Article
The Benefits of Quality Management for Business Success
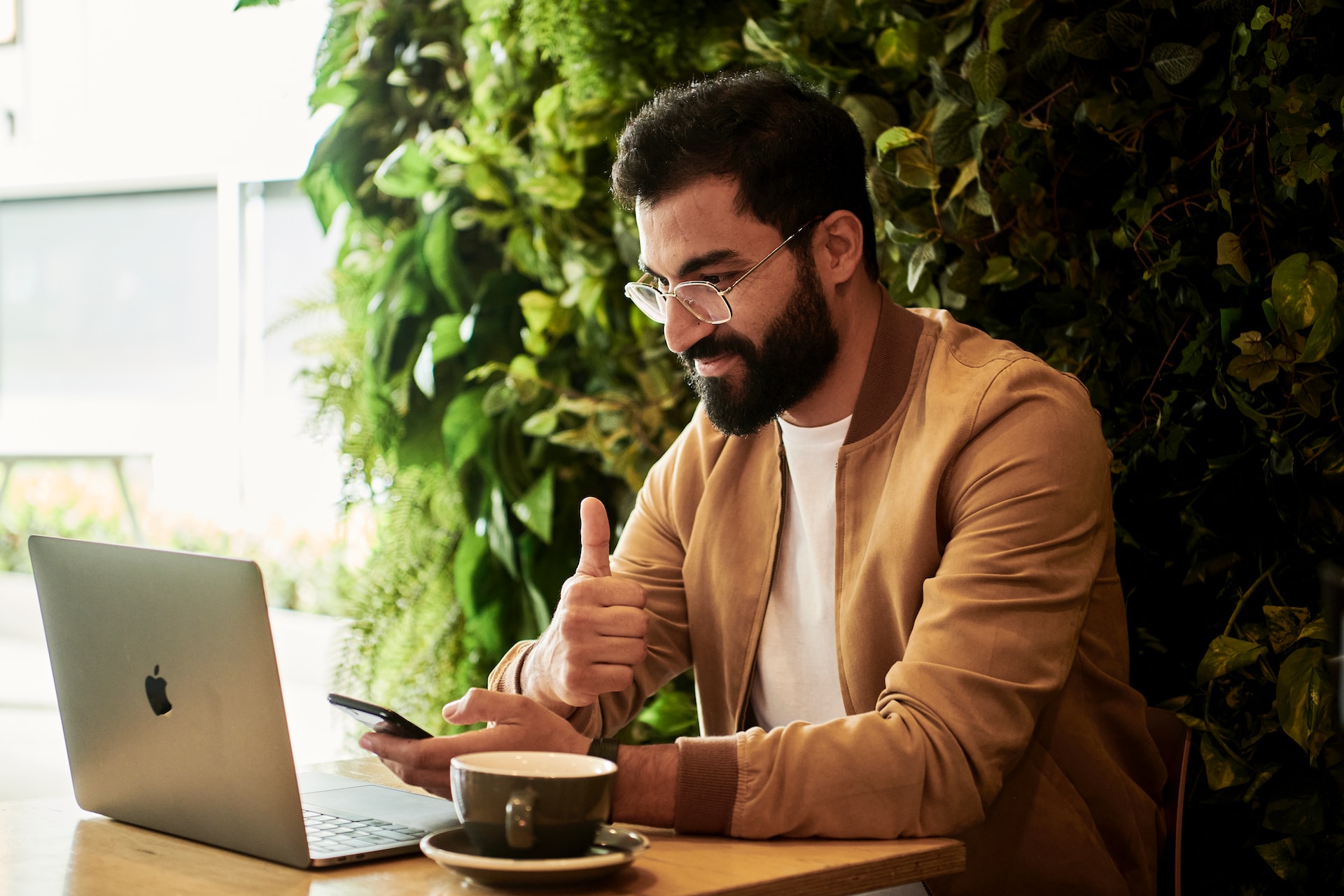
Quality management plays a crucial role in the success of any business. By implementing a systematic approach to improving quality, companies can enhance customer satisfaction, reduce costs, foster a culture of accountability, and encouraging continuous improvement. In this article, we'll take a closer look at quality management and its many benefits, as well as share some real-life success stories to illustrate its effectiveness.
