Article
Process Mapping: A Comprehensive Guide to Streamlining Your Business
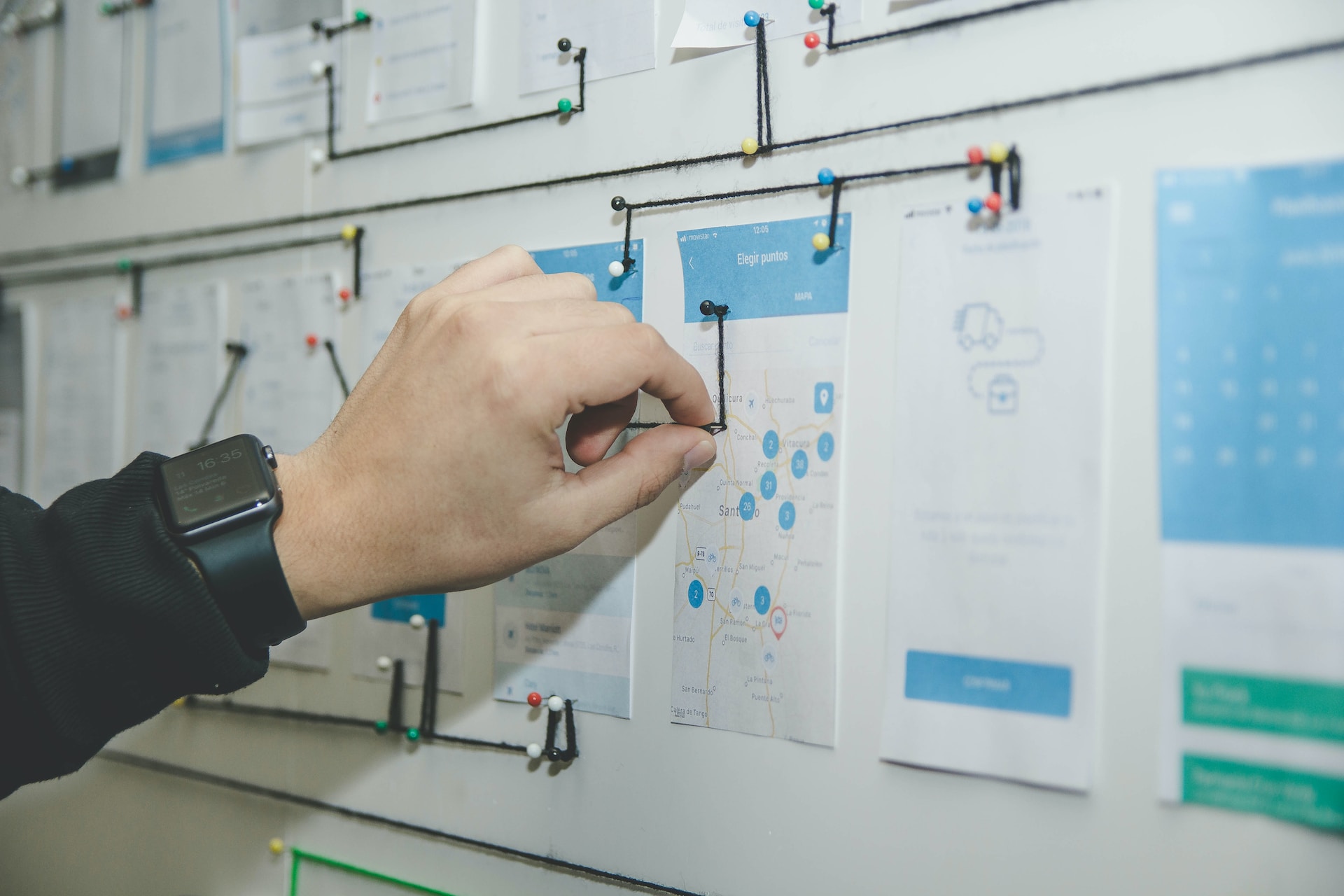
As a business owner or manager, optimizing your operations is always a priority. One powerful technique for streamlining business processes is process mapping. This comprehensive guide will walk you through what process mapping is, its importance in business, the types of process maps you can create, and how to create them.
Understanding Process Mapping
What is Process Mapping?
