Article
The Benefits of Quality Control in the Manufacturing Process
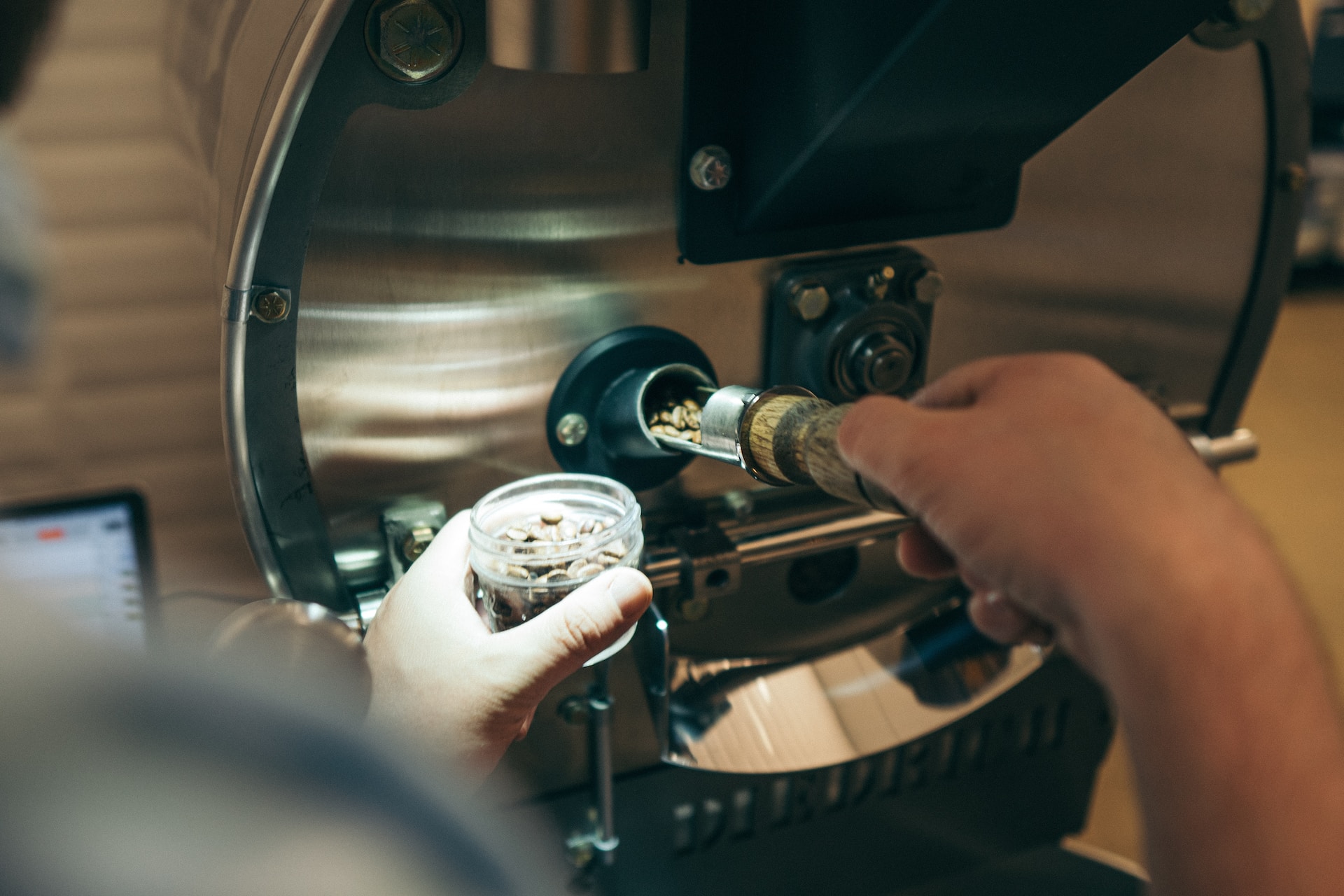
When it comes to manufacturing, one of the most important aspects that cannot be overlooked is quality control. Ensuring that the final product meets the required standards is not only necessary for maintaining consistency in the production process, but it also has a significant impact on the overall success of a business. In this article, we will explore the various benefits of quality control in manufacturing, its techniques, and tools, as well as the difference between quality control and quality assurance.