Understanding Quality Management
Definition of Quality Management
Quality management is a comprehensive approach to improving the performance, effectiveness, and efficiency of an organization. It involves the development and implementation of quality standards and processes, as well as ongoing monitoring, measurement, and improvement of those standards.
The primary goal of quality management is to ensure that an organization consistently meets or exceeds customer expectations, while also improving internal processes and reducing waste.
Effective quality management requires a commitment from all levels of an organization, from top executives to front-line workers. It involves a continuous cycle of planning, implementing, monitoring, and improving processes and procedures.
Key Principles of Quality Management
There are several key principles that guide quality management, including:
- Focus on customer satisfaction: Quality management is centered around meeting and exceeding customer expectations.
- Continuous improvement: Quality management is an ongoing process of improvement, with a focus on identifying and eliminating waste and inefficiencies.
- Fact-based decision making: Quality management relies on data and analysis to drive decision making.
- Employee involvement and empowerment: Quality management encourages and empowers employees to take ownership of their work and contribute to the organization's success.
- Leadership: Effective quality management requires strong leadership and a commitment to continuous improvement.
- System-based approach: Quality management involves a holistic approach to improving all aspects of an organization's processes and procedures.
Quality Management Standards and Certifications
Several international standards and certifications exist to help companies implement and maintain effective quality management practices. These standards provide a framework for organizations to follow, ensuring that they are meeting best practices and industry standards. Some of the most common quality management standards and certifications include:
- ISO 9001: This is a widely recognized international standard for quality management systems.
- Six Sigma: This is a data-driven approach to quality management that focuses on reducing defects and improving processes.
- Total Quality Management: This is a comprehensive approach to quality management that involves all aspects of an organization.
By implementing these standards and certifications, organizations can improve their processes and procedures, reduce waste and inefficiencies, and ultimately improve customer satisfaction.
The Role of Quality Management in Business Success
Enhancing Customer Satisfaction
One of the most significant benefits of quality management is an increase in customer satisfaction. By providing high-quality products or services that meet or exceed customer expectations, companies can improve their overall reputation and gain a competitive advantage in the marketplace.
For example, a company that produces high-quality furniture that is durable and stylish will likely have more satisfied customers than a company that produces furniture that is cheaply made and falls apart easily. This can lead to repeat business, positive word-of-mouth referrals, and increased revenue.
Reducing Costs and Increasing Efficiency
Effective quality management can also lead to significant cost reductions and improved efficiency. By identifying and eliminating waste, reducing errors, and streamlining processes, companies can operate more efficiently, reduce costs, and increase profitability.
For instance, a manufacturing company that implements a quality management system can identify areas where it is producing defective products and take steps to reduce or eliminate those defects. This can lead to a reduction in waste, lower production costs, and an increase in efficiency.
Encouraging Continuous Improvement
Quality management encourages companies to continually seek out opportunities for improvement. By regularly assessing and measuring performance, identifying areas for improvement, and implementing changes, companies can stay ahead of the competition and continue to grow and evolve.
For example, a software development company that uses a quality management system can continually test and improve its products to ensure they are bug-free and meet customer needs. This can lead to increased customer satisfaction, improved sales, and a stronger reputation in the market.
Fostering a Culture of Accountability
Quality management promotes a culture of accountability, where employees take ownership of their work and strive to achieve high-quality results. This leads to increased employee engagement and motivation, as well as improved overall performance and productivity.
For instance, a company that implements a quality management system can set clear expectations for employees and provide them with the tools and resources they need to meet those expectations. This can lead to a more engaged and motivated workforce, as well as improved quality of work and increased productivity.
Implementing Quality Management in Your Business
Quality management is a critical process that helps businesses to improve their products and services while reducing costs and increasing customer satisfaction. By implementing quality management practices, you can ensure that your business is delivering the best possible products and services to your customers.
Assessing Your Current Quality Management Practices
The first step in implementing quality management in your business is to assess your current practices. This involves identifying strengths and weaknesses, determining areas for improvement, and setting goals and objectives. To do this, you will need to conduct a thorough analysis of your business processes, including your production methods, customer service practices, and quality control procedures. You may also want to gather feedback from your customers and employees to gain a better understanding of how your business is currently performing.
Once you have identified areas for improvement, you can begin to develop a plan for implementing changes. This plan should be based on your goals and objectives and should outline the steps you will take to improve your quality management practices.
Developing a Quality Management Plan
Next, you'll want to develop a quality management plan that outlines your objectives, strategies, and tactics for achieving success. This should include a timeline, budget, and resources required to implement the plan effectively. Your plan should also include a system for measuring and evaluating your progress so that you can make adjustments as needed.
When developing your plan, it's important to consider the specific needs of your business. For example, if you operate in a highly regulated industry, you may need to comply with specific quality standards. Alternatively, if you are a small business owner, you may need to focus on improving customer service and reducing costs.
Training and Developing Your Team
Training and development are essential to the success of any quality management initiative. Ensure that your team has the knowledge, skills, and resources necessary to adopt and implement new practices successfully. This may involve providing training on new equipment or software, or it may involve coaching your team on new customer service techniques or quality control procedures.
You may also want to consider hiring outside consultants or experts to provide additional training and support. These professionals can help you to identify areas for improvement and provide guidance on how to implement new practices effectively.
Monitoring and Measuring Success
Finally, it's essential to monitor and measure the success of your quality management efforts regularly. This involves ongoing evaluation, measurement, and reporting of key performance indicators and metrics. Some of the metrics you may want to track include customer satisfaction rates, defect rates, and production efficiency.
By monitoring these metrics, you can identify areas where you are succeeding and areas where you need to improve. You can then make adjustments to your quality management plan to ensure that you are continually improving your processes and delivering the best possible products and services to your customers.
Overall, implementing quality management practices in your business is a critical step in improving your operations and increasing your bottom line. By following these steps, you can develop a plan that is tailored to the specific needs of your business and ensure that you are delivering the best possible products and services to your customers.
Examples of Quality Management Success Stories
Quality management is a vital aspect of any business that seeks to improve its products and services, reduce costs, and increase customer satisfaction. Here are some examples of companies that have experienced significant success with quality management:
Case Study 1: Company X's Quality Management Journey
Company X, a manufacturer of medical devices, recognized the importance of quality management in ensuring the safety and effectiveness of their products. They implemented ISO 9001 quality certification and saw a significant improvement in their operations. The company experienced a 50% reduction in customer complaints, a 30% improvement in product defect rates, and a 20% increase in customer satisfaction. These improvements not only enhanced the company's reputation but also increased their revenue and profitability.
Case Study 2: How Company Y Improved Customer Satisfaction
Company Y, a software development firm, faced challenges in meeting customer expectations and delivering high-quality products. They implemented Total Quality Management (TQM) and saw remarkable improvements in their operations. The company achieved a 25% increase in customer satisfaction ratings, which resulted in increased customer loyalty and repeat business. They also reduced software defects by 50%, improved project completion rates by 30%, and reduced costs by 20%. These improvements not only enhanced the company's reputation but also increased their profitability.
Case Study 3: Company Z's Cost Reduction and Efficiency Gains
Company Z, a manufacturing company, recognized the need to improve their production processes to reduce costs and increase efficiency. They implemented Lean Six Sigma, a methodology that focuses on eliminating waste and improving quality, and saw significant improvements in their operations. The company reduced their production cycle times by 40%, resulting in a 30% increase in production volumes and a 25% reduction in costs. These improvements not only enhanced the company's profitability but also increased their competitiveness in the market.
These case studies demonstrate the importance of quality management in enhancing the operations and profitability of businesses. By implementing quality management methodologies such as ISO 9001, TQM, and Lean Six Sigma, companies can improve their products and services, reduce costs, and increase customer satisfaction, resulting in increased revenue and profitability.
Conclusion
Quality management is essential for the success of any organization. By implementing effective quality management practices, companies can enhance customer satisfaction, reduce costs, foster a culture of accountability, and encourage continuous improvement. With the right approach, resources, and commitment, any business can achieve significant success with quality management.