Process mapping is a visual representation of a business process, often created with a flowchart or diagram. The purpose of a process map is to identify inefficiencies, redundancies, and bottlenecks in a process. By understanding how a process works, managers can identify opportunities for improvement and create a more streamlined and efficient process.
Process mapping is a valuable tool for businesses of all sizes and industries. It can be used to map out any process, from manufacturing and production to customer service and sales. The process map provides a clear and concise overview of the process, making it easier for managers to identify areas of improvement.
The Importance of Process Mapping in Business
When it comes to running a successful business, efficiency is key. Wasted time, effort, and resources can all contribute to decreased productivity and lost profits. Process mapping helps businesses identify areas of inefficiency and waste so they can improve operations and increase profitability.
Process mapping also helps businesses to standardize their processes. By creating a visual representation of the process, everyone involved in the process can see how it works and understand their role in it. This makes it easier to train new employees and ensures that everyone is following the same process.
Key Components of Process Mapping
The key components of process mapping include process owners, stakeholders, inputs, outputs, and process steps. Process owners are responsible for the entire process, while stakeholders are individuals or groups who have an interest or involvement in the process. Inputs and outputs are the materials or information that are used or produced during the process. Finally, process steps are the individual actions or decisions that take place during the process.
Process mapping is an iterative process, meaning that it is constantly being reviewed and improved. As the process is mapped out, managers can identify areas of improvement and make changes to the process. This process of continuous improvement helps businesses to stay competitive and adapt to changing market conditions.
In conclusion, process mapping is a valuable tool for businesses looking to improve efficiency and increase profitability. By creating a visual representation of a process, managers can identify areas of inefficiency and waste, standardize processes, and continuously improve operations.
Types of Process Maps
Process maps are visual representations of a process that help in identifying areas of improvement and inefficiencies. They provide a clear understanding of the process, making it easier to optimize and streamline it. There are different types of process maps, each with a unique purpose. Let's explore some of the most commonly used process maps:
Flowcharts
Flowcharts are the most commonly used type of process map. They are visual diagrams that show the steps of a process, using symbols to represent each step. With flowcharts, you can easily identify decision points, delays, and potential inefficiencies in the process. They're popular options for business process mapping.
For instance, a flowchart can be used to depict the process of manufacturing a product. The flowchart can start with the raw materials, and then move on to the various stages of production, such as design, assembly, quality control, and packaging. By analyzing the flowchart, you can identify bottlenecks and areas where the process can be improved.
Swimlane Diagrams
Swimlane diagrams are similar to flowcharts but are organized by department or function. The swimlanes represent different areas of responsibility, allowing for a more detailed and comprehensive map of the process.
For example, a swimlane diagram can be used to depict the hiring process in an organization. The swimlanes can represent the different departments involved in the process, such as HR, the hiring manager, and the finance department. By analyzing the swimlane diagram, you can identify areas where the process can be improved, such as reducing the time taken to fill a position.
Value Stream Maps
Value stream maps are used to analyze the flow of materials and information during a process. They focus on identifying areas of waste and non-value-added activities, helping to optimize the flow of materials and increase productivity.
For instance, a value stream map can be used to depict the process of delivering a product to a customer. The value stream map can start with the customer order, and then move on to the various stages of production, such as design, manufacturing, and delivery. By analyzing the value stream map, you can identify areas where the process can be improved, such as reducing lead times and eliminating waste.
SIPOC Diagrams
SIPOC diagrams are high-level process maps that visualize the process from start to finish. They show the suppliers, inputs, process, outputs, and customers involved in the process, helping to identify areas of waste and inefficiency.
For example, a SIPOC diagram can be used to depict the process of developing a new product. The SIPOC diagram can start with the suppliers of raw materials, move on to the inputs required for the process, such as design, manufacturing, and testing, and then move on to the outputs, such as the finished product. By analyzing the SIPOC diagram, you can identify areas where the process can be improved, such as reducing the time taken to develop a new product and improving the quality of the finished product.
Steps to Create a Process Map
If you don't already have process mapping tools, here's a step-by-step guide to creating a process map:
Define the Process Scope
The first step in creating a process map is to define the scope of the process. This involves determining the start and end points, as well as the inputs, outputs, and stakeholders involved in the process.
