Article
Understanding Lean Six Sigma: A Comprehensive Guide
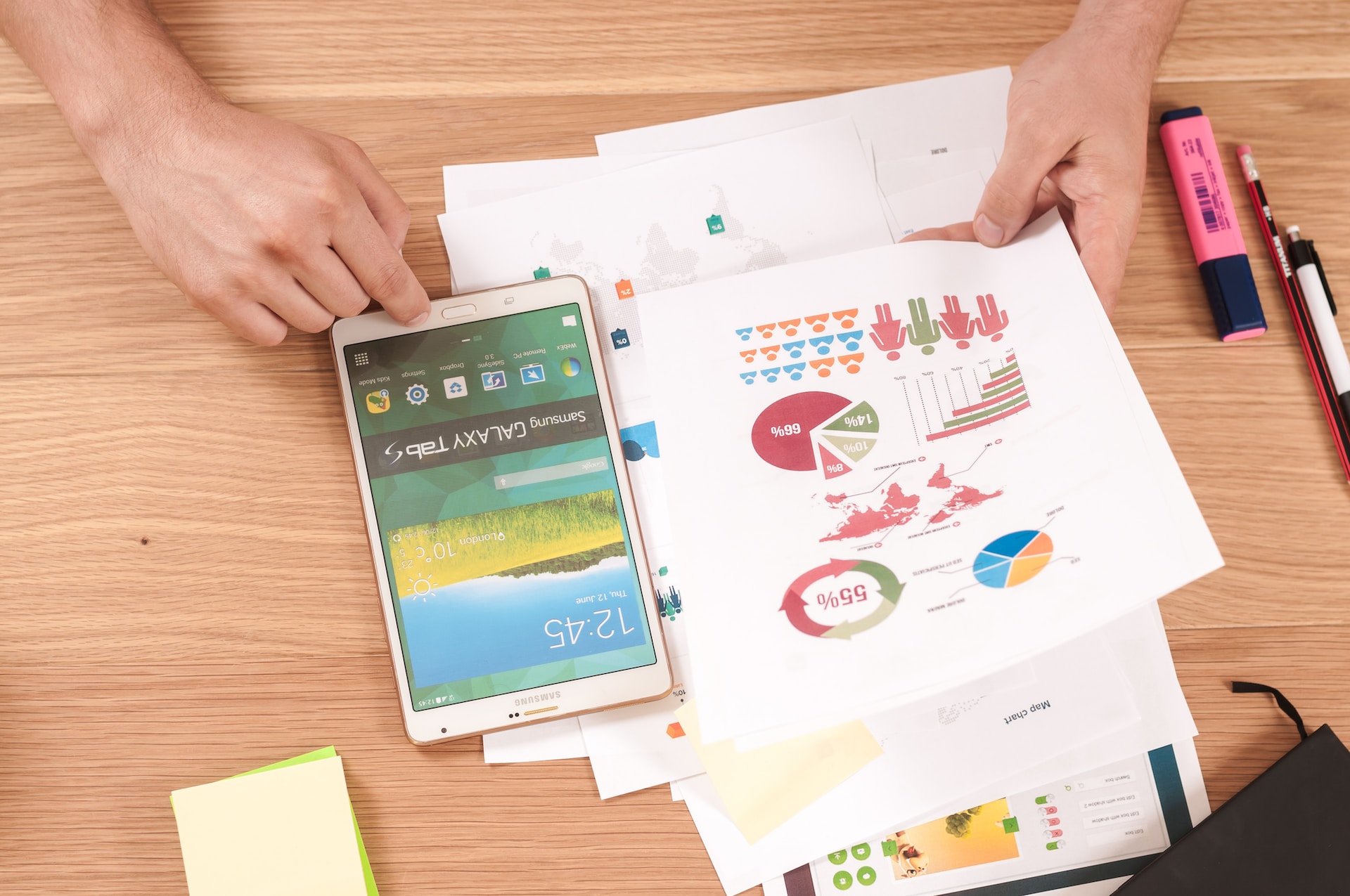
In today's fast-paced business world, organizations are constantly striving to improve their processes and deliver exceptional results. One methodology that has gained significant popularity over the years is Lean Six Sigma. In this comprehensive guide, we will delve into the intricacies of Lean Six Sigma, exploring its origins, core principles, methodology, benefits, roles and responsibilities, as well as the process of getting certified. So let's dive in and uncover the power of Lean Six Sigma!