Similar Blog Posts
Article
The Benefits of Quality Management for Business Success
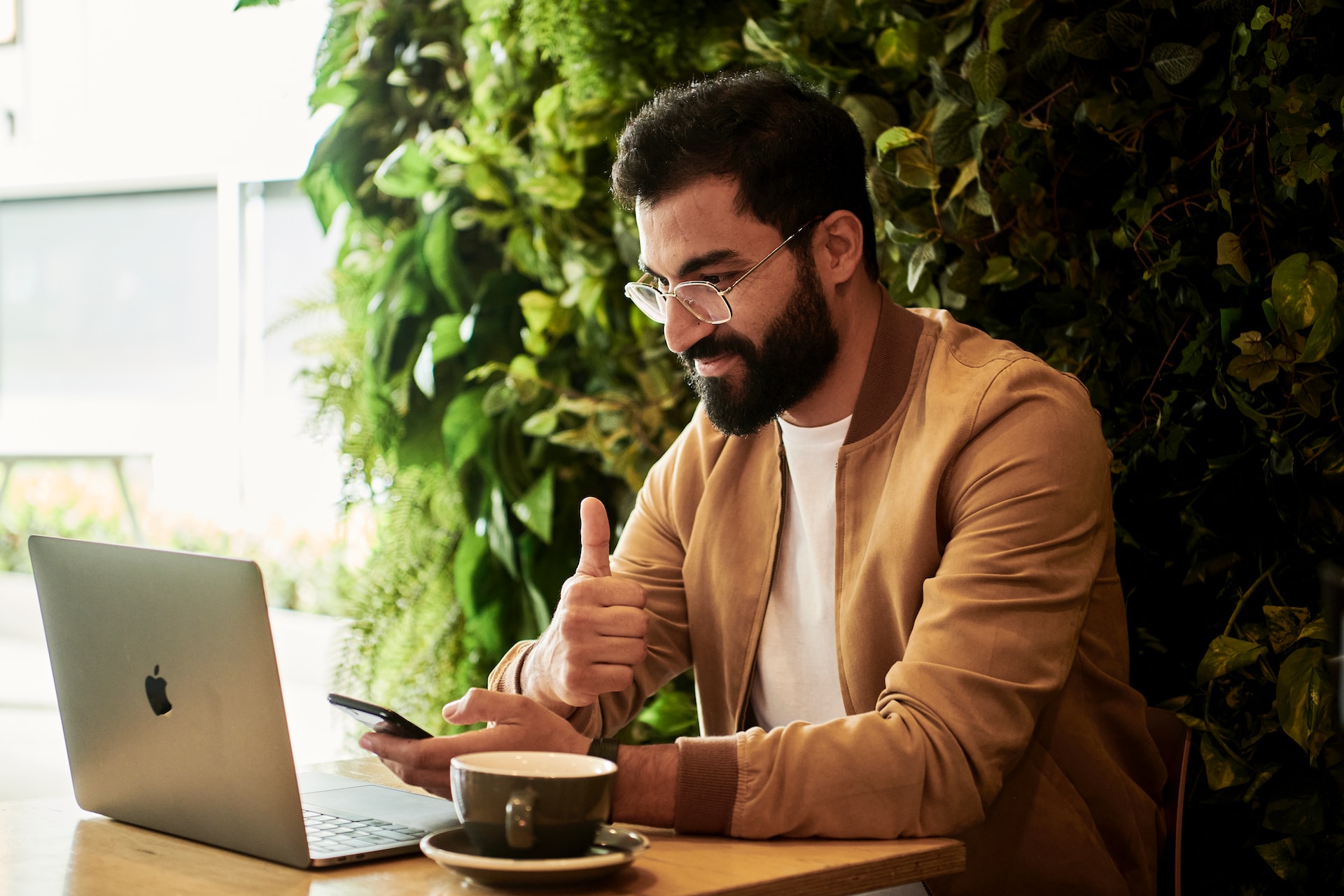
Quality management plays a crucial role in the success of any business. By implementing a systematic approach to improving quality, companies can enhance customer satisfaction, reduce costs, foster a culture of accountability, and encouraging continuous improvement. In this article, we'll take a closer look at quality management and its many benefits, as well as share some real-life success stories to illustrate its effectiveness.