For example, if the process is related to product development, the scope may include defining the start point as the conceptualization of the product idea and the end point as the product launch. Inputs may include market research and customer feedback, while outputs may include a fully developed and tested product. Stakeholders may include product managers, engineers, marketing teams, and customers.
Gather Information and Identify Stakeholders
Next, gather information about the process by talking to the individuals involved and reviewing any existing documentation. Identify all stakeholders, including those who own the process and those who are affected by it.
For example, if the process is related to employee onboarding, gather information by talking to HR representatives, hiring managers, and new employees. Identify stakeholders such as the HR department, hiring managers, new employees, and existing employees who may need to work with the new hires.
Map the Process Steps
With the information gathered, create a rough draft of the process map, using symbols or shapes to represent each step. Focus on clarity and simplicity, breaking down complex steps into smaller, more manageable parts.
For example, if the process is related to software development, map the steps involved in the development cycle, such as requirements gathering, design, coding, testing, and deployment. Break down each step into smaller parts, such as creating a design document, writing code, and conducting unit tests.
Analyze the Process Map
Once the rough draft is complete, analyze the process map for inefficiencies, redundancies, and bottlenecks. Identify areas where improvements can be made, and brainstorm potential solutions with stakeholders.
For example, if the process is related to customer service, analyze the process map to identify areas where customers may experience long wait times or delays in getting their issues resolved. Brainstorm potential solutions with customer service representatives, such as implementing a chatbot to handle common inquiries or providing additional training for representatives to handle complex issues more efficiently.
Implement Improvements and Monitor Progress
With a plan in place, implement the identified improvements and monitor progress to ensure they are effective. Continuously evaluate the process and update the process map as needed to maintain a streamlined and efficient operation.
For example, if the process is related to supply chain management, implement improvements such as automating inventory tracking or streamlining the order fulfillment process. Monitor progress by analyzing metrics such as order processing time and inventory accuracy, and update the process map as needed to reflect any changes or improvements.
Conclusion
Process mapping is a powerful technique for streamlining business processes, identifying inefficiencies, and increasing profitability. By creating a visual representation of a process, businesses can easily identify areas for improvement and implement effective solutions. By following the steps outlined in this comprehensive guide, you can create effective process maps that help you optimize your operations and achieve success in your business.
Similar Blog Posts
Article
Process Mapping: A Comprehensive Guide to Streamlining Your Business
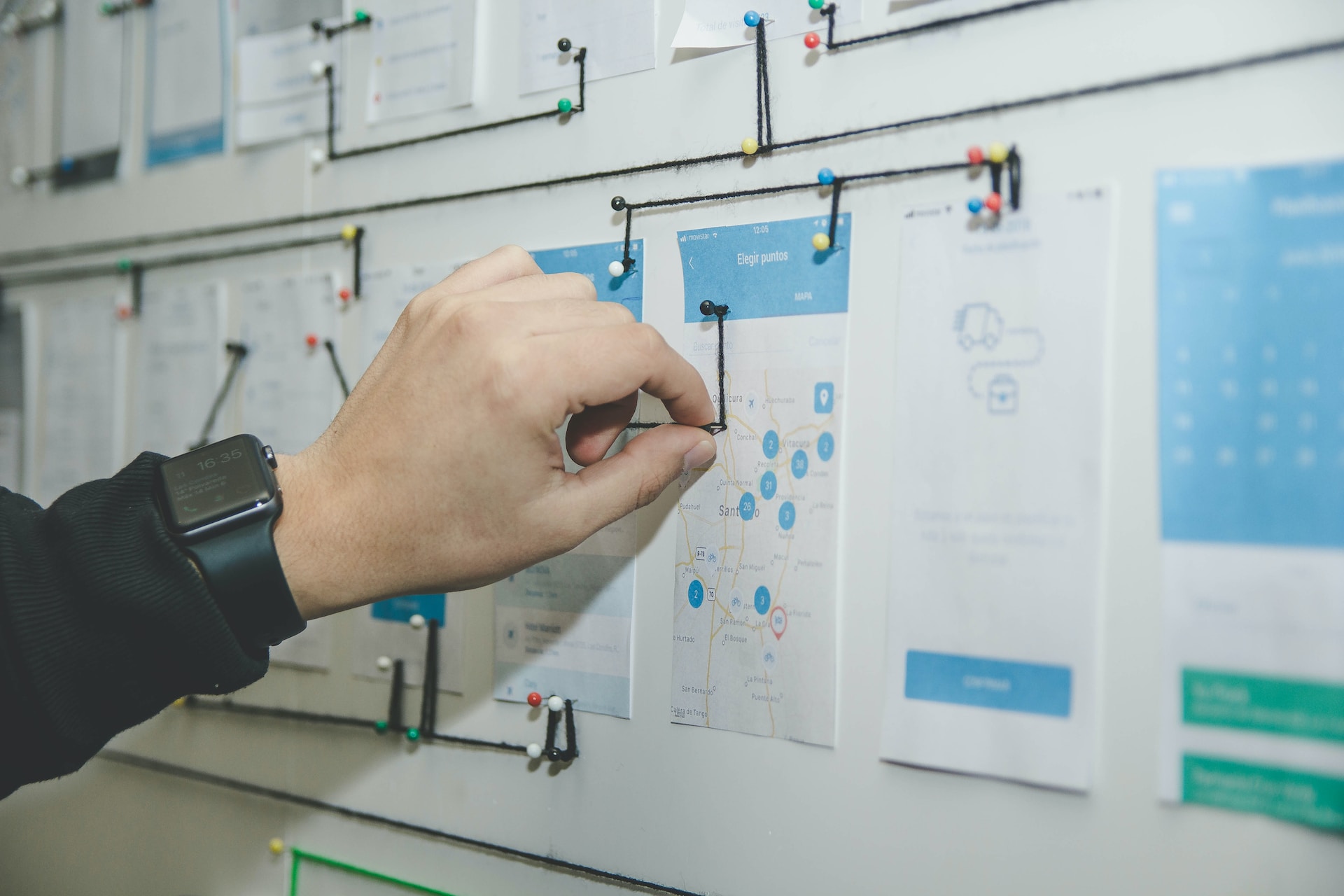
