Article
Process Optimization: Strategies for Improving Efficiency and Productivity
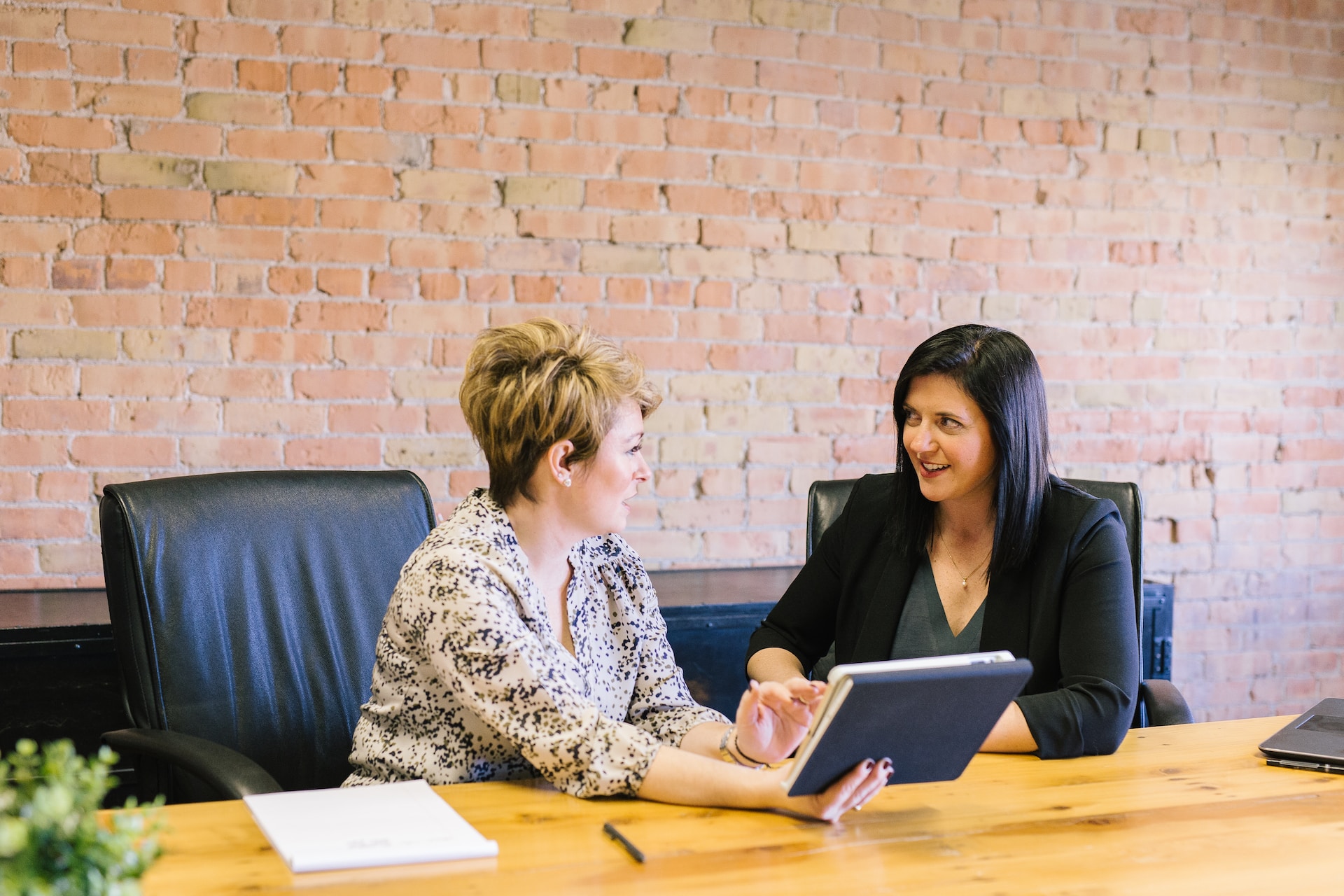
As businesses strive to become more competitive and profitable, one area that often receives a lot of attention is process optimization. By making improvements to the way tasks are carried out, companies can boost productivity, streamline workflows, and reduce costs. But where do you start when it comes to process optimization? In this article, we'll explore some of the fundamental strategies that organizations can use to optimize their processes and improve efficiency.