Understanding Quality Control in Manufacturing
Definition of Quality Control
Quality control is a crucial aspect of the manufacturing process that ensures that the final product meets the required standards. It involves analyzing and identifying potential defects or issues during the manufacturing process to produce a high-quality product that meets customer requirements in a cost-effective and efficient way.
The process of quality control begins with the identification of the critical quality attributes of the product. These attributes are characteristics that are essential to the product's quality, and they are identified by the customers, regulatory agencies, or the manufacturer. Once the critical quality attributes are identified, the manufacturer develops a quality control plan that outlines the procedures and tests that will be used to ensure that the product meets these attributes.
The quality control process involves several steps, including testing raw materials, monitoring the manufacturing process, and inspecting the final product. The goal is to identify any defects or deviations from the required standards and take corrective action to eliminate or minimize them.
Importance of Quality Control in Manufacturing
The importance of quality control in manufacturing cannot be overstated. Here are some reasons why it is crucial:
- Improves product quality: Quality control helps to ensure that the final product meets the required standards and is of high quality. This, in turn, enhances customer satisfaction and loyalty.
- Increases customer satisfaction: Customers expect high-quality products that meet their requirements. Quality control helps to ensure that the final product meets these requirements, resulting in increased customer satisfaction.
- Reduces production costs: Quality control helps to identify defects and deviations early in the manufacturing process, reducing the cost of rework and scrap.
- Enhances brand reputation: High-quality products that meet customer requirements and are manufactured in a cost-effective and efficient way enhance a company's brand reputation.
- Ensures compliance with industry standards and regulations: Quality control helps to ensure that the final product meets industry standards and regulations, reducing the risk of legal and financial penalties.
Quality Control vs. Quality Assurance
Quality control and quality assurance are two essential aspects of the manufacturing process that are often confused. While they are related, they are not the same thing.
Quality assurance is the process of ensuring that a product is manufactured in compliance with established standards and regulations. It focuses on the development of processes that help minimize variations and defects in manufacturing. Quality assurance is a proactive process that involves identifying potential issues before they occur and taking corrective action to prevent them from happening.
Quality control, on the other hand, is the process of identifying defects and deviations during the manufacturing process to eliminate or minimize them. Quality control is a reactive process that involves testing and inspecting the final product to ensure that it meets the required standards.
In summary, quality control and quality assurance are both essential aspects of the manufacturing process that work together to ensure that the final product meets the required standards. While they are different processes, they are both crucial to producing high-quality products that meet customer requirements and are manufactured in a cost-effective and efficient way.
Key Benefits of Quality Control
Quality control is a crucial aspect of any manufacturing process. It involves a series of measures and processes that are put in place to ensure that the final product meets the required specifications and customer expectations. Quality control has numerous benefits, including:
Improved Product Quality
One of the primary benefits of quality control is improved product quality. By having a strict quality control process in place, manufacturers can identify potential defects and deviations early on, enabling them to take corrective action before they develop into major problems. This results in products that meet the required specifications and customer expectations, improving customer satisfaction in the long run.
For example, a manufacturer of electronic devices may implement quality control measures to ensure that each device is tested for functionality and durability before being released to the market. This helps to identify any defects early on and ensures that the final product meets the required standards and customer expectations.
Increased Customer Satisfaction
When customers purchase a product, they expect it to be of high quality. By ensuring that the final product meets the required standards, manufacturers can increase customer satisfaction and loyalty. This, in turn, leads to repeat business and positive word-of-mouth marketing.
For instance, a clothing manufacturer may implement quality control measures to ensure that each garment is made with high-quality materials and is free from defects. This helps to improve customer satisfaction and loyalty, as customers are more likely to return to a brand that consistently produces high-quality products.
Reduced Production Costs
Poor quality products can result in high production costs due to the need for rework, scrap, and retesting. By implementing quality control processes and identifying defects early on, manufacturers can minimize such costs and increase their operational efficiency in the long run.
For example, a food manufacturer may implement quality control measures to ensure that each batch of food is tested for quality and safety. This helps to identify any defects early on and ensures that the final product meets the required standards, reducing the need for rework and minimizing production costs.
Enhanced Brand Reputation
Manufacturers who consistently produce high-quality products are likely to build a positive brand reputation. Word-of-mouth marketing from satisfied customers helps to improve their reputation, resulting in increased brand loyalty and customer trust.
For instance, a car manufacturer may implement quality control measures to ensure that each vehicle is made with high-quality materials and is free from defects. This helps to improve the brand's reputation, as customers are more likely to trust a brand that consistently produces high-quality vehicles.
Compliance with Industry Standards and Regulations
Adherence to industry standards and regulations is necessary for manufacturers to remain competitive and avoid legal implications. By implementing quality control processes that comply with industry regulations and standards, manufacturers can avoid costly legal actions and maintain their position in the market.
For example, a pharmaceutical manufacturer may implement quality control measures to ensure that each batch of drugs is tested for quality and safety. This helps to ensure that the final product complies with industry regulations and standards, reducing the risk of legal actions and maintaining the manufacturer's position in the market.
In conclusion, quality control is essential for any manufacturing process. It helps to improve product quality, increase customer satisfaction, reduce production costs, enhance brand reputation, and ensure compliance with industry standards and regulations. By implementing quality control processes, manufacturers can produce high-quality products that meet customer expectations and maintain their position in the market.
Quality Control Techniques and Tools
Quality control is an essential aspect of manufacturing that ensures the products meet the required standards. It involves using various techniques and tools to monitor and control the quality of the manufacturing process. Here are some of the quality control techniques and tools used in the manufacturing industry:
Statistical Process Control (SPC)
SPC is a statistical technique that involves collecting data and analyzing it to identify potential issues or defects early on in the manufacturing process. This technique enables manufacturers to take corrective actions before the product is complete, ensuring that the final product meets the required standards. SPC involves using statistical tools such as control charts, histograms, and scatter diagrams to monitor the manufacturing process.
Inspection and Testing
Inspection and testing are crucial quality control techniques used to ensure that products meet the required specifications. They involve visual inspection, functional testing, and performance testing, among others. Inspection and testing are typically carried out at various stages of the manufacturing process to ensure that the final product meets the required standards.
Quality Audits
Quality audits are a systematic and independent examination of a manufacturing process to determine whether it conforms to established standards. It involves analyzing the process, procedures, and records to identify gaps in the quality control processes. Quality audits enable manufacturers to take corrective action before the issues become major problems.
Root Cause Analysis
Root cause analysis is a problem-solving technique used to identify the underlying cause of issues in a manufacturing process. It involves analyzing the data collected during the manufacturing process to identify the root cause of defects or issues. Root cause analysis enables manufacturers to address the root cause of defects or issues rather than just treating the symptoms.
Corrective and Preventive Actions
Corrective and preventive actions involve analyzing and addressing the root cause of defects and deviations in a manufacturing process. By taking corrective and preventive actions, manufacturers can minimize the occurrence of such issues in the future. Corrective actions involve addressing the issues that have already occurred, while preventive actions involve taking steps to prevent the issues from occurring in the future.
In conclusion, quality control techniques and tools are essential in the manufacturing industry to ensure that the final product meets the required standards. By using these techniques and tools, manufacturers can identify potential issues early on in the manufacturing process and take corrective actions to prevent the issues from becoming major problems.
Conclusion
In conclusion, quality control is an essential process in the manufacturing industry. By implementing quality control techniques and tools, manufacturers can improve product quality, increase customer satisfaction, reduce production costs, enhance brand reputation, and comply with industry standards and regulations. It is, therefore, crucial for manufacturers to prioritize quality control processes to remain competitive in the market and meet customer expectations.
