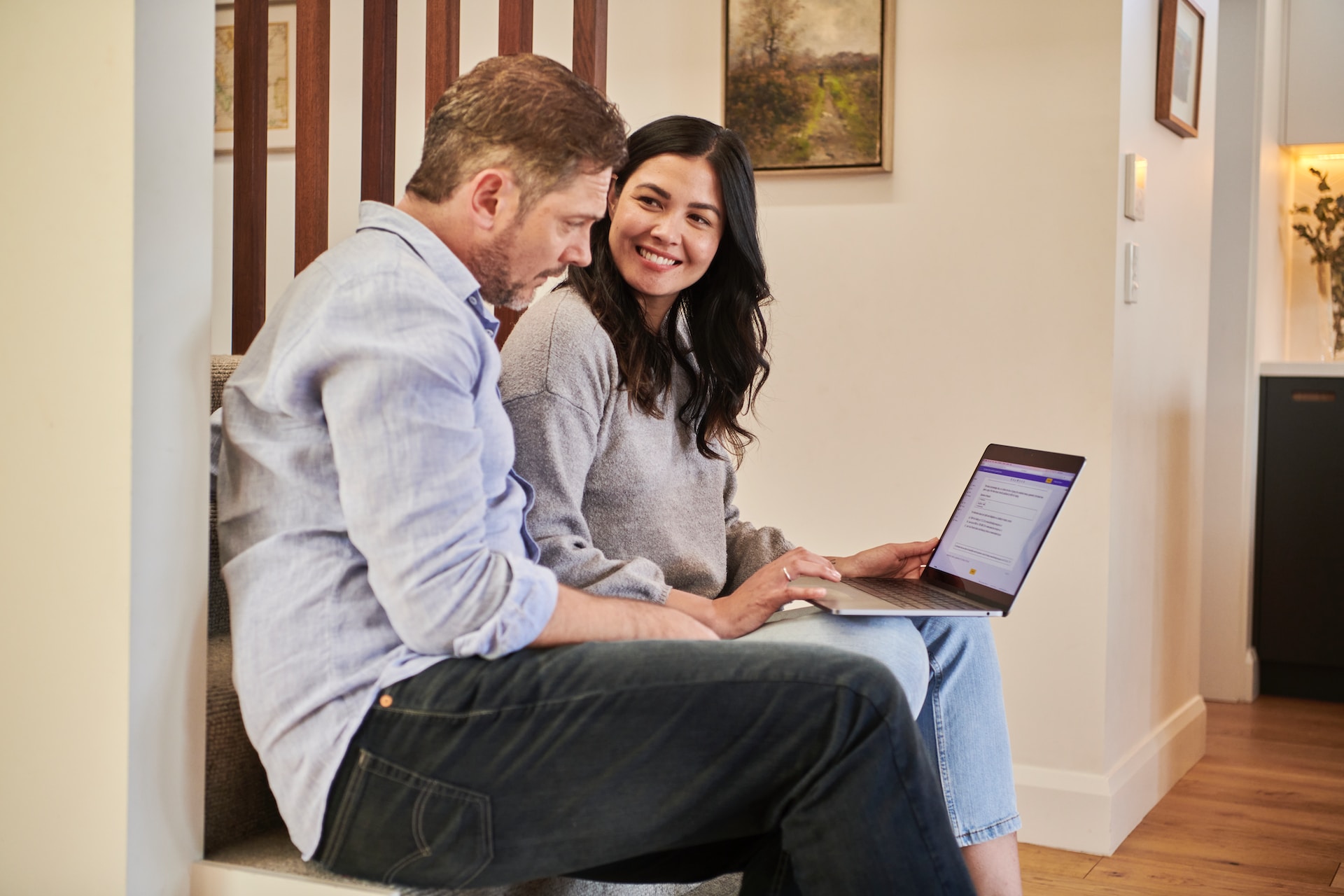