Article
What is Six Sigma and How Can It Help Your Business?
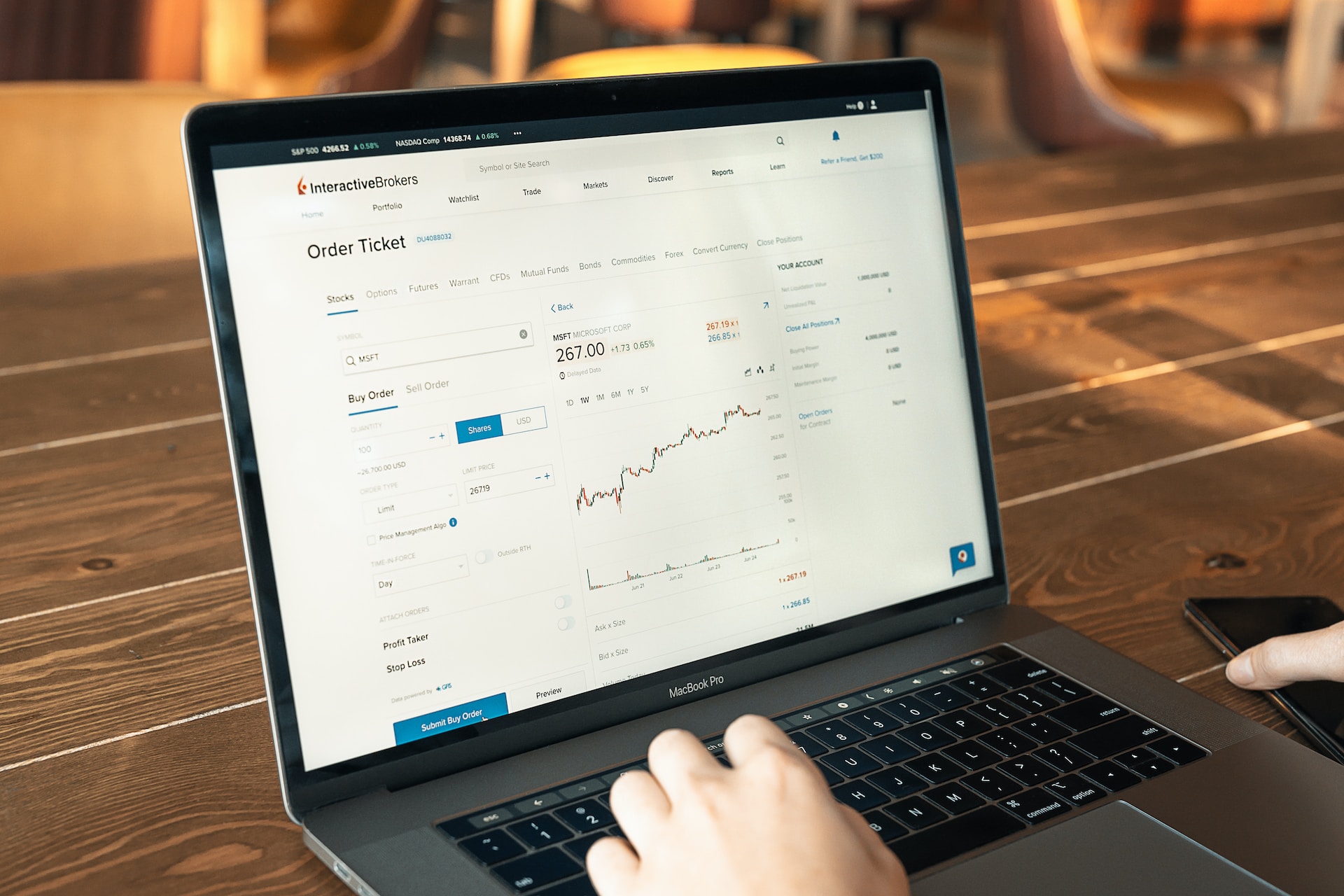
If you've been in the business world for any length of time, you may have heard the term "Six Sigma" thrown around. But what exactly does it mean, and how can it benefit your business? In this article, we will dive deep into the world of Six Sigma and explore its principles, methodologies, and real-world benefits.
Understanding the Concept of Six Sigma
Before we delve into the intricacies of Six Sigma, let's start with a brief overview. Six Sigma is a data-driven methodology that aims to improve business processes and reduce variation. It was developed in the 1980s by Motorola, a leading telecommunications company, and later popularized by Jack Welch during his tenure as CEO of General Electric.
Six Sigma is not just a passing trend; it has a rich history rooted in statistical quality control techniques. The concepts behind Six Sigma can be traced back to the work of process engineers and statisticians like William Edwards Deming and Joseph M. Juran. These pioneers laid the foundation for the methodology with their research and insights into quality management.
The History of Six Sigma
However, it wasn't until the 1980s that Motorola recognized the potential of these concepts and started using them to streamline their manufacturing processes. Motorola's success with Six Sigma attracted the attention of other major corporations, including General Electric, which adopted the methodology under the leadership of Jack Welch.
Under Welch's guidance, General Electric became synonymous with Six Sigma excellence. The company achieved remarkable results by implementing the methodology across its various business units. This success story further propelled Six Sigma into the mainstream, making it a widely adopted practice in industries ranging from manufacturing to healthcare, finance, and beyond.
