Article
The Benefits of Implementing Lean Manufacturing
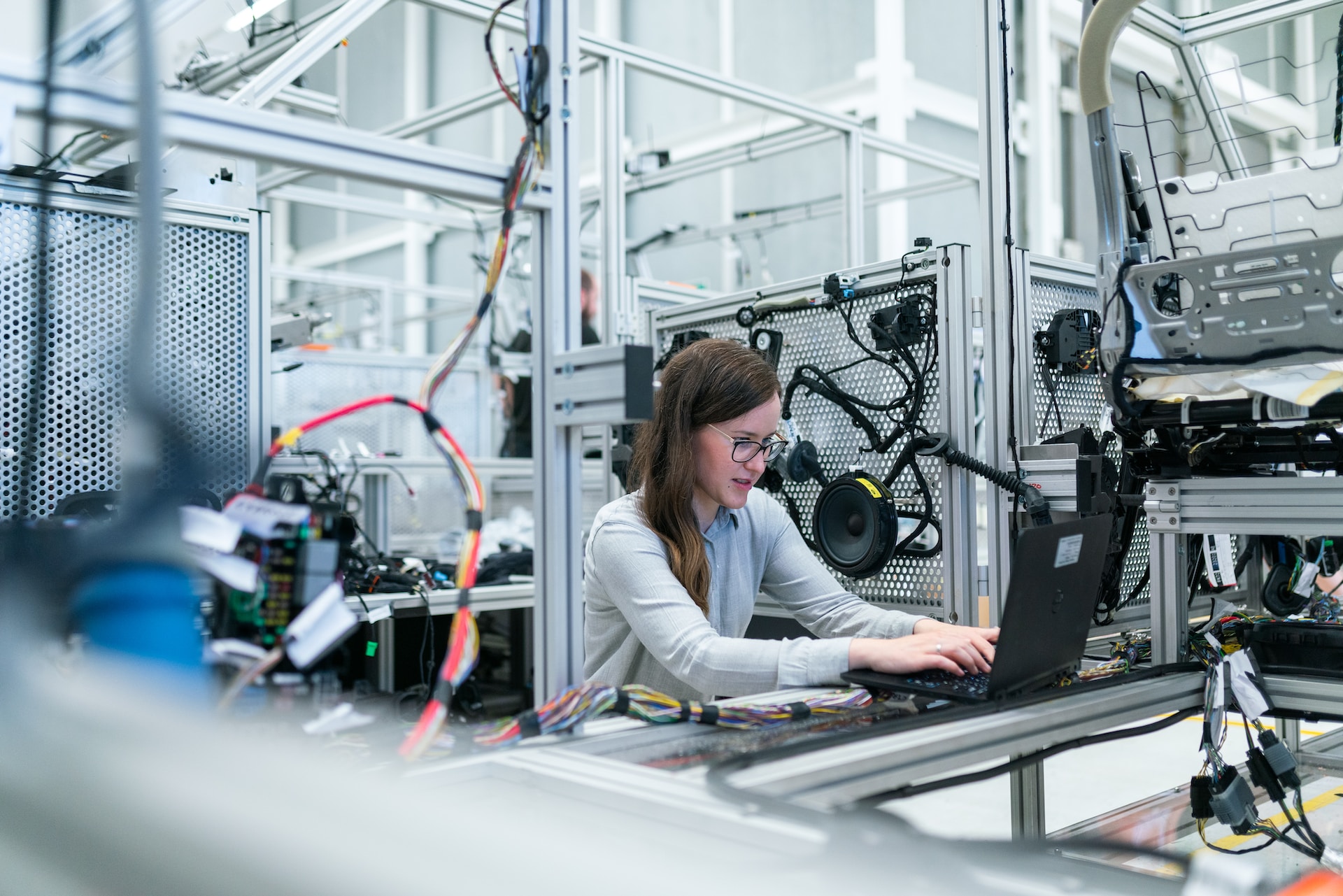
Lean manufacturing has revolutionized the way businesses operate, providing numerous benefits that help organizations thrive in today's competitive market. By adopting lean principles, companies can optimize their production processes, enhance efficiency, reduce costs, improve product quality, and boost employee morale. In this article, we will explore the advantages of implementing lean manufacturing and how it can positively impact your business.