As a business owner or manager, optimizing your operations is always a priority. One powerful technique for streamlining business processes is process mapping. This comprehensive guide will walk you through what process mapping is, its importance in business, the types of process maps you can create, and how to create them.
Understanding Process Mapping
What is Process Mapping?
Process mapping is a visual representation of a business process, often created with a flowchart or diagram. The purpose of a process map is to identify inefficiencies, redundancies, and bottlenecks in a process. By understanding how a process works, managers can identify opportunities for improvement and create a more streamlined and efficient process.
Process mapping is a valuable tool for businesses of all sizes and industries. It can be used to map out any process, from manufacturing and production to customer service and sales. The process map provides a clear and concise overview of the process, making it easier for managers to identify areas of improvement.
The Importance of Process Mapping in Business
When it comes to running a successful business, efficiency is key. Wasted time, effort, and resources can all contribute to decreased productivity and lost profits. Process mapping helps businesses identify areas of inefficiency and waste so they can improve operations and increase profitability.
Process mapping also helps businesses to standardize their processes. By creating a visual representation of the process, everyone involved in the process can see how it works and understand their role in it. This makes it easier to train new employees and ensures that everyone is following the same process.
Key Components of Process Mapping
The key components of process mapping include process owners, stakeholders, inputs, outputs, and process steps. Process owners are responsible for the entire process, while stakeholders are individuals or groups who have an interest or involvement in the process. Inputs and outputs are the materials or information that are used or produced during the process. Finally, process steps are the individual actions or decisions that take place during the process.
Process mapping is an iterative process, meaning that it is constantly being reviewed and improved. As the process is mapped out, managers can identify areas of improvement and make changes to the process. This process of continuous improvement helps businesses to stay competitive and adapt to changing market conditions.
In conclusion, process mapping is a valuable tool for businesses looking to improve efficiency and increase profitability. By creating a visual representation of a process, managers can identify areas of inefficiency and waste, standardize processes, and continuously improve operations.
Types of Process Maps
Process maps are visual representations of a process that help in identifying areas of improvement and inefficiencies. They provide a clear understanding of the process, making it easier to optimize and streamline it. There are different types of process maps, each with a unique purpose. Let's explore some of the most commonly used process maps:
Flowcharts
Flowcharts are the most commonly used type of process map. They are visual diagrams that show the steps of a process, using symbols to represent each step. With flowcharts, you can easily identify decision points, delays, and potential inefficiencies in the process. They're popular options for business process mapping.
