Article
A Step-by-Step Guide to Process Analysis
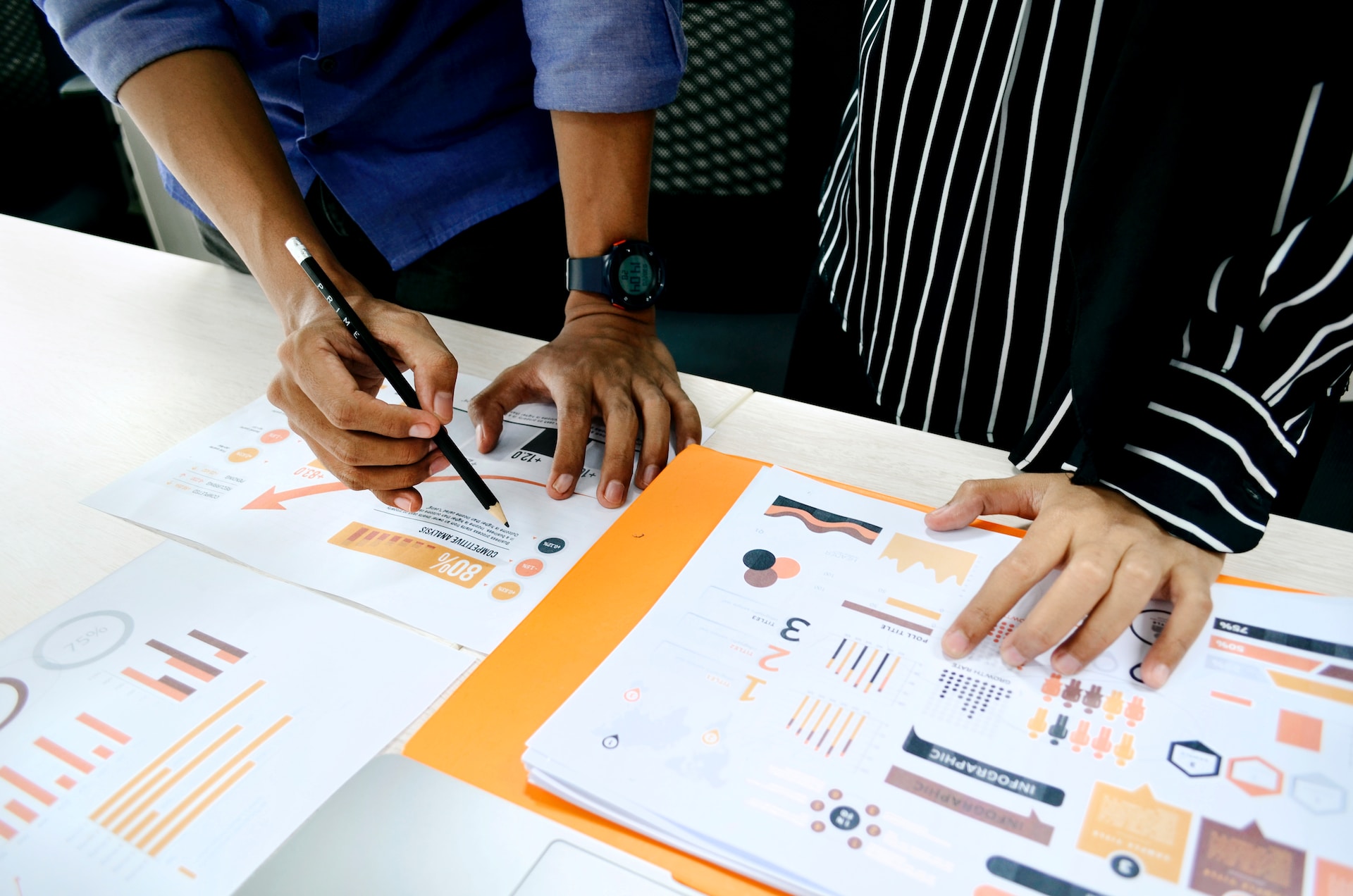
Process analysis is a powerful tool that can help organizations improve their operations and become more efficient. By understanding the flow of work, identifying bottlenecks, and streamlining processes, businesses can reduce costs, improve customer satisfaction, and boost productivity. But how does one go about conducting process analysis? In this article, we'll provide a step-by-step guide to the process, from understanding what process analysis is, to gathering information, mapping the process, and analyzing the data.