Understanding Lean Manufacturing
Lean manufacturing is a systematic approach to process improvement that focuses on eliminating waste while maximizing value for the customer. It aims to create a streamlined and efficient production system by continuously identifying and eliminating non-value-added activities.
But what exactly is waste in the context of lean manufacturing? Waste refers to any activity or process that does not add value to the final product or service. This can include things like excess inventory, overproduction, unnecessary transportation, waiting time, defects, and even excessive motion by employees. Lean manufacturing seeks to minimize or eliminate these wasteful activities to optimize the production process.
The Principles of Lean Manufacturing
At the heart of lean manufacturing are a set of core principles that guide its implementation. These principles act as a compass, providing organizations with a clear direction to follow in their pursuit of operational excellence. Let's take a closer look at each of these principles:
- Identifying customer value: The first step in lean manufacturing is understanding what customers truly value. By identifying the specific features, quality, and functionality that customers desire, organizations can align their production processes to deliver maximum value.
- Mapping the value stream: Once customer value is identified, the next step is to map out the entire value stream. This involves documenting all the steps and processes involved in transforming raw materials into a finished product or service. By visualizing the value stream, organizations can identify areas of waste and opportunities for improvement.
- Creating flow: Flow refers to the smooth and uninterrupted movement of products or services through the value stream. Lean manufacturing emphasizes the need to eliminate bottlenecks, reduce cycle times, and ensure a continuous flow of value. This principle encourages organizations to design their production processes in a way that minimizes interruptions and delays.
- Establishing pull: Pull is a concept that revolves around producing only what is needed, when it is needed. Instead of relying on forecasts and pushing products into the market, lean manufacturing encourages organizations to establish a pull system, where production is triggered by actual customer demand. This helps minimize inventory levels and reduces the risk of overproduction.
- Pursuing perfection: The pursuit of perfection is an ongoing journey in lean manufacturing. Organizations are encouraged to continuously strive for improvement, seeking to eliminate any remaining waste and inefficiencies. This principle emphasizes the importance of a culture of continuous improvement, where everyone in the organization is engaged in finding better ways of doing things.
By aligning their operations with these principles, companies can significantly enhance their efficiency and effectiveness. Lean manufacturing is not just a set of tools and techniques; it is a mindset and a way of thinking that permeates the entire organization. It requires a commitment to continuous improvement and a willingness to challenge the status quo.
Implementing lean manufacturing can lead to a wide range of benefits, including reduced lead times, improved quality, increased customer satisfaction, higher productivity, and lower costs. However, it is important to note that lean manufacturing is not a one-size-fits-all solution. Each organization needs to tailor its approach to fit its unique circumstances and challenges.
In conclusion, lean manufacturing is a powerful methodology that can help organizations transform their operations and achieve sustainable competitive advantage. By eliminating waste, optimizing processes, and focusing on customer value, companies can create a lean and agile production system that is responsive to changing market demands. Embracing lean manufacturing is not just about improving operational efficiency; it is about creating a culture of continuous improvement that drives long-term success.
The Impact of Lean Manufacturing on Efficiency
Lean manufacturing is a production philosophy that aims to maximize efficiency by minimizing waste in all its forms. By identifying and eliminating sources of waste, companies can optimize their processes, reduce lead times, and increase overall productivity. This article explores the various ways in which lean manufacturing impacts efficiency in the production process.
Reducing Waste in the Production Process
One of the primary goals of lean manufacturing is to minimize waste in all its forms. This includes excess inventory, overproduction, defects, waiting times, unnecessary motion, and transportation. By meticulously analyzing each step of the production process, companies can identify areas where waste is occurring and take appropriate measures to eliminate or reduce it.
For example, excess inventory can lead to increased storage costs and the risk of obsolescence. Lean manufacturing encourages companies to implement just-in-time (JIT) inventory systems, where materials are delivered exactly when they are needed, minimizing the need for excess stock. By reducing inventory levels, companies can free up valuable space and capital, allowing for more efficient operations.