For instance, a flowchart can be used to depict the process of manufacturing a product. The flowchart can start with the raw materials, and then move on to the various stages of production, such as design, assembly, quality control, and packaging. By analyzing the flowchart, you can identify bottlenecks and areas where the process can be improved.
Swimlane Diagrams
Swimlane diagrams are similar to flowcharts but are organized by department or function. The swimlanes represent different areas of responsibility, allowing for a more detailed and comprehensive map of the process.
For example, a swimlane diagram can be used to depict the hiring process in an organization. The swimlanes can represent the different departments involved in the process, such as HR, the hiring manager, and the finance department. By analyzing the swimlane diagram, you can identify areas where the process can be improved, such as reducing the time taken to fill a position.
Value Stream Maps
Value stream maps are used to analyze the flow of materials and information during a process. They focus on identifying areas of waste and non-value-added activities, helping to optimize the flow of materials and increase productivity.
For instance, a value stream map can be used to depict the process of delivering a product to a customer. The value stream map can start with the customer order, and then move on to the various stages of production, such as design, manufacturing, and delivery. By analyzing the value stream map, you can identify areas where the process can be improved, such as reducing lead times and eliminating waste.
SIPOC Diagrams
SIPOC diagrams are high-level process maps that visualize the process from start to finish. They show the suppliers, inputs, process, outputs, and customers involved in the process, helping to identify areas of waste and inefficiency.
For example, a SIPOC diagram can be used to depict the process of developing a new product. The SIPOC diagram can start with the suppliers of raw materials, move on to the inputs required for the process, such as design, manufacturing, and testing, and then move on to the outputs, such as the finished product. By analyzing the SIPOC diagram, you can identify areas where the process can be improved, such as reducing the time taken to develop a new product and improving the quality of the finished product.
Steps to Create a Process Map
If you don't already have process mapping tools, here's a step-by-step guide to creating a process map:
Define the Process Scope
The first step in creating a process map is to define the scope of the process. This involves determining the start and end points, as well as the inputs, outputs, and stakeholders involved in the process.
For example, if the process is related to product development, the scope may include defining the start point as the conceptualization of the product idea and the end point as the product launch. Inputs may include market research and customer feedback, while outputs may include a fully developed and tested product. Stakeholders may include product managers, engineers, marketing teams, and customers.
Gather Information and Identify Stakeholders
Next, gather information about the process by talking to the individuals involved and reviewing any existing documentation. Identify all stakeholders, including those who own the process and those who are affected by it.
For example, if the process is related to employee onboarding, gather information by talking to HR representatives, hiring managers, and new employees. Identify stakeholders such as the HR department, hiring managers, new employees, and existing employees who may need to work with the new hires.
Map the Process Steps
With the information gathered, create a rough draft of the process map, using symbols or shapes to represent each step. Focus on clarity and simplicity, breaking down complex steps into smaller, more manageable parts.
For example, if the process is related to software development, map the steps involved in the development cycle, such as requirements gathering, design, coding, testing, and deployment. Break down each step into smaller parts, such as creating a design document, writing code, and conducting unit tests.
Analyze the Process Map
Once the rough draft is complete, analyze the process map for inefficiencies, redundancies, and bottlenecks. Identify areas where improvements can be made, and brainstorm potential solutions with stakeholders.
For example, if the process is related to customer service, analyze the process map to identify areas where customers may experience long wait times or delays in getting their issues resolved. Brainstorm potential solutions with customer service representatives, such as implementing a chatbot to handle common inquiries or providing additional training for representatives to handle complex issues more efficiently.
Implement Improvements and Monitor Progress
With a plan in place, implement the identified improvements and monitor progress to ensure they are effective. Continuously evaluate the process and update the process map as needed to maintain a streamlined and efficient operation.
For example, if the process is related to supply chain management, implement improvements such as automating inventory tracking or streamlining the order fulfillment process. Monitor progress by analyzing metrics such as order processing time and inventory accuracy, and update the process map as needed to reflect any changes or improvements.