Understanding Quality Management
Definition of Quality Management
Quality management is a comprehensive approach to improving the performance, effectiveness, and efficiency of an organization. It involves the development and implementation of quality standards and processes, as well as ongoing monitoring, measurement, and improvement of those standards.
The primary goal of quality management is to ensure that an organization consistently meets or exceeds customer expectations, while also improving internal processes and reducing waste.
Effective quality management requires a commitment from all levels of an organization, from top executives to front-line workers. It involves a continuous cycle of planning, implementing, monitoring, and improving processes and procedures.
Key Principles of Quality Management
There are several key principles that guide quality management, including:
- Focus on customer satisfaction: Quality management is centered around meeting and exceeding customer expectations.
- Continuous improvement: Quality management is an ongoing process of improvement, with a focus on identifying and eliminating waste and inefficiencies.
- Fact-based decision making: Quality management relies on data and analysis to drive decision making.
- Employee involvement and empowerment: Quality management encourages and empowers employees to take ownership of their work and contribute to the organization's success.
- Leadership: Effective quality management requires strong leadership and a commitment to continuous improvement.
- System-based approach: Quality management involves a holistic approach to improving all aspects of an organization's processes and procedures.
Quality Management Standards and Certifications
Several international standards and certifications exist to help companies implement and maintain effective quality management practices. These standards provide a framework for organizations to follow, ensuring that they are meeting best practices and industry standards. Some of the most common quality management standards and certifications include:
- ISO 9001: This is a widely recognized international standard for quality management systems.
- Six Sigma: This is a data-driven approach to quality management that focuses on reducing defects and improving processes.
- Total Quality Management: This is a comprehensive approach to quality management that involves all aspects of an organization.
By implementing these standards and certifications, organizations can improve their processes and procedures, reduce waste and inefficiencies, and ultimately improve customer satisfaction.
The Role of Quality Management in Business Success
Enhancing Customer Satisfaction
One of the most significant benefits of quality management is an increase in customer satisfaction. By providing high-quality products or services that meet or exceed customer expectations, companies can improve their overall reputation and gain a competitive advantage in the marketplace.
For example, a company that produces high-quality furniture that is durable and stylish will likely have more satisfied customers than a company that produces furniture that is cheaply made and falls apart easily. This can lead to repeat business, positive word-of-mouth referrals, and increased revenue.
Reducing Costs and Increasing Efficiency
Effective quality management can also lead to significant cost reductions and improved efficiency. By identifying and eliminating waste, reducing errors, and streamlining processes, companies can operate more efficiently, reduce costs, and increase profitability.
For instance, a manufacturing company that implements a quality management system can identify areas where it is producing defective products and take steps to reduce or eliminate those defects. This can lead to a reduction in waste, lower production costs, and an increase in efficiency.
Encouraging Continuous Improvement
Quality management encourages companies to continually seek out opportunities for improvement. By regularly assessing and measuring performance, identifying areas for improvement, and implementing changes, companies can stay ahead of the competition and continue to grow and evolve.
For example, a software development company that uses a quality management system can continually test and improve its products to ensure they are bug-free and meet customer needs. This can lead to increased customer satisfaction, improved sales, and a stronger reputation in the market.
Fostering a Culture of Accountability
Quality management promotes a culture of accountability, where employees take ownership of their work and strive to achieve high-quality results. This leads to increased employee engagement and motivation, as well as improved overall performance and productivity.
For instance, a company that implements a quality management system can set clear expectations for employees and provide them with the tools and resources they need to meet those expectations. This can lead to a more engaged and motivated workforce, as well as improved quality of work and increased productivity.
Implementing Quality Management in Your Business
Quality management is a critical process that helps businesses to improve their products and services while reducing costs and increasing customer satisfaction. By implementing quality management practices, you can ensure that your business is delivering the best possible products and services to your customers.
