Article
Understanding Lean Manufacturing Principles
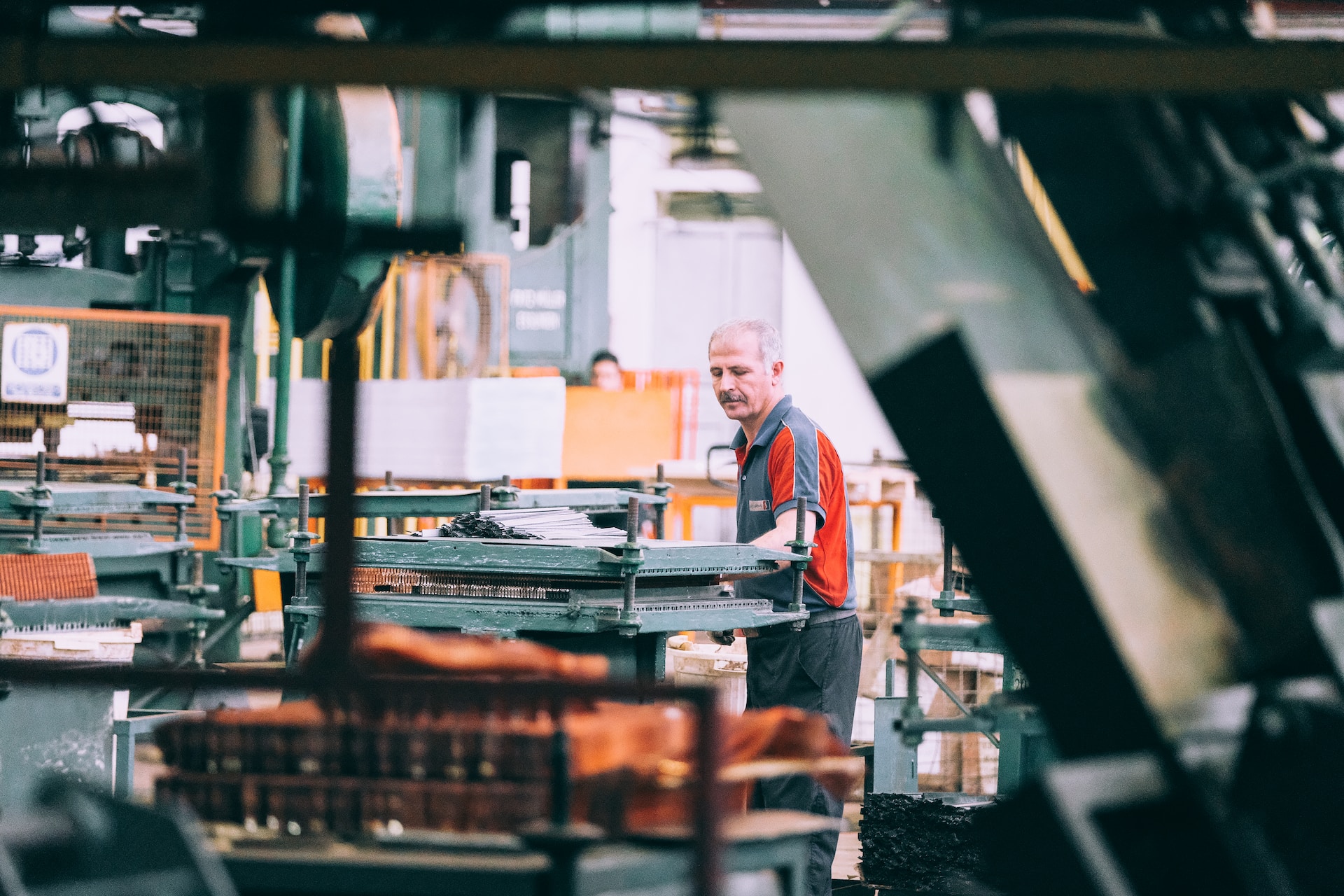
Lean manufacturing is a systematic approach that aims to eliminate waste and improve efficiency in the production process. By focusing on creating value from the customer's perspective, identifying and eliminating waste, and continuously improving processes, lean manufacturing can help organizations streamline their operations and achieve greater profitability.
Introduction to Lean Manufacturing
In this section, we will provide an overview of lean manufacturing, its origins, and its key concepts. Lean manufacturing, also known as lean production or just lean, was first developed by Toyota in Japan in the 1940s. It was inspired by the principles of the Toyota Production System (TPS), which emphasized the elimination of waste to create value for the customer.
Lean manufacturing revolutionized the way companies approach production by focusing on efficiency and waste reduction. By implementing lean principles, companies can streamline their processes, improve customer satisfaction, and increase profitability.
The Origins of Lean Manufacturing
The origins of lean manufacturing can be traced back to the post-World War II era in Japan. At the time, resources were scarce, and Toyota faced significant challenges in meeting the growing demand for automobiles. To address these challenges, Toyota's founder, Sakichi Toyoda, and his son, Kiichiro Toyoda, developed the concept of lean manufacturing as a way to streamline production and reduce waste.
Toyota's journey towards lean manufacturing was driven by the need to optimize resource utilization and improve productivity. They recognized that traditional mass production methods were inefficient and led to excessive inventory levels, long lead times, and high costs. By focusing on eliminating waste and improving efficiency, Toyota was able to overcome the limitations of scarce resources and become a global leader in the automotive industry.
One of the key figures in the development of lean manufacturing was Taiichi Ohno, an engineer at Toyota. Ohno is often credited as the father of the Toyota Production System and played a crucial role in implementing lean principles on the shop floor. He introduced concepts such as Just-in-Time (JIT) production, where materials are delivered to the production line exactly when they are needed, and the Kanban system, which visualizes the flow of materials and triggers production based on actual demand.
Key Concepts of Lean Manufacturing
There are several key concepts associated with lean manufacturing:
- Value: Understanding what is valuable from the customer's perspective and focusing on delivering that value. In lean manufacturing, value is defined as any action or process that the customer is willing to pay for. By identifying and eliminating non-value-added activities, companies can optimize their processes and improve customer satisfaction.
- Value Stream: Mapping the entire value stream, from raw materials to the end customer, and identifying areas of waste. A value stream map provides a visual representation of the flow of materials and information through the production process. It helps identify bottlenecks, inefficiencies, and opportunities for improvement.
- Flow: Creating a seamless flow of value-adding steps in the production process, reducing time and waste. In a lean manufacturing environment, the goal is to eliminate any interruptions or delays in the flow of work. This can be achieved through various techniques such as cellular manufacturing, where workstations are arranged in a way that minimizes movement and transportation.
- Pull: Establishing a pull-based system where products are produced in response to customer demand, reducing inventory and waste. Instead of producing goods based on forecasts or pushing products through the production process, lean manufacturing relies on a pull system. This means that production is triggered by actual customer orders, ensuring that products are made only when there is demand.
- Continuous Improvement: Continuously seeking ways to improve processes and eliminate waste. Lean manufacturing is not a one-time implementation; it is a mindset of continuous improvement. Companies are encouraged to involve employees at all levels in identifying and implementing improvements. This can be done through techniques such as Kaizen, which focuses on small, incremental changes that add up to significant improvements over time.
By embracing these key concepts, companies can transform their operations and achieve higher levels of efficiency, quality, and customer satisfaction. Lean manufacturing is not limited to the automotive industry; it has been successfully applied in various sectors, including healthcare, aerospace, and service industries.
The Five Principles of Lean Manufacturing
The five principles of lean manufacturing provide a framework for organizations to implement lean practices in their operations. These principles are:
Define Value from the Customer's Perspective
The first principle of lean manufacturing is to understand what customers value and focus on delivering that value. This requires organizations to have a deep understanding of their customers' needs, preferences, and expectations. By aligning all activities with the customer's perspective, organizations can eliminate waste and create value in every step of the production process.
For example, a company that manufactures smartphones may conduct extensive market research to understand the features and qualities that customers value the most. They may analyze customer feedback, conduct surveys, and study market trends to identify the key factors that drive customer satisfaction. Armed with this knowledge, the company can then design and produce smartphones that meet or exceed customer expectations, ensuring a high level of value is delivered.
Identify the Value Stream and Eliminate Waste
The second principle of lean manufacturing is to map the entire value stream and identify areas of waste. Waste can take many forms, including overproduction, defects, waiting time, and excess inventory. By eliminating waste, organizations can streamline their processes, reduce costs, and improve efficiency.
Let's consider a manufacturing plant that produces automobiles. To identify waste in their value stream, the company may conduct a thorough analysis of their production line. They may observe the flow of materials, the efficiency of each workstation, and the time it takes to complete each step. By doing so, they can identify areas where waste is occurring, such as excessive waiting time between workstations or unnecessary movement of materials. Once identified, the company can implement strategies to eliminate or minimize these wastes, such as redesigning the layout of the production line or implementing just-in-time inventory management systems.
Create Flow to Make the Value-Adding Steps Run Smoothly
The third principle of lean manufacturing is to create a seamless flow of value-adding steps in the production process. This requires eliminating bottlenecks, reducing process cycle times, and ensuring a smooth flow of materials and information. By optimizing the flow, organizations can minimize delays, reduce inventory, and improve overall efficiency.
Continuing with the example of the automobile manufacturing plant, the company may implement various strategies to create a smooth flow. They may redesign the layout of the production line to minimize the distance traveled by workers and materials. They may also implement standardized work procedures to ensure consistency and efficiency in each step. Additionally, the company may invest in automation and technology to streamline processes and reduce human error. By creating a flow that eliminates interruptions and maximizes efficiency, the company can improve productivity and reduce costs.
Establish Pull Based on Customer Demand
The fourth principle of lean manufacturing is to establish a pull-based system where products are produced in response to customer demand. This requires organizations to have a flexible production system that can quickly respond to changes in customer demand. By reducing inventory and producing only what is needed, organizations can minimize waste and improve responsiveness.
Imagine a clothing retailer that operates based on a pull-based system. Instead of producing clothes in large quantities based on forecasts, the retailer produces garments only when customers place orders. By doing so, they can avoid overproduction and the accumulation of excess inventory. This not only reduces waste but also allows the retailer to respond quickly to changing fashion trends and customer preferences. The pull-based system ensures that the retailer is producing what customers want, when they want it, resulting in higher customer satisfaction and reduced costs.
Seek Continuous Improvement
The fifth principle of lean manufacturing is to continuously seek ways to improve processes and eliminate waste. This requires organizations to foster a culture of continuous learning and improvement. By encouraging employees to identify and solve problems, organizations can achieve ongoing improvements in efficiency, quality, and customer satisfaction.
For instance, a software development company may adopt an agile approach to continuously improve their development processes. They may hold regular retrospective meetings where team members reflect on their work, identify areas for improvement, and implement changes to enhance productivity and quality. By fostering a culture of continuous improvement, the company can stay ahead of the competition, adapt to changing market conditions, and deliver high-quality software products that meet customer needs.
Benefits of Implementing Lean Manufacturing
Implementing lean manufacturing principles can provide organizations with several benefits:
Increased Productivity and Efficiency
By eliminating waste and streamlining processes, lean manufacturing can significantly enhance productivity and efficiency. This allows organizations to produce more with fewer resources, reducing costs and improving profitability.
Improved Quality and Customer Satisfaction
Lean manufacturing places a strong emphasis on quality, as defects and errors are considered a form of waste. By implementing rigorous quality control measures and focusing on continuous improvement, organizations can deliver products that meet or exceed customer expectations, leading to higher levels of customer satisfaction.
Reduced Costs and Waste
One of the primary goals of lean manufacturing is to eliminate waste in all its forms. By identifying and eliminating non-value-added activities, organizations can reduce costs, reduce lead times, and improve overall efficiency. This can result in significant cost savings and increased profitability.
Challenges in Implementing Lean Manufacturing
While the benefits of lean manufacturing are compelling, implementing lean practices can also pose several challenges:
Resistance to Change
Implementing lean manufacturing requires a fundamental shift in mindset and practices. Resistance to change is a common challenge, as employees may be accustomed to traditional ways of working and may be resistant to new approaches. Overcoming resistance to change requires effective communication, training, and leadership support.
Need for Continuous Training and Development
Lean manufacturing requires a skilled workforce that is capable of identifying and solving problems, improving processes, and driving continuous improvement. Organizations need to invest in training and development programs that help employees acquire the necessary knowledge and skills to implement lean practices successfully.
Balancing Lean and Flexibility
While lean manufacturing can improve efficiency and reduce waste, it can also make organizations less flexible and more vulnerable to disruptions. Achieving a balance between lean practices and the need for flexibility is a challenge that organizations need to address. This may involve adopting agile manufacturing techniques and developing strategies to manage variability and uncertainty.
In conclusion, understanding lean manufacturing principles is essential for organizations looking to optimize their operations and achieve greater efficiency and profitability. By embracing the concepts of value, waste elimination, flow, pull, and continuous improvement, organizations can transform their production processes and deliver superior value to their customers.
Similar Blog Posts
Article
Understanding Lean Manufacturing Principles
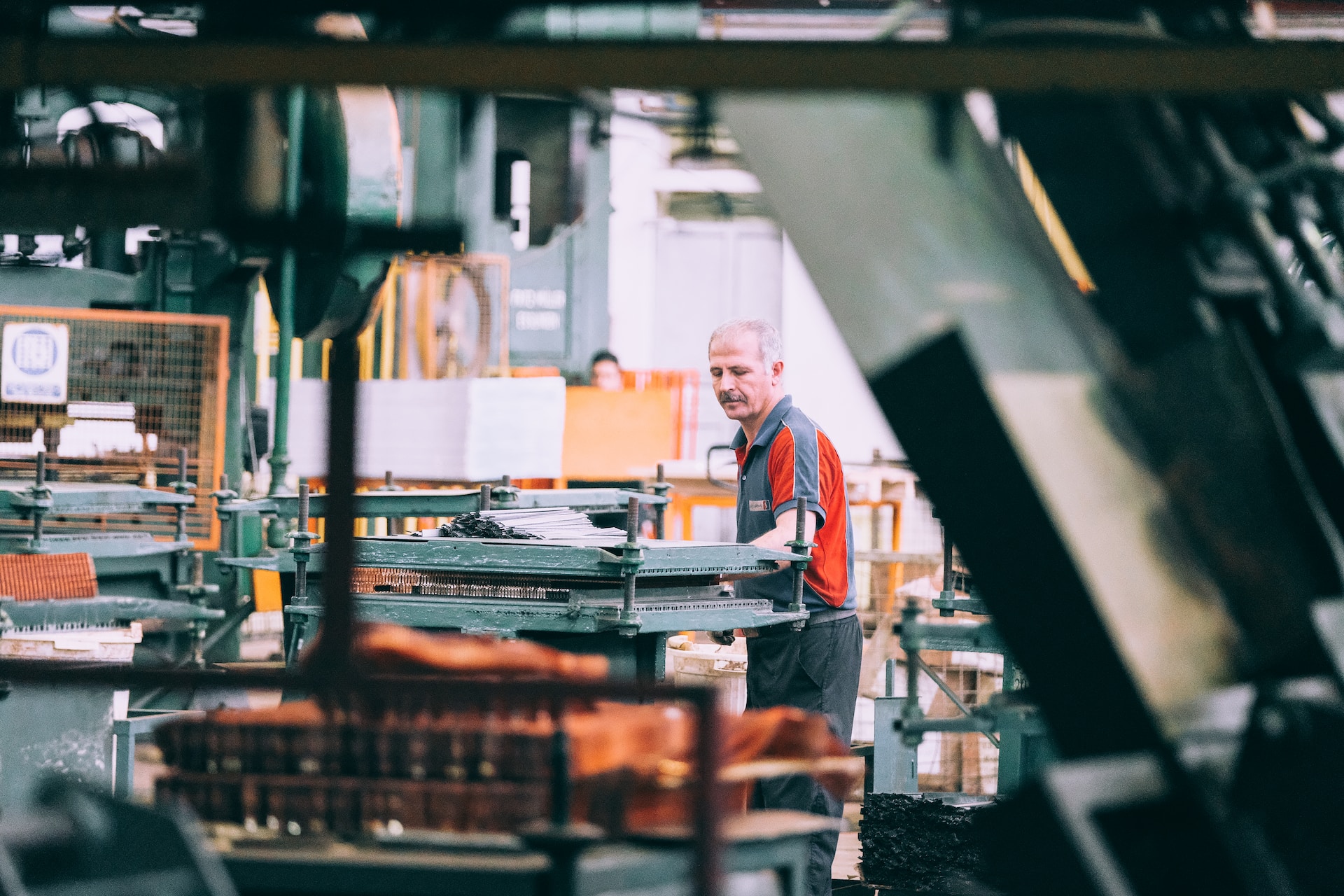
Lean manufacturing is a systematic approach that aims to eliminate waste and improve efficiency in the production process. By focusing on creating value from the customer's perspective, identifying and eliminating waste, and continuously improving processes, lean manufacturing can help organizations streamline their operations and achieve greater profitability.
Introduction to Lean Manufacturing
In this section, we will provide an overview of lean manufacturing, its origins, and its key concepts. Lean manufacturing, also known as lean production or just lean, was first developed by Toyota in Japan in the 1940s. It was inspired by the principles of the Toyota Production System (TPS), which emphasized the elimination of waste to create value for the customer.
Lean manufacturing revolutionized the way companies approach production by focusing on efficiency and waste reduction. By implementing lean principles, companies can streamline their processes, improve customer satisfaction, and increase profitability.
The Origins of Lean Manufacturing
The origins of lean manufacturing can be traced back to the post-World War II era in Japan. At the time, resources were scarce, and Toyota faced significant challenges in meeting the growing demand for automobiles. To address these challenges, Toyota's founder, Sakichi Toyoda, and his son, Kiichiro Toyoda, developed the concept of lean manufacturing as a way to streamline production and reduce waste.
Toyota's journey towards lean manufacturing was driven by the need to optimize resource utilization and improve productivity. They recognized that traditional mass production methods were inefficient and led to excessive inventory levels, long lead times, and high costs. By focusing on eliminating waste and improving efficiency, Toyota was able to overcome the limitations of scarce resources and become a global leader in the automotive industry.
One of the key figures in the development of lean manufacturing was Taiichi Ohno, an engineer at Toyota. Ohno is often credited as the father of the Toyota Production System and played a crucial role in implementing lean principles on the shop floor. He introduced concepts such as Just-in-Time (JIT) production, where materials are delivered to the production line exactly when they are needed, and the Kanban system, which visualizes the flow of materials and triggers production based on actual demand.
Key Concepts of Lean Manufacturing
There are several key concepts associated with lean manufacturing:
- Value: Understanding what is valuable from the customer's perspective and focusing on delivering that value. In lean manufacturing, value is defined as any action or process that the customer is willing to pay for. By identifying and eliminating non-value-added activities, companies can optimize their processes and improve customer satisfaction.
- Value Stream: Mapping the entire value stream, from raw materials to the end customer, and identifying areas of waste. A value stream map provides a visual representation of the flow of materials and information through the production process. It helps identify bottlenecks, inefficiencies, and opportunities for improvement.
- Flow: Creating a seamless flow of value-adding steps in the production process, reducing time and waste. In a lean manufacturing environment, the goal is to eliminate any interruptions or delays in the flow of work. This can be achieved through various techniques such as cellular manufacturing, where workstations are arranged in a way that minimizes movement and transportation.
- Pull: Establishing a pull-based system where products are produced in response to customer demand, reducing inventory and waste. Instead of producing goods based on forecasts or pushing products through the production process, lean manufacturing relies on a pull system. This means that production is triggered by actual customer orders, ensuring that products are made only when there is demand.
- Continuous Improvement: Continuously seeking ways to improve processes and eliminate waste. Lean manufacturing is not a one-time implementation; it is a mindset of continuous improvement. Companies are encouraged to involve employees at all levels in identifying and implementing improvements. This can be done through techniques such as Kaizen, which focuses on small, incremental changes that add up to significant improvements over time.
By embracing these key concepts, companies can transform their operations and achieve higher levels of efficiency, quality, and customer satisfaction. Lean manufacturing is not limited to the automotive industry; it has been successfully applied in various sectors, including healthcare, aerospace, and service industries.
The Five Principles of Lean Manufacturing
The five principles of lean manufacturing provide a framework for organizations to implement lean practices in their operations. These principles are:
Define Value from the Customer's Perspective
The first principle of lean manufacturing is to understand what customers value and focus on delivering that value. This requires organizations to have a deep understanding of their customers' needs, preferences, and expectations. By aligning all activities with the customer's perspective, organizations can eliminate waste and create value in every step of the production process.
For example, a company that manufactures smartphones may conduct extensive market research to understand the features and qualities that customers value the most. They may analyze customer feedback, conduct surveys, and study market trends to identify the key factors that drive customer satisfaction. Armed with this knowledge, the company can then design and produce smartphones that meet or exceed customer expectations, ensuring a high level of value is delivered.
Identify the Value Stream and Eliminate Waste
The second principle of lean manufacturing is to map the entire value stream and identify areas of waste. Waste can take many forms, including overproduction, defects, waiting time, and excess inventory. By eliminating waste, organizations can streamline their processes, reduce costs, and improve efficiency.
Let's consider a manufacturing plant that produces automobiles. To identify waste in their value stream, the company may conduct a thorough analysis of their production line. They may observe the flow of materials, the efficiency of each workstation, and the time it takes to complete each step. By doing so, they can identify areas where waste is occurring, such as excessive waiting time between workstations or unnecessary movement of materials. Once identified, the company can implement strategies to eliminate or minimize these wastes, such as redesigning the layout of the production line or implementing just-in-time inventory management systems.
Create Flow to Make the Value-Adding Steps Run Smoothly
The third principle of lean manufacturing is to create a seamless flow of value-adding steps in the production process. This requires eliminating bottlenecks, reducing process cycle times, and ensuring a smooth flow of materials and information. By optimizing the flow, organizations can minimize delays, reduce inventory, and improve overall efficiency.
Continuing with the example of the automobile manufacturing plant, the company may implement various strategies to create a smooth flow. They may redesign the layout of the production line to minimize the distance traveled by workers and materials. They may also implement standardized work procedures to ensure consistency and efficiency in each step. Additionally, the company may invest in automation and technology to streamline processes and reduce human error. By creating a flow that eliminates interruptions and maximizes efficiency, the company can improve productivity and reduce costs.
Establish Pull Based on Customer Demand
The fourth principle of lean manufacturing is to establish a pull-based system where products are produced in response to customer demand. This requires organizations to have a flexible production system that can quickly respond to changes in customer demand. By reducing inventory and producing only what is needed, organizations can minimize waste and improve responsiveness.
Imagine a clothing retailer that operates based on a pull-based system. Instead of producing clothes in large quantities based on forecasts, the retailer produces garments only when customers place orders. By doing so, they can avoid overproduction and the accumulation of excess inventory. This not only reduces waste but also allows the retailer to respond quickly to changing fashion trends and customer preferences. The pull-based system ensures that the retailer is producing what customers want, when they want it, resulting in higher customer satisfaction and reduced costs.
Seek Continuous Improvement
The fifth principle of lean manufacturing is to continuously seek ways to improve processes and eliminate waste. This requires organizations to foster a culture of continuous learning and improvement. By encouraging employees to identify and solve problems, organizations can achieve ongoing improvements in efficiency, quality, and customer satisfaction.
For instance, a software development company may adopt an agile approach to continuously improve their development processes. They may hold regular retrospective meetings where team members reflect on their work, identify areas for improvement, and implement changes to enhance productivity and quality. By fostering a culture of continuous improvement, the company can stay ahead of the competition, adapt to changing market conditions, and deliver high-quality software products that meet customer needs.
Benefits of Implementing Lean Manufacturing
Implementing lean manufacturing principles can provide organizations with several benefits:
Increased Productivity and Efficiency
By eliminating waste and streamlining processes, lean manufacturing can significantly enhance productivity and efficiency. This allows organizations to produce more with fewer resources, reducing costs and improving profitability.
Improved Quality and Customer Satisfaction
Lean manufacturing places a strong emphasis on quality, as defects and errors are considered a form of waste. By implementing rigorous quality control measures and focusing on continuous improvement, organizations can deliver products that meet or exceed customer expectations, leading to higher levels of customer satisfaction.
Reduced Costs and Waste
One of the primary goals of lean manufacturing is to eliminate waste in all its forms. By identifying and eliminating non-value-added activities, organizations can reduce costs, reduce lead times, and improve overall efficiency. This can result in significant cost savings and increased profitability.
Challenges in Implementing Lean Manufacturing
While the benefits of lean manufacturing are compelling, implementing lean practices can also pose several challenges:
Resistance to Change
Implementing lean manufacturing requires a fundamental shift in mindset and practices. Resistance to change is a common challenge, as employees may be accustomed to traditional ways of working and may be resistant to new approaches. Overcoming resistance to change requires effective communication, training, and leadership support.
Need for Continuous Training and Development
Lean manufacturing requires a skilled workforce that is capable of identifying and solving problems, improving processes, and driving continuous improvement. Organizations need to invest in training and development programs that help employees acquire the necessary knowledge and skills to implement lean practices successfully.
Balancing Lean and Flexibility
While lean manufacturing can improve efficiency and reduce waste, it can also make organizations less flexible and more vulnerable to disruptions. Achieving a balance between lean practices and the need for flexibility is a challenge that organizations need to address. This may involve adopting agile manufacturing techniques and developing strategies to manage variability and uncertainty.
In conclusion, understanding lean manufacturing principles is essential for organizations looking to optimize their operations and achieve greater efficiency and profitability. By embracing the concepts of value, waste elimination, flow, pull, and continuous improvement, organizations can transform their production processes and deliver superior value to their customers.
Article
Understanding Lean Manufacturing Principles
•
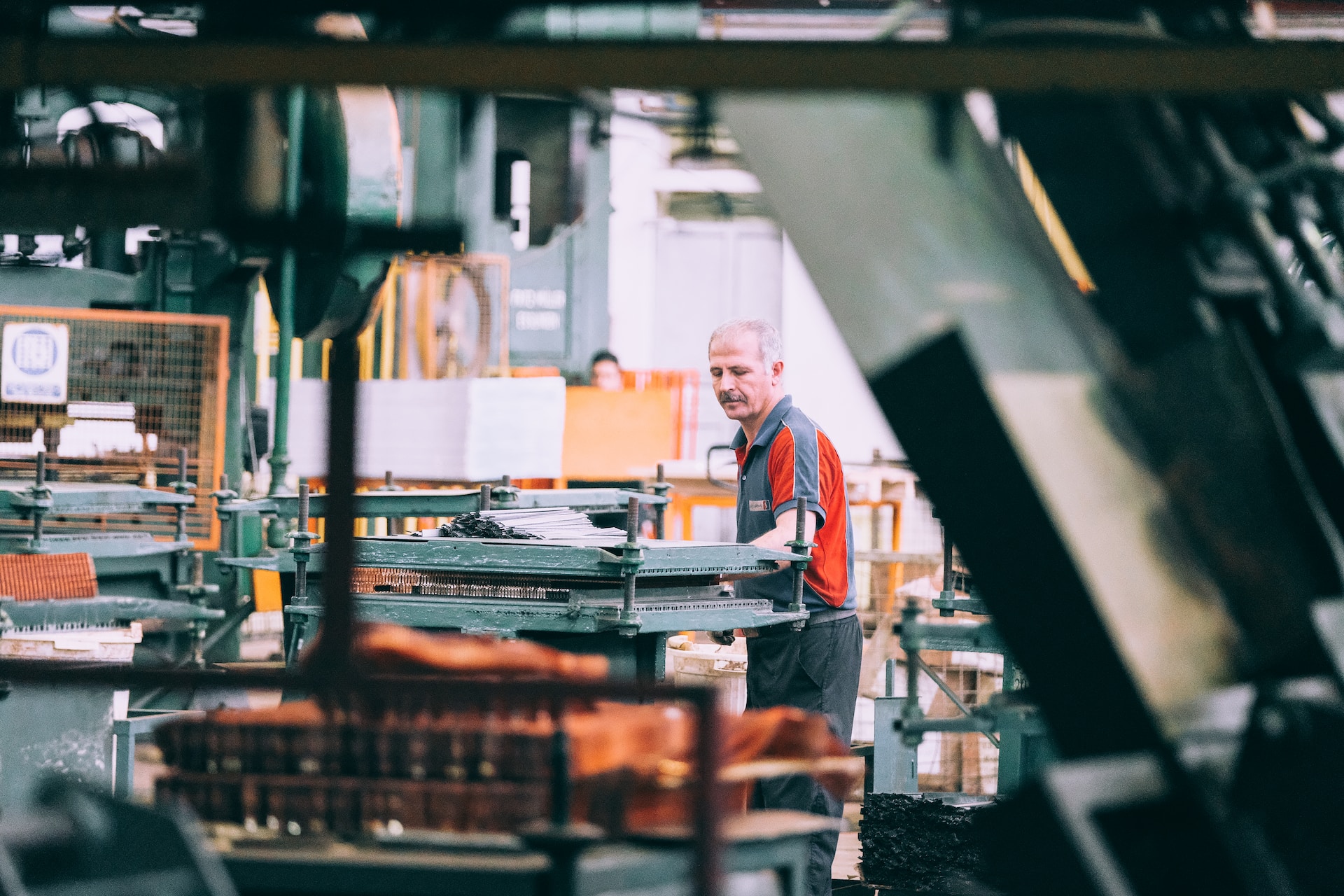