Article
A Comprehensive Guide to Process Management
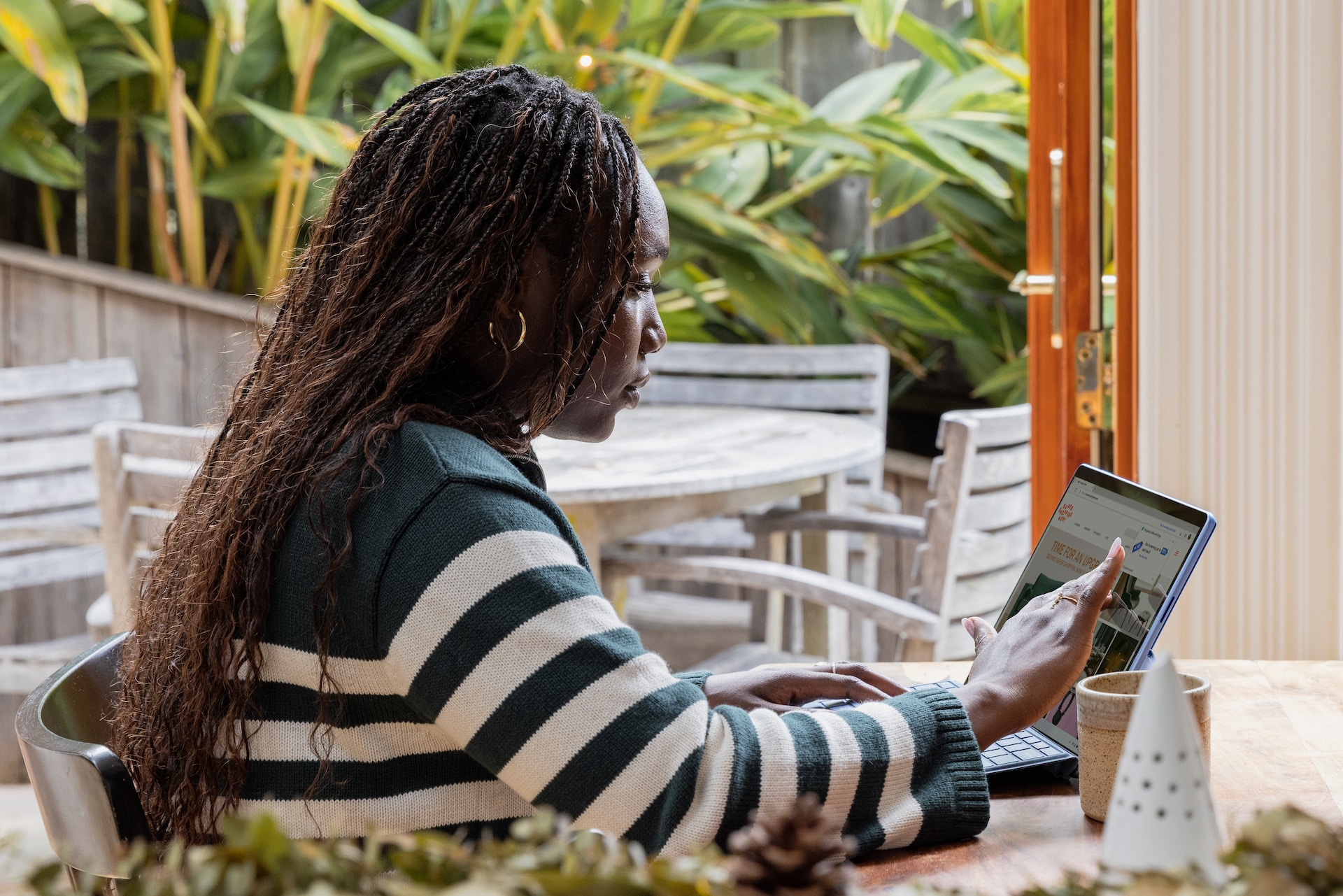
If you run a business, it's highly likely that you've heard the phrase "process management" before. But what exactly does this term mean, and how does it apply to your company? In this comprehensive guide, we'll explore the ins and outs of process management, from its definition and importance to its key components and benefits. We'll also delve into popular process management methodologies like Lean and Six Sigma, and explore the process mapping and analysis techniques that can be used to improve your company's overall performance. So, let's get started!