Introduction to Lean Six Sigma
Before we embark on this journey, let's start by understanding the basics of Lean Six Sigma. Lean Six Sigma is a powerful management approach that combines the concepts of Lean and Six Sigma to eliminate waste, reduce variation, and improve efficiency and effectiveness in organizations. By embracing Lean Six Sigma, companies can streamline their processes, enhance customer satisfaction, and maximize profitability.
The Origins of Lean Six Sigma
The origins of Lean Six Sigma can be traced back to two separate methodologies: Lean and Six Sigma. Lean, also known as Lean Manufacturing or Lean Production, emerged from the renowned Toyota Production System (TPS) in the 1950s. Its primary focus is on reducing waste and creating value for customers.
Lean Manufacturing originated from the need for Toyota to compete with American automakers who were producing cars at a faster rate. Toyota realized that they could not match the production speed, so they decided to focus on eliminating waste in their processes. This led to the development of the Toyota Production System, which later became known as Lean Manufacturing.
On the other hand, Six Sigma, developed by Motorola in the 1980s, is a data-driven methodology aimed at eliminating defects and reducing process variation. By leveraging statistical tools and techniques, organizations can achieve near-perfect quality levels and drive process improvement.
Six Sigma was initially implemented by Motorola as a way to improve their manufacturing processes. The term "Six Sigma" refers to the statistical concept of measuring process variation. Motorola aimed to reduce defects in their products by targeting a defect rate of no more than 3.4 defects per million opportunities. This rigorous approach to quality improvement gained popularity and has since been adopted by many organizations across various industries.
The Core Principles of Lean Six Sigma
Now that we have a grasp on the origins of Lean Six Sigma, let's explore its core principles, which form the foundation of this powerful methodology.
- Customer-centricity: Lean Six Sigma places the customer at the heart of every process and decision-making. By understanding customer needs and expectations, organizations can deliver products or services that truly add value and exceed customer satisfaction.
- Data-driven decision-making: Rather than relying on assumptions or personal opinions, Lean Six Sigma encourages organizations to make decisions based on data and facts. By analyzing data, organizations can identify areas for improvement and make informed decisions that lead to impactful results.
- Continuous improvement: An essential principle of Lean Six Sigma is the pursuit of continuous improvement. Organizations are encouraged to constantly evaluate their processes and look for opportunities to eliminate waste, reduce defects, and optimize performance. This mindset allows organizations to remain competitive in an ever-evolving business landscape.
- Employee empowerment: Lean Six Sigma recognizes that employees are the key drivers of process improvement. Organizations are encouraged to empower their employees by providing them with the necessary training, tools, and support to identify and solve problems. This not only fosters a culture of continuous improvement but also enhances employee engagement and satisfaction.
- Leadership commitment: Lean Six Sigma requires strong leadership commitment and support. Leaders play a crucial role in driving the implementation of Lean Six Sigma initiatives, setting goals, and providing resources. Their commitment sets the tone for the entire organization and ensures that Lean Six Sigma becomes embedded in the organizational culture.
By embracing these core principles, organizations can unlock the full potential of Lean Six Sigma and achieve sustainable improvements in their processes, products, and services.
The Lean Six Sigma Methodology
Now that we understand the core principles of Lean Six Sigma, let's dive into the methodology that drives its success.
Lean Six Sigma is a powerful approach that combines the principles of Lean manufacturing and Six Sigma quality management. It aims to eliminate waste, reduce variation, and improve process efficiency and effectiveness. By following a structured methodology, organizations can achieve significant improvements in quality, customer satisfaction, and overall business performance.
The Five Phases of Lean Six Sigma
The Lean Six Sigma methodology consists of five phases, commonly known as DMAIC: Define, Measure, Analyze, Improve, and Control.
- Define: In this initial phase, the project goals and scope are defined. Organizations must clearly understand the problem they are trying to solve and the desired outcome. By setting specific and measurable objectives, teams can align their efforts and establish a solid foundation for success.
- Measure: Once the problem has been defined, the next step is to gather data and baseline the current state of the process. This phase involves the collection of relevant metrics and measurements to provide a clear understanding of the process performance.
- Analyze: With the data in hand, organizations can now analyze the root causes of the problem and identify areas for improvement. This phase involves various tools and techniques such as root cause analysis, process mapping, and statistical analysis.
- Improve: Armed with insights from the previous phases, it's time to develop and implement solutions. During the Improve phase, teams brainstorm ideas, pilot test potential improvements, and refine them based on feedback. This phase aims to optimize the process and achieve the desired future state.
- Control: The final phase of the Lean Six Sigma methodology focuses on sustaining the improvements made. By implementing control measures, organizations ensure that the process remains stable and continues to deliver results over time. This phase involves establishing performance monitoring systems, creating standard operating procedures, and providing training to relevant stakeholders.
Each phase of the DMAIC methodology is crucial for the success of a Lean Six Sigma project. It provides a structured approach that guides teams from problem identification to sustainable solutions.
Tools and Techniques Used in Lean Six Sigma
Throughout the Lean Six Sigma journey, various tools and techniques are employed to facilitate data analysis, problem-solving, and process improvement. These tools help teams make informed decisions and drive meaningful change within their processes.
One commonly used tool is process mapping, which visually represents the steps and interactions in a process. It helps identify bottlenecks, redundancies, and opportunities for improvement. Another tool is the Pareto chart, which helps prioritize problems by showing the frequency and impact of different issues. Statistical Process Control (SPC) techniques are used to monitor process performance and detect any deviations from the desired standard. Root cause analysis helps identify the underlying causes of problems, enabling teams to address them effectively.
Value stream mapping is another valuable tool in Lean Six Sigma. It provides a holistic view of the end-to-end process, highlighting areas of waste and opportunities for improvement. Hypothesis testing is used to validate potential improvements and ensure that they have a significant impact on the process. Failure Mode and Effects Analysis (FMEA) helps identify and mitigate potential risks and failures in a process.
These are just a few examples of the tools and techniques used in Lean Six Sigma. There are many more available, each with its own unique purpose and benefits. By leveraging these tools effectively, organizations can uncover insights, make data-driven decisions, and drive continuous improvement.
The Benefits of Implementing Lean Six Sigma
Now that we have a solid understanding of the Lean Six Sigma methodology and its components, let's explore the benefits that organizations can reap by implementing this powerful approach.
Implementing Lean Six Sigma offers a wide range of benefits that can have a transformative impact on organizations. Let's dive deeper into two key benefits: improving operational efficiency and enhancing customer satisfaction.
Improving Operational Efficiency
One of the primary benefits of Lean Six Sigma is its ability to improve operational efficiency. By eliminating waste and streamlining processes, organizations can reduce lead times, increase productivity, and enhance overall operational performance.
Lean Six Sigma provides organizations with a set of tools and methodologies that enable them to identify and eliminate bottlenecks in their processes. By analyzing data and using statistical methods, companies can pinpoint areas of inefficiency and implement targeted improvements.
For example, a manufacturing company implementing Lean Six Sigma may identify a particular process that is causing delays in production. By analyzing data and using tools like value stream mapping, they can identify the root causes of these delays and implement changes to streamline the process.
Through the use of Lean Six Sigma tools and methodologies, companies can optimize workflows, reduce cycle times, and achieve significant cost savings. By eliminating unnecessary steps, reducing errors, and improving process flow, organizations can operate more efficiently and effectively.
Enhancing Customer Satisfaction
Another critical aspect of Lean Six Sigma is its focus on enhancing customer satisfaction. By putting the customer at the center of every decision, organizations can identify and address pain points, improve product or service quality, and deliver exceptional customer experiences.
Lean Six Sigma provides organizations with a structured approach to understanding customer needs and expectations. Through methods like voice of the customer analysis and customer journey mapping, companies can gain valuable insights into what drives customer satisfaction and loyalty.
By using Lean Six Sigma tools and methodologies, organizations can identify areas where they are falling short of customer expectations and make targeted improvements. For example, a service-based company may use Lean Six Sigma to analyze customer feedback and identify common complaints or issues. They can then implement changes to address these concerns and improve the overall customer experience.
Satisfied customers are more likely to become loyal advocates, spreading positive word-of-mouth and contributing to business growth. By consistently meeting and exceeding customer expectations, organizations can build strong relationships with their customers and gain a competitive edge in the market.