Similarly, overproduction can lead to unnecessary costs and increased lead times. Lean manufacturing advocates for producing only what is needed, when it is needed, in the required quantities. By aligning production with customer demand, companies can avoid the accumulation of excess inventory and reduce the risk of producing items that may become obsolete.
Defects in the production process can also have a significant impact on efficiency. Lean manufacturing emphasizes the importance of quality control and error prevention. By implementing rigorous quality control measures and empowering employees to identify and address defects early on, companies can reduce rework, scrap, and the associated costs. This not only improves efficiency but also enhances customer satisfaction.
Waiting times, unnecessary motion, and transportation are other sources of waste that lean manufacturing aims to eliminate. By optimizing workflow, arranging workstations ergonomically, and minimizing unnecessary movement and transportation of materials, companies can reduce non-value-added activities and improve overall efficiency.
Streamlining Operations for Greater Productivity
In addition to reducing waste, lean manufacturing also emphasizes the importance of continuously improving processes to eliminate bottlenecks and inefficiencies. By implementing lean tools and methodologies, companies can streamline their operations and achieve higher levels of productivity.
Value stream mapping is one such tool used in lean manufacturing. It involves mapping out the entire production process, from raw materials to the delivery of finished products, in order to identify areas of waste and opportunities for improvement. By visualizing the flow of materials and information, companies can identify bottlenecks and implement changes to streamline the process.
The 5S methodology is another key aspect of lean manufacturing. It focuses on organizing the workplace to optimize efficiency and productivity. The five pillars of 5S are sort, set in order, shine, standardize, and sustain. By implementing these principles, companies can create a clean and organized work environment, reduce the time wasted searching for tools and materials, and improve overall efficiency.
Standardized work procedures are also essential in lean manufacturing. By establishing clear and standardized processes, companies can eliminate variations and inconsistencies in how tasks are performed. This ensures that each employee follows the most efficient and effective method, leading to improved productivity and quality.
In conclusion, lean manufacturing has a significant impact on efficiency in the production process. By reducing waste and streamlining operations, companies can optimize their processes, reduce lead times, and increase overall productivity. Implementing lean tools and methodologies empowers companies to continuously improve and achieve higher levels of efficiency, ultimately leading to greater success in today's competitive business environment.
Cost Savings from Lean Manufacturing
Cost savings are a crucial aspect of any business's success, and lean manufacturing is a proven strategy to achieve significant reductions in operational expenses. By implementing lean principles, companies can streamline their processes, eliminate waste, and optimize resource utilization, resulting in substantial cost savings and improved profitability.
Lowering Operational Costs
One of the primary benefits of lean manufacturing is its ability to lower operational costs. By identifying and eliminating non-value-added activities, companies can streamline their operations and reduce unnecessary expenses. Lean practices focus on improving efficiency and productivity, ensuring that every step in the production process adds value to the final product.
Additionally, lean manufacturing emphasizes process optimization, allowing companies to identify bottlenecks and implement improvements. By streamlining workflows and eliminating unnecessary steps, businesses can reduce labor costs, minimize equipment downtime, and enhance overall operational efficiency.
Furthermore, lean manufacturing enables companies to improve resource utilization. By analyzing production data and implementing effective scheduling techniques, businesses can ensure that resources, such as materials and machinery, are used efficiently. This optimization leads to reduced costs associated with overutilization or underutilization of resources.
Minimizing Inventory Costs
Excess inventory is not only a drain on capital but also incurs additional costs, such as storage, insurance, and obsolescence. Lean manufacturing provides effective strategies to minimize inventory levels and optimize inventory management.
One such strategy is implementing just-in-time (JIT) production, where materials are delivered to the production line exactly when they are needed. By reducing inventory to the bare minimum required for production, companies can minimize carrying costs and free up valuable capital for other business initiatives.
In addition to JIT, lean manufacturing encourages the use of kanban systems. Kanban is a visual signaling system that helps companies manage inventory levels effectively. By using kanban cards or electronic systems, businesses can maintain optimal inventory levels, ensuring that materials are replenished only when necessary, thereby reducing holding costs.