Understanding Process Management
Process management is all about controlling and improving the efficiency of your business operations. Essentially, it involves the act of analyzing, documenting, and refining all the various processes that your company uses to get work done. By doing so, you can ensure that these processes are as streamlined and efficient as possible — ultimately resulting in better products, happier customers, and higher profits. Let's dive deeper into the world of process management.
Definition and Importance of Process Management
In simple terms, process management involves the systematic approach to mapping, designing, implementing, monitoring, and refining business processes to reach their fullest potential. This is a critical aspect of business management because it leads to more effective use of time, resources, and materials, as well as an increase in overall productivity and profitability.
Process management is essential for any business that wants to stay competitive in today's fast-paced market. It allows companies to identify inefficiencies in their operations and make necessary adjustments to improve their performance. By doing so, businesses can reduce costs, increase customer satisfaction, and ultimately, grow their bottom line.
In addition, having well-defined processes makes it easier for organizations to detect errors, spot areas that need improvement, and make adjustments as needed. Without effective process management, businesses often experience missed deadlines, reduced output quality, higher costs, and lower customer satisfaction levels.
Key Components of Process Management
Process management has several key components that serve as the building blocks for effective implementation. These include process design, process modeling, process execution, process monitoring, and process optimization. Let's take a closer look at each:
- Process Design: This phase involves identifying and defining business processes based on the goals of the organization, the needs of its customers, and other relevant factors. During this phase, businesses must consider the various steps involved in each process and determine the most efficient way to complete them.
- Process Modeling: In this step, stakeholders analyze and develop a visual representation of the design, documenting key steps that need to be taken in order to execute the process effectively. This phase often involves the use of flowcharts and other visual aids to help stakeholders understand how the process works.
- Process Execution: This involves putting the process model to work and measuring its effectiveness in real-world practice. During this phase, businesses must ensure that the process is being executed as designed and that it is producing the desired results.
- Process Monitoring: During this step, businesses keep track of the process performance and make necessary adjustments to improve its efficiency and effectiveness. This phase often involves the use of key performance indicators (KPIs) to measure the success of the process and identify areas for improvement.
- Process Optimization: Finally, process optimization involves taking the best-performing processes and improving them even further, streamlining them for maximum return on investment. This phase often involves the use of automation and other technologies to further improve the efficiency of the process.
These components work together to form a continuous cycle of improvement, allowing businesses to refine and optimize their operations over time.
Benefits of Effective Process Management
Effective process management has numerous advantages for businesses, including:
- Improved efficiency and productivity: Well-designed processes reduce the likelihood of errors, delays, and unproductive activities, leading to more output in less time. This can help businesses to meet deadlines, increase output, and ultimately, grow their bottom line.
- Increased customer satisfaction: Efficient processes lead to better product quality, faster delivery times, and improved communication, all of which customers appreciate and tend to reward with repeat business. By improving customer satisfaction, businesses can increase their customer base and build a strong reputation in their industry.
- Reduced costs: Optimized processes lead to fewer resources spent on wasted time and materials, resulting in lower costs and higher profits. By reducing costs, businesses can increase their profit margins and reinvest those savings into other areas of the business.
- Faster growth: Well-structured processes provide a solid foundation for growth, allowing businesses to scale and expand more easily while maintaining high levels of quality and customer satisfaction. By improving their processes, businesses can position themselves for future growth and success.
Overall, effective process management is essential for any business that wants to stay competitive in today's fast-paced market. By analyzing, documenting, and refining their processes, businesses can improve their efficiency, reduce costs, increase customer satisfaction, and ultimately, grow their bottom line.
Process Management Methodologies
Of course, there are many different approaches to process management, each with its unique strengths and weaknesses. Let's explore some of the most popular methodologies and frameworks:
Lean Process Management
Lean is a methodology that is focused on identifying and eliminating non-value-added activities in business operations. It is centered around principles such as continuous improvement, respect for people, and waste reduction. Implementing Lean processes results in streamlined and efficient operations, with minimal waste and maximum productivity.
Six Sigma
Six Sigma is a methodology that strives for near-perfect performance levels, aiming to reduce defects and errors in operations to less than 3.4 per million. This is achieved through data-driven analysis and process improvement techniques that allow organizations to identify and eliminate errors in their workflows.