Article
The Benefits of Quality Control in the Manufacturing Process
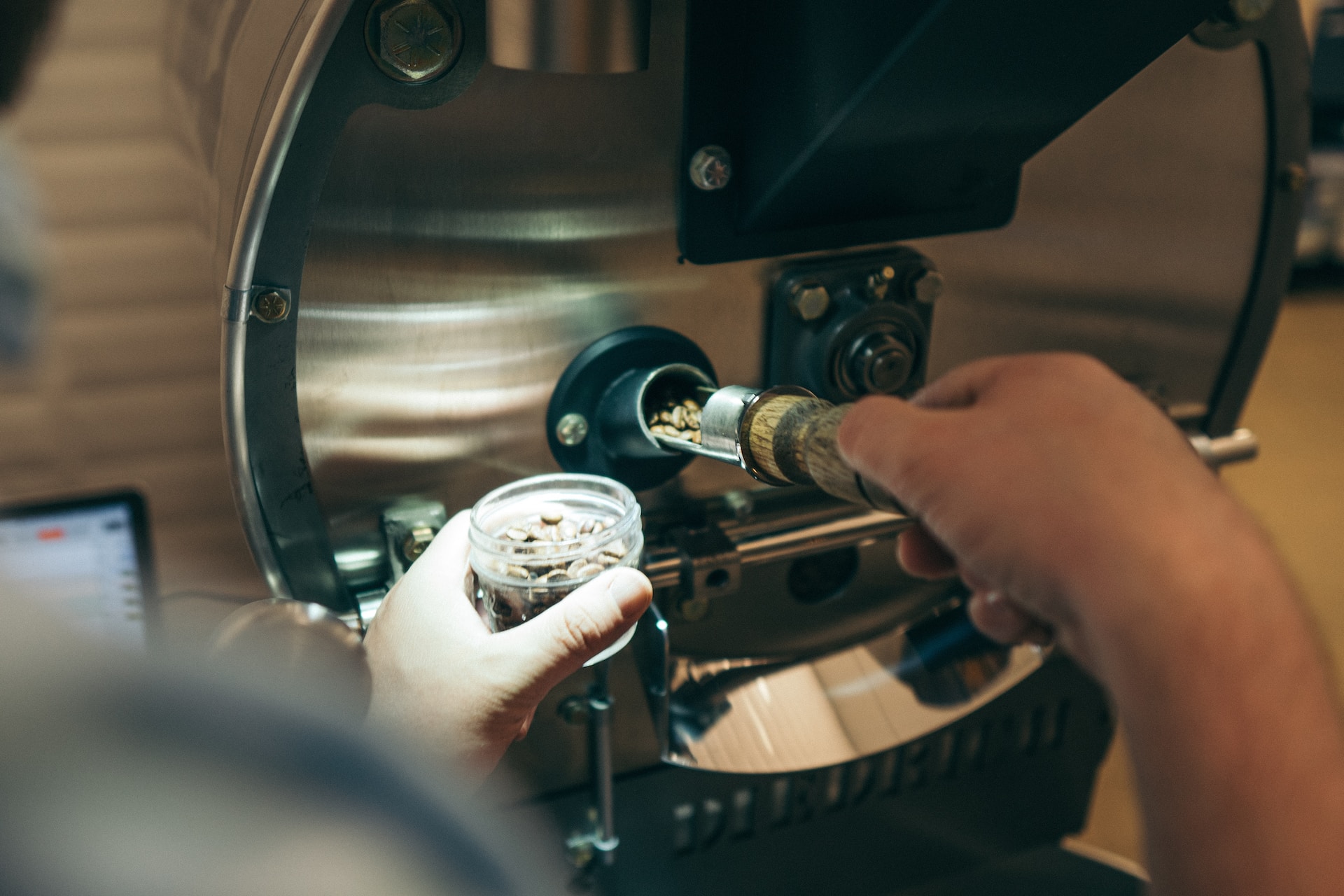
When it comes to manufacturing, one of the most important aspects that cannot be overlooked is quality control. Ensuring that the final product meets the required standards is not only necessary for maintaining consistency in the production process, but it also has a significant impact on the overall success of a business. In this article, we will explore the various benefits of quality control in manufacturing, its techniques, and tools, as well as the difference between quality control and quality assurance.