Understanding Process Optimization
Before we dive into the specifics of process optimization, let's first define what we mean by this term. At its core, process optimization is all about finding ways to optimize the way work gets done. It's about identifying inefficiencies and bottlenecks and making changes to overcome those challenges. This can involve overhauling entire processes or making smaller, incremental changes to individual steps.
Definition of Process Optimization
Process optimization is the practice of analyzing and improving workflow processes to make them more efficient and effective. The goal is to reduce waste, lower costs, and improve quality.
Importance of Process Optimization in Business
The benefits of process optimization can be far-reaching. By improving workflows, companies can reduce lead times, reduce errors, and improve customer satisfaction. This can translate into better financial outcomes, increased employee morale, and a better reputation in the marketplace.
One of the key advantages of process optimization is that it helps businesses stay competitive. In today's fast-paced business environment, companies must be able to pivot quickly and adapt to changing market conditions. By streamlining their processes, businesses can become more agile and responsive to customer needs.
Another benefit of process optimization is that it can help businesses identify areas for growth and expansion. By analyzing their workflows, companies can identify areas where they are underutilizing resources or where they could benefit from additional investment. This can help businesses make more informed decisions about where to allocate their resources.
Process optimization can also have a positive impact on employee satisfaction. When workflows are streamlined and processes are more efficient, employees can be more productive and feel more fulfilled in their work. This can lead to increased employee engagement and retention.
Finally, process optimization can help businesses reduce their environmental impact. By reducing waste and improving efficiency, companies can lower their carbon footprint and contribute to a more sustainable future.
Identifying Areas for Improvement
The first step to optimizing processes is identifying where improvements are needed. This can involve analyzing workflows, gathering employee feedback, and looking for signs of inefficiency or bottlenecks.
Analyzing Current Processes
The first step in identifying areas for improvement is analyzing current workflows. This involves looking at each step in the process and examining it in detail. Some things to look for include steps that take a long time to complete, steps that are prone to errors or mistakes, and steps that are not necessary for achieving the desired outcome.
For example, let's say you run a small e-commerce business. You notice that your order fulfillment process takes longer than it should, causing delays in shipping products to customers. By analyzing the current workflow, you discover that the delay is caused by a manual data entry process. You realize that by automating this process, you can significantly reduce the time it takes to fulfill orders.
Recognizing Bottlenecks and Inefficiencies
Inefficiencies and bottlenecks can occur at any stage of a workflow process. It's important to identify these early on so that they can be addressed. Some common examples of bottlenecks include manual data entry, long wait times, and redundant approvals.
For instance, suppose you manage a customer service team. You notice that customers are complaining about long wait times when calling your support line. By examining the current workflow, you discover that your team is spending too much time on redundant approvals. You realize that by simplifying the approval process, you can reduce wait times and improve customer satisfaction.
Gathering Employee Feedback
Your employees are often the best source of information when it comes to identifying bottlenecks or inefficiencies in a workflow process. Solicit feedback from your team to uncover areas for improvement.
For example, let's say you run a marketing department. You notice that your team is struggling to meet deadlines for upcoming campaigns. By gathering feedback from your team, you discover that the current workflow is causing confusion and delays. You realize that by restructuring the workflow and clarifying roles and responsibilities, you can improve efficiency and meet deadlines more effectively.
Process Optimization Techniques
Once you've identified areas for improvement, the next step is to implement process optimization techniques. There are several approaches you can take, depending on the specific needs of your organization.
Lean Manufacturing Principles
Lean manufacturing is a methodology that focuses on reducing waste in the production process. This approach involves using value stream mapping to identify areas where improvements can be made. Common techniques used in lean manufacturing include just-in-time production, kanban systems, and continuous flow.