Total Quality Management (TQM)
TQM is an all-encompassing approach to business management that emphasizes the involvement of every member in the organization in the pursuit of high-quality products and services. It is based on continuous improvement, customer focus, employee involvement, and systematic problem-solving. Implementing TQM results in improved quality and reduced costs, as well as happier and more engaged employees.
Business Process Reengineering (BPR)
BPR is a strategy that involves rethinking and redesigning business processes from scratch, with the goal of achieving radical improvement in performance and efficiency. It involves taking a holistic approach to process management, analyzing and re-engineering entire workflows rather than simply optimizing individual steps. Successful implementation of this method can lead to step-change improvements in efficiency and productivity, but it requires a significant investment of time, resources, and capital.
Process Mapping and Documentation
One of the most fundamental aspects of process management is process mapping and documentation. This involves creating detailed maps of the various steps involved in a process and documenting best practices for each activity. There are several types of process maps, and each one serves a unique purpose:
Types of Process Maps
- Flowchart: A flowchart is a visual representation of a process, demonstrating the sequence of steps using symbols and arrows to indicate where decisions need to be made.
- Value Stream Map: This type of map provides a high-level overview of an entire process, focusing on the value-added and non-value-added activities.
- SIPOC Diagram: SIPOC (Supplier-Input-Process-Output-Customer) diagrams are used to define the boundaries of a process and to identify the key elements.
- Swimlane Flowchart: A swimlane flowchart is similar to a flowchart, but it also includes swimlanes that divide the chart into categories, such as different departments or participants in the process.
Creating a process map can provide a clear understanding of how each step of a process contributes to overall performance, and can reveal areas where improvements can be made.
Creating a Process Map
When creating a process map, it's important to keep the following steps in mind:
- Identify the process you want to map and the boundaries of that process.
- Interview and involve all stakeholders in the process.
- Identify the order of the steps in the process using a flowchart or other mapping tool.
- Add relevant details such as decision points, data inputs and outputs, and key metrics relevant to the process.
- Review the process map with stakeholders and identify areas for improvement.
Documenting Processes and Procedures
Documenting processes and procedures is an essential part of process management. It helps ensure that everyone in the organization understands the steps involved in a given process and can perform those steps consistently. Documentation might include written guides, video tutorials, or interactive manuals. It should be updated regularly and reviewed by all stakeholders to ensure it remains accurate and relevant.
Maintaining and Updating Process Documentation
Just as processes evolve over time, so too must documentation. Regularly reviewing and updating documentation is essential to ensure that it remains accurate. In addition, regular review allows you to identify bottlenecks and areas for improvement and implement changes that increase the efficiency and effectiveness of your processes.
Process Analysis and Improvement
Finally, the most important part of process management is the process of analyzing and improving processes. This involves taking a deep dive into each step of a process to identify inefficiencies or obstacles that can be improved. The following steps can help organizations to identify possible areas for improvement:
Identifying Process Inefficiencies
To identify inefficiencies in processes, it's essential to have a clear understanding of the process in question. This can be achieved through a combination of process mapping, documentation, and stakeholder interviews. Once you have a clear understanding of the process, you can start to looking for areas of inefficiency. This might include searching for steps that take longer than necessary, redundant steps, or communication failures.
Root Cause Analysis Techniques
To get to the bottom of inefficiencies, it can be helpful to use root cause analysis techniques like the Five Whys method or Fishbone diagrams.
- The Five Whys method is a questioning technique that involves asking "why" several times to get to the underlying cause of a particular problem.
- A Fishbone diagram, also known as an Ishikawa diagram or cause-and-effect diagram, is a visual tool used to identify the root causes of problems in order to solve them more effectively. It does this by illustrating the various causes of a problem and showing how they contribute to the issue at hand.
Implementing Process Improvements
Once you've identified areas for improvement, it's time to put your plan into action. This might involve reorganizing the process, eliminating steps, or introducing new technology. It's important to have a clear plan of action and to involve all stakeholders in the process of implementing change.
Measuring and Monitoring Process Performance
Finally, it's important to measure and monitor the performance of your processes on an ongoing basis. This involves identifying key metrics that impact process performance and tracking those metrics over time. By doing so, you can get a clear picture of how well your processes are performing and where improvements can be made.
Conclusion
Effective process management is essential for businesses that want to operate at peak efficiency and drive their growth and profitability. By understanding the key components of process management, exploring different methodologies, and implementing best practices for process mapping, documentation, and analysis, you can optimize your business operations and achieve your goals in a highly competitive market. Remember, process management is a continuous cycle- one that requires constant analysis, feedback, and improvement. By staying vigilant, your company can stay ahead of the curve and achieve success for years to come.
Article
A Comprehensive Guide to Process Management
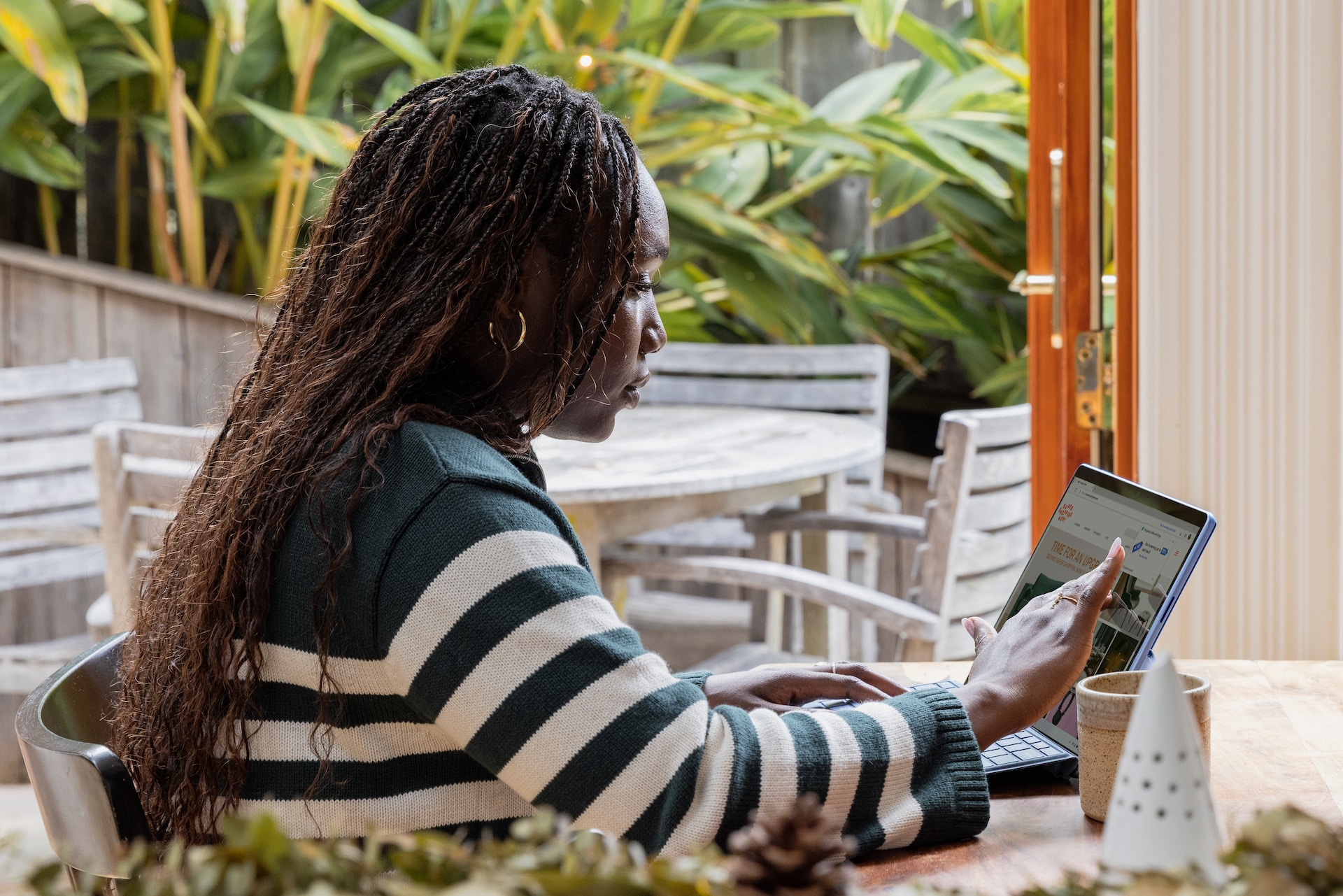
If you run a business, it's highly likely that you've heard the phrase "process management" before. But what exactly does this term mean, and how does it apply to your company? In this comprehensive guide, we'll explore the ins and outs of process management, from its definition and importance to its key components and benefits. We'll also delve into popular process management methodologies like Lean and Six Sigma, and explore the process mapping and analysis techniques that can be used to improve your company's overall performance. So, let's get started!