Assessing Your Current Quality Management Practices
The first step in implementing quality management in your business is to assess your current practices. This involves identifying strengths and weaknesses, determining areas for improvement, and setting goals and objectives. To do this, you will need to conduct a thorough analysis of your business processes, including your production methods, customer service practices, and quality control procedures. You may also want to gather feedback from your customers and employees to gain a better understanding of how your business is currently performing.
Once you have identified areas for improvement, you can begin to develop a plan for implementing changes. This plan should be based on your goals and objectives and should outline the steps you will take to improve your quality management practices.
Developing a Quality Management Plan
Next, you'll want to develop a quality management plan that outlines your objectives, strategies, and tactics for achieving success. This should include a timeline, budget, and resources required to implement the plan effectively. Your plan should also include a system for measuring and evaluating your progress so that you can make adjustments as needed.
When developing your plan, it's important to consider the specific needs of your business. For example, if you operate in a highly regulated industry, you may need to comply with specific quality standards. Alternatively, if you are a small business owner, you may need to focus on improving customer service and reducing costs.
Training and Developing Your Team
Training and development are essential to the success of any quality management initiative. Ensure that your team has the knowledge, skills, and resources necessary to adopt and implement new practices successfully. This may involve providing training on new equipment or software, or it may involve coaching your team on new customer service techniques or quality control procedures.
You may also want to consider hiring outside consultants or experts to provide additional training and support. These professionals can help you to identify areas for improvement and provide guidance on how to implement new practices effectively.
Monitoring and Measuring Success
Finally, it's essential to monitor and measure the success of your quality management efforts regularly. This involves ongoing evaluation, measurement, and reporting of key performance indicators and metrics. Some of the metrics you may want to track include customer satisfaction rates, defect rates, and production efficiency.
By monitoring these metrics, you can identify areas where you are succeeding and areas where you need to improve. You can then make adjustments to your quality management plan to ensure that you are continually improving your processes and delivering the best possible products and services to your customers.
Overall, implementing quality management practices in your business is a critical step in improving your operations and increasing your bottom line. By following these steps, you can develop a plan that is tailored to the specific needs of your business and ensure that you are delivering the best possible products and services to your customers.
Examples of Quality Management Success Stories
Quality management is a vital aspect of any business that seeks to improve its products and services, reduce costs, and increase customer satisfaction. Here are some examples of companies that have experienced significant success with quality management:
Case Study 1: Company X's Quality Management Journey
Company X, a manufacturer of medical devices, recognized the importance of quality management in ensuring the safety and effectiveness of their products. They implemented ISO 9001 quality certification and saw a significant improvement in their operations. The company experienced a 50% reduction in customer complaints, a 30% improvement in product defect rates, and a 20% increase in customer satisfaction. These improvements not only enhanced the company's reputation but also increased their revenue and profitability.
Case Study 2: How Company Y Improved Customer Satisfaction
Company Y, a software development firm, faced challenges in meeting customer expectations and delivering high-quality products. They implemented Total Quality Management (TQM) and saw remarkable improvements in their operations. The company achieved a 25% increase in customer satisfaction ratings, which resulted in increased customer loyalty and repeat business. They also reduced software defects by 50%, improved project completion rates by 30%, and reduced costs by 20%. These improvements not only enhanced the company's reputation but also increased their profitability.
Case Study 3: Company Z's Cost Reduction and Efficiency Gains
Company Z, a manufacturing company, recognized the need to improve their production processes to reduce costs and increase efficiency. They implemented Lean Six Sigma, a methodology that focuses on eliminating waste and improving quality, and saw significant improvements in their operations. The company reduced their production cycle times by 40%, resulting in a 30% increase in production volumes and a 25% reduction in costs. These improvements not only enhanced the company's profitability but also increased their competitiveness in the market.
These case studies demonstrate the importance of quality management in enhancing the operations and profitability of businesses. By implementing quality management methodologies such as ISO 9001, TQM, and Lean Six Sigma, companies can improve their products and services, reduce costs, and increase customer satisfaction, resulting in increased revenue and profitability.