Understanding Process Analysis
Definition of Process Analysis
Process analysis is a systematic method of examining how work is done in an organization, with the aim of improving that work. It involves breaking down a process into its component parts and studying each part to determine how it contributes to the overall outcome.
For example, in a manufacturing process, process analysis might involve studying the steps involved in assembling a product, from the raw materials to the finished product. The goal would be to identify any steps that are inefficient or unnecessary, and to find ways to streamline the process to reduce costs and increase productivity.
Importance of Process Analysis
Process analysis is important because it allows organizations to identify areas of inefficiency and waste in their operations. By analyzing the flow of work, it's possible to identify bottlenecks and areas where work is duplicated or unnecessary. This insight can then be used to develop strategies for improving the process, reducing costs, and increasing productivity.
For example, a healthcare organization might use process analysis to study the steps involved in admitting a patient to the hospital. By identifying any inefficiencies in the process, such as long wait times or duplicated paperwork, the organization can develop strategies to improve the process and provide better care to patients.
Applications of Process Analysis
Process analysis can be applied to any process within an organization, from manufacturing and logistics to customer service and administrative tasks. It can help organizations in industries such as healthcare, finance, and retail improve operations and provide better services to their customers.
For example, a retail organization might use process analysis to study the steps involved in stocking shelves and serving customers. By identifying any inefficiencies in the process, such as slow restocking times or long checkout lines, the organization can develop strategies to improve the process and provide better service to customers.
Process analysis can also be used to identify opportunities for automation and technology implementation. By studying the steps involved in a process, organizations can identify areas where technology can be used to streamline the process and reduce costs.
In conclusion, process analysis is a valuable tool for organizations looking to improve their operations and provide better services to their customers. By breaking down processes into their component parts and studying each part in detail, organizations can identify inefficiencies and develop strategies for improvement.
Identifying the Process to Analyze
Selecting the Right Process
The first step in process analysis is to identify the process that you want to analyze. This process should be one that has a significant impact on the organization's operations, either in terms of cost, speed, or quality. It should also be a process that can be improved through process analysis.
For example, let's say that you work for a manufacturing company that produces widgets. One process that could have a significant impact on the company's operations is the assembly process. If the assembly process is slow or error-prone, it could lead to delays in production and increased costs. By analyzing the assembly process, you may be able to identify ways to streamline the process and improve efficiency.
Defining Process Boundaries
Once you have selected the process to analyze, it's important to define the boundaries of the process. This means identifying the inputs and outputs of the process, as well as the start and end points.
Continuing with the example of the assembly process, the inputs may include individual components, while the outputs may be finished widgets. The start point may be when the components are first received, and the end point may be when the finished widgets are shipped out to customers.
Establishing Process Objectives
Before beginning the analysis, it's important to establish clear objectives for the process. These objectives should be specific, measurable, achievable, relevant, and time-bound. This will help ensure that the analysis stays focused and that the results are actionable.
For the assembly process, some possible objectives could include reducing the time it takes to assemble each widget, improving the quality of the finished product, and reducing the number of defects.
Once these objectives have been established, you can begin the process analysis. This may involve gathering data on the current process, identifying bottlenecks or areas of inefficiency, and brainstorming potential solutions.
Overall, process analysis can be a powerful tool for improving organizational efficiency and effectiveness. By selecting the right process, defining clear boundaries, and establishing specific objectives, you can ensure that your analysis is focused and actionable.
Gathering Process Information
Process analysis is a critical step in identifying areas of improvement within a company. The process analysis begins with gathering information about the process. In order to do this, there are several methods that can be used.
Process Documentation
One of the most common ways to gather information is through process documentation. This includes process maps, standard operating procedures, and work instructions. Process documentation provides a detailed overview of the process, including the steps involved and the roles of each person involved.
When reviewing process documentation, it is important to ensure that it accurately reflects the current state of the process. This means that the documentation should be updated regularly to reflect any changes that have been made.
Stakeholder Interviews
Another way to gather information is through stakeholder interviews. This involves talking to people who are involved in the process, including employees, managers, and customers. Stakeholder interviews can provide valuable insights into how the process works in practice, as well as areas for improvement.
During stakeholder interviews, it is important to ask open-ended questions that encourage discussion. This allows stakeholders to provide detailed information about their experiences with the process.