Understanding Process Management
Process management is all about controlling and improving the efficiency of your business operations. Essentially, it involves the act of analyzing, documenting, and refining all the various processes that your company uses to get work done. By doing so, you can ensure that these processes are as streamlined and efficient as possible — ultimately resulting in better products, happier customers, and higher profits. Let's dive deeper into the world of process management.
Definition and Importance of Process Management
In simple terms, process management involves the systematic approach to mapping, designing, implementing, monitoring, and refining business processes to reach their fullest potential. This is a critical aspect of business management because it leads to more effective use of time, resources, and materials, as well as an increase in overall productivity and profitability.
Process management is essential for any business that wants to stay competitive in today's fast-paced market. It allows companies to identify inefficiencies in their operations and make necessary adjustments to improve their performance. By doing so, businesses can reduce costs, increase customer satisfaction, and ultimately, grow their bottom line.
In addition, having well-defined processes makes it easier for organizations to detect errors, spot areas that need improvement, and make adjustments as needed. Without effective process management, businesses often experience missed deadlines, reduced output quality, higher costs, and lower customer satisfaction levels.
Key Components of Process Management
Process management has several key components that serve as the building blocks for effective implementation. These include process design, process modeling, process execution, process monitoring, and process optimization. Let's take a closer look at each:
- Process Design: This phase involves identifying and defining business processes based on the goals of the organization, the needs of its customers, and other relevant factors. During this phase, businesses must consider the various steps involved in each process and determine the most efficient way to complete them.
- Process Modeling: In this step, stakeholders analyze and develop a visual representation of the design, documenting key steps that need to be taken in order to execute the process effectively. This phase often involves the use of flowcharts and other visual aids to help stakeholders understand how the process works.
- Process Execution: This involves putting the process model to work and measuring its effectiveness in real-world practice. During this phase, businesses must ensure that the process is being executed as designed and that it is producing the desired results.
- Process Monitoring: During this step, businesses keep track of the process performance and make necessary adjustments to improve its efficiency and effectiveness. This phase often involves the use of key performance indicators (KPIs) to measure the success of the process and identify areas for improvement.
- Process Optimization: Finally, process optimization involves taking the best-performing processes and improving them even further, streamlining them for maximum return on investment. This phase often involves the use of automation and other technologies to further improve the efficiency of the process.
These components work together to form a continuous cycle of improvement, allowing businesses to refine and optimize their operations over time.
Benefits of Effective Process Management
Effective process management has numerous advantages for businesses, including:
- Improved efficiency and productivity: Well-designed processes reduce the likelihood of errors, delays, and unproductive activities, leading to more output in less time. This can help businesses to meet deadlines, increase output, and ultimately, grow their bottom line.
- Increased customer satisfaction: Efficient processes lead to better product quality, faster delivery times, and improved communication, all of which customers appreciate and tend to reward with repeat business. By improving customer satisfaction, businesses can increase their customer base and build a strong reputation in their industry.
- Reduced costs: Optimized processes lead to fewer resources spent on wasted time and materials, resulting in lower costs and higher profits. By reducing costs, businesses can increase their profit margins and reinvest those savings into other areas of the business.
- Faster growth: Well-structured processes provide a solid foundation for growth, allowing businesses to scale and expand more easily while maintaining high levels of quality and customer satisfaction. By improving their processes, businesses can position themselves for future growth and success.
Overall, effective process management is essential for any business that wants to stay competitive in today's fast-paced market. By analyzing, documenting, and refining their processes, businesses can improve their efficiency, reduce costs, increase customer satisfaction, and ultimately, grow their bottom line.
Process Management Methodologies
Of course, there are many different approaches to process management, each with its unique strengths and weaknesses. Let's explore some of the most popular methodologies and frameworks:
Lean Process Management
Lean is a methodology that is focused on identifying and eliminating non-value-added activities in business operations. It is centered around principles such as continuous improvement, respect for people, and waste reduction. Implementing Lean processes results in streamlined and efficient operations, with minimal waste and maximum productivity.
Six Sigma
Six Sigma is a methodology that strives for near-perfect performance levels, aiming to reduce defects and errors in operations to less than 3.4 per million. This is achieved through data-driven analysis and process improvement techniques that allow organizations to identify and eliminate errors in their workflows.
