Article
Understanding Value Stream Mapping: A Comprehensive Guide
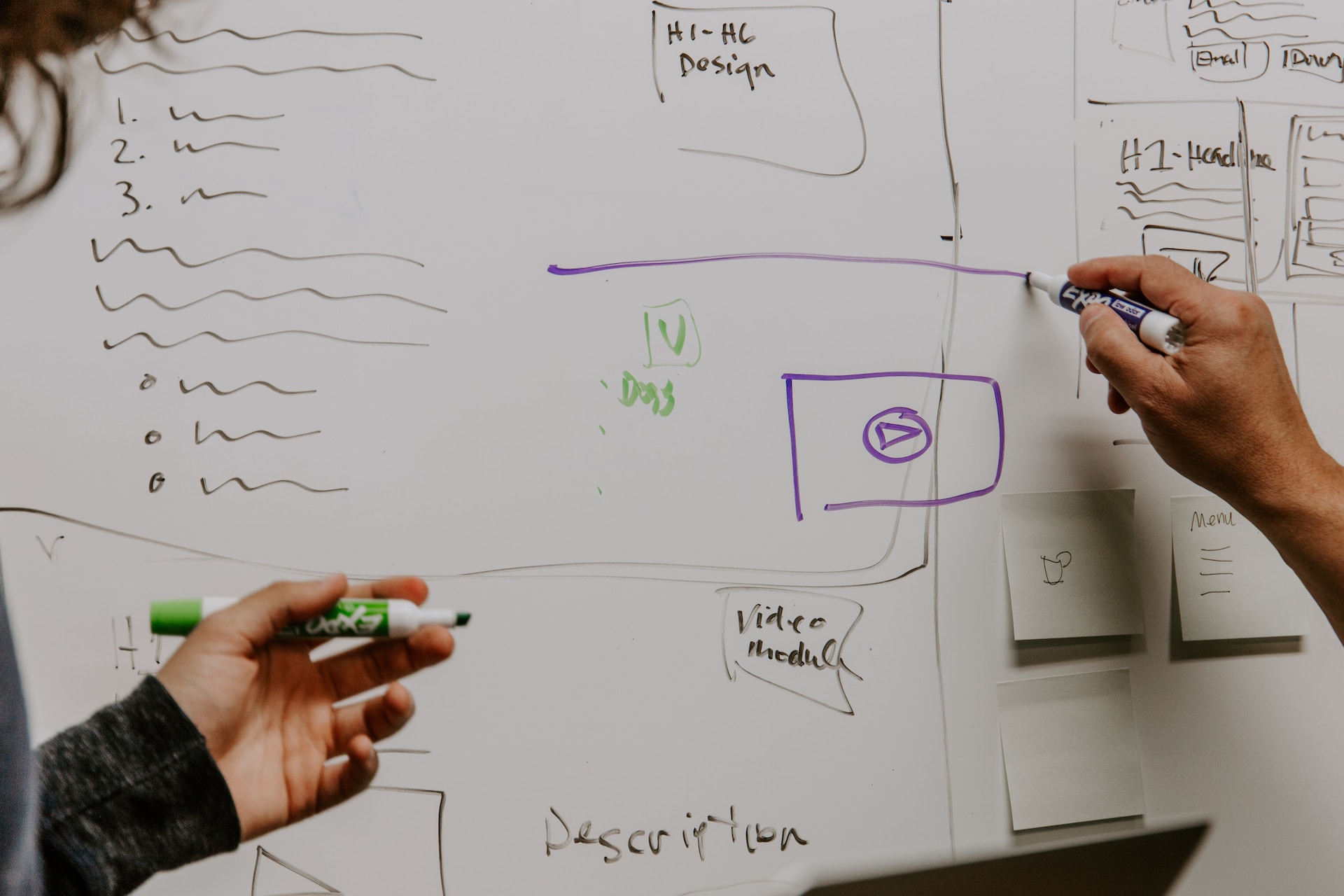
Value Stream Mapping (VSM) is a powerful lean management tool that allows organizations to visualize, analyze, and improve their core processes. By providing a comprehensive overview of the entire value stream, from raw materials to customer delivery, VSM helps identify waste, streamline operations, and enhance overall efficiency. In this guide, we will explore the key concepts, steps, and benefits of value stream mapping, as well as provide practical tips for successful implementation.
