Article
7 Steps to Implementing Effective Process Improvement
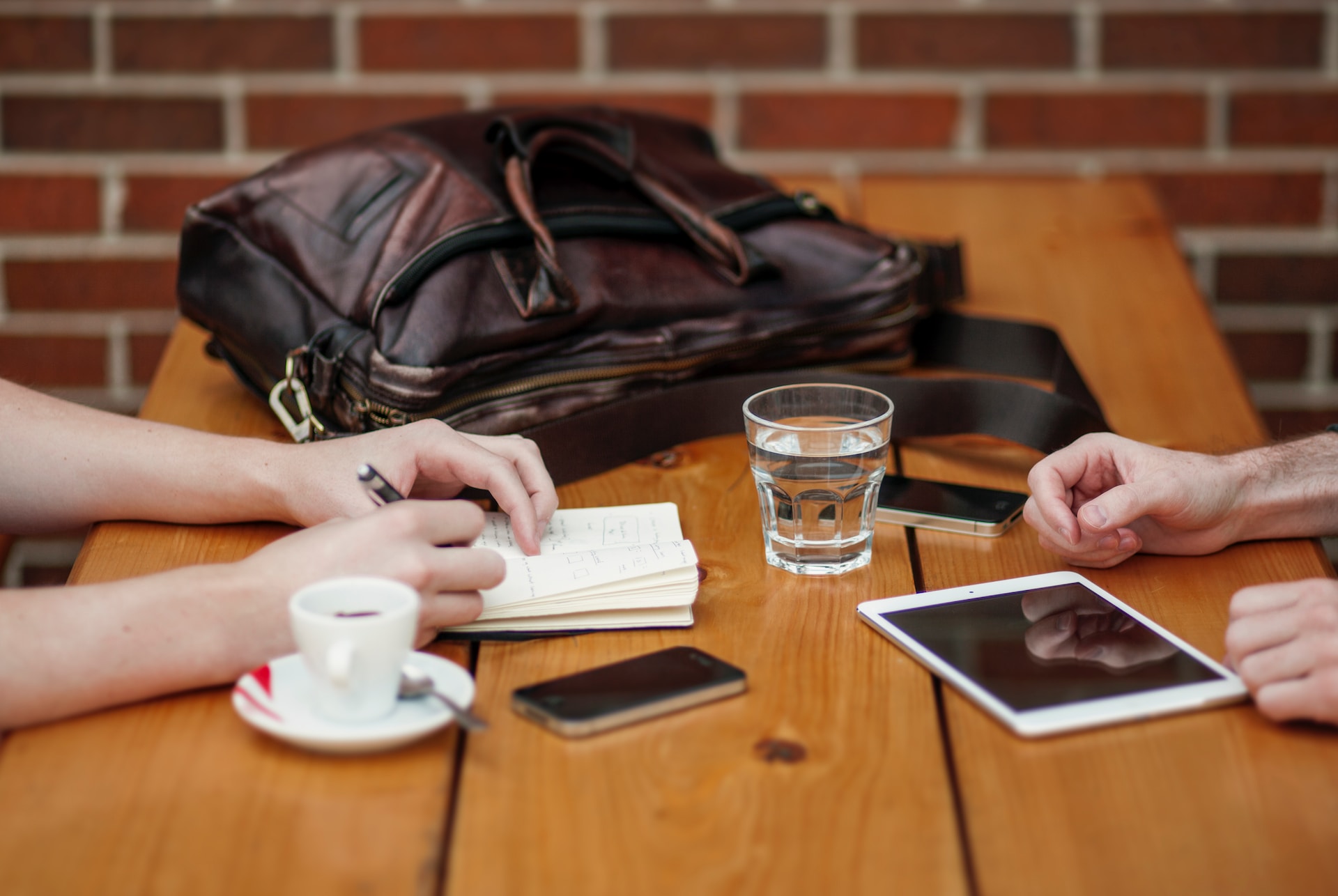
As businesses strive to remain competitive in today's fast-paced market, the need for process improvement has become crucial. To stay relevant, companies must continuously evaluate and improve their processes to optimize effectiveness and efficiency. This article outlines seven steps for implementing effective process improvement and the benefits it can provide.