Understanding Quality Control in Manufacturing
Definition of Quality Control
Quality control is a crucial aspect of the manufacturing process that ensures that the final product meets the required standards. It involves analyzing and identifying potential defects or issues during the manufacturing process to produce a high-quality product that meets customer requirements in a cost-effective and efficient way.
The process of quality control begins with the identification of the critical quality attributes of the product. These attributes are characteristics that are essential to the product's quality, and they are identified by the customers, regulatory agencies, or the manufacturer. Once the critical quality attributes are identified, the manufacturer develops a quality control plan that outlines the procedures and tests that will be used to ensure that the product meets these attributes.
The quality control process involves several steps, including testing raw materials, monitoring the manufacturing process, and inspecting the final product. The goal is to identify any defects or deviations from the required standards and take corrective action to eliminate or minimize them.
Importance of Quality Control in Manufacturing
The importance of quality control in manufacturing cannot be overstated. Here are some reasons why it is crucial:
- Improves product quality: Quality control helps to ensure that the final product meets the required standards and is of high quality. This, in turn, enhances customer satisfaction and loyalty.
- Increases customer satisfaction: Customers expect high-quality products that meet their requirements. Quality control helps to ensure that the final product meets these requirements, resulting in increased customer satisfaction.
- Reduces production costs: Quality control helps to identify defects and deviations early in the manufacturing process, reducing the cost of rework and scrap.
- Enhances brand reputation: High-quality products that meet customer requirements and are manufactured in a cost-effective and efficient way enhance a company's brand reputation.
- Ensures compliance with industry standards and regulations: Quality control helps to ensure that the final product meets industry standards and regulations, reducing the risk of legal and financial penalties.
Quality Control vs. Quality Assurance
Quality control and quality assurance are two essential aspects of the manufacturing process that are often confused. While they are related, they are not the same thing.
Quality assurance is the process of ensuring that a product is manufactured in compliance with established standards and regulations. It focuses on the development of processes that help minimize variations and defects in manufacturing. Quality assurance is a proactive process that involves identifying potential issues before they occur and taking corrective action to prevent them from happening.
Quality control, on the other hand, is the process of identifying defects and deviations during the manufacturing process to eliminate or minimize them. Quality control is a reactive process that involves testing and inspecting the final product to ensure that it meets the required standards.
In summary, quality control and quality assurance are both essential aspects of the manufacturing process that work together to ensure that the final product meets the required standards. While they are different processes, they are both crucial to producing high-quality products that meet customer requirements and are manufactured in a cost-effective and efficient way.
Key Benefits of Quality Control
Quality control is a crucial aspect of any manufacturing process. It involves a series of measures and processes that are put in place to ensure that the final product meets the required specifications and customer expectations. Quality control has numerous benefits, including:
Improved Product Quality
One of the primary benefits of quality control is improved product quality. By having a strict quality control process in place, manufacturers can identify potential defects and deviations early on, enabling them to take corrective action before they develop into major problems. This results in products that meet the required specifications and customer expectations, improving customer satisfaction in the long run.
For example, a manufacturer of electronic devices may implement quality control measures to ensure that each device is tested for functionality and durability before being released to the market. This helps to identify any defects early on and ensures that the final product meets the required standards and customer expectations.
Increased Customer Satisfaction
When customers purchase a product, they expect it to be of high quality. By ensuring that the final product meets the required standards, manufacturers can increase customer satisfaction and loyalty. This, in turn, leads to repeat business and positive word-of-mouth marketing.
For instance, a clothing manufacturer may implement quality control measures to ensure that each garment is made with high-quality materials and is free from defects. This helps to improve customer satisfaction and loyalty, as customers are more likely to return to a brand that consistently produces high-quality products.
