Article
Quality Assurance vs Quality Control: What's the Difference?
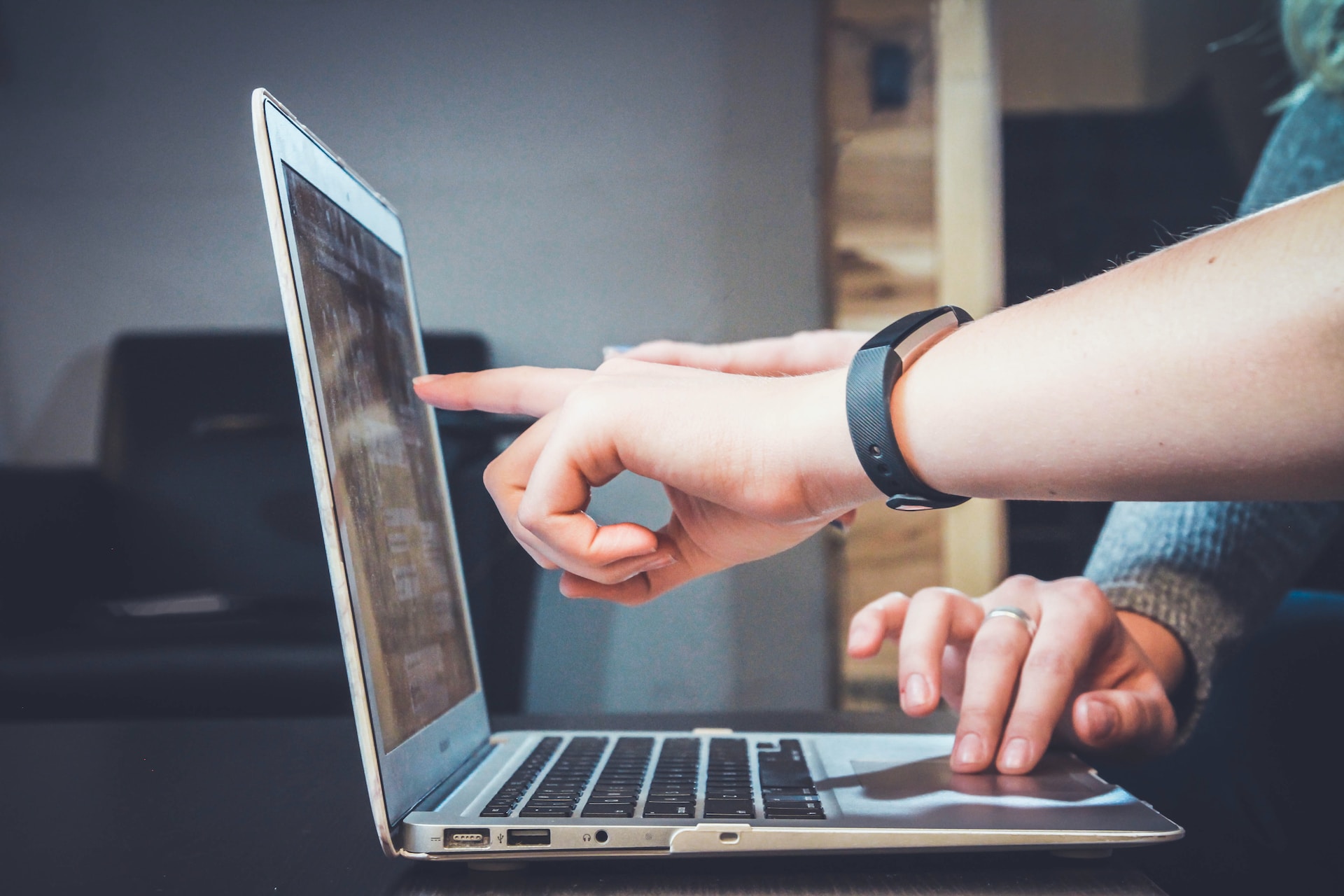
If you're new to quality management, you may find yourself confused by the terms "quality assurance" and "quality control." While these phrases are often used interchangeably, they have different connotations in the world of business. So, what exactly do these terms mean and how do they differ? In this article, we'll explore the nuances of quality assurance and quality control, examine their key differences, and highlight the importance of implementing both into your business strategy.
Understanding Quality Assurance and Quality Control
Before we jump into the specifics, let's define "quality assurance" and "quality control."
Quality assurance and quality control are two essential elements of any successful business. Both are critical to ensuring that a company's products or services meet the highest standards of quality. While they may sound similar, they are actually quite different.
Defining Quality Assurance
Quality assurance is a process of ensuring that the products or services a company provides meet predetermined standards of quality. It involves establishing guidelines, procedures, and systems to guarantee that the end result consistently meets customer expectations. Quality assurance is a proactive approach that focuses on preventing potential issues before they occur.
Quality assurance is essential for any business that wants to ensure customer satisfaction and build a strong reputation. By implementing quality assurance processes, a company can identify and address potential issues before they become major problems. This can save time, money, and resources in the long run.
Some common quality assurance techniques include:
- Developing quality standards and guidelines.
- Implementing quality control processes.
- Conducting regular audits and inspections.
- Providing training and support to employees.
Defining Quality Control
On the other hand, quality control is a method of monitoring product or service quality in order to identify and address issues that arise. It involves inspecting and testing products or services to ensure they meet established quality standards. Quality control is a reactive approach that focuses on identifying and correcting problems after they have occurred.
Quality control is essential for any business that wants to ensure that its products or services meet the highest standards of quality. By implementing quality control processes, a company can identify and address issues quickly, minimizing the impact on customers and the business.
Some common quality control techniques include:
- Inspecting products or services before they are delivered to customers
- Testing products or services to ensure they meet quality standards
- Identifying and addressing issues as they arise
- Providing feedback to employees to improve quality
Overall, both quality assurance and quality control are essential for any business that wants to provide the highest quality products or services to its customers. By implementing these processes, a company can improve customer satisfaction, build a strong reputation, and ultimately achieve long-term success.
Key Differences Between Quality Assurance and Quality Control
Quality assurance (QA) and quality control (QC) are two essential processes for ensuring the quality of a product or service. While the two terms are often used interchangeably, they are distinct processes with different objectives and responsibilities.
Here are some additional details that can help you understand the differences between QA and QC:
Process vs Product
The main difference between QA and QC is their focus. QA focuses on the process of product development or service delivery, while QC focuses on the end result. QA aims to prevent errors from occurring during the development process, while QC seeks to identify and correct errors after the product or service has been completed.
For example, in a software development project, QA would involve testing the code and ensuring that it meets the project requirements, while QC would involve testing the final product to ensure that it works as intended.
Proactive vs Reactive Approach
Another significant difference is the approach taken. QA takes a proactive approach, anticipating issues and creating systems to avoid them. QC, on the other hand, is reactive, identifying problems and fixing them once they occur.
For example, in a manufacturing process, QA would involve setting up systems to ensure that the production line is operating at optimal levels, while QC would involve inspecting the final product and identifying defects.
Responsibility and Roles
The two approaches involve different teams and responsibilities. QA is the responsibility of everyone involved in the product or service development process, from designers to engineers to customer service representatives. Every individual has a duty to ensure that guidelines and procedures are followed.
QC, on the other hand, is primarily the responsibility of the quality control department. This team is responsible for conducting inspections and tests to ensure that the final product or service meets predetermined standards.
It is important to note that while QA and QC have different objectives and responsibilities, they are both critical for ensuring the quality of a product or service. By implementing both processes, organizations can minimize errors, reduce costs, and improve customer satisfaction.
The Importance of Quality Assurance and Quality Control in Business
Quality assurance and quality control are two important aspects of a business that are often overlooked. Quality assurance is the process of ensuring that a product or service meets the specified requirements, while quality control is the process of identifying defects or errors in a product or service. Both of these processes are essential to the success of any business, regardless of its size or industry.
Ensuring Customer Satisfaction
One of the biggest benefits of implementing quality assurance and quality control in your business is the ability to ensure customer satisfaction. By consistently delivering high-quality products or services, you can improve customer satisfaction and increase customer loyalty. This, in turn, can lead to repeat business and positive word-of-mouth marketing.
For example, imagine you run a restaurant. By implementing quality control measures, you can ensure that every dish that leaves your kitchen meets the highest standards of quality. This will not only improve customer satisfaction but also help you build a positive reputation in your community.
Reducing Costs and Increasing Efficiency
Another benefit of quality assurance and quality control is the ability to reduce costs and increase efficiency. By preventing errors from occurring, you can reduce the need for costly rework or redesign. This can save your business time, money, and resources in the long run.
For example, imagine you run a manufacturing plant. By implementing quality assurance measures, you can identify potential defects in your products before they leave the factory floor. This can help you avoid costly recalls or repairs down the line.
Maintaining a Competitive Edge
In today's market, quality is a key differentiator between companies. Businesses that consistently deliver high-quality products or services will stand out from their competitors. By implementing quality assurance and quality control, you can ensure that your products or services meet the highest standards of quality.
For example, imagine you run a software development company. By implementing quality assurance measures, you can ensure that your software is bug-free and meets the needs of your customers. This can help you maintain a competitive edge in the crowded software market.
In conclusion, quality assurance and quality control are essential components of any successful business strategy. By ensuring customer satisfaction, reducing costs and increasing efficiency, and maintaining a competitive edge, you can position your business for long-term success.
Implementing Quality Assurance and Quality Control in Your Organization
To implement quality assurance and quality control in your organization, you will need to establish a quality management system. This system should include:
Establishing a Quality Management System
Your quality management system should include clear guidelines, procedures, and protocols for every stage of the product development or service delivery process. This ensures that everyone involved knows what is expected of them and can consistently meet those expectations.
One of the key components of a quality management system is documentation. It's important to document every step of the process, from initial planning to final delivery. This documentation should include details about the materials used, the processes followed, and any testing or inspections that were conducted.
Another important aspect of a quality management system is risk management. You should identify potential risks and hazards at every stage of the process and take steps to mitigate them. This includes conducting risk assessments, implementing safety procedures, and providing training to employees.
Training and Developing Employees
Your employees are your biggest asset when it comes to quality management. It's important to provide them with the necessary skills and knowledge to implement quality practices effectively. This includes training on quality management systems, quality control methods, and customer service skills.
Training should be an ongoing process, not a one-time event. You should provide regular training sessions to ensure that employees are up-to-date on the latest quality practices and standards. This will help them to identify potential issues and take corrective action before they become major problems.
Employee development is also important. You should provide opportunities for employees to learn new skills and take on new responsibilities. This will help to keep them engaged and motivated, and will also help to ensure that your organization has a strong pipeline of talent for future growth.
Monitoring and Measuring Performance
Finally, you'll need to monitor and measure the performance of your quality management systems. This includes analyzing customer feedback, conducting internal audits, and identifying areas for improvement. By tracking your progress, you can ensure that your quality management system is effective and efficient.
One way to monitor performance is to establish key performance indicators (KPIs). These are metrics that you can use to measure the effectiveness of your quality management system. Examples of KPIs include customer satisfaction ratings, defect rates, and on-time delivery rates.
It's also important to conduct regular audits of your quality management system. This will help you to identify any areas where processes are not being followed correctly or where improvements can be made. Audits can be conducted internally or by a third-party organization.
By implementing a strong quality management system, providing ongoing training and development to employees, and monitoring and measuring performance, you can ensure that your organization consistently delivers high-quality products and services to your customers.
Conclusion
Quality assurance and quality control may seem like confusing terms, but they are vital components of a successful business strategy. By implementing both processes, you can ensure that your products or services meet established standards of quality, reduce costs, and improve customer satisfaction. Remember to establish a quality management system, train and develop your employees, and monitor and measure your performance to ensure that your quality management processes are effective and efficient.
Similar Blog Posts
Article
Quality Assurance vs Quality Control: What's the Difference?
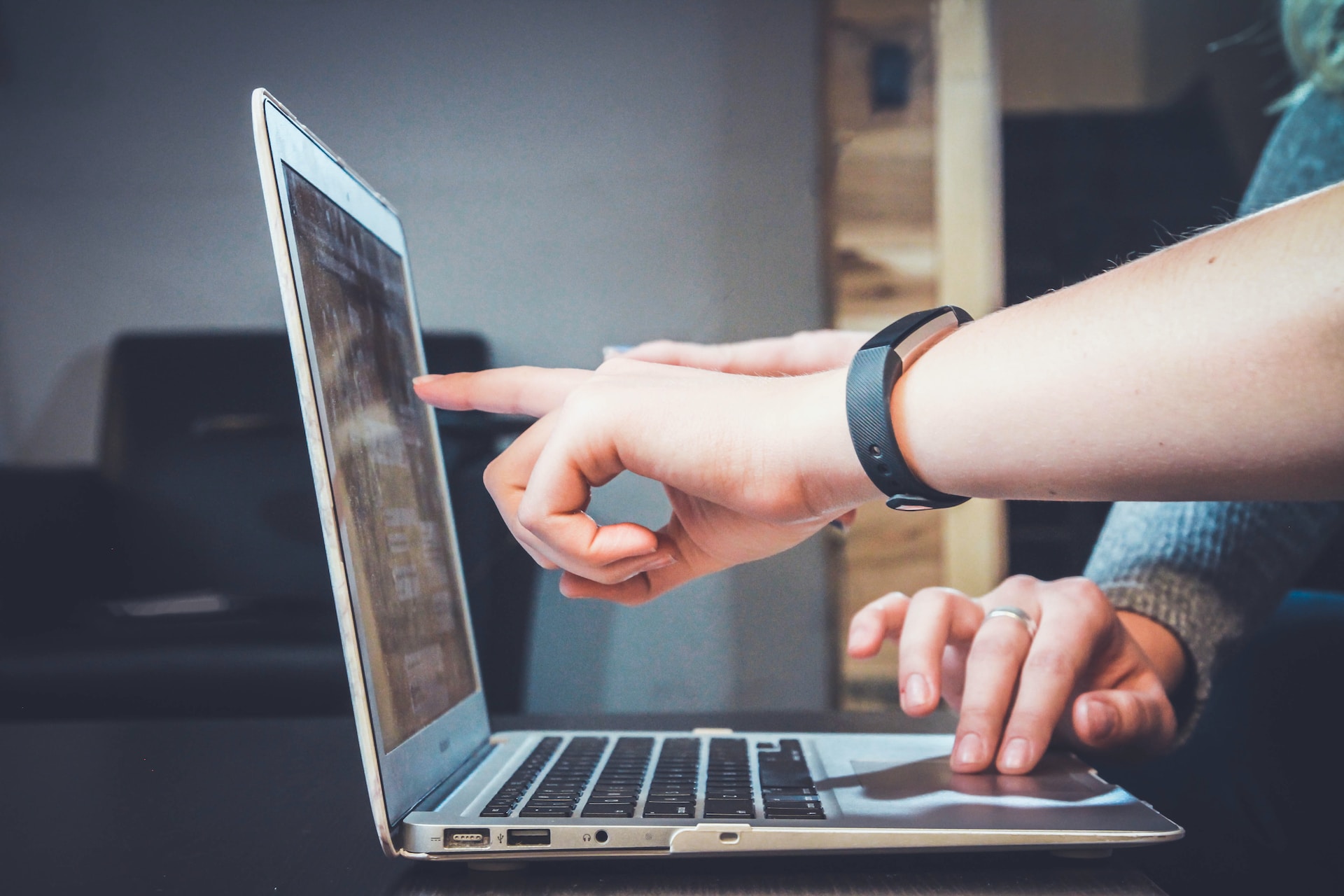
If you're new to quality management, you may find yourself confused by the terms "quality assurance" and "quality control." While these phrases are often used interchangeably, they have different connotations in the world of business. So, what exactly do these terms mean and how do they differ? In this article, we'll explore the nuances of quality assurance and quality control, examine their key differences, and highlight the importance of implementing both into your business strategy.
Understanding Quality Assurance and Quality Control
Before we jump into the specifics, let's define "quality assurance" and "quality control."
Quality assurance and quality control are two essential elements of any successful business. Both are critical to ensuring that a company's products or services meet the highest standards of quality. While they may sound similar, they are actually quite different.
Defining Quality Assurance
Quality assurance is a process of ensuring that the products or services a company provides meet predetermined standards of quality. It involves establishing guidelines, procedures, and systems to guarantee that the end result consistently meets customer expectations. Quality assurance is a proactive approach that focuses on preventing potential issues before they occur.
Quality assurance is essential for any business that wants to ensure customer satisfaction and build a strong reputation. By implementing quality assurance processes, a company can identify and address potential issues before they become major problems. This can save time, money, and resources in the long run.
Some common quality assurance techniques include:
- Developing quality standards and guidelines.
- Implementing quality control processes.
- Conducting regular audits and inspections.
- Providing training and support to employees.
Defining Quality Control
On the other hand, quality control is a method of monitoring product or service quality in order to identify and address issues that arise. It involves inspecting and testing products or services to ensure they meet established quality standards. Quality control is a reactive approach that focuses on identifying and correcting problems after they have occurred.
Quality control is essential for any business that wants to ensure that its products or services meet the highest standards of quality. By implementing quality control processes, a company can identify and address issues quickly, minimizing the impact on customers and the business.
Some common quality control techniques include:
- Inspecting products or services before they are delivered to customers
- Testing products or services to ensure they meet quality standards
- Identifying and addressing issues as they arise
- Providing feedback to employees to improve quality
Overall, both quality assurance and quality control are essential for any business that wants to provide the highest quality products or services to its customers. By implementing these processes, a company can improve customer satisfaction, build a strong reputation, and ultimately achieve long-term success.
Key Differences Between Quality Assurance and Quality Control
Quality assurance (QA) and quality control (QC) are two essential processes for ensuring the quality of a product or service. While the two terms are often used interchangeably, they are distinct processes with different objectives and responsibilities.
Here are some additional details that can help you understand the differences between QA and QC:
Process vs Product
The main difference between QA and QC is their focus. QA focuses on the process of product development or service delivery, while QC focuses on the end result. QA aims to prevent errors from occurring during the development process, while QC seeks to identify and correct errors after the product or service has been completed.
For example, in a software development project, QA would involve testing the code and ensuring that it meets the project requirements, while QC would involve testing the final product to ensure that it works as intended.
Proactive vs Reactive Approach
Another significant difference is the approach taken. QA takes a proactive approach, anticipating issues and creating systems to avoid them. QC, on the other hand, is reactive, identifying problems and fixing them once they occur.
For example, in a manufacturing process, QA would involve setting up systems to ensure that the production line is operating at optimal levels, while QC would involve inspecting the final product and identifying defects.
Responsibility and Roles
The two approaches involve different teams and responsibilities. QA is the responsibility of everyone involved in the product or service development process, from designers to engineers to customer service representatives. Every individual has a duty to ensure that guidelines and procedures are followed.
QC, on the other hand, is primarily the responsibility of the quality control department. This team is responsible for conducting inspections and tests to ensure that the final product or service meets predetermined standards.
It is important to note that while QA and QC have different objectives and responsibilities, they are both critical for ensuring the quality of a product or service. By implementing both processes, organizations can minimize errors, reduce costs, and improve customer satisfaction.
The Importance of Quality Assurance and Quality Control in Business
Quality assurance and quality control are two important aspects of a business that are often overlooked. Quality assurance is the process of ensuring that a product or service meets the specified requirements, while quality control is the process of identifying defects or errors in a product or service. Both of these processes are essential to the success of any business, regardless of its size or industry.