Understanding Process Improvement
What is Process Improvement?
Process improvement is the systematic approach of analyzing a company's current processes, identifying areas of inefficiency, and implementing effective solutions to optimize these processes. It involves a continuous cycle of evaluation and improvement geared towards achieving the best possible outcomes. This approach focuses on improving effectiveness, efficiency, and customer satisfaction.
Process improvement is a critical component of any successful business. It helps organizations to identify areas where they can improve their operations and deliver better results to their customers. By analyzing their processes and making necessary changes, companies can achieve significant improvements in their bottom line.
One of the key benefits of process improvement is that it helps organizations to reduce costs and waste. By identifying areas of inefficiency and implementing effective solutions, companies can reduce their operating costs and increase their profitability. This, in turn, allows them to invest in other areas of their business and stay ahead of their competition.
Benefits of Process Improvement
The benefits of process improvement are numerous, ranging from improving operational efficiency to delivering better customer experiences. Other benefits include:
- Reducing costs and waste.
- Increasing productivity and output.
- Streamlining operations and reducing errors.
- Improving employee engagement and satisfaction.
- Enhancing the quality of goods and services.
These benefits provide a competitive advantage and make companies better equipped to meet the ever-evolving demands of their customers. By improving their processes, companies can deliver better products and services, increase customer satisfaction, and build stronger relationships with their customers.
Another key benefit of process improvement is that it helps organizations to increase their productivity and output. By streamlining their operations and reducing errors, companies can produce more goods and services in less time, which allows them to meet the growing demands of their customers. This, in turn, helps them to stay ahead of their competition and maintain their market position.
Process improvement also plays a critical role in improving employee engagement and satisfaction. By involving employees in the process improvement, companies can create a culture of continuous improvement and innovation. This, in turn, helps to boost employee morale and job satisfaction, which leads to higher levels of productivity and better results for the company.
In conclusion, process improvement is a critical component of any successful business. By analyzing their processes and making necessary changes, companies can achieve significant improvements in their bottom line. The benefits of process improvement are numerous, ranging from reducing costs and waste to increasing productivity and output. By improving their processes, companies can deliver better products and services, increase customer satisfaction, and build stronger relationships with their customers.
Identifying Areas for Improvement
Identifying areas for improvement is a crucial step towards achieving organizational success. By analyzing current processes, businesses can identify inefficiencies and develop strategies to improve them. This not only enhances the quality of the products or services offered but also improves customer satisfaction. In this article, we will discuss the two critical steps in identifying areas for improvement.
Analyzing Current Processes
The first step in process improvement is to analyze the current processes. This involves closely examining each step of the process, starting from the initiation to the final stage. The objective is to identify bottlenecks, redundancies, delays, and other inefficiencies that negatively affect the process. By doing so, businesses can develop a clear understanding of the process and its shortcomings.
For instance, a manufacturing company may identify that the production process takes longer than expected due to a bottleneck in the assembly line. By analyzing the process, the company can identify the root cause of the bottleneck and develop strategies to eliminate it. This may involve reorganizing the assembly line, investing in new equipment, or hiring additional staff.
The analysis of current processes is a critical step towards process improvement. It provides businesses with a clear understanding of the process and its shortcomings, allowing them to develop effective strategies to improve it.
Gathering Feedback from Stakeholders
Gathering feedback from stakeholders is another critical step in identifying areas for improvement. Stakeholders are individuals or groups who have a vested interest in the process, such as staff, customers, and vendors. They have first-hand experience with the process and can provide valuable insights into its strengths and weaknesses.