Reduced Production Costs
Poor quality products can result in high production costs due to the need for rework, scrap, and retesting. By implementing quality control processes and identifying defects early on, manufacturers can minimize such costs and increase their operational efficiency in the long run.
For example, a food manufacturer may implement quality control measures to ensure that each batch of food is tested for quality and safety. This helps to identify any defects early on and ensures that the final product meets the required standards, reducing the need for rework and minimizing production costs.
Enhanced Brand Reputation
Manufacturers who consistently produce high-quality products are likely to build a positive brand reputation. Word-of-mouth marketing from satisfied customers helps to improve their reputation, resulting in increased brand loyalty and customer trust.
For instance, a car manufacturer may implement quality control measures to ensure that each vehicle is made with high-quality materials and is free from defects. This helps to improve the brand's reputation, as customers are more likely to trust a brand that consistently produces high-quality vehicles.
Compliance with Industry Standards and Regulations
Adherence to industry standards and regulations is necessary for manufacturers to remain competitive and avoid legal implications. By implementing quality control processes that comply with industry regulations and standards, manufacturers can avoid costly legal actions and maintain their position in the market.
For example, a pharmaceutical manufacturer may implement quality control measures to ensure that each batch of drugs is tested for quality and safety. This helps to ensure that the final product complies with industry regulations and standards, reducing the risk of legal actions and maintaining the manufacturer's position in the market.
In conclusion, quality control is essential for any manufacturing process. It helps to improve product quality, increase customer satisfaction, reduce production costs, enhance brand reputation, and ensure compliance with industry standards and regulations. By implementing quality control processes, manufacturers can produce high-quality products that meet customer expectations and maintain their position in the market.
Quality Control Techniques and Tools
Quality control is an essential aspect of manufacturing that ensures the products meet the required standards. It involves using various techniques and tools to monitor and control the quality of the manufacturing process. Here are some of the quality control techniques and tools used in the manufacturing industry:
Statistical Process Control (SPC)
SPC is a statistical technique that involves collecting data and analyzing it to identify potential issues or defects early on in the manufacturing process. This technique enables manufacturers to take corrective actions before the product is complete, ensuring that the final product meets the required standards. SPC involves using statistical tools such as control charts, histograms, and scatter diagrams to monitor the manufacturing process.
Inspection and Testing
Inspection and testing are crucial quality control techniques used to ensure that products meet the required specifications. They involve visual inspection, functional testing, and performance testing, among others. Inspection and testing are typically carried out at various stages of the manufacturing process to ensure that the final product meets the required standards.
Quality Audits
Quality audits are a systematic and independent examination of a manufacturing process to determine whether it conforms to established standards. It involves analyzing the process, procedures, and records to identify gaps in the quality control processes. Quality audits enable manufacturers to take corrective action before the issues become major problems.
Root Cause Analysis
Root cause analysis is a problem-solving technique used to identify the underlying cause of issues in a manufacturing process. It involves analyzing the data collected during the manufacturing process to identify the root cause of defects or issues. Root cause analysis enables manufacturers to address the root cause of defects or issues rather than just treating the symptoms.
Corrective and Preventive Actions
Corrective and preventive actions involve analyzing and addressing the root cause of defects and deviations in a manufacturing process. By taking corrective and preventive actions, manufacturers can minimize the occurrence of such issues in the future. Corrective actions involve addressing the issues that have already occurred, while preventive actions involve taking steps to prevent the issues from occurring in the future.
In conclusion, quality control techniques and tools are essential in the manufacturing industry to ensure that the final product meets the required standards. By using these techniques and tools, manufacturers can identify potential issues early on in the manufacturing process and take corrective actions to prevent the issues from becoming major problems.
Conclusion
In conclusion, quality control is an essential process in the manufacturing industry. By implementing quality control techniques and tools, manufacturers can improve product quality, increase customer satisfaction, reduce production costs, enhance brand reputation, and comply with industry standards and regulations. It is, therefore, crucial for manufacturers to prioritize quality control processes to remain competitive in the market and meet customer expectations.