Ensuring Customer Satisfaction
One of the biggest benefits of implementing quality assurance and quality control in your business is the ability to ensure customer satisfaction. By consistently delivering high-quality products or services, you can improve customer satisfaction and increase customer loyalty. This, in turn, can lead to repeat business and positive word-of-mouth marketing.
For example, imagine you run a restaurant. By implementing quality control measures, you can ensure that every dish that leaves your kitchen meets the highest standards of quality. This will not only improve customer satisfaction but also help you build a positive reputation in your community.
Reducing Costs and Increasing Efficiency
Another benefit of quality assurance and quality control is the ability to reduce costs and increase efficiency. By preventing errors from occurring, you can reduce the need for costly rework or redesign. This can save your business time, money, and resources in the long run.
For example, imagine you run a manufacturing plant. By implementing quality assurance measures, you can identify potential defects in your products before they leave the factory floor. This can help you avoid costly recalls or repairs down the line.
Maintaining a Competitive Edge
In today's market, quality is a key differentiator between companies. Businesses that consistently deliver high-quality products or services will stand out from their competitors. By implementing quality assurance and quality control, you can ensure that your products or services meet the highest standards of quality.
For example, imagine you run a software development company. By implementing quality assurance measures, you can ensure that your software is bug-free and meets the needs of your customers. This can help you maintain a competitive edge in the crowded software market.
In conclusion, quality assurance and quality control are essential components of any successful business strategy. By ensuring customer satisfaction, reducing costs and increasing efficiency, and maintaining a competitive edge, you can position your business for long-term success.
Implementing Quality Assurance and Quality Control in Your Organization
To implement quality assurance and quality control in your organization, you will need to establish a quality management system. This system should include:
Establishing a Quality Management System
Your quality management system should include clear guidelines, procedures, and protocols for every stage of the product development or service delivery process. This ensures that everyone involved knows what is expected of them and can consistently meet those expectations.
One of the key components of a quality management system is documentation. It's important to document every step of the process, from initial planning to final delivery. This documentation should include details about the materials used, the processes followed, and any testing or inspections that were conducted.
Another important aspect of a quality management system is risk management. You should identify potential risks and hazards at every stage of the process and take steps to mitigate them. This includes conducting risk assessments, implementing safety procedures, and providing training to employees.
Training and Developing Employees
Your employees are your biggest asset when it comes to quality management. It's important to provide them with the necessary skills and knowledge to implement quality practices effectively. This includes training on quality management systems, quality control methods, and customer service skills.
Training should be an ongoing process, not a one-time event. You should provide regular training sessions to ensure that employees are up-to-date on the latest quality practices and standards. This will help them to identify potential issues and take corrective action before they become major problems.
Employee development is also important. You should provide opportunities for employees to learn new skills and take on new responsibilities. This will help to keep them engaged and motivated, and will also help to ensure that your organization has a strong pipeline of talent for future growth.
Monitoring and Measuring Performance
Finally, you'll need to monitor and measure the performance of your quality management systems. This includes analyzing customer feedback, conducting internal audits, and identifying areas for improvement. By tracking your progress, you can ensure that your quality management system is effective and efficient.
One way to monitor performance is to establish key performance indicators (KPIs). These are metrics that you can use to measure the effectiveness of your quality management system. Examples of KPIs include customer satisfaction ratings, defect rates, and on-time delivery rates.
It's also important to conduct regular audits of your quality management system. This will help you to identify any areas where processes are not being followed correctly or where improvements can be made. Audits can be conducted internally or by a third-party organization.
By implementing a strong quality management system, providing ongoing training and development to employees, and monitoring and measuring performance, you can ensure that your organization consistently delivers high-quality products and services to your customers.
Conclusion
Quality assurance and quality control may seem like confusing terms, but they are vital components of a successful business strategy. By implementing both processes, you can ensure that your products or services meet established standards of quality, reduce costs, and improve customer satisfaction. Remember to establish a quality management system, train and develop your employees, and monitor and measure your performance to ensure that your quality management processes are effective and efficient.
Article
Quality Assurance vs Quality Control: What's the Difference?
•
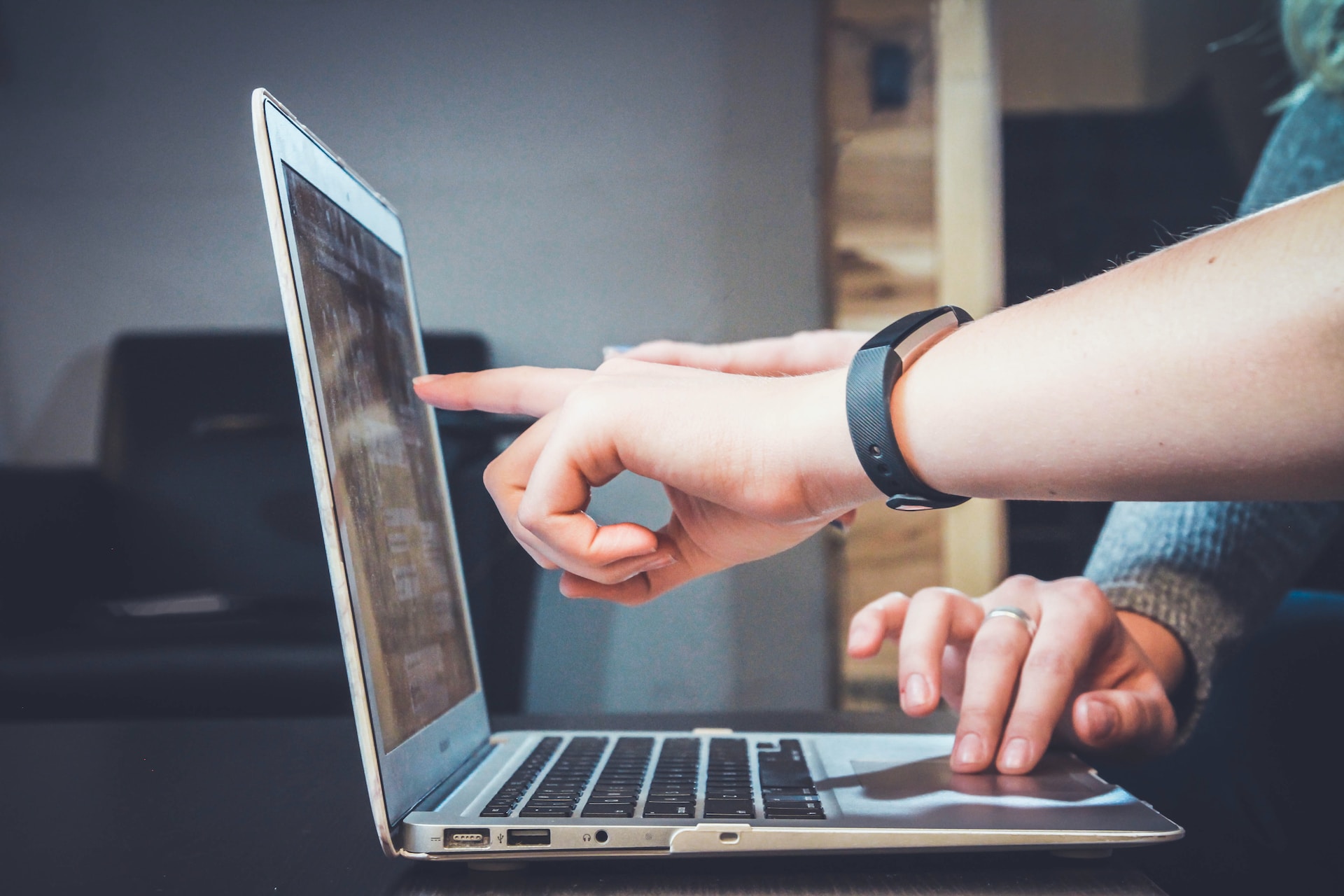