Conclusion
Process mapping is a powerful technique for streamlining business processes, identifying inefficiencies, and increasing profitability. By creating a visual representation of a process, businesses can easily identify areas for improvement and implement effective solutions. By following the steps outlined in this comprehensive guide, you can create effective process maps that help you optimize your operations and achieve success in your business.
Article
Process Mapping: A Comprehensive Guide to Streamlining Your Business
•
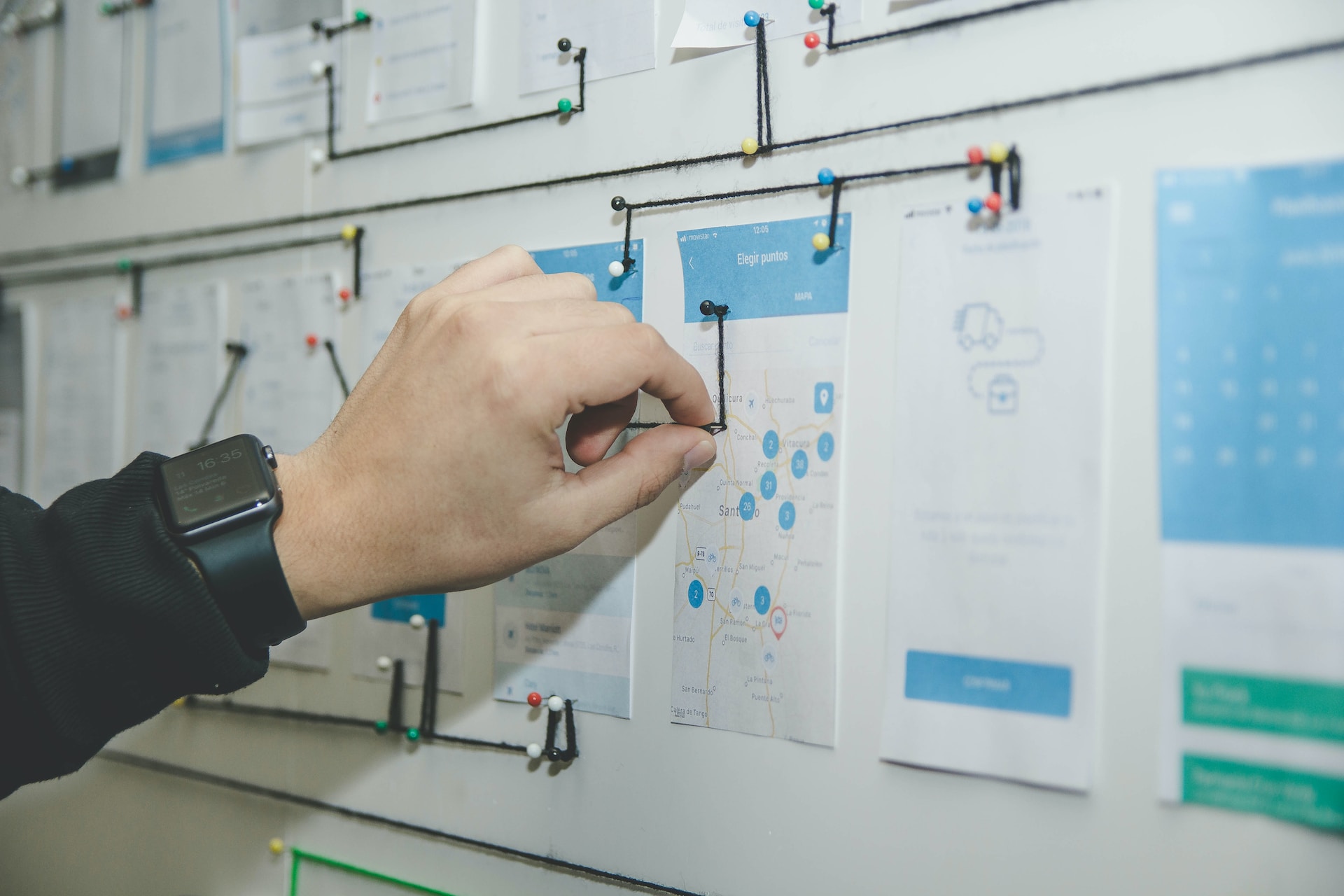