For example, implementing a just-in-time production system can help reduce inventory costs and improve production efficiency by ensuring that materials are delivered to the production line only when they are needed. Kanban systems can help reduce waste by ensuring that materials are replenished only when they are needed, reducing the need for excess inventory.
Continuous flow, on the other hand, involves optimizing the flow of materials and products through the production process, reducing the time and resources required to produce each unit. This can be achieved by eliminating bottlenecks and optimizing the layout of the production line.
Six Sigma Methodology
Six Sigma is a data-driven approach to process improvement that focuses on reducing defects and errors. This methodology uses statistical analysis to identify areas where improvements are needed. Key techniques used in Six Sigma include DMAIC (Define, Measure, Analyze, Improve, Control) and statistical process control.
For example, implementing a statistical process control system can help identify when a process is deviating from its expected performance, allowing for corrective action to be taken before defects occur. This can help reduce waste and improve product quality.
Business Process Reengineering
Business process reengineering involves completely overhauling existing processes to improve efficiency and effectiveness. This approach often involves radical changes to workflows and reorganizing the way work is done. It requires a significant investment of time and resources but can yield significant improvements.
For example, reorganizing the way work is done can involve eliminating unnecessary steps in a process, automating tasks that are currently done manually, and redesigning workflows to better align with the needs of the organization. This can lead to significant improvements in efficiency and effectiveness.
Continuous Improvement (Kaizen)
Continuous improvement involves making small, incremental changes to processes over time. This approach focuses on empowering employees to identify areas for improvement and make changes on their own. It's a bottom-up approach that can lead to significant process optimization over time.
For example, implementing a suggestion box system can encourage employees to share their ideas for process improvement. Regular meetings can be held to discuss these ideas and implement changes that are identified.
Continuous improvement can also involve providing training and development opportunities for employees to improve their skills and knowledge. This can lead to more efficient and effective processes and can help employees feel more engaged and motivated in their work.
Implementing Process Optimization Strategies
Once you've identified areas for improvement and selected a process optimization approach, the next step is to implement your strategy. This involves putting together a plan of action and engaging stakeholders and employees in the process.
When implementing your process optimization strategy, it's important to keep in mind that change can be challenging for some employees. It's essential to communicate the benefits of the new approach clearly and involve employees in the planning process.
Establishing Clear Goals and Objectives
Before you begin implementing your process optimization strategy, it's important to clearly define your goals and objectives. This can include identifying specific metrics you want to improve, such as lead times, quality, or costs. Having clear goals in place will help you measure the success of your strategy and keep everyone on track.
It's important to involve stakeholders and employees in the goal-setting process. This can help to ensure that everyone is working towards a common objective and has a stake in the success of the project.
Engaging Stakeholders and Employees
Process optimization is a team effort. It's important to engage stakeholders and employees in the process to get their buy-in and support. This can involve providing training and education on the new workflows, and building a culture of continuous improvement.
One way to engage employees is to involve them in the planning and implementation process. This can help to ensure that their concerns are addressed and that the new processes are designed with their needs in mind.
Monitoring and Measuring Progress
Once you've implemented your process optimization strategy, it's important to monitor and measure progress. This can involve tracking key metrics over time, such as cycle time, throughput, and quality. Use this information to refine your strategy over time and identify areas for further improvement.
Regular communication with stakeholders and employees is essential during the monitoring and measuring phase. It's important to keep everyone informed of progress and any changes that are made to the strategy.
Adapting and Refining Processes
Process optimization is an ongoing effort. It's important to be flexible and adapt your processes as new challenges arise. Solicit feedback from employees and stakeholders and be open to making changes that will further improve efficiency and productivity.
Regular reviews of the process optimization strategy can help to identify areas for improvement. It's important to involve stakeholders and employees in these reviews to ensure that everyone's concerns are addressed.
By following these steps and involving stakeholders and employees in the process, you can successfully implement a process optimization strategy that improves efficiency, productivity, and quality.
Conclusion
Process optimization is a critical component of any successful business. By improving workflows and eliminating inefficiencies, organizations can reduce costs, improve quality, and increase customer satisfaction. By following the steps outlined in this article, you can identify areas for improvement and implement process optimization strategies that will help you achieve your goals.
Article
Process Optimization: Strategies for Improving Efficiency and Productivity
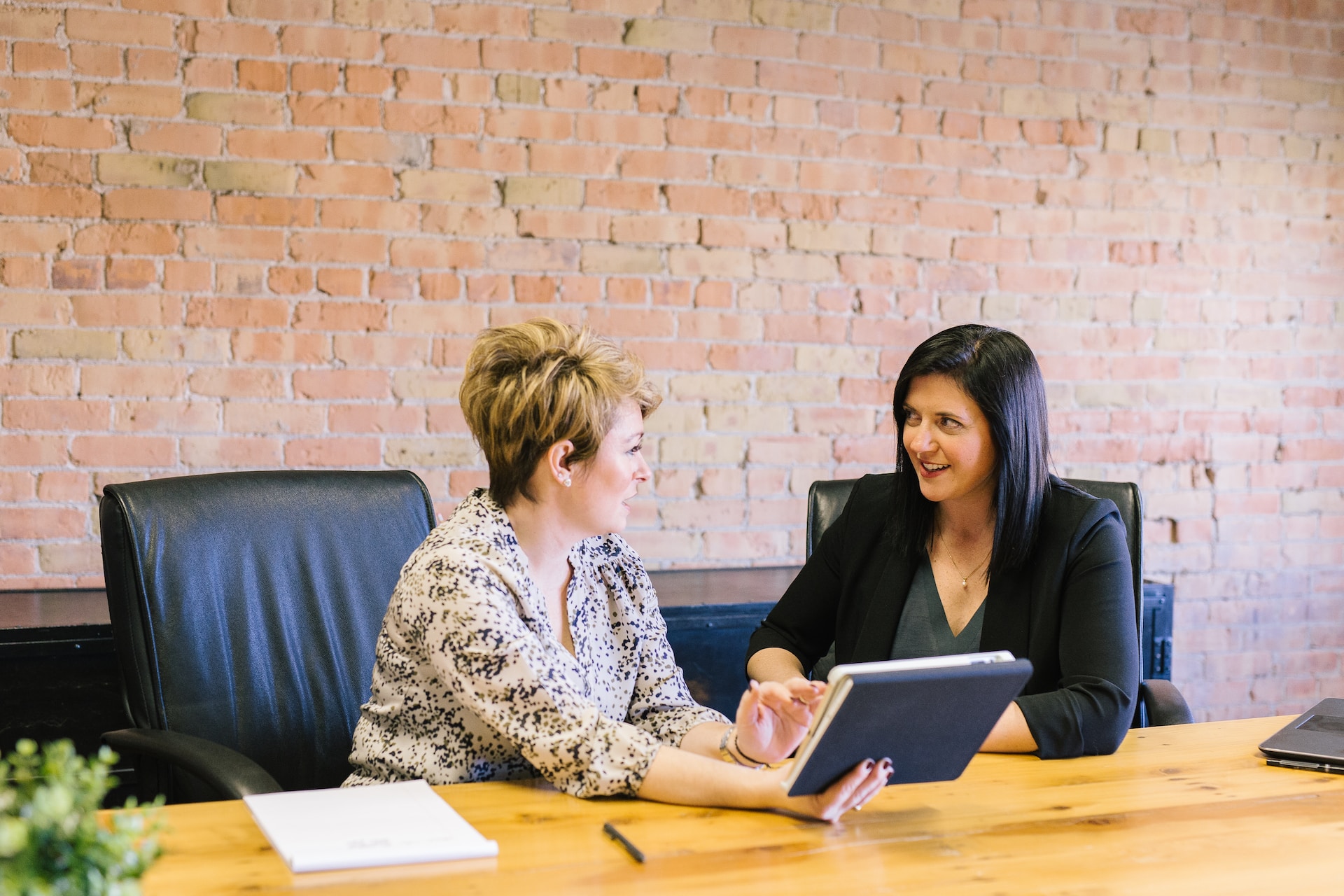
As businesses strive to become more competitive and profitable, one area that often receives a lot of attention is process optimization. By making improvements to the way tasks are carried out, companies can boost productivity, streamline workflows, and reduce costs. But where do you start when it comes to process optimization? In this article, we'll explore some of the fundamental strategies that organizations can use to optimize their processes and improve efficiency.
Understanding Process Optimization
Before we dive into the specifics of process optimization, let's first define what we mean by this term. At its core, process optimization is all about finding ways to optimize the way work gets done. It's about identifying inefficiencies and bottlenecks and making changes to overcome those challenges. This can involve overhauling entire processes or making smaller, incremental changes to individual steps.
Definition of Process Optimization
Process optimization is the practice of analyzing and improving workflow processes to make them more efficient and effective. The goal is to reduce waste, lower costs, and improve quality.
Importance of Process Optimization in Business
The benefits of process optimization can be far-reaching. By improving workflows, companies can reduce lead times, reduce errors, and improve customer satisfaction. This can translate into better financial outcomes, increased employee morale, and a better reputation in the marketplace.
One of the key advantages of process optimization is that it helps businesses stay competitive. In today's fast-paced business environment, companies must be able to pivot quickly and adapt to changing market conditions. By streamlining their processes, businesses can become more agile and responsive to customer needs.
Another benefit of process optimization is that it can help businesses identify areas for growth and expansion. By analyzing their workflows, companies can identify areas where they are underutilizing resources or where they could benefit from additional investment. This can help businesses make more informed decisions about where to allocate their resources.
Process optimization can also have a positive impact on employee satisfaction. When workflows are streamlined and processes are more efficient, employees can be more productive and feel more fulfilled in their work. This can lead to increased employee engagement and retention.
Finally, process optimization can help businesses reduce their environmental impact. By reducing waste and improving efficiency, companies can lower their carbon footprint and contribute to a more sustainable future.
Identifying Areas for Improvement
The first step to optimizing processes is identifying where improvements are needed. This can involve analyzing workflows, gathering employee feedback, and looking for signs of inefficiency or bottlenecks.
Analyzing Current Processes
The first step in identifying areas for improvement is analyzing current workflows. This involves looking at each step in the process and examining it in detail. Some things to look for include steps that take a long time to complete, steps that are prone to errors or mistakes, and steps that are not necessary for achieving the desired outcome.
For example, let's say you run a small e-commerce business. You notice that your order fulfillment process takes longer than it should, causing delays in shipping products to customers. By analyzing the current workflow, you discover that the delay is caused by a manual data entry process. You realize that by automating this process, you can significantly reduce the time it takes to fulfill orders.
Recognizing Bottlenecks and Inefficiencies
Inefficiencies and bottlenecks can occur at any stage of a workflow process. It's important to identify these early on so that they can be addressed. Some common examples of bottlenecks include manual data entry, long wait times, and redundant approvals.
For instance, suppose you manage a customer service team. You notice that customers are complaining about long wait times when calling your support line. By examining the current workflow, you discover that your team is spending too much time on redundant approvals. You realize that by simplifying the approval process, you can reduce wait times and improve customer satisfaction.
Gathering Employee Feedback
Your employees are often the best source of information when it comes to identifying bottlenecks or inefficiencies in a workflow process. Solicit feedback from your team to uncover areas for improvement.
For example, let's say you run a marketing department. You notice that your team is struggling to meet deadlines for upcoming campaigns. By gathering feedback from your team, you discover that the current workflow is causing confusion and delays. You realize that by restructuring the workflow and clarifying roles and responsibilities, you can improve efficiency and meet deadlines more effectively.
Process Optimization Techniques
Once you've identified areas for improvement, the next step is to implement process optimization techniques. There are several approaches you can take, depending on the specific needs of your organization.
Lean Manufacturing Principles
Lean manufacturing is a methodology that focuses on reducing waste in the production process. This approach involves using value stream mapping to identify areas where improvements can be made. Common techniques used in lean manufacturing include just-in-time production, kanban systems, and continuous flow.
For example, implementing a just-in-time production system can help reduce inventory costs and improve production efficiency by ensuring that materials are delivered to the production line only when they are needed. Kanban systems can help reduce waste by ensuring that materials are replenished only when they are needed, reducing the need for excess inventory.
Continuous flow, on the other hand, involves optimizing the flow of materials and products through the production process, reducing the time and resources required to produce each unit. This can be achieved by eliminating bottlenecks and optimizing the layout of the production line.
Six Sigma Methodology
Six Sigma is a data-driven approach to process improvement that focuses on reducing defects and errors. This methodology uses statistical analysis to identify areas where improvements are needed. Key techniques used in Six Sigma include DMAIC (Define, Measure, Analyze, Improve, Control) and statistical process control.
For example, implementing a statistical process control system can help identify when a process is deviating from its expected performance, allowing for corrective action to be taken before defects occur. This can help reduce waste and improve product quality.
Business Process Reengineering
Business process reengineering involves completely overhauling existing processes to improve efficiency and effectiveness. This approach often involves radical changes to workflows and reorganizing the way work is done. It requires a significant investment of time and resources but can yield significant improvements.
For example, reorganizing the way work is done can involve eliminating unnecessary steps in a process, automating tasks that are currently done manually, and redesigning workflows to better align with the needs of the organization. This can lead to significant improvements in efficiency and effectiveness.
Continuous Improvement (Kaizen)
Continuous improvement involves making small, incremental changes to processes over time. This approach focuses on empowering employees to identify areas for improvement and make changes on their own. It's a bottom-up approach that can lead to significant process optimization over time.
For example, implementing a suggestion box system can encourage employees to share their ideas for process improvement. Regular meetings can be held to discuss these ideas and implement changes that are identified.
Continuous improvement can also involve providing training and development opportunities for employees to improve their skills and knowledge. This can lead to more efficient and effective processes and can help employees feel more engaged and motivated in their work.
Implementing Process Optimization Strategies
Once you've identified areas for improvement and selected a process optimization approach, the next step is to implement your strategy. This involves putting together a plan of action and engaging stakeholders and employees in the process.
When implementing your process optimization strategy, it's important to keep in mind that change can be challenging for some employees. It's essential to communicate the benefits of the new approach clearly and involve employees in the planning process.
Establishing Clear Goals and Objectives
Before you begin implementing your process optimization strategy, it's important to clearly define your goals and objectives. This can include identifying specific metrics you want to improve, such as lead times, quality, or costs. Having clear goals in place will help you measure the success of your strategy and keep everyone on track.
It's important to involve stakeholders and employees in the goal-setting process. This can help to ensure that everyone is working towards a common objective and has a stake in the success of the project.
Engaging Stakeholders and Employees
Process optimization is a team effort. It's important to engage stakeholders and employees in the process to get their buy-in and support. This can involve providing training and education on the new workflows, and building a culture of continuous improvement.
One way to engage employees is to involve them in the planning and implementation process. This can help to ensure that their concerns are addressed and that the new processes are designed with their needs in mind.
Monitoring and Measuring Progress
Once you've implemented your process optimization strategy, it's important to monitor and measure progress. This can involve tracking key metrics over time, such as cycle time, throughput, and quality. Use this information to refine your strategy over time and identify areas for further improvement.
Regular communication with stakeholders and employees is essential during the monitoring and measuring phase. It's important to keep everyone informed of progress and any changes that are made to the strategy.
Adapting and Refining Processes
Process optimization is an ongoing effort. It's important to be flexible and adapt your processes as new challenges arise. Solicit feedback from employees and stakeholders and be open to making changes that will further improve efficiency and productivity.
Regular reviews of the process optimization strategy can help to identify areas for improvement. It's important to involve stakeholders and employees in these reviews to ensure that everyone's concerns are addressed.
By following these steps and involving stakeholders and employees in the process, you can successfully implement a process optimization strategy that improves efficiency, productivity, and quality.
Conclusion
Process optimization is a critical component of any successful business. By improving workflows and eliminating inefficiencies, organizations can reduce costs, improve quality, and increase customer satisfaction. By following the steps outlined in this article, you can identify areas for improvement and implement process optimization strategies that will help you achieve your goals.