In conclusion, implementing Lean Six Sigma offers organizations numerous benefits, including improved operational efficiency and enhanced customer satisfaction. By leveraging the tools and methodologies of Lean Six Sigma, companies can streamline processes, reduce waste, and deliver exceptional customer experiences. These benefits can lead to increased productivity, cost savings, and business growth.
Roles and Responsibilities in Lean Six Sigma
Now that we have explored the intricacies of Lean Six Sigma, let's shift our focus to the roles and responsibilities within this methodology.
The Role of a Green Belt
The Green Belt is an essential player in the Lean Six Sigma framework. These individuals are responsible for leading process improvement projects within their respective areas of expertise. Green Belts undergo rigorous training to acquire the necessary Lean Six Sigma skills and tools, allowing them to drive continuous improvement and deliver tangible results.
The Role of a Black Belt
Black Belts are highly skilled professionals who take on more significant process improvement initiatives and provide mentorship to Green Belts. They possess a deep understanding of Lean Six Sigma concepts, tools, and methodologies, and are responsible for leading cross-functional teams to achieve breakthrough improvements.
Lean Six Sigma Certification
Now that we have a clear understanding of the roles within Lean Six Sigma, let's turn our attention to the process of getting certified.
The Process of Getting Certified
Obtaining Lean Six Sigma certification is a valuable asset for professionals looking to enhance their skills and propel their careers forward. The certification process typically involves completing training courses, passing exams, and demonstrating practical application through the completion of real-world improvement projects. Different certification levels include Yellow Belt, Green Belt, Black Belt, and Master Black Belt, each representing a higher level of expertise and responsibility.
The Benefits of Lean Six Sigma Certification
Lean Six Sigma certification offers numerous benefits, including enhanced job prospects, increased earning potential, and the ability to lead impactful process improvement initiatives. Additionally, certified professionals gain valuable problem-solving and analytical skills that can be applied across various industries and sectors.
Conclusion
Lean Six Sigma is a powerful methodology that enables organizations to eliminate waste, reduce variation, enhance customer satisfaction, and drive continuous improvement. By embracing Lean Six Sigma, organizations position themselves for success in today's highly competitive business landscape. Whether you are a novice exploring Lean Six Sigma for the first time or a seasoned professional looking to deepen your knowledge, this comprehensive guide has provided you with a solid foundation to embark on your Lean Six Sigma journey. So seize the opportunity and unlock the potential of Lean Six Sigma in your organization today!