Introduction to Value Stream Mapping
In order to grasp the essence of value stream mapping, it is important to understand what it entails. At its core, value stream mapping is a visual representation of the flow of materials, information, and value-added activities in a process or system. It allows organizations to identify bottlenecks, redundancies, and areas of improvement by mapping out the current state and envisioning the future state of the value stream. By doing so, companies can make data-driven decisions and drive continuous improvement initiatives.
Value stream mapping provides a comprehensive view of how value flows through a process or system. It goes beyond just looking at individual steps and focuses on the entire value stream, from supplier interactions to customer interactions. This holistic understanding allows organizations to identify areas of waste and inefficiency and make targeted improvements.
When conducting value stream mapping, organizations involve cross-functional teams to ensure that all perspectives are considered. This collaborative approach fosters a sense of ownership and accountability among team members, leading to more effective problem-solving and decision-making.
What is Value Stream Mapping?
Value stream mapping is a lean management technique that originated from the Toyota Production System. It provides a holistic understanding of how value flows through a process, highlighting areas of waste and inefficiency. The value stream encompasses every step involved in delivering a product or service, including supplier interactions, internal processes, and customer interactions. By visualizing and analyzing the value stream, organizations can identify opportunities for improvement and create a more streamlined and customer-focused process.
Value stream mapping involves creating a visual representation of the current state value stream and the future state value stream. The current state map helps organizations identify areas of business waste, such as excess inventory, unnecessary transportation, or overprocessing. The future state map, on the other hand, outlines the ideal state of the value stream, incorporating improvements and eliminating waste.
Value stream mapping is not a one-time exercise. It is an ongoing process that organizations use to continuously improve their operations. By regularly reviewing and updating the value stream maps, organizations can monitor their progress and identify new areas for improvement.
The Importance of Value Stream Mapping
Value stream mapping is crucial for organizations seeking to optimize their processes and enhance business performance. By identifying waste and value-added activities within the value stream, companies can eliminate non-value-added tasks, reduce lead times, improve quality, and increase customer satisfaction. Additionally, value stream mapping promotes cross-functional collaboration, as it requires input from various departments and stakeholders. By involving all relevant parties, organizations can foster a culture of continuous improvement and drive sustainable change.
One of the key benefits of value stream mapping is its ability to uncover hidden opportunities for improvement. By visualizing the entire value stream, organizations can identify areas that may have been overlooked or considered as "just the way things are done." This fresh perspective allows organizations to challenge the status quo and implement innovative solutions.
Furthermore, value stream mapping enables organizations to align their processes with customer needs and expectations. By understanding the value stream from the customer's perspective, organizations can identify areas where value is not being delivered and make the necessary changes to improve customer satisfaction.
Overall, value stream mapping is a powerful tool for organizations looking to optimize their operations, reduce waste, and create value for their customers. It provides a structured approach to process improvement and empowers organizations to make data-driven decisions that lead to tangible results.
The History of Value Stream Mapping
The roots of value stream mapping can be traced back to the early years of the Toyota Production System, which revolutionized the manufacturing industry by introducing lean production principles. Over time, value stream mapping has evolved and expanded beyond the automotive industry to other sectors, including healthcare, service, and information technology. Understanding the history of value stream mapping can provide valuable insights into its development and application.
Origins and Evolution
Value stream mapping emerged in the 1970s as a key component of the Toyota Production System's focus on waste reduction and continuous improvement. Toyota recognized the importance of visualizing the entire value stream to identify bottlenecks, excessive inventory, and non-value-added activities. By mapping out the value stream, Toyota was able to streamline its production processes and respond more effectively to customer demand.
Key Milestones in Value Stream Mapping
Over the years, value stream mapping has evolved as a result of advancements in technology, changes in business models, and the need for greater efficiency. The advent of computer modeling and simulation tools has made it easier to create detailed and accurate value stream maps. Additionally, the application of value stream mapping has expanded beyond the realm of manufacturing, with organizations in various industries adopting the technique to improve their operations.
Core Concepts of Value Stream Mapping
Before diving into the practical aspects of value stream mapping, it is important to understand the core concepts that underpin this powerful technique. By familiarizing ourselves with these foundational elements, we can better appreciate the value and significance of value stream mapping in driving operational excellence.
The Value Stream
The value stream represents the flow of products or services from the supplier to the customer. It encompasses all the activities, processes, and interactions required to convert raw materials into finished goods or deliver a service to the end-user. The value stream can be divided into three main components: the supplier, the producer, and the customer. Visualizing and understanding the value stream is essential for identifying waste, optimizing processes, and delivering value to the customer.
Mapping the Stream
The mapping phase of value stream mapping involves creating a visual representation of the current state and future state of the value stream. This is typically done using standardized symbols and icons to represent different activities, inputs, outputs, and flow. By accurately mapping the value stream, organizations can gain insights into the flow of materials, information, and activities, and identify areas of improvement. The mapping process provides a shared understanding of the value stream and serves as a foundation for improvement efforts.
Identifying Waste
One of the key objectives of value stream mapping is to identify waste in the value stream. Waste refers to any activity, process, or resource that does not add value from the customer's perspective. There are eight commonly recognized forms of waste: overproduction, waiting, transportation, overprocessing, inventory, motion, defects, and underutilized talent. By identifying and eliminating waste, organizations can improve efficiency, reduce costs, and enhance customer satisfaction.
Steps to Create a Value Stream Map
Creating a value stream map involves a systematic approach that requires gathering data, analyzing the current state, and envisioning the future state. By following these steps, organizations can create a comprehensive and accurate representation of their value stream, identify areas of improvement, and develop a roadmap for change.
Gathering Data
The first step in value stream mapping is to gather data about the current state of the value stream. This involves observing and documenting the flow of materials, information, and activities throughout the process. Data can be collected through direct observation, interviews with employees, and analysis of existing documentation, such as process maps and standard operating procedures. The data collected should provide a clear understanding of the current state and serve as a basis for future analysis and improvement efforts.
Drawing the Current State Map
Once the data has been collected, the next step is to create a visual representation of the current state of the value stream. This involves mapping out the flow of materials, information, and activities using appropriate symbols and icons. The current state map should accurately depict the current state of the value stream, including all inputs, outputs, and areas of waste. The current state map serves as a baseline against which future improvements can be measured.
Envisioning the Future State Map
After mapping the current state, the next step is to envision the future state of the value stream. This involves identifying areas of improvement, eliminating waste, and designing a more efficient and customer-focused process. The future state map should outline the ideal flow of materials, information, and activities, taking into account best practices and organizational goals. The future state map serves as a roadmap for improvement and provides a vision of the desired future state of the value stream.
Implementing Value Stream Mapping in Your Organization
Implementing value stream mapping in your organization requires careful planning, effective leadership, and strong commitment from all stakeholders. While the process can be challenging, the rewards in terms of improved efficiency, reduced waste, and increased customer satisfaction are worth the effort. In this section, we will explore some practical tips and strategies to successfully implement value stream mapping in your organization.
Preparing Your Team
One of the key factors in a successful value stream mapping implementation is having a well-prepared and engaged team. It is important to involve stakeholders from different departments and levels of the organization, as their insights and perspectives are essential for a comprehensive understanding of the value stream. Providing training and education on value stream mapping techniques and principles can also help prepare the team for the mapping process and foster a culture of continuous improvement.
Common Challenges and Solutions
Implementing value stream mapping can present various challenges, ranging from resistance to change to lack of data and organizational complexity. It is important to anticipate these challenges and have strategies in place to overcome them. Some common challenges include resistance to new ways of working, difficulty gathering accurate and reliable data, and complexity within the value stream. By addressing these challenges head-on and seeking solutions collaboratively, organizations can overcome obstacles and ensure the successful implementation of value stream mapping.
Case Studies of Successful Implementation
There are numerous examples of organizations that have successfully implemented value stream mapping and reaped the benefits of improved efficiency, reduced waste, and enhanced customer satisfaction. By studying these case studies, organizations can gain valuable insights into best practices, lessons learned, and innovative approaches to value stream mapping. Case studies provide real-life examples that can inspire and guide organizations in their own value stream mapping journeys.
Conclusion
Value stream mapping is a powerful tool for organizations seeking to optimize their processes and drive continuous improvement. By visualizing the value stream, identifying waste, and designing more efficient processes, organizations can streamline operations, reduce costs, and enhance customer satisfaction. While implementing value stream mapping can present challenges, the benefits far outweigh the effort. By following the steps outlined in this comprehensive guide and learning from successful case studies, organizations can embark on a journey of operational excellence and achieve sustainable improvement.
Similar Blog Posts
Article
Understanding Value Stream Mapping: A Comprehensive Guide
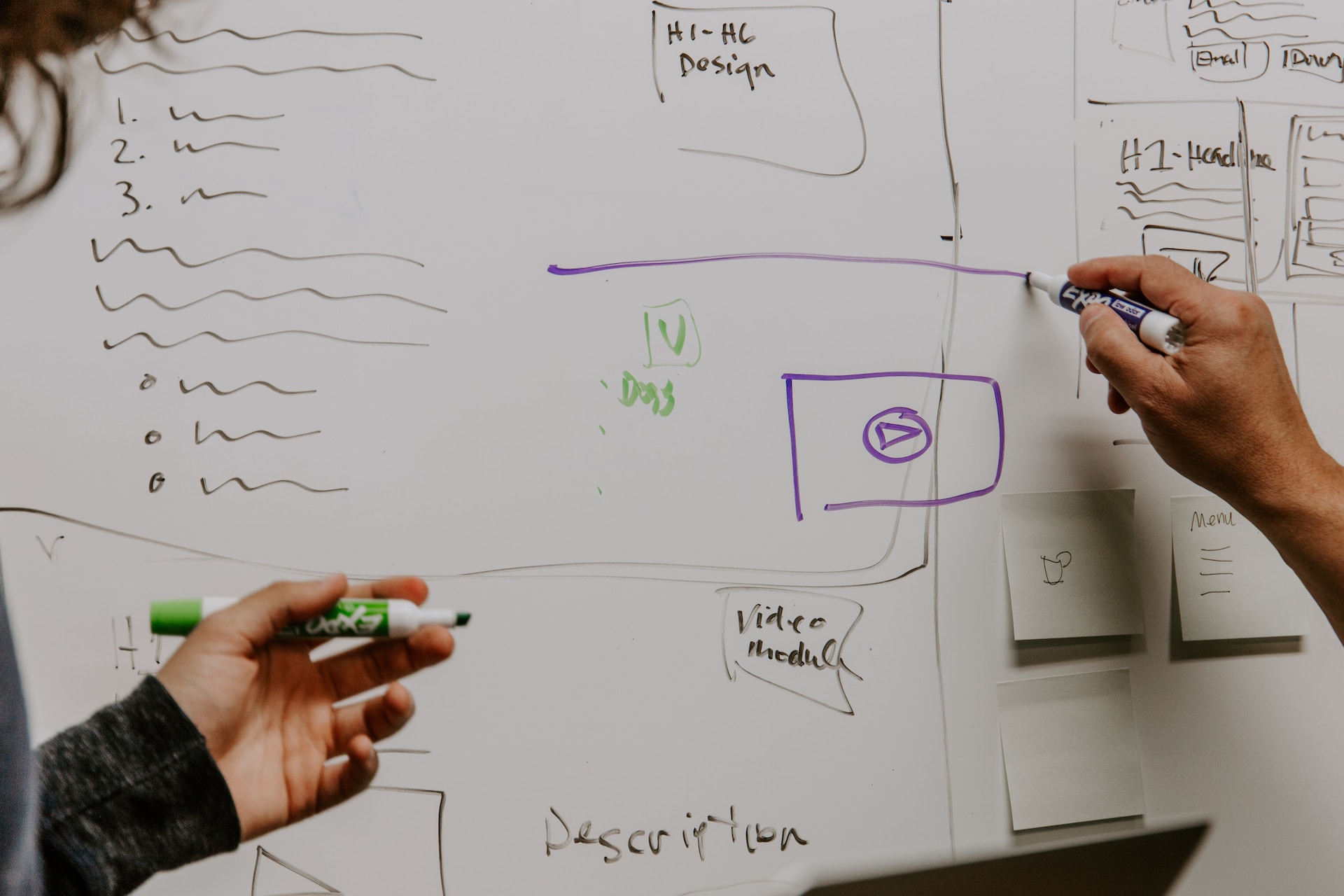
Value Stream Mapping (VSM) is a powerful lean management tool that allows organizations to visualize, analyze, and improve their core processes. By providing a comprehensive overview of the entire value stream, from raw materials to customer delivery, VSM helps identify waste, streamline operations, and enhance overall efficiency. In this guide, we will explore the key concepts, steps, and benefits of value stream mapping, as well as provide practical tips for successful implementation.
Introduction to Value Stream Mapping
In order to grasp the essence of value stream mapping, it is important to understand what it entails. At its core, value stream mapping is a visual representation of the flow of materials, information, and value-added activities in a process or system. It allows organizations to identify bottlenecks, redundancies, and areas of improvement by mapping out the current state and envisioning the future state of the value stream. By doing so, companies can make data-driven decisions and drive continuous improvement initiatives.
Value stream mapping provides a comprehensive view of how value flows through a process or system. It goes beyond just looking at individual steps and focuses on the entire value stream, from supplier interactions to customer interactions. This holistic understanding allows organizations to identify areas of waste and inefficiency and make targeted improvements.
When conducting value stream mapping, organizations involve cross-functional teams to ensure that all perspectives are considered. This collaborative approach fosters a sense of ownership and accountability among team members, leading to more effective problem-solving and decision-making.
What is Value Stream Mapping?
Value stream mapping is a lean management technique that originated from the Toyota Production System. It provides a holistic understanding of how value flows through a process, highlighting areas of waste and inefficiency. The value stream encompasses every step involved in delivering a product or service, including supplier interactions, internal processes, and customer interactions. By visualizing and analyzing the value stream, organizations can identify opportunities for improvement and create a more streamlined and customer-focused process.
Value stream mapping involves creating a visual representation of the current state value stream and the future state value stream. The current state map helps organizations identify areas of business waste, such as excess inventory, unnecessary transportation, or overprocessing. The future state map, on the other hand, outlines the ideal state of the value stream, incorporating improvements and eliminating waste.
Value stream mapping is not a one-time exercise. It is an ongoing process that organizations use to continuously improve their operations. By regularly reviewing and updating the value stream maps, organizations can monitor their progress and identify new areas for improvement.
The Importance of Value Stream Mapping
Value stream mapping is crucial for organizations seeking to optimize their processes and enhance business performance. By identifying waste and value-added activities within the value stream, companies can eliminate non-value-added tasks, reduce lead times, improve quality, and increase customer satisfaction. Additionally, value stream mapping promotes cross-functional collaboration, as it requires input from various departments and stakeholders. By involving all relevant parties, organizations can foster a culture of continuous improvement and drive sustainable change.
One of the key benefits of value stream mapping is its ability to uncover hidden opportunities for improvement. By visualizing the entire value stream, organizations can identify areas that may have been overlooked or considered as "just the way things are done." This fresh perspective allows organizations to challenge the status quo and implement innovative solutions.
Furthermore, value stream mapping enables organizations to align their processes with customer needs and expectations. By understanding the value stream from the customer's perspective, organizations can identify areas where value is not being delivered and make the necessary changes to improve customer satisfaction.
Overall, value stream mapping is a powerful tool for organizations looking to optimize their operations, reduce waste, and create value for their customers. It provides a structured approach to process improvement and empowers organizations to make data-driven decisions that lead to tangible results.
The History of Value Stream Mapping
The roots of value stream mapping can be traced back to the early years of the Toyota Production System, which revolutionized the manufacturing industry by introducing lean production principles. Over time, value stream mapping has evolved and expanded beyond the automotive industry to other sectors, including healthcare, service, and information technology. Understanding the history of value stream mapping can provide valuable insights into its development and application.
Origins and Evolution
Value stream mapping emerged in the 1970s as a key component of the Toyota Production System's focus on waste reduction and continuous improvement. Toyota recognized the importance of visualizing the entire value stream to identify bottlenecks, excessive inventory, and non-value-added activities. By mapping out the value stream, Toyota was able to streamline its production processes and respond more effectively to customer demand.
Key Milestones in Value Stream Mapping
Over the years, value stream mapping has evolved as a result of advancements in technology, changes in business models, and the need for greater efficiency. The advent of computer modeling and simulation tools has made it easier to create detailed and accurate value stream maps. Additionally, the application of value stream mapping has expanded beyond the realm of manufacturing, with organizations in various industries adopting the technique to improve their operations.
Core Concepts of Value Stream Mapping
Before diving into the practical aspects of value stream mapping, it is important to understand the core concepts that underpin this powerful technique. By familiarizing ourselves with these foundational elements, we can better appreciate the value and significance of value stream mapping in driving operational excellence.
The Value Stream
The value stream represents the flow of products or services from the supplier to the customer. It encompasses all the activities, processes, and interactions required to convert raw materials into finished goods or deliver a service to the end-user. The value stream can be divided into three main components: the supplier, the producer, and the customer. Visualizing and understanding the value stream is essential for identifying waste, optimizing processes, and delivering value to the customer.
Mapping the Stream
The mapping phase of value stream mapping involves creating a visual representation of the current state and future state of the value stream. This is typically done using standardized symbols and icons to represent different activities, inputs, outputs, and flow. By accurately mapping the value stream, organizations can gain insights into the flow of materials, information, and activities, and identify areas of improvement. The mapping process provides a shared understanding of the value stream and serves as a foundation for improvement efforts.
Identifying Waste
One of the key objectives of value stream mapping is to identify waste in the value stream. Waste refers to any activity, process, or resource that does not add value from the customer's perspective. There are eight commonly recognized forms of waste: overproduction, waiting, transportation, overprocessing, inventory, motion, defects, and underutilized talent. By identifying and eliminating waste, organizations can improve efficiency, reduce costs, and enhance customer satisfaction.
Steps to Create a Value Stream Map
Creating a value stream map involves a systematic approach that requires gathering data, analyzing the current state, and envisioning the future state. By following these steps, organizations can create a comprehensive and accurate representation of their value stream, identify areas of improvement, and develop a roadmap for change.
Gathering Data
The first step in value stream mapping is to gather data about the current state of the value stream. This involves observing and documenting the flow of materials, information, and activities throughout the process. Data can be collected through direct observation, interviews with employees, and analysis of existing documentation, such as process maps and standard operating procedures. The data collected should provide a clear understanding of the current state and serve as a basis for future analysis and improvement efforts.
Drawing the Current State Map
Once the data has been collected, the next step is to create a visual representation of the current state of the value stream. This involves mapping out the flow of materials, information, and activities using appropriate symbols and icons. The current state map should accurately depict the current state of the value stream, including all inputs, outputs, and areas of waste. The current state map serves as a baseline against which future improvements can be measured.
Envisioning the Future State Map
After mapping the current state, the next step is to envision the future state of the value stream. This involves identifying areas of improvement, eliminating waste, and designing a more efficient and customer-focused process. The future state map should outline the ideal flow of materials, information, and activities, taking into account best practices and organizational goals. The future state map serves as a roadmap for improvement and provides a vision of the desired future state of the value stream.
Implementing Value Stream Mapping in Your Organization
Implementing value stream mapping in your organization requires careful planning, effective leadership, and strong commitment from all stakeholders. While the process can be challenging, the rewards in terms of improved efficiency, reduced waste, and increased customer satisfaction are worth the effort. In this section, we will explore some practical tips and strategies to successfully implement value stream mapping in your organization.
Preparing Your Team
One of the key factors in a successful value stream mapping implementation is having a well-prepared and engaged team. It is important to involve stakeholders from different departments and levels of the organization, as their insights and perspectives are essential for a comprehensive understanding of the value stream. Providing training and education on value stream mapping techniques and principles can also help prepare the team for the mapping process and foster a culture of continuous improvement.
Common Challenges and Solutions
Implementing value stream mapping can present various challenges, ranging from resistance to change to lack of data and organizational complexity. It is important to anticipate these challenges and have strategies in place to overcome them. Some common challenges include resistance to new ways of working, difficulty gathering accurate and reliable data, and complexity within the value stream. By addressing these challenges head-on and seeking solutions collaboratively, organizations can overcome obstacles and ensure the successful implementation of value stream mapping.
Case Studies of Successful Implementation
There are numerous examples of organizations that have successfully implemented value stream mapping and reaped the benefits of improved efficiency, reduced waste, and enhanced customer satisfaction. By studying these case studies, organizations can gain valuable insights into best practices, lessons learned, and innovative approaches to value stream mapping. Case studies provide real-life examples that can inspire and guide organizations in their own value stream mapping journeys.