Data Collection Methods
Data can also be collected through quantitative and qualitative methods. Quantitative methods include surveys and data analysis, while qualitative methods include observation and focus groups.
Surveys can be used to gather data from a large group of people. This data can then be analyzed to identify patterns and trends in the process. Observation involves watching the process in action and taking notes on how it works. Focus groups involve bringing together a group of stakeholders to discuss their experiences with the process.
Regardless of the method used, the data collected should be analyzed to identify areas for improvement in the process. This analysis can then be used to develop a plan for making changes to the process.
Mapping the Process
Mapping out a process is a crucial step in identifying areas for improvement and increasing efficiency. By creating a visual representation of the process, it becomes easier to identify bottlenecks and areas for improvement. This, in turn, can help to reduce costs and improve the quality of the output.
Creating a Process Flowchart
The first step in mapping out a process is to create a process flowchart. This involves identifying the steps involved in the process and mapping them out in a visual format. The flowchart should clearly show the input and output points of the process, as well as any decision points or loops.
Creating a process flowchart can be a collaborative process, involving input from all stakeholders. By involving everyone in the process, it becomes easier to identify areas for improvement and ensure that the final process map accurately reflects the current process.
Identifying Process Inputs and Outputs
In addition to mapping out the steps involved in the process, it is also important to identify the inputs and outputs of the process. Inputs are the resources that are required for the process to work, while outputs are the end products or services that are produced by the process.
By tracking inputs and outputs, it becomes easier to identify areas where resources are being wasted or where the output is not meeting expectations. This information can then be used to make improvements to the process.
Analyzing Process Steps
The final step in process analysis is to analyze each step in the process. This involves identifying areas where work is duplicated, unnecessary, or inefficient. By analyzing each step, it becomes easier to identify opportunities for streamlining the process and reducing costs.
One way to analyze process steps is to use a process map. This involves mapping out the process and then identifying areas where work is duplicated or inefficient. Once these areas have been identified, they can be targeted for improvement.
Overall, mapping out a process and analyzing each step is a crucial step in improving efficiency and reducing costs. By identifying areas for improvement, it becomes easier to make changes that will improve the quality of the output and increase customer satisfaction.
Conclusion
In conclusion, process analysis is an essential tool for organizations looking to improve their operations and become more efficient. By following this step-by-step guide, businesses can gain valuable insights into their processes, identify areas for improvement, and develop strategies for increasing productivity and reducing costs.
Similar Blog Posts
Article
A Step-by-Step Guide to Process Analysis
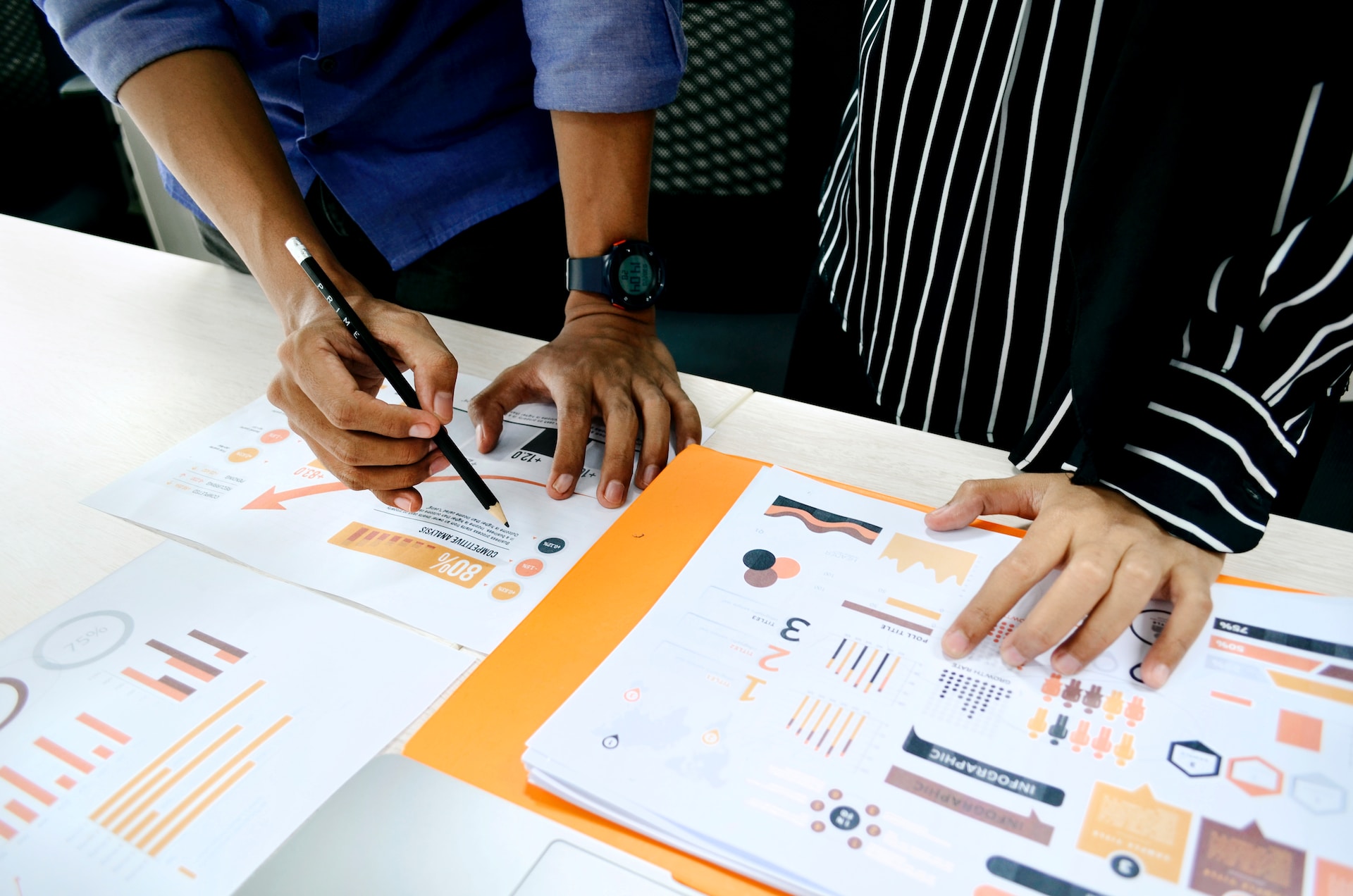