Moreover, lean manufacturing promotes a culture of continuous improvement, encouraging employees to identify and eliminate waste throughout the supply chain. By fostering a mindset of waste reduction, companies can further minimize inventory costs and enhance overall efficiency.
In conclusion, lean manufacturing offers numerous opportunities for cost savings. By eliminating non-value-added activities, optimizing processes, and minimizing inventory levels, companies can achieve significant reductions in operational expenses. Embracing lean principles not only leads to cost savings but also enhances overall profitability, positioning businesses for long-term success.
Improving Quality with Lean Manufacturing
Enhancing Product Quality
Quality is a critical aspect of lean manufacturing. By focusing on identifying and eliminating defects at their source, companies can enhance the overall quality of their products. This, in turn, leads to reduced rework, increased customer satisfaction, and lower costs associated with quality issues.
Increasing Customer Satisfaction
Lean manufacturing approaches the production process from a customer-centric perspective. By delivering products that meet or exceed customer expectations, businesses can enhance customer satisfaction, build strong relationships, and gain a competitive edge in the marketplace.
Lean Manufacturing and Employee Morale
Promoting a Culture of Continuous Improvement
Lean manufacturing encourages employees to actively contribute to process improvement initiatives. By involving employees in problem-solving, encouraging their suggestions, and recognizing their efforts, companies can foster a culture of continuous improvement. This not only boosts employee morale but also enhances overall operational effectiveness.
Empowering Employees through Lean Practices
Lean manufacturing empowers employees by giving them the tools and freedom to make decisions and take ownership of their work. This autonomy fosters a sense of empowerment, leading to increased job satisfaction, higher employee engagement, and improved performance.
Implementing lean manufacturing principles can yield a wide range of benefits for businesses of all sizes and across industries. By embracing lean principles, companies can optimize their operations, reduce costs, improve product quality, and create a culture of continuous improvement. In today's fast-paced and competitive landscape, lean manufacturing is not just an option; it's a necessity for businesses seeking sustainable growth and success.
Similar Blog Posts
Article
The Benefits of Implementing Lean Manufacturing
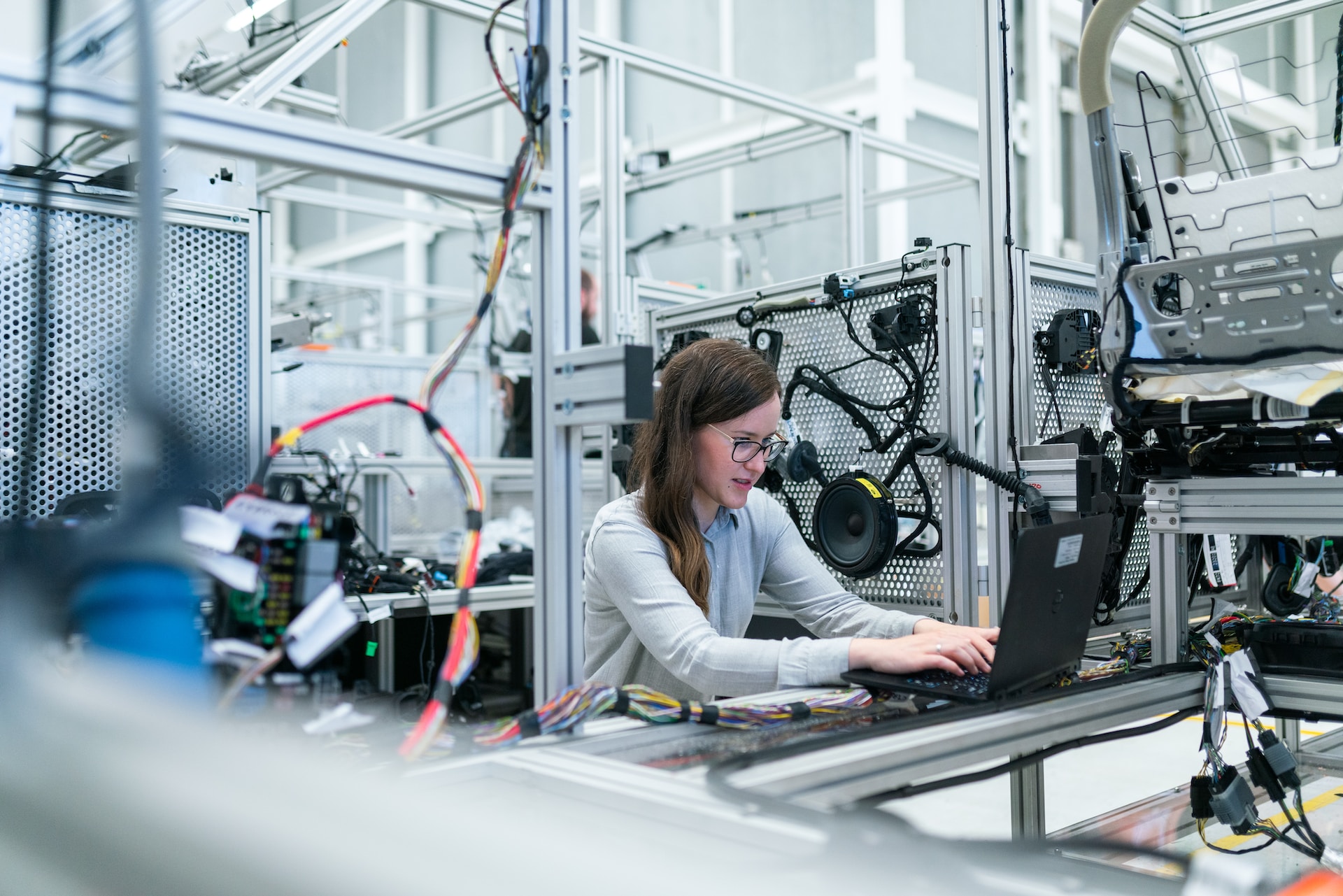
Lean manufacturing has revolutionized the way businesses operate, providing numerous benefits that help organizations thrive in today's competitive market. By adopting lean principles, companies can optimize their production processes, enhance efficiency, reduce costs, improve product quality, and boost employee morale. In this article, we will explore the advantages of implementing lean manufacturing and how it can positively impact your business.
Understanding Lean Manufacturing
Lean manufacturing is a systematic approach to process improvement that focuses on eliminating waste while maximizing value for the customer. It aims to create a streamlined and efficient production system by continuously identifying and eliminating non-value-added activities.
But what exactly is waste in the context of lean manufacturing? Waste refers to any activity or process that does not add value to the final product or service. This can include things like excess inventory, overproduction, unnecessary transportation, waiting time, defects, and even excessive motion by employees. Lean manufacturing seeks to minimize or eliminate these wasteful activities to optimize the production process.
The Principles of Lean Manufacturing
At the heart of lean manufacturing are a set of core principles that guide its implementation. These principles act as a compass, providing organizations with a clear direction to follow in their pursuit of operational excellence. Let's take a closer look at each of these principles:
- Identifying customer value: The first step in lean manufacturing is understanding what customers truly value. By identifying the specific features, quality, and functionality that customers desire, organizations can align their production processes to deliver maximum value.
- Mapping the value stream: Once customer value is identified, the next step is to map out the entire value stream. This involves documenting all the steps and processes involved in transforming raw materials into a finished product or service. By visualizing the value stream, organizations can identify areas of waste and opportunities for improvement.
- Creating flow: Flow refers to the smooth and uninterrupted movement of products or services through the value stream. Lean manufacturing emphasizes the need to eliminate bottlenecks, reduce cycle times, and ensure a continuous flow of value. This principle encourages organizations to design their production processes in a way that minimizes interruptions and delays.
- Establishing pull: Pull is a concept that revolves around producing only what is needed, when it is needed. Instead of relying on forecasts and pushing products into the market, lean manufacturing encourages organizations to establish a pull system, where production is triggered by actual customer demand. This helps minimize inventory levels and reduces the risk of overproduction.