Article
Process Optimization: Strategies for Improving Efficiency and Productivity
•
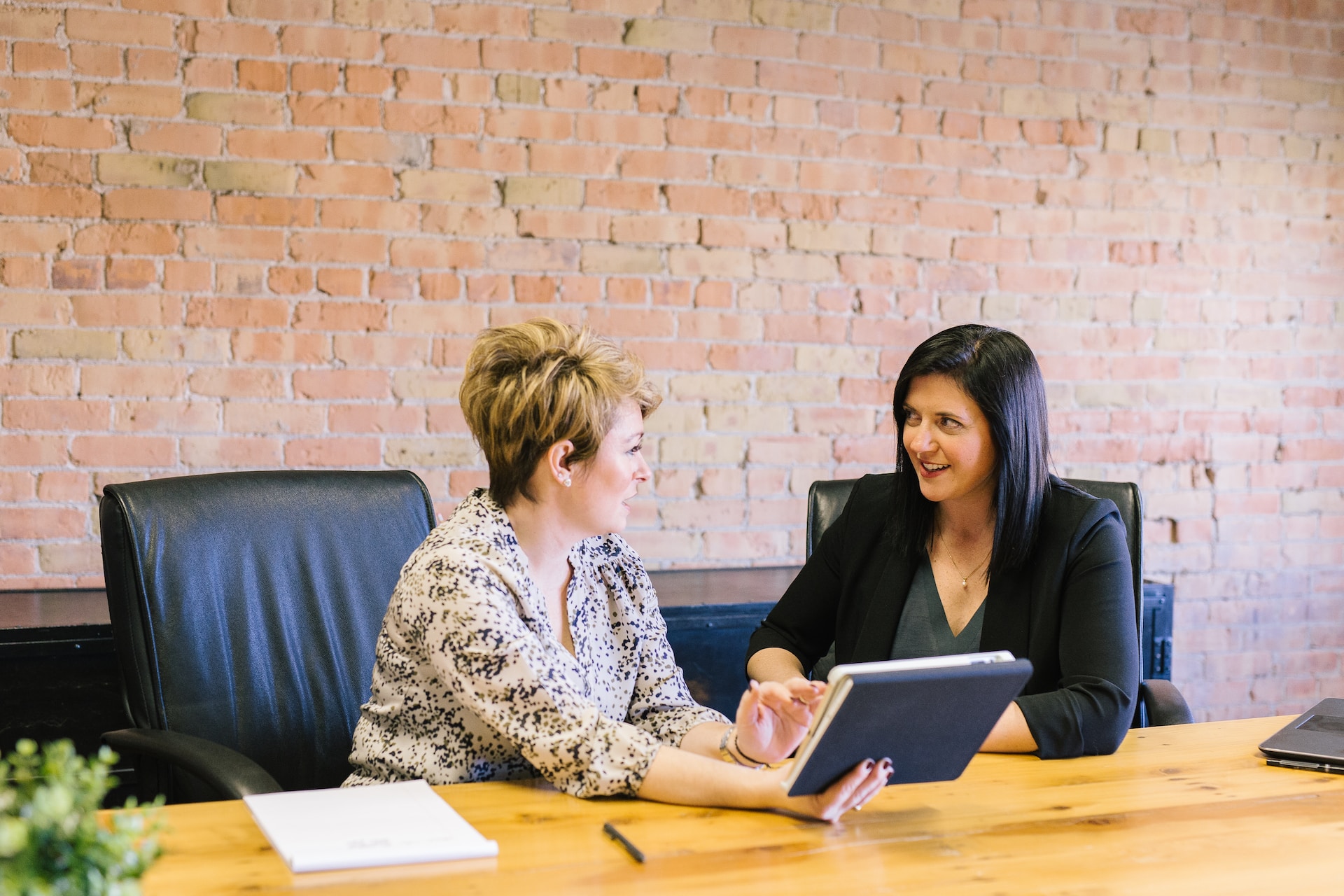