Conclusion
Quality management is essential for the success of any organization. By implementing effective quality management practices, companies can enhance customer satisfaction, reduce costs, foster a culture of accountability, and encourage continuous improvement. With the right approach, resources, and commitment, any business can achieve significant success with quality management.
Article
The Benefits of Quality Management for Business Success
•
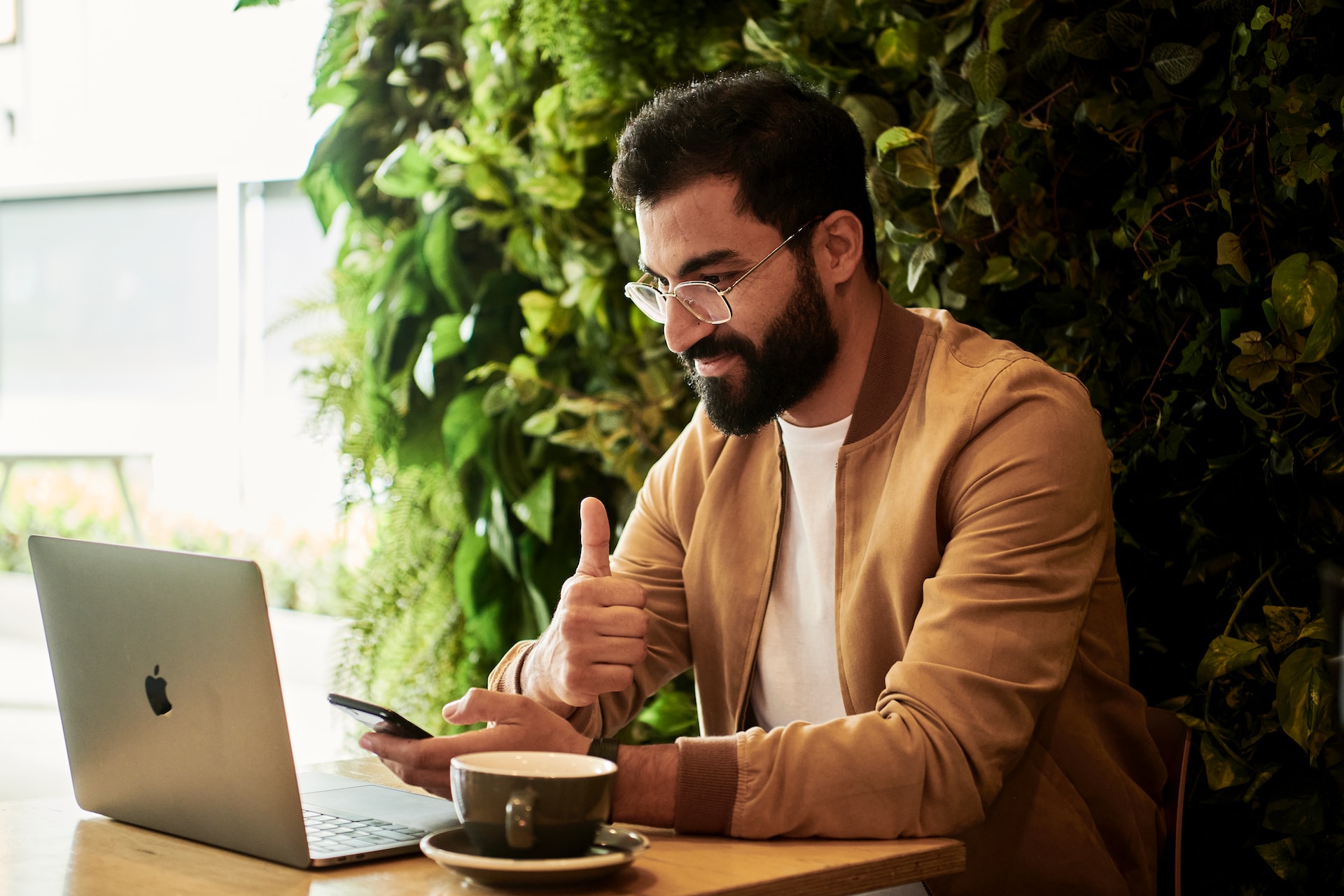