- Pursuing perfection: The pursuit of perfection is an ongoing journey in lean manufacturing. Organizations are encouraged to continuously strive for improvement, seeking to eliminate any remaining waste and inefficiencies. This principle emphasizes the importance of a culture of continuous improvement, where everyone in the organization is engaged in finding better ways of doing things.
By aligning their operations with these principles, companies can significantly enhance their efficiency and effectiveness. Lean manufacturing is not just a set of tools and techniques; it is a mindset and a way of thinking that permeates the entire organization. It requires a commitment to continuous improvement and a willingness to challenge the status quo.
Implementing lean manufacturing can lead to a wide range of benefits, including reduced lead times, improved quality, increased customer satisfaction, higher productivity, and lower costs. However, it is important to note that lean manufacturing is not a one-size-fits-all solution. Each organization needs to tailor its approach to fit its unique circumstances and challenges.
In conclusion, lean manufacturing is a powerful methodology that can help organizations transform their operations and achieve sustainable competitive advantage. By eliminating waste, optimizing processes, and focusing on customer value, companies can create a lean and agile production system that is responsive to changing market demands. Embracing lean manufacturing is not just about improving operational efficiency; it is about creating a culture of continuous improvement that drives long-term success.
The Impact of Lean Manufacturing on Efficiency
Lean manufacturing is a production philosophy that aims to maximize efficiency by minimizing waste in all its forms. By identifying and eliminating sources of waste, companies can optimize their processes, reduce lead times, and increase overall productivity. This article explores the various ways in which lean manufacturing impacts efficiency in the production process.
Reducing Waste in the Production Process
One of the primary goals of lean manufacturing is to minimize waste in all its forms. This includes excess inventory, overproduction, defects, waiting times, unnecessary motion, and transportation. By meticulously analyzing each step of the production process, companies can identify areas where waste is occurring and take appropriate measures to eliminate or reduce it.
For example, excess inventory can lead to increased storage costs and the risk of obsolescence. Lean manufacturing encourages companies to implement just-in-time (JIT) inventory systems, where materials are delivered exactly when they are needed, minimizing the need for excess stock. By reducing inventory levels, companies can free up valuable space and capital, allowing for more efficient operations.
Similarly, overproduction can lead to unnecessary costs and increased lead times. Lean manufacturing advocates for producing only what is needed, when it is needed, in the required quantities. By aligning production with customer demand, companies can avoid the accumulation of excess inventory and reduce the risk of producing items that may become obsolete.
Defects in the production process can also have a significant impact on efficiency. Lean manufacturing emphasizes the importance of quality control and error prevention. By implementing rigorous quality control measures and empowering employees to identify and address defects early on, companies can reduce rework, scrap, and the associated costs. This not only improves efficiency but also enhances customer satisfaction.
Waiting times, unnecessary motion, and transportation are other sources of waste that lean manufacturing aims to eliminate. By optimizing workflow, arranging workstations ergonomically, and minimizing unnecessary movement and transportation of materials, companies can reduce non-value-added activities and improve overall efficiency.
Streamlining Operations for Greater Productivity
In addition to reducing waste, lean manufacturing also emphasizes the importance of continuously improving processes to eliminate bottlenecks and inefficiencies. By implementing lean tools and methodologies, companies can streamline their operations and achieve higher levels of productivity.
Value stream mapping is one such tool used in lean manufacturing. It involves mapping out the entire production process, from raw materials to the delivery of finished products, in order to identify areas of waste and opportunities for improvement. By visualizing the flow of materials and information, companies can identify bottlenecks and implement changes to streamline the process.
The 5S methodology is another key aspect of lean manufacturing. It focuses on organizing the workplace to optimize efficiency and productivity. The five pillars of 5S are sort, set in order, shine, standardize, and sustain. By implementing these principles, companies can create a clean and organized work environment, reduce the time wasted searching for tools and materials, and improve overall efficiency.
Standardized work procedures are also essential in lean manufacturing. By establishing clear and standardized processes, companies can eliminate variations and inconsistencies in how tasks are performed. This ensures that each employee follows the most efficient and effective method, leading to improved productivity and quality.