For instance, customers can provide feedback on the quality of the products or services offered, the level of customer service, and the overall experience. Staff members can provide feedback on the efficiency of the process, the level of training provided, and the resources available. Vendors can provide feedback on the quality of the materials or services provided and the level of communication.
Gathering feedback from stakeholders is essential as it provides businesses with valuable insights into the process. This feedback can be used to identify areas of improvement and develop strategies to address them. It also demonstrates a commitment to continuous improvement, which can enhance customer satisfaction and increase brand loyalty.
In conclusion, identifying areas for improvement is a critical step towards achieving organizational success. By analyzing current processes and gathering feedback from stakeholders, businesses can identify inefficiencies and develop strategies to improve them. This leads to enhanced product or service quality, increased customer satisfaction, and improved brand loyalty.
Setting Goals and Objectives
Setting goals and objectives is an essential part of any successful process improvement initiative. Goals provide a sense of direction and purpose, and objectives help define the specific actions necessary to achieve those goals.
Defining SMART Goals
When setting goals, it's important to make them SMART: Specific, Measurable, Achievable, Relevant, and Time-bound. Specific goals clearly define what needs to be accomplished, while measurable goals provide a way to track progress. Achievable goals are realistic and within reach, while relevant goals align with the overall purpose of the initiative. Time-bound goals have a specific deadline for completion, creating a sense of urgency and accountability.
By setting SMART goals, you can ensure that the objectives are attainable and measurable, and can be achieved effectively and efficiently.
Aligning Goals with Business Strategy
While setting SMART goals is important, it's also crucial to align those goals with the overall business strategy. This alignment ensures that the process improvement initiatives support the business strategy, increase efficiency, and sustain long-term objectives.
For example, if the business strategy is to increase customer satisfaction, the process improvement initiative should focus on improving customer service processes. By aligning the goals with the business strategy, the initiative is more likely to have a positive impact on the overall success of the organization.
Overall, setting SMART goals and aligning them with the business strategy is a critical step in any process improvement initiative. By doing so, you can ensure that the initiative is focused, effective, and contributes to the long-term success of the organization.
Developing a Process Improvement Plan
Process improvement is a crucial aspect of any business or organization. It helps to streamline operations, eliminate waste, and increase efficiency. Developing a process improvement plan is essential to ensure that the organization is continuously improving and adapting to the changing business environment. In this article, we will discuss the key steps involved in developing a process improvement plan.
Prioritizing Improvement Initiatives
Before embarking on any process improvement initiative, it is vital to prioritize the initiatives based on their impact and importance. This involves identifying the critical areas that require improvement and evaluating the potential impact of each initiative. Prioritization is necessary because resources are limited, and improvements generate the most significant impact to obtain the best results.
For example, if an organization is experiencing significant delays in its supply chain, it may prioritize initiatives that address this issue before focusing on other areas of the business.
Assigning Roles and Responsibilities
Roles and responsibilities must be assigned to ensure the process improvement initiatives are effectively managed. This includes identifying the team responsible for spearheading the improvement initiative. Defining roles, responsibilities, accountabilities, and timelines ensures that everyone understands what is expected and who is responsible for driving the process forward.
For instance, if an organization is implementing a new software system to improve its accounting processes, it may assign a project manager to oversee the initiative, a team of accountants to test and implement the software, and an IT team to provide technical support.
Identifying Improvement Opportunities
Identifying improvement opportunities is the next step in developing a process improvement plan. This involves analyzing the current processes and identifying areas where improvements can be made. Improvement opportunities may be identified through a variety of methods, such as process mapping, data analysis, and customer feedback.
For example, an organization may conduct a customer survey to identify areas where customers are dissatisfied with the service. Based on the survey results, the organization may identify opportunities to improve its customer service processes.
Developing Improvement Strategies
Once improvement opportunities have been identified, the next step is to develop improvement strategies. Improvement strategies should be designed to address the identified opportunities and align with the organization's overall goals and objectives.
For example, if an organization identifies an opportunity to improve its manufacturing processes, it may develop a strategy to implement lean manufacturing principles. The strategy may involve training employees on lean principles, redesigning the manufacturing process, and implementing new technology to support the new process.
Implementing and Monitoring Improvement Initiatives
The final step in developing a process improvement plan is to implement and monitor improvement initiatives. Implementation involves putting the improvement strategies into action, while monitoring involves tracking progress and making adjustments as necessary.
For example, if an organization implements a new software system to improve its accounting processes, it may monitor the system's performance to ensure that it is achieving the desired results. If the system is not performing as expected, the organization may make adjustments to the system or the processes to improve its performance.
In conclusion, developing a process improvement plan is essential for any organization that wants to remain competitive and adapt to the changing business environment. By prioritizing improvement initiatives, assigning roles and responsibilities, identifying improvement opportunities, developing improvement strategies, and implementing and monitoring improvement initiatives, organizations can continuously improve their processes and achieve their goals.
Implementing the Process Improvement Plan
Communicating the Plan to Stakeholders
It is essential to communicate the process improvement plan to all stakeholders, including staff, customers, and vendors. An effective communication plan includes outlining the changes, their benefits, and timings to reduce resistance and increase buy-in to the new process.
Providing Training and Support
The final step is to provide the necessary training and support to staff to perform their new roles. Training ensures that staff members understand how to implement the new process successfully and efficiently. Support ensures that the team is available to provide guidance and address any issues encountered during the implementation phase.
Conclusion
Process improvement is crucial for businesses looking to streamline their operations and grow in today's competitive environment. Implementing the seven-step process outlined in this article can help drive efficiency, improve customer experiences, and provide long-term benefits for organizations. Whether you're enhancing existing processes or creating new ones, effective process improvement requires a commitment to evaluating and continuously improving.
Article
7 Steps to Implementing Effective Process Improvement