Similar Blog Posts
Article
Understanding Lean Six Sigma: A Comprehensive Guide
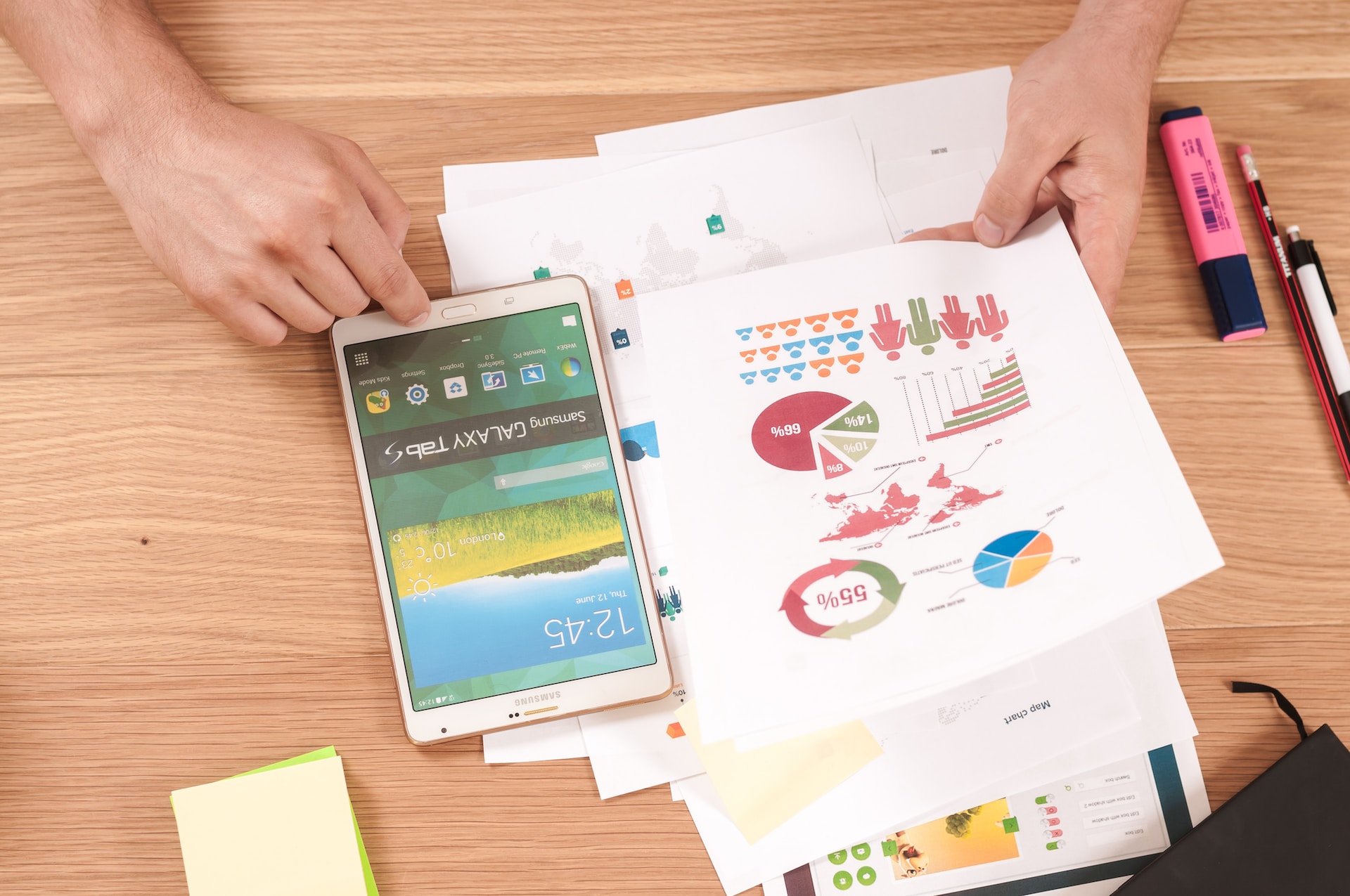
In today's fast-paced business world, organizations are constantly striving to improve their processes and deliver exceptional results. One methodology that has gained significant popularity over the years is Lean Six Sigma. In this comprehensive guide, we will delve into the intricacies of Lean Six Sigma, exploring its origins, core principles, methodology, benefits, roles and responsibilities, as well as the process of getting certified. So let's dive in and uncover the power of Lean Six Sigma!
Introduction to Lean Six Sigma
Before we embark on this journey, let's start by understanding the basics of Lean Six Sigma. Lean Six Sigma is a powerful management approach that combines the concepts of Lean and Six Sigma to eliminate waste, reduce variation, and improve efficiency and effectiveness in organizations. By embracing Lean Six Sigma, companies can streamline their processes, enhance customer satisfaction, and maximize profitability.
The Origins of Lean Six Sigma
The origins of Lean Six Sigma can be traced back to two separate methodologies: Lean and Six Sigma. Lean, also known as Lean Manufacturing or Lean Production, emerged from the renowned Toyota Production System (TPS) in the 1950s. Its primary focus is on reducing waste and creating value for customers.
Lean Manufacturing originated from the need for Toyota to compete with American automakers who were producing cars at a faster rate. Toyota realized that they could not match the production speed, so they decided to focus on eliminating waste in their processes. This led to the development of the Toyota Production System, which later became known as Lean Manufacturing.
On the other hand, Six Sigma, developed by Motorola in the 1980s, is a data-driven methodology aimed at eliminating defects and reducing process variation. By leveraging statistical tools and techniques, organizations can achieve near-perfect quality levels and drive process improvement.
Six Sigma was initially implemented by Motorola as a way to improve their manufacturing processes. The term "Six Sigma" refers to the statistical concept of measuring process variation. Motorola aimed to reduce defects in their products by targeting a defect rate of no more than 3.4 defects per million opportunities. This rigorous approach to quality improvement gained popularity and has since been adopted by many organizations across various industries.
The Core Principles of Lean Six Sigma
Now that we have a grasp on the origins of Lean Six Sigma, let's explore its core principles, which form the foundation of this powerful methodology.
- Customer-centricity: Lean Six Sigma places the customer at the heart of every process and decision-making. By understanding customer needs and expectations, organizations can deliver products or services that truly add value and exceed customer satisfaction.