In conclusion, lean manufacturing has a significant impact on efficiency in the production process. By reducing waste and streamlining operations, companies can optimize their processes, reduce lead times, and increase overall productivity. Implementing lean tools and methodologies empowers companies to continuously improve and achieve higher levels of efficiency, ultimately leading to greater success in today's competitive business environment.
Cost Savings from Lean Manufacturing
Cost savings are a crucial aspect of any business's success, and lean manufacturing is a proven strategy to achieve significant reductions in operational expenses. By implementing lean principles, companies can streamline their processes, eliminate waste, and optimize resource utilization, resulting in substantial cost savings and improved profitability.
Lowering Operational Costs
One of the primary benefits of lean manufacturing is its ability to lower operational costs. By identifying and eliminating non-value-added activities, companies can streamline their operations and reduce unnecessary expenses. Lean practices focus on improving efficiency and productivity, ensuring that every step in the production process adds value to the final product.
Additionally, lean manufacturing emphasizes process optimization, allowing companies to identify bottlenecks and implement improvements. By streamlining workflows and eliminating unnecessary steps, businesses can reduce labor costs, minimize equipment downtime, and enhance overall operational efficiency.
Furthermore, lean manufacturing enables companies to improve resource utilization. By analyzing production data and implementing effective scheduling techniques, businesses can ensure that resources, such as materials and machinery, are used efficiently. This optimization leads to reduced costs associated with overutilization or underutilization of resources.
Minimizing Inventory Costs
Excess inventory is not only a drain on capital but also incurs additional costs, such as storage, insurance, and obsolescence. Lean manufacturing provides effective strategies to minimize inventory levels and optimize inventory management.
One such strategy is implementing just-in-time (JIT) production, where materials are delivered to the production line exactly when they are needed. By reducing inventory to the bare minimum required for production, companies can minimize carrying costs and free up valuable capital for other business initiatives.
In addition to JIT, lean manufacturing encourages the use of kanban systems. Kanban is a visual signaling system that helps companies manage inventory levels effectively. By using kanban cards or electronic systems, businesses can maintain optimal inventory levels, ensuring that materials are replenished only when necessary, thereby reducing holding costs.
Moreover, lean manufacturing promotes a culture of continuous improvement, encouraging employees to identify and eliminate waste throughout the supply chain. By fostering a mindset of waste reduction, companies can further minimize inventory costs and enhance overall efficiency.
In conclusion, lean manufacturing offers numerous opportunities for cost savings. By eliminating non-value-added activities, optimizing processes, and minimizing inventory levels, companies can achieve significant reductions in operational expenses. Embracing lean principles not only leads to cost savings but also enhances overall profitability, positioning businesses for long-term success.
Improving Quality with Lean Manufacturing
Enhancing Product Quality
Quality is a critical aspect of lean manufacturing. By focusing on identifying and eliminating defects at their source, companies can enhance the overall quality of their products. This, in turn, leads to reduced rework, increased customer satisfaction, and lower costs associated with quality issues.
Increasing Customer Satisfaction
Lean manufacturing approaches the production process from a customer-centric perspective. By delivering products that meet or exceed customer expectations, businesses can enhance customer satisfaction, build strong relationships, and gain a competitive edge in the marketplace.
Lean Manufacturing and Employee Morale
Promoting a Culture of Continuous Improvement
Lean manufacturing encourages employees to actively contribute to process improvement initiatives. By involving employees in problem-solving, encouraging their suggestions, and recognizing their efforts, companies can foster a culture of continuous improvement. This not only boosts employee morale but also enhances overall operational effectiveness.
Empowering Employees through Lean Practices
Lean manufacturing empowers employees by giving them the tools and freedom to make decisions and take ownership of their work. This autonomy fosters a sense of empowerment, leading to increased job satisfaction, higher employee engagement, and improved performance.
Implementing lean manufacturing principles can yield a wide range of benefits for businesses of all sizes and across industries. By embracing lean principles, companies can optimize their operations, reduce costs, improve product quality, and create a culture of continuous improvement. In today's fast-paced and competitive landscape, lean manufacturing is not just an option; it's a necessity for businesses seeking sustainable growth and success.