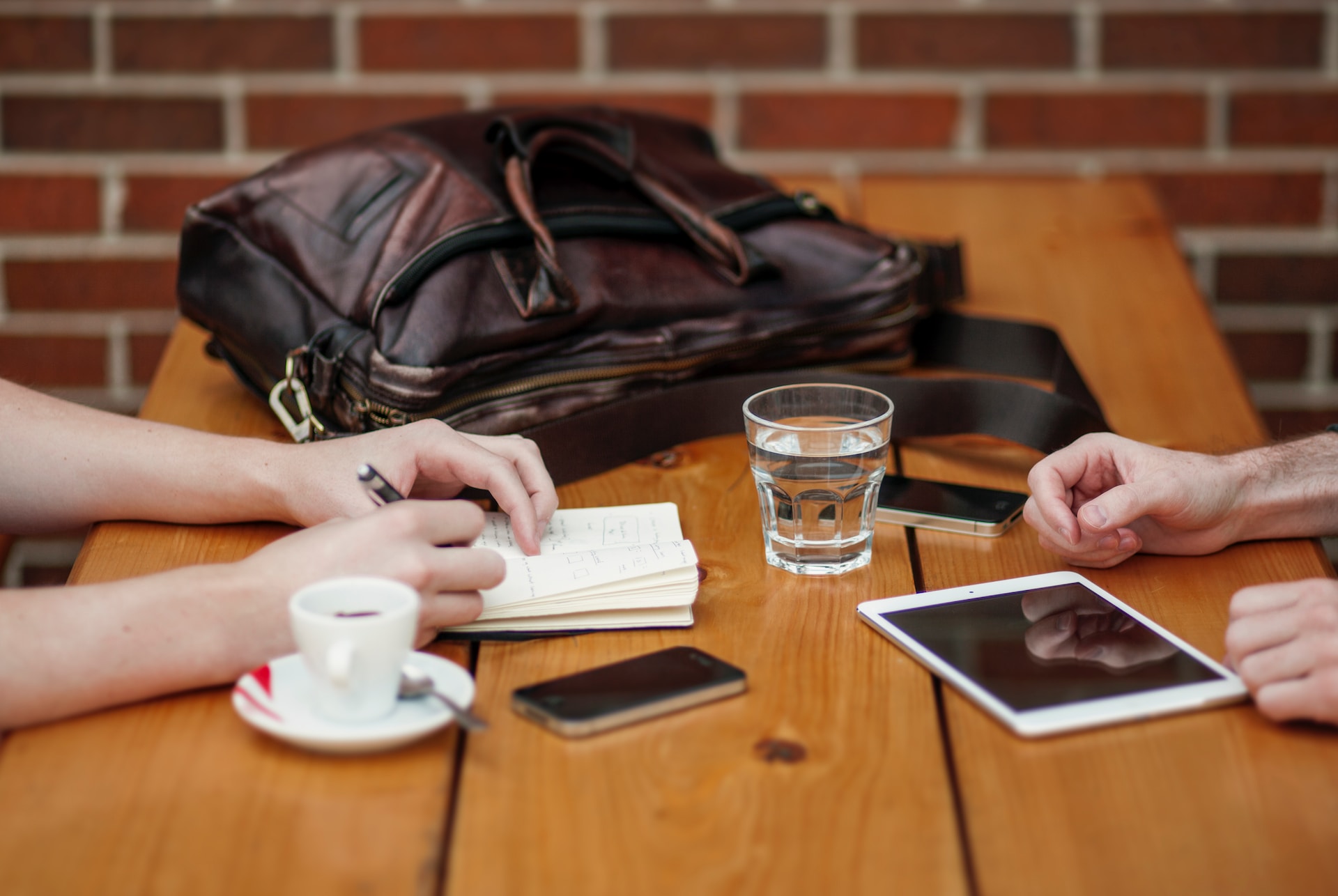
As businesses strive to remain competitive in today's fast-paced market, the need for process improvement has become crucial. To stay relevant, companies must continuously evaluate and improve their processes to optimize effectiveness and efficiency. This article outlines seven steps for implementing effective process improvement and the benefits it can provide.
Understanding Process Improvement
What is Process Improvement?
Process improvement is the systematic approach of analyzing a company's current processes, identifying areas of inefficiency, and implementing effective solutions to optimize these processes. It involves a continuous cycle of evaluation and improvement geared towards achieving the best possible outcomes. This approach focuses on improving effectiveness, efficiency, and customer satisfaction.
Process improvement is a critical component of any successful business. It helps organizations to identify areas where they can improve their operations and deliver better results to their customers. By analyzing their processes and making necessary changes, companies can achieve significant improvements in their bottom line.
One of the key benefits of process improvement is that it helps organizations to reduce costs and waste. By identifying areas of inefficiency and implementing effective solutions, companies can reduce their operating costs and increase their profitability. This, in turn, allows them to invest in other areas of their business and stay ahead of their competition.
Benefits of Process Improvement
The benefits of process improvement are numerous, ranging from improving operational efficiency to delivering better customer experiences. Other benefits include:
- Reducing costs and waste.
- Increasing productivity and output.
- Streamlining operations and reducing errors.
- Improving employee engagement and satisfaction.
- Enhancing the quality of goods and services.
These benefits provide a competitive advantage and make companies better equipped to meet the ever-evolving demands of their customers. By improving their processes, companies can deliver better products and services, increase customer satisfaction, and build stronger relationships with their customers.
Another key benefit of process improvement is that it helps organizations to increase their productivity and output. By streamlining their operations and reducing errors, companies can produce more goods and services in less time, which allows them to meet the growing demands of their customers. This, in turn, helps them to stay ahead of their competition and maintain their market position.
Process improvement also plays a critical role in improving employee engagement and satisfaction. By involving employees in the process improvement, companies can create a culture of continuous improvement and innovation. This, in turn, helps to boost employee morale and job satisfaction, which leads to higher levels of productivity and better results for the company.
In conclusion, process improvement is a critical component of any successful business. By analyzing their processes and making necessary changes, companies can achieve significant improvements in their bottom line. The benefits of process improvement are numerous, ranging from reducing costs and waste to increasing productivity and output. By improving their processes, companies can deliver better products and services, increase customer satisfaction, and build stronger relationships with their customers.
Identifying Areas for Improvement
Identifying areas for improvement is a crucial step towards achieving organizational success. By analyzing current processes, businesses can identify inefficiencies and develop strategies to improve them. This not only enhances the quality of the products or services offered but also improves customer satisfaction. In this article, we will discuss the two critical steps in identifying areas for improvement.
Analyzing Current Processes
The first step in process improvement is to analyze the current processes. This involves closely examining each step of the process, starting from the initiation to the final stage. The objective is to identify bottlenecks, redundancies, delays, and other inefficiencies that negatively affect the process. By doing so, businesses can develop a clear understanding of the process and its shortcomings.
For instance, a manufacturing company may identify that the production process takes longer than expected due to a bottleneck in the assembly line. By analyzing the process, the company can identify the root cause of the bottleneck and develop strategies to eliminate it. This may involve reorganizing the assembly line, investing in new equipment, or hiring additional staff.
The analysis of current processes is a critical step towards process improvement. It provides businesses with a clear understanding of the process and its shortcomings, allowing them to develop effective strategies to improve it.
Gathering Feedback from Stakeholders
Gathering feedback from stakeholders is another critical step in identifying areas for improvement. Stakeholders are individuals or groups who have a vested interest in the process, such as staff, customers, and vendors. They have first-hand experience with the process and can provide valuable insights into its strengths and weaknesses.
For instance, customers can provide feedback on the quality of the products or services offered, the level of customer service, and the overall experience. Staff members can provide feedback on the efficiency of the process, the level of training provided, and the resources available. Vendors can provide feedback on the quality of the materials or services provided and the level of communication.
Gathering feedback from stakeholders is essential as it provides businesses with valuable insights into the process. This feedback can be used to identify areas of improvement and develop strategies to address them. It also demonstrates a commitment to continuous improvement, which can enhance customer satisfaction and increase brand loyalty.
In conclusion, identifying areas for improvement is a critical step towards achieving organizational success. By analyzing current processes and gathering feedback from stakeholders, businesses can identify inefficiencies and develop strategies to improve them. This leads to enhanced product or service quality, increased customer satisfaction, and improved brand loyalty.
Setting Goals and Objectives
Setting goals and objectives is an essential part of any successful process improvement initiative. Goals provide a sense of direction and purpose, and objectives help define the specific actions necessary to achieve those goals.
Defining SMART Goals
When setting goals, it's important to make them SMART: Specific, Measurable, Achievable, Relevant, and Time-bound. Specific goals clearly define what needs to be accomplished, while measurable goals provide a way to track progress. Achievable goals are realistic and within reach, while relevant goals align with the overall purpose of the initiative. Time-bound goals have a specific deadline for completion, creating a sense of urgency and accountability.
By setting SMART goals, you can ensure that the objectives are attainable and measurable, and can be achieved effectively and efficiently.
Aligning Goals with Business Strategy
While setting SMART goals is important, it's also crucial to align those goals with the overall business strategy. This alignment ensures that the process improvement initiatives support the business strategy, increase efficiency, and sustain long-term objectives.
For example, if the business strategy is to increase customer satisfaction, the process improvement initiative should focus on improving customer service processes. By aligning the goals with the business strategy, the initiative is more likely to have a positive impact on the overall success of the organization.
Overall, setting SMART goals and aligning them with the business strategy is a critical step in any process improvement initiative. By doing so, you can ensure that the initiative is focused, effective, and contributes to the long-term success of the organization.
Developing a Process Improvement Plan
Process improvement is a crucial aspect of any business or organization. It helps to streamline operations, eliminate waste, and increase efficiency. Developing a process improvement plan is essential to ensure that the organization is continuously improving and adapting to the changing business environment. In this article, we will discuss the key steps involved in developing a process improvement plan.
Prioritizing Improvement Initiatives
Before embarking on any process improvement initiative, it is vital to prioritize the initiatives based on their impact and importance. This involves identifying the critical areas that require improvement and evaluating the potential impact of each initiative. Prioritization is necessary because resources are limited, and improvements generate the most significant impact to obtain the best results.
For example, if an organization is experiencing significant delays in its supply chain, it may prioritize initiatives that address this issue before focusing on other areas of the business.
Assigning Roles and Responsibilities
Roles and responsibilities must be assigned to ensure the process improvement initiatives are effectively managed. This includes identifying the team responsible for spearheading the improvement initiative. Defining roles, responsibilities, accountabilities, and timelines ensures that everyone understands what is expected and who is responsible for driving the process forward.
For instance, if an organization is implementing a new software system to improve its accounting processes, it may assign a project manager to oversee the initiative, a team of accountants to test and implement the software, and an IT team to provide technical support.
Identifying Improvement Opportunities
Identifying improvement opportunities is the next step in developing a process improvement plan. This involves analyzing the current processes and identifying areas where improvements can be made. Improvement opportunities may be identified through a variety of methods, such as process mapping, data analysis, and customer feedback.
For example, an organization may conduct a customer survey to identify areas where customers are dissatisfied with the service. Based on the survey results, the organization may identify opportunities to improve its customer service processes.
Developing Improvement Strategies
Once improvement opportunities have been identified, the next step is to develop improvement strategies. Improvement strategies should be designed to address the identified opportunities and align with the organization's overall goals and objectives.
For example, if an organization identifies an opportunity to improve its manufacturing processes, it may develop a strategy to implement lean manufacturing principles. The strategy may involve training employees on lean principles, redesigning the manufacturing process, and implementing new technology to support the new process.
Implementing and Monitoring Improvement Initiatives
The final step in developing a process improvement plan is to implement and monitor improvement initiatives. Implementation involves putting the improvement strategies into action, while monitoring involves tracking progress and making adjustments as necessary.
For example, if an organization implements a new software system to improve its accounting processes, it may monitor the system's performance to ensure that it is achieving the desired results. If the system is not performing as expected, the organization may make adjustments to the system or the processes to improve its performance.
In conclusion, developing a process improvement plan is essential for any organization that wants to remain competitive and adapt to the changing business environment. By prioritizing improvement initiatives, assigning roles and responsibilities, identifying improvement opportunities, developing improvement strategies, and implementing and monitoring improvement initiatives, organizations can continuously improve their processes and achieve their goals.
Implementing the Process Improvement Plan
Communicating the Plan to Stakeholders
It is essential to communicate the process improvement plan to all stakeholders, including staff, customers, and vendors. An effective communication plan includes outlining the changes, their benefits, and timings to reduce resistance and increase buy-in to the new process.
Providing Training and Support
The final step is to provide the necessary training and support to staff to perform their new roles. Training ensures that staff members understand how to implement the new process successfully and efficiently. Support ensures that the team is available to provide guidance and address any issues encountered during the implementation phase.
Conclusion
Process improvement is crucial for businesses looking to streamline their operations and grow in today's competitive environment. Implementing the seven-step process outlined in this article can help drive efficiency, improve customer experiences, and provide long-term benefits for organizations. Whether you're enhancing existing processes or creating new ones, effective process improvement requires a commitment to evaluating and continuously improving.