Total Quality Management (TQM)
TQM is an all-encompassing approach to business management that emphasizes the involvement of every member in the organization in the pursuit of high-quality products and services. It is based on continuous improvement, customer focus, employee involvement, and systematic problem-solving. Implementing TQM results in improved quality and reduced costs, as well as happier and more engaged employees.
Business Process Reengineering (BPR)
BPR is a strategy that involves rethinking and redesigning business processes from scratch, with the goal of achieving radical improvement in performance and efficiency. It involves taking a holistic approach to process management, analyzing and re-engineering entire workflows rather than simply optimizing individual steps. Successful implementation of this method can lead to step-change improvements in efficiency and productivity, but it requires a significant investment of time, resources, and capital.
Process Mapping and Documentation
One of the most fundamental aspects of process management is process mapping and documentation. This involves creating detailed maps of the various steps involved in a process and documenting best practices for each activity. There are several types of process maps, and each one serves a unique purpose:
Types of Process Maps
- Flowchart: A flowchart is a visual representation of a process, demonstrating the sequence of steps using symbols and arrows to indicate where decisions need to be made.
- Value Stream Map: This type of map provides a high-level overview of an entire process, focusing on the value-added and non-value-added activities.
- SIPOC Diagram: SIPOC (Supplier-Input-Process-Output-Customer) diagrams are used to define the boundaries of a process and to identify the key elements.
- Swimlane Flowchart: A swimlane flowchart is similar to a flowchart, but it also includes swimlanes that divide the chart into categories, such as different departments or participants in the process.
Creating a process map can provide a clear understanding of how each step of a process contributes to overall performance, and can reveal areas where improvements can be made.
Creating a Process Map
When creating a process map, it's important to keep the following steps in mind:
- Identify the process you want to map and the boundaries of that process.
- Interview and involve all stakeholders in the process.
- Identify the order of the steps in the process using a flowchart or other mapping tool.
- Add relevant details such as decision points, data inputs and outputs, and key metrics relevant to the process.
- Review the process map with stakeholders and identify areas for improvement.
Documenting Processes and Procedures
Documenting processes and procedures is an essential part of process management. It helps ensure that everyone in the organization understands the steps involved in a given process and can perform those steps consistently. Documentation might include written guides, video tutorials, or interactive manuals. It should be updated regularly and reviewed by all stakeholders to ensure it remains accurate and relevant.
Maintaining and Updating Process Documentation
Just as processes evolve over time, so too must documentation. Regularly reviewing and updating documentation is essential to ensure that it remains accurate. In addition, regular review allows you to identify bottlenecks and areas for improvement and implement changes that increase the efficiency and effectiveness of your processes.
Process Analysis and Improvement
Finally, the most important part of process management is the process of analyzing and improving processes. This involves taking a deep dive into each step of a process to identify inefficiencies or obstacles that can be improved. The following steps can help organizations to identify possible areas for improvement:
Identifying Process Inefficiencies
To identify inefficiencies in processes, it's essential to have a clear understanding of the process in question. This can be achieved through a combination of process mapping, documentation, and stakeholder interviews. Once you have a clear understanding of the process, you can start to looking for areas of inefficiency. This might include searching for steps that take longer than necessary, redundant steps, or communication failures.
Root Cause Analysis Techniques
To get to the bottom of inefficiencies, it can be helpful to use root cause analysis techniques like the Five Whys method or Fishbone diagrams.
- The Five Whys method is a questioning technique that involves asking "why" several times to get to the underlying cause of a particular problem.
- A Fishbone diagram, also known as an Ishikawa diagram or cause-and-effect diagram, is a visual tool used to identify the root causes of problems in order to solve them more effectively. It does this by illustrating the various causes of a problem and showing how they contribute to the issue at hand.
Implementing Process Improvements
Once you've identified areas for improvement, it's time to put your plan into action. This might involve reorganizing the process, eliminating steps, or introducing new technology. It's important to have a clear plan of action and to involve all stakeholders in the process of implementing change.
Measuring and Monitoring Process Performance
Finally, it's important to measure and monitor the performance of your processes on an ongoing basis. This involves identifying key metrics that impact process performance and tracking those metrics over time. By doing so, you can get a clear picture of how well your processes are performing and where improvements can be made.