- Data-driven decision-making: Rather than relying on assumptions or personal opinions, Lean Six Sigma encourages organizations to make decisions based on data and facts. By analyzing data, organizations can identify areas for improvement and make informed decisions that lead to impactful results.
- Continuous improvement: An essential principle of Lean Six Sigma is the pursuit of continuous improvement. Organizations are encouraged to constantly evaluate their processes and look for opportunities to eliminate waste, reduce defects, and optimize performance. This mindset allows organizations to remain competitive in an ever-evolving business landscape.
- Employee empowerment: Lean Six Sigma recognizes that employees are the key drivers of process improvement. Organizations are encouraged to empower their employees by providing them with the necessary training, tools, and support to identify and solve problems. This not only fosters a culture of continuous improvement but also enhances employee engagement and satisfaction.
- Leadership commitment: Lean Six Sigma requires strong leadership commitment and support. Leaders play a crucial role in driving the implementation of Lean Six Sigma initiatives, setting goals, and providing resources. Their commitment sets the tone for the entire organization and ensures that Lean Six Sigma becomes embedded in the organizational culture.
By embracing these core principles, organizations can unlock the full potential of Lean Six Sigma and achieve sustainable improvements in their processes, products, and services.
The Lean Six Sigma Methodology
Now that we understand the core principles of Lean Six Sigma, let's dive into the methodology that drives its success.
Lean Six Sigma is a powerful approach that combines the principles of Lean manufacturing and Six Sigma quality management. It aims to eliminate waste, reduce variation, and improve process efficiency and effectiveness. By following a structured methodology, organizations can achieve significant improvements in quality, customer satisfaction, and overall business performance.
The Five Phases of Lean Six Sigma
The Lean Six Sigma methodology consists of five phases, commonly known as DMAIC: Define, Measure, Analyze, Improve, and Control.
- Define: In this initial phase, the project goals and scope are defined. Organizations must clearly understand the problem they are trying to solve and the desired outcome. By setting specific and measurable objectives, teams can align their efforts and establish a solid foundation for success.
- Measure: Once the problem has been defined, the next step is to gather data and baseline the current state of the process. This phase involves the collection of relevant metrics and measurements to provide a clear understanding of the process performance.
- Analyze: With the data in hand, organizations can now analyze the root causes of the problem and identify areas for improvement. This phase involves various tools and techniques such as root cause analysis, process mapping, and statistical analysis.
- Improve: Armed with insights from the previous phases, it's time to develop and implement solutions. During the Improve phase, teams brainstorm ideas, pilot test potential improvements, and refine them based on feedback. This phase aims to optimize the process and achieve the desired future state.
- Control: The final phase of the Lean Six Sigma methodology focuses on sustaining the improvements made. By implementing control measures, organizations ensure that the process remains stable and continues to deliver results over time. This phase involves establishing performance monitoring systems, creating standard operating procedures, and providing training to relevant stakeholders.
Each phase of the DMAIC methodology is crucial for the success of a Lean Six Sigma project. It provides a structured approach that guides teams from problem identification to sustainable solutions.
Tools and Techniques Used in Lean Six Sigma
Throughout the Lean Six Sigma journey, various tools and techniques are employed to facilitate data analysis, problem-solving, and process improvement. These tools help teams make informed decisions and drive meaningful change within their processes.
One commonly used tool is process mapping, which visually represents the steps and interactions in a process. It helps identify bottlenecks, redundancies, and opportunities for improvement. Another tool is the Pareto chart, which helps prioritize problems by showing the frequency and impact of different issues. Statistical Process Control (SPC) techniques are used to monitor process performance and detect any deviations from the desired standard. Root cause analysis helps identify the underlying causes of problems, enabling teams to address them effectively.
Value stream mapping is another valuable tool in Lean Six Sigma. It provides a holistic view of the end-to-end process, highlighting areas of waste and opportunities for improvement. Hypothesis testing is used to validate potential improvements and ensure that they have a significant impact on the process. Failure Mode and Effects Analysis (FMEA) helps identify and mitigate potential risks and failures in a process.
These are just a few examples of the tools and techniques used in Lean Six Sigma. There are many more available, each with its own unique purpose and benefits. By leveraging these tools effectively, organizations can uncover insights, make data-driven decisions, and drive continuous improvement.
The Benefits of Implementing Lean Six Sigma
Now that we have a solid understanding of the Lean Six Sigma methodology and its components, let's explore the benefits that organizations can reap by implementing this powerful approach.
Implementing Lean Six Sigma offers a wide range of benefits that can have a transformative impact on organizations. Let's dive deeper into two key benefits: improving operational efficiency and enhancing customer satisfaction.
Improving Operational Efficiency
One of the primary benefits of Lean Six Sigma is its ability to improve operational efficiency. By eliminating waste and streamlining processes, organizations can reduce lead times, increase productivity, and enhance overall operational performance.
Lean Six Sigma provides organizations with a set of tools and methodologies that enable them to identify and eliminate bottlenecks in their processes. By analyzing data and using statistical methods, companies can pinpoint areas of inefficiency and implement targeted improvements.
For example, a manufacturing company implementing Lean Six Sigma may identify a particular process that is causing delays in production. By analyzing data and using tools like value stream mapping, they can identify the root causes of these delays and implement changes to streamline the process.
Through the use of Lean Six Sigma tools and methodologies, companies can optimize workflows, reduce cycle times, and achieve significant cost savings. By eliminating unnecessary steps, reducing errors, and improving process flow, organizations can operate more efficiently and effectively.
Enhancing Customer Satisfaction
Another critical aspect of Lean Six Sigma is its focus on enhancing customer satisfaction. By putting the customer at the center of every decision, organizations can identify and address pain points, improve product or service quality, and deliver exceptional customer experiences.
Lean Six Sigma provides organizations with a structured approach to understanding customer needs and expectations. Through methods like voice of the customer analysis and customer journey mapping, companies can gain valuable insights into what drives customer satisfaction and loyalty.
By using Lean Six Sigma tools and methodologies, organizations can identify areas where they are falling short of customer expectations and make targeted improvements. For example, a service-based company may use Lean Six Sigma to analyze customer feedback and identify common complaints or issues. They can then implement changes to address these concerns and improve the overall customer experience.
Satisfied customers are more likely to become loyal advocates, spreading positive word-of-mouth and contributing to business growth. By consistently meeting and exceeding customer expectations, organizations can build strong relationships with their customers and gain a competitive edge in the market.
In conclusion, implementing Lean Six Sigma offers organizations numerous benefits, including improved operational efficiency and enhanced customer satisfaction. By leveraging the tools and methodologies of Lean Six Sigma, companies can streamline processes, reduce waste, and deliver exceptional customer experiences. These benefits can lead to increased productivity, cost savings, and business growth.
Roles and Responsibilities in Lean Six Sigma
Now that we have explored the intricacies of Lean Six Sigma, let's shift our focus to the roles and responsibilities within this methodology.
The Role of a Green Belt
The Green Belt is an essential player in the Lean Six Sigma framework. These individuals are responsible for leading process improvement projects within their respective areas of expertise. Green Belts undergo rigorous training to acquire the necessary Lean Six Sigma skills and tools, allowing them to drive continuous improvement and deliver tangible results.
The Role of a Black Belt
Black Belts are highly skilled professionals who take on more significant process improvement initiatives and provide mentorship to Green Belts. They possess a deep understanding of Lean Six Sigma concepts, tools, and methodologies, and are responsible for leading cross-functional teams to achieve breakthrough improvements.
Lean Six Sigma Certification
Now that we have a clear understanding of the roles within Lean Six Sigma, let's turn our attention to the process of getting certified.
The Process of Getting Certified
Obtaining Lean Six Sigma certification is a valuable asset for professionals looking to enhance their skills and propel their careers forward. The certification process typically involves completing training courses, passing exams, and demonstrating practical application through the completion of real-world improvement projects. Different certification levels include Yellow Belt, Green Belt, Black Belt, and Master Black Belt, each representing a higher level of expertise and responsibility.
The Benefits of Lean Six Sigma Certification
Lean Six Sigma certification offers numerous benefits, including enhanced job prospects, increased earning potential, and the ability to lead impactful process improvement initiatives. Additionally, certified professionals gain valuable problem-solving and analytical skills that can be applied across various industries and sectors.
Conclusion
Lean Six Sigma is a powerful methodology that enables organizations to eliminate waste, reduce variation, enhance customer satisfaction, and drive continuous improvement. By embracing Lean Six Sigma, organizations position themselves for success in today's highly competitive business landscape. Whether you are a novice exploring Lean Six Sigma for the first time or a seasoned professional looking to deepen your knowledge, this comprehensive guide has provided you with a solid foundation to embark on your Lean Six Sigma journey. So seize the opportunity and unlock the potential of Lean Six Sigma in your organization today!
Article
Understanding Lean Six Sigma: A Comprehensive Guide
•
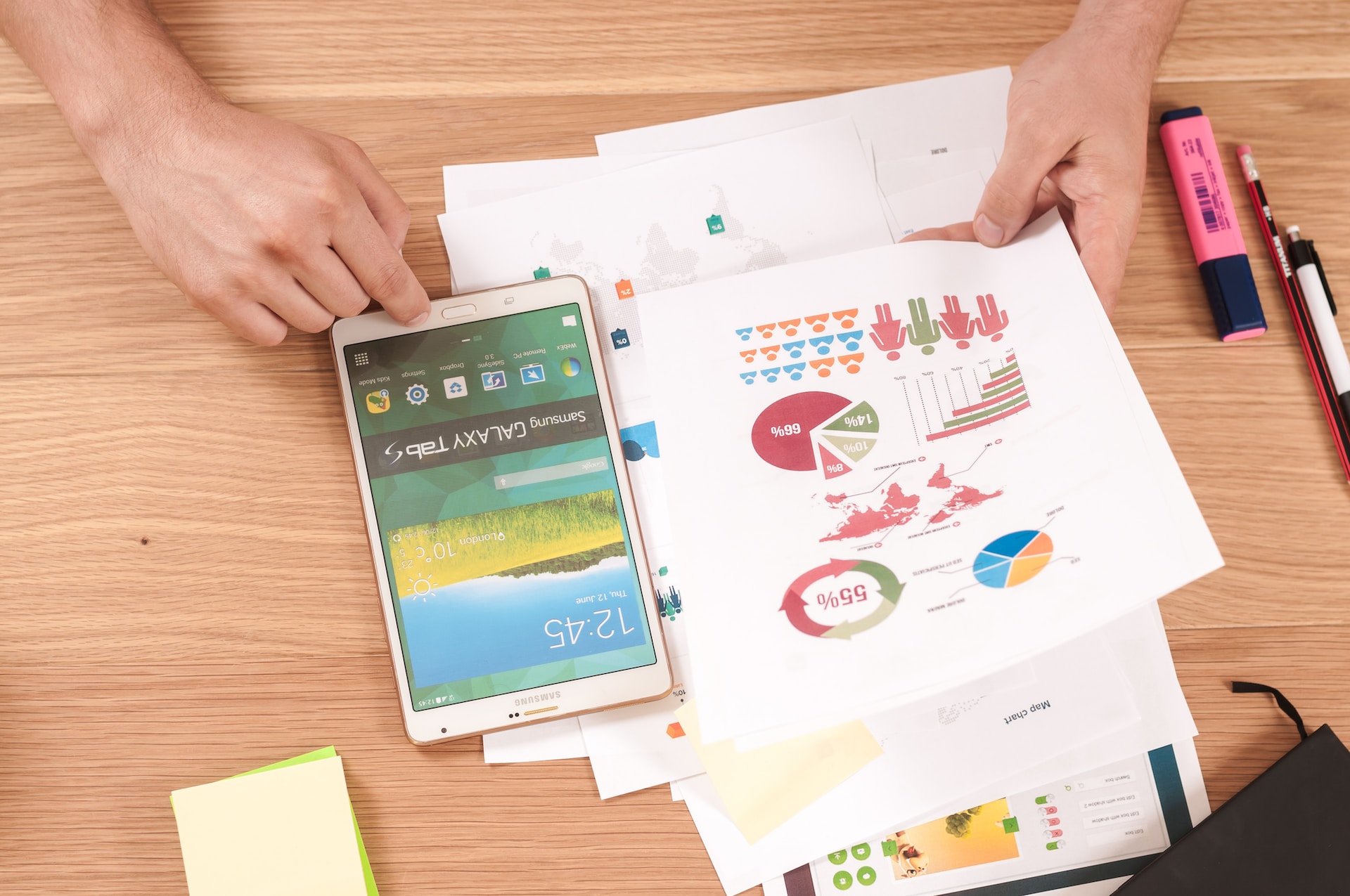