Conclusion
Value stream mapping is a powerful tool for organizations seeking to optimize their processes and drive continuous improvement. By visualizing the value stream, identifying waste, and designing more efficient processes, organizations can streamline operations, reduce costs, and enhance customer satisfaction. While implementing value stream mapping can present challenges, the benefits far outweigh the effort. By following the steps outlined in this comprehensive guide and learning from successful case studies, organizations can embark on a journey of operational excellence and achieve sustainable improvement.
Article
Understanding Value Stream Mapping: A Comprehensive Guide
•
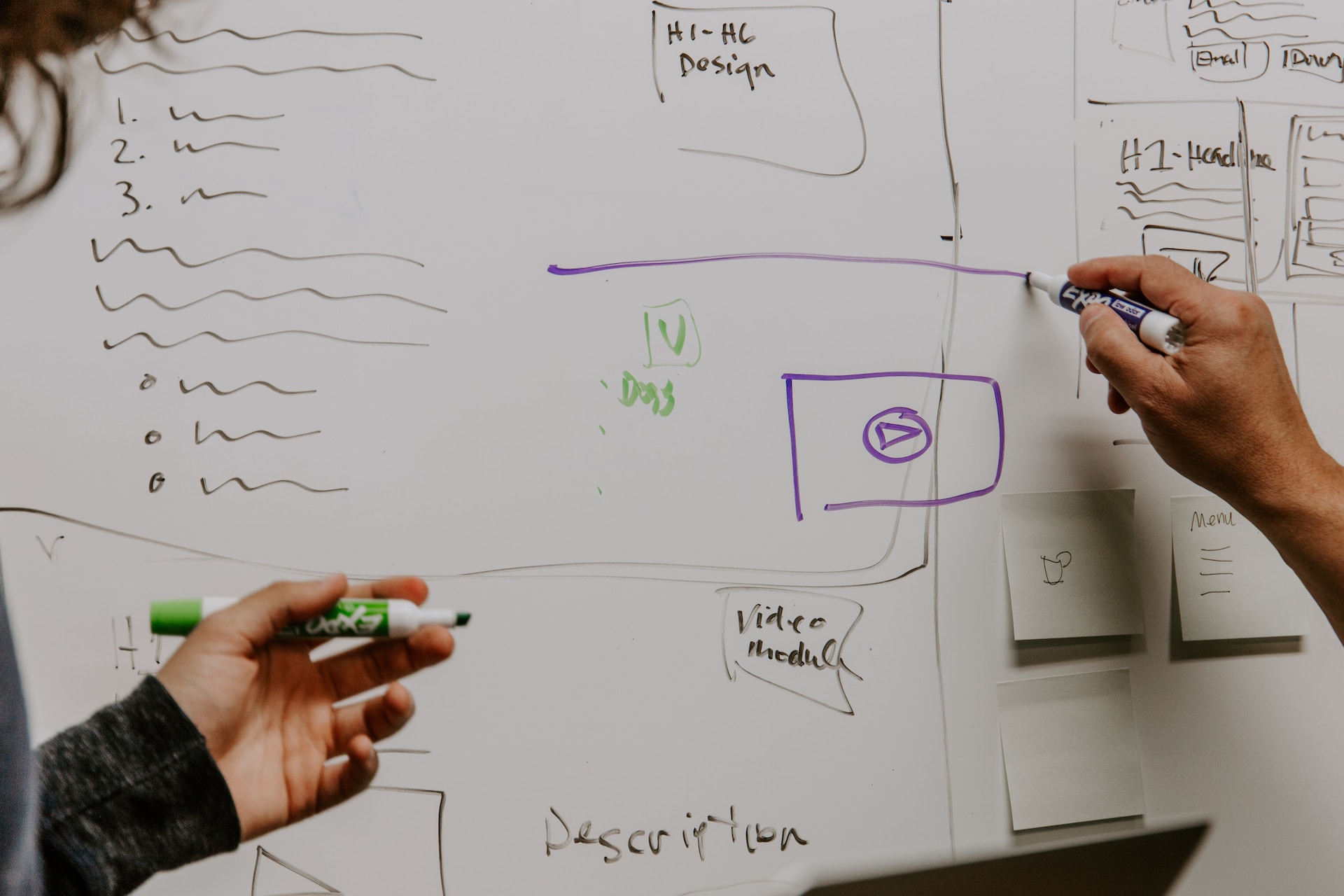