Conclusion
Effective process management is essential for businesses that want to operate at peak efficiency and drive their growth and profitability. By understanding the key components of process management, exploring different methodologies, and implementing best practices for process mapping, documentation, and analysis, you can optimize your business operations and achieve your goals in a highly competitive market. Remember, process management is a continuous cycle- one that requires constant analysis, feedback, and improvement. By staying vigilant, your company can stay ahead of the curve and achieve success for years to come.
Article
A Comprehensive Guide to Process Management
•
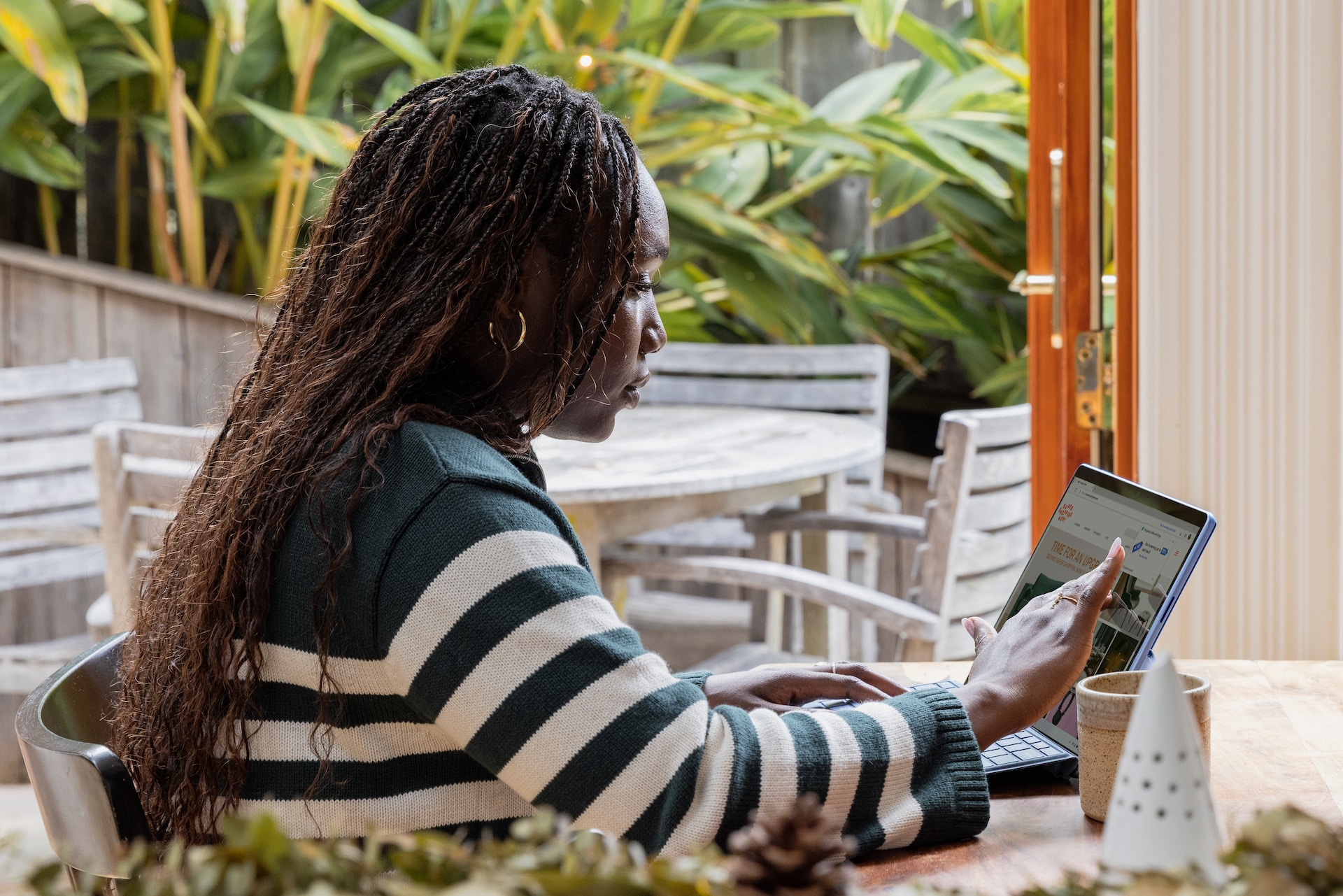