Article
The Benefits of Implementing Lean Manufacturing
•
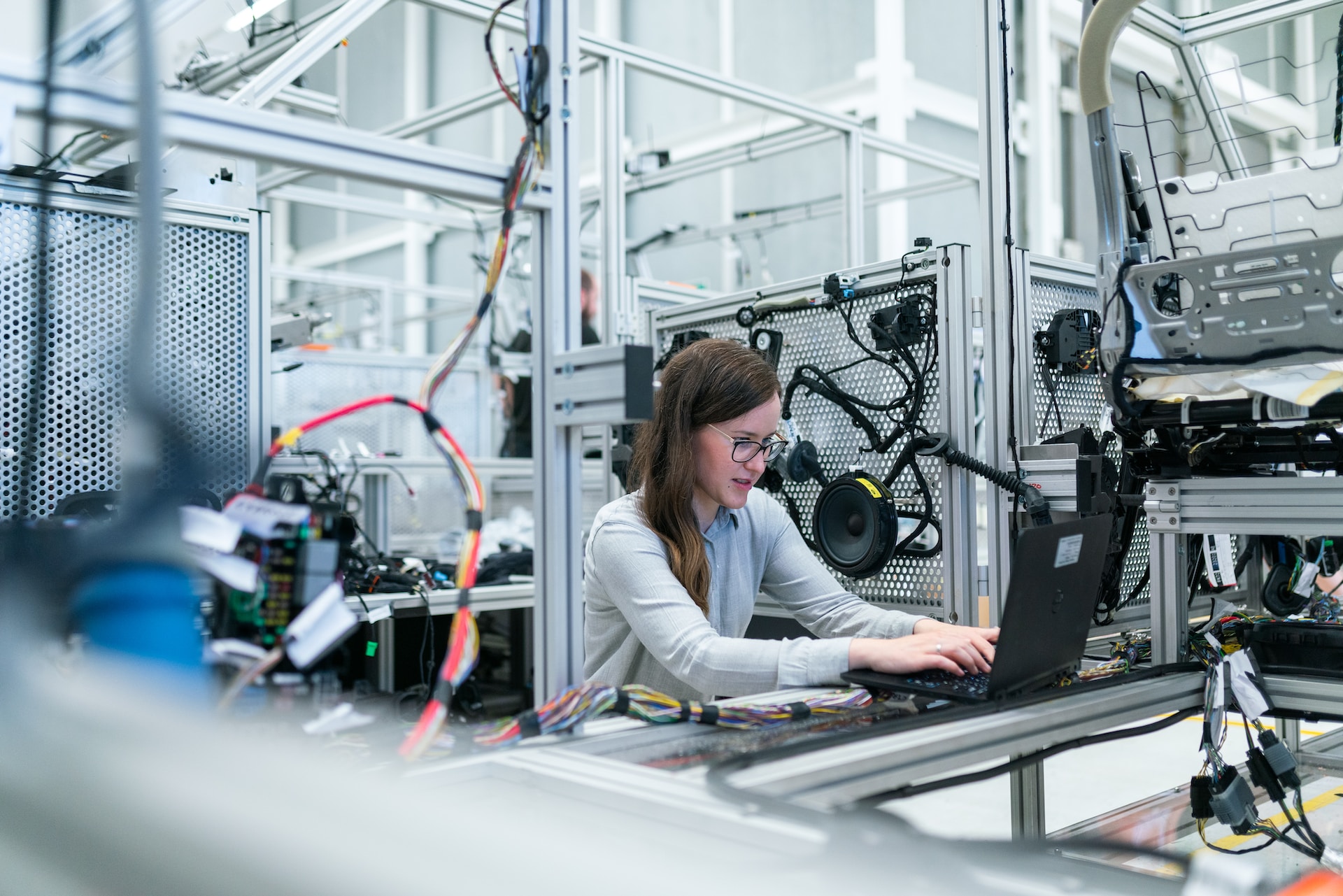