Process analysis is a powerful tool that can help organizations improve their operations and become more efficient. By understanding the flow of work, identifying bottlenecks, and streamlining processes, businesses can reduce costs, improve customer satisfaction, and boost productivity. But how does one go about conducting process analysis? In this article, we'll provide a step-by-step guide to the process, from understanding what process analysis is, to gathering information, mapping the process, and analyzing the data.
Understanding Process Analysis
Definition of Process Analysis
Process analysis is a systematic method of examining how work is done in an organization, with the aim of improving that work. It involves breaking down a process into its component parts and studying each part to determine how it contributes to the overall outcome.
For example, in a manufacturing process, process analysis might involve studying the steps involved in assembling a product, from the raw materials to the finished product. The goal would be to identify any steps that are inefficient or unnecessary, and to find ways to streamline the process to reduce costs and increase productivity.
Importance of Process Analysis
Process analysis is important because it allows organizations to identify areas of inefficiency and waste in their operations. By analyzing the flow of work, it's possible to identify bottlenecks and areas where work is duplicated or unnecessary. This insight can then be used to develop strategies for improving the process, reducing costs, and increasing productivity.
For example, a healthcare organization might use process analysis to study the steps involved in admitting a patient to the hospital. By identifying any inefficiencies in the process, such as long wait times or duplicated paperwork, the organization can develop strategies to improve the process and provide better care to patients.
Applications of Process Analysis
Process analysis can be applied to any process within an organization, from manufacturing and logistics to customer service and administrative tasks. It can help organizations in industries such as healthcare, finance, and retail improve operations and provide better services to their customers.
For example, a retail organization might use process analysis to study the steps involved in stocking shelves and serving customers. By identifying any inefficiencies in the process, such as slow restocking times or long checkout lines, the organization can develop strategies to improve the process and provide better service to customers.
Process analysis can also be used to identify opportunities for automation and technology implementation. By studying the steps involved in a process, organizations can identify areas where technology can be used to streamline the process and reduce costs.
In conclusion, process analysis is a valuable tool for organizations looking to improve their operations and provide better services to their customers. By breaking down processes into their component parts and studying each part in detail, organizations can identify inefficiencies and develop strategies for improvement.
Identifying the Process to Analyze
Selecting the Right Process
The first step in process analysis is to identify the process that you want to analyze. This process should be one that has a significant impact on the organization's operations, either in terms of cost, speed, or quality. It should also be a process that can be improved through process analysis.