Article
The Benefits of Quality Control in the Manufacturing Process
•
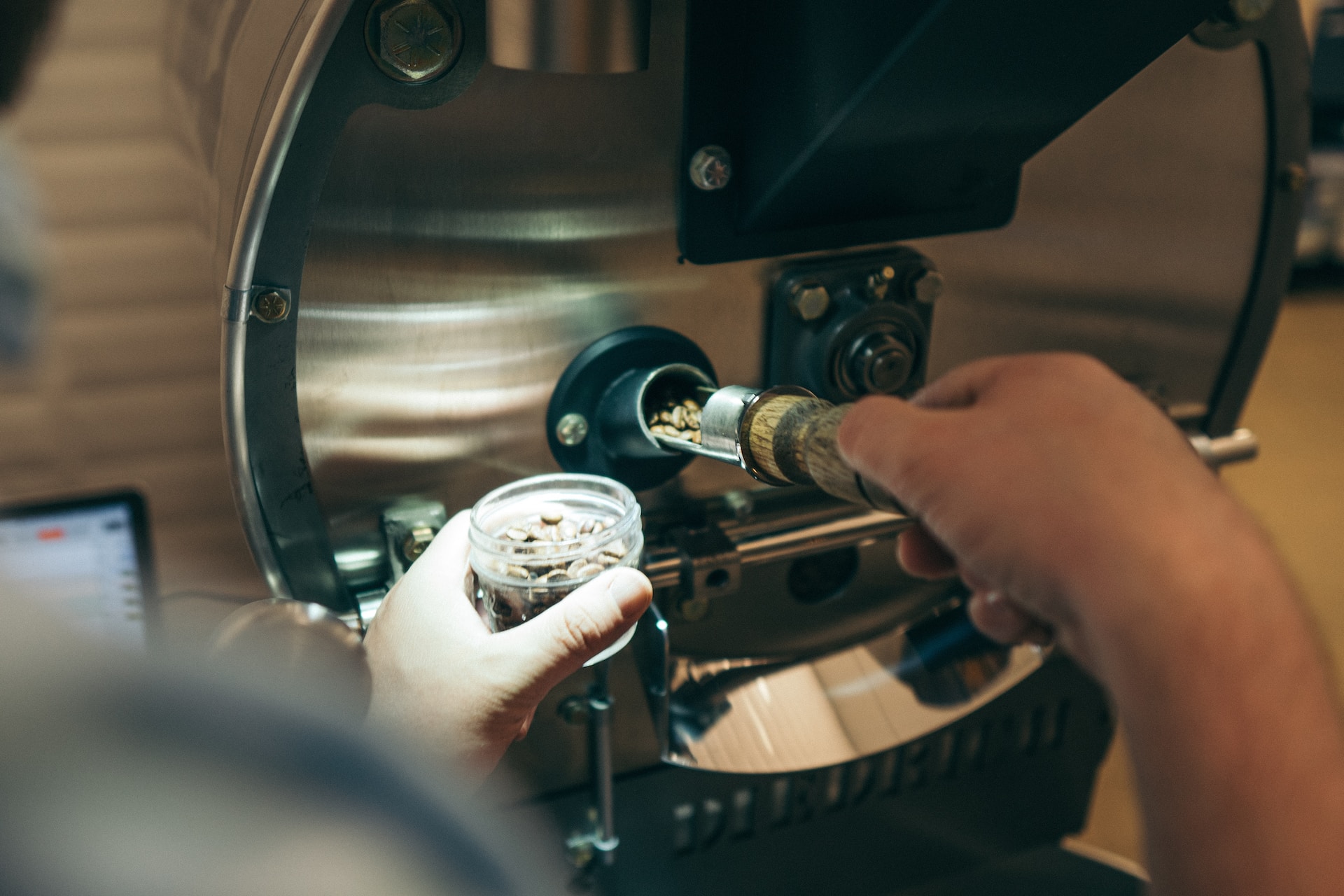