Article
7 Steps to Implementing Effective Process Improvement
•
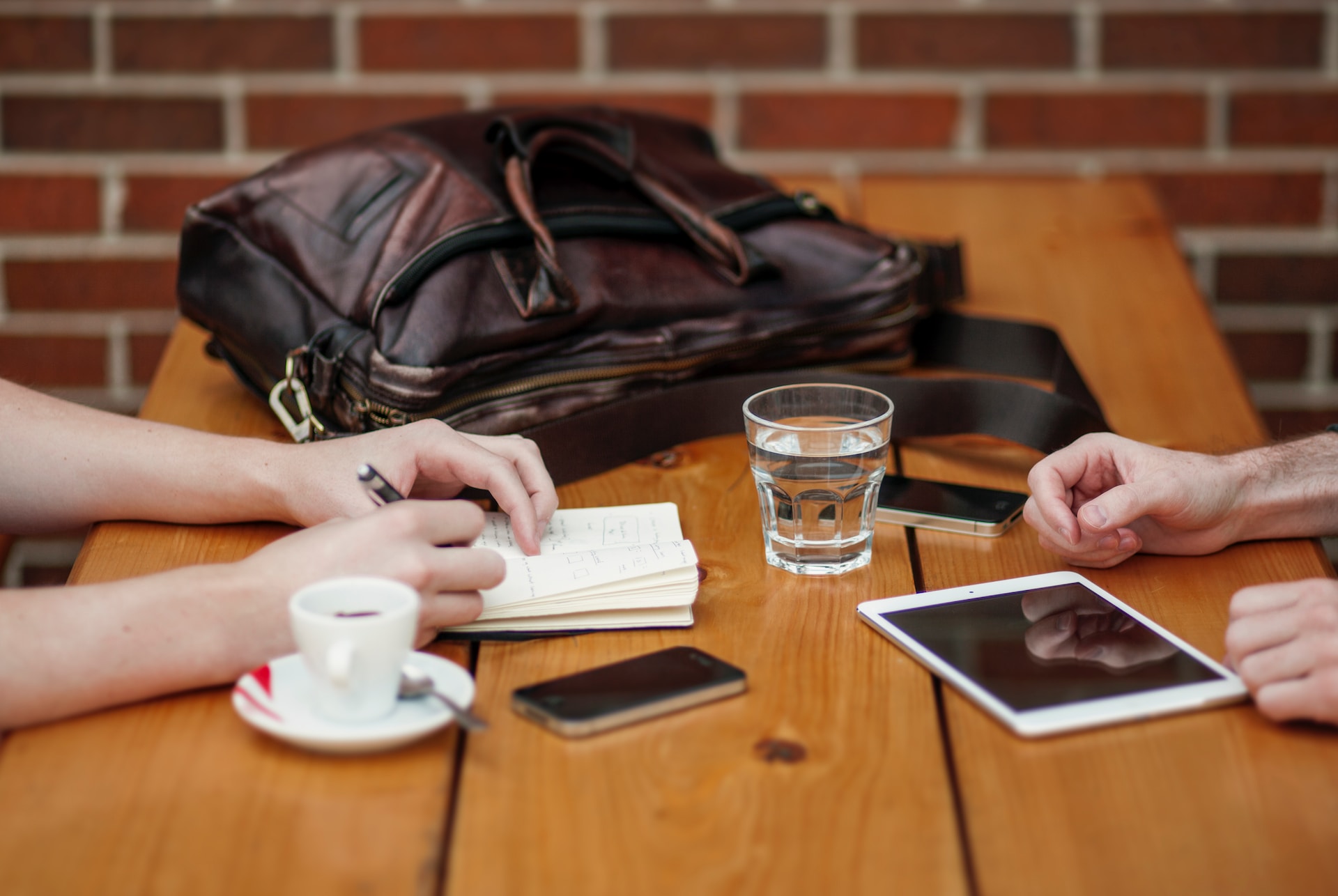