For example, let's say that you work for a manufacturing company that produces widgets. One process that could have a significant impact on the company's operations is the assembly process. If the assembly process is slow or error-prone, it could lead to delays in production and increased costs. By analyzing the assembly process, you may be able to identify ways to streamline the process and improve efficiency.
Defining Process Boundaries
Once you have selected the process to analyze, it's important to define the boundaries of the process. This means identifying the inputs and outputs of the process, as well as the start and end points.
Continuing with the example of the assembly process, the inputs may include individual components, while the outputs may be finished widgets. The start point may be when the components are first received, and the end point may be when the finished widgets are shipped out to customers.
Establishing Process Objectives
Before beginning the analysis, it's important to establish clear objectives for the process. These objectives should be specific, measurable, achievable, relevant, and time-bound. This will help ensure that the analysis stays focused and that the results are actionable.
For the assembly process, some possible objectives could include reducing the time it takes to assemble each widget, improving the quality of the finished product, and reducing the number of defects.
Once these objectives have been established, you can begin the process analysis. This may involve gathering data on the current process, identifying bottlenecks or areas of inefficiency, and brainstorming potential solutions.
Overall, process analysis can be a powerful tool for improving organizational efficiency and effectiveness. By selecting the right process, defining clear boundaries, and establishing specific objectives, you can ensure that your analysis is focused and actionable.
Gathering Process Information
Process analysis is a critical step in identifying areas of improvement within a company. The process analysis begins with gathering information about the process. In order to do this, there are several methods that can be used.
Process Documentation
One of the most common ways to gather information is through process documentation. This includes process maps, standard operating procedures, and work instructions. Process documentation provides a detailed overview of the process, including the steps involved and the roles of each person involved.
When reviewing process documentation, it is important to ensure that it accurately reflects the current state of the process. This means that the documentation should be updated regularly to reflect any changes that have been made.
Stakeholder Interviews
Another way to gather information is through stakeholder interviews. This involves talking to people who are involved in the process, including employees, managers, and customers. Stakeholder interviews can provide valuable insights into how the process works in practice, as well as areas for improvement.
During stakeholder interviews, it is important to ask open-ended questions that encourage discussion. This allows stakeholders to provide detailed information about their experiences with the process.
Data Collection Methods
Data can also be collected through quantitative and qualitative methods. Quantitative methods include surveys and data analysis, while qualitative methods include observation and focus groups.
Surveys can be used to gather data from a large group of people. This data can then be analyzed to identify patterns and trends in the process. Observation involves watching the process in action and taking notes on how it works. Focus groups involve bringing together a group of stakeholders to discuss their experiences with the process.
Regardless of the method used, the data collected should be analyzed to identify areas for improvement in the process. This analysis can then be used to develop a plan for making changes to the process.
Mapping the Process
Mapping out a process is a crucial step in identifying areas for improvement and increasing efficiency. By creating a visual representation of the process, it becomes easier to identify bottlenecks and areas for improvement. This, in turn, can help to reduce costs and improve the quality of the output.
Creating a Process Flowchart
The first step in mapping out a process is to create a process flowchart. This involves identifying the steps involved in the process and mapping them out in a visual format. The flowchart should clearly show the input and output points of the process, as well as any decision points or loops.
Creating a process flowchart can be a collaborative process, involving input from all stakeholders. By involving everyone in the process, it becomes easier to identify areas for improvement and ensure that the final process map accurately reflects the current process.
Identifying Process Inputs and Outputs
In addition to mapping out the steps involved in the process, it is also important to identify the inputs and outputs of the process. Inputs are the resources that are required for the process to work, while outputs are the end products or services that are produced by the process.
By tracking inputs and outputs, it becomes easier to identify areas where resources are being wasted or where the output is not meeting expectations. This information can then be used to make improvements to the process.
Analyzing Process Steps
The final step in process analysis is to analyze each step in the process. This involves identifying areas where work is duplicated, unnecessary, or inefficient. By analyzing each step, it becomes easier to identify opportunities for streamlining the process and reducing costs.
One way to analyze process steps is to use a process map. This involves mapping out the process and then identifying areas where work is duplicated or inefficient. Once these areas have been identified, they can be targeted for improvement.
Overall, mapping out a process and analyzing each step is a crucial step in improving efficiency and reducing costs. By identifying areas for improvement, it becomes easier to make changes that will improve the quality of the output and increase customer satisfaction.
Conclusion
In conclusion, process analysis is an essential tool for organizations looking to improve their operations and become more efficient. By following this step-by-step guide, businesses can gain valuable insights into their processes, identify areas for improvement, and develop strategies for increasing productivity and reducing costs.
Article
A Step-by-Step Guide to Process Analysis
•
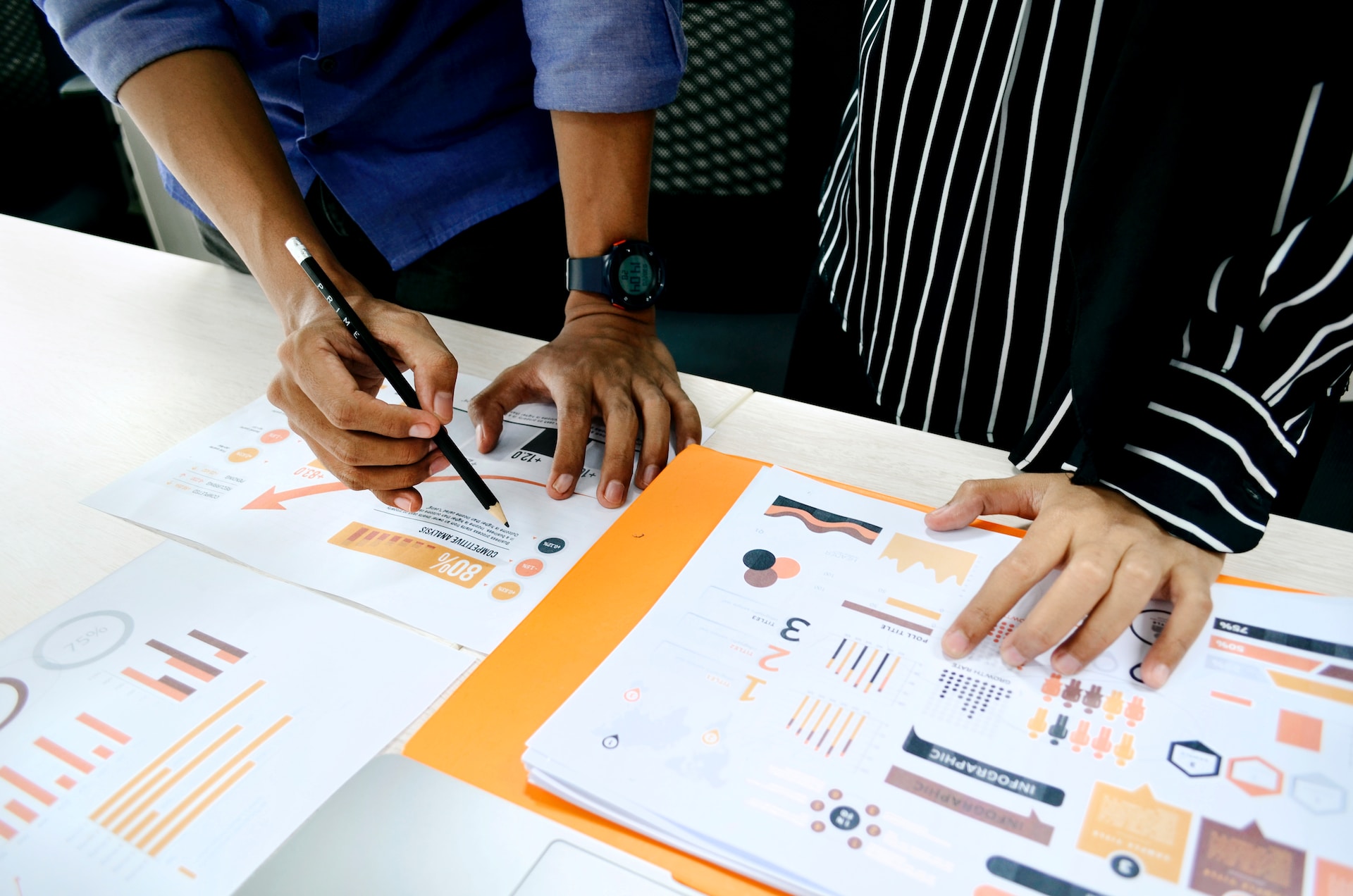