The Principles of Six Sigma
The foundation of Six Sigma lies in its principles, which guide its implementation in organizations. These principles serve as the pillars of the methodology, ensuring that its core values are upheld. Let's take a closer look at these principles:
- Focus on the customer: Six Sigma emphasizes the importance of understanding customer needs and delivering products or services that meet or exceed their expectations. By putting the customer at the center of the improvement process, organizations can ensure their offerings are truly valuable and relevant.
- Data-driven decision making: The methodology relies on data and statistical analysis to drive decision making. It ensures that changes are based on objective evidence rather than guesswork. By using data to identify patterns, trends, and root causes of problems, organizations can make informed decisions that lead to meaningful improvements.
- Process improvement: Six Sigma aims to identify and eliminate process defects, reduce variability, and continuously improve business processes to achieve better outcomes. By analyzing processes, organizations can identify bottlenecks, inefficiencies, and areas for improvement, leading to increased productivity and customer satisfaction.
- Employee involvement: Six Sigma encourages active engagement from employees at all levels of the organization. By empowering employees to contribute to process improvement efforts, organizations tap into a wealth of knowledge and creativity. This involvement fosters a culture of continuous improvement and ownership, driving sustainable change.
- Management commitment: Successful implementation of Six Sigma requires strong leadership support and commitment to the methodology's goals. Management plays a crucial role in setting the direction, providing resources, and creating an environment conducive to Six Sigma success. Their commitment sets the tone for the entire organization and ensures that Six Sigma becomes ingrained in the company's DNA.
These principles, when applied effectively, can transform organizations by driving operational excellence, improving customer satisfaction, and achieving sustainable growth. Six Sigma is not just a set of tools and techniques; it is a mindset that fosters a culture of continuous improvement and data-driven decision making.
The Importance of Six Sigma in Business
In today's competitive business landscape, organizations strive for excellence in all aspects of their operations. Six Sigma offers a proven framework to achieve this, helping businesses enhance their processes and drive continuous improvement.
But what exactly is Six Sigma and why is it so important in the business world? Six Sigma is a data-driven methodology that focuses on reducing process variation and eliminating defects or non-value-added activities. By systematically identifying and addressing these issues, organizations can streamline their operations, improve quality, lower costs, and ultimately increase customer satisfaction.
Enhancing Business Processes with Six Sigma
One of the primary goals of Six Sigma is to reduce process variation, which in turn leads to improved quality, lower costs, and increased customer satisfaction. By systematically identifying and eliminating defects or non-value-added activities, organizations can streamline their operations and deliver products or services that consistently meet or exceed customer expectations.
Implementing Six Sigma involves a rigorous methodology that includes defining, measuring, analyzing, improving, and controlling processes. This structured approach ensures that organizations not only identify areas for improvement but also implement sustainable solutions that drive continuous improvement.
Furthermore, Six Sigma empowers organizations to identify and prioritize improvement opportunities based on data analysis. This analytical approach ensures that resources are allocated to the most critical areas, leading to tangible and measurable results.
By embracing Six Sigma, businesses can foster a culture of continuous improvement, where every employee is encouraged to identify and solve problems, leading to increased efficiency and effectiveness across the organization.
The Role of Six Sigma in Quality Management
Quality management is a crucial aspect of Six Sigma. The methodology provides organizations with a systematic approach to quality improvement, aiming to reduce process variation and eliminate defects. By implementing robust quality control procedures and continuously monitoring key performance indicators, businesses can achieve higher levels of quality and customer satisfaction.
One of the key tools used in Six Sigma for quality management is the DMAIC (Define, Measure, Analyze, Improve, Control) process. This process allows organizations to define the problem, measure the current state, analyze the root causes, implement improvements, and establish control measures to sustain the improvements.
By following the DMAIC process, organizations can effectively identify and address quality issues, leading to improved product or service quality, reduced waste, and increased customer loyalty. Six Sigma also emphasizes the importance of involving employees at all levels in the quality improvement process, fostering a sense of ownership and accountability.
Moreover, Six Sigma provides businesses with a set of statistical tools and techniques that help in analyzing data, identifying trends, and making data-driven decisions. These tools enable organizations to identify areas of improvement, validate the effectiveness of implemented solutions, and monitor ongoing performance.
Ultimately, Six Sigma helps organizations achieve a competitive edge by consistently delivering high-quality products or services that meet or exceed customer expectations. By focusing on process improvement and data-driven decision-making, businesses can drive continuous improvement, foster innovation, and stay ahead in today's dynamic business environment.
The Six Sigma Methodology
The Six Sigma methodology consists of two primary processes: DMAIC and DMADV. Let's explore each process in detail.
The DMAIC Process
DMAIC, which stands for Define, Measure, Analyze, Improve, and Control, is a problem-solving approach widely used in Six Sigma. This process enables organizations to tackle existing process issues and ensure sustained improvements. Let's break down each step:
- Define: Clearly define the problem, project goals, and customer requirements.
- Measure: Collect data and measure process performance to establish a baseline.
- Analyze: Analyze the collected data to identify the root causes of process variation and performance issues.
- Improve: Develop and implement solutions to address the identified root causes.
- Control: Implement control measures to sustain the improvements and monitor ongoing performance.
The DMADV Process
The DMADV process, short for Define, Measure, Analyze, Design, and Verify, is used when a new product or process is being developed. This process aims to ensure that the final product or process meets or exceeds customer expectations. Let's explore each step:
- Define: Clearly define customer requirements and project goals.
- Measure: Measure and analyze customer needs and competitive benchmarks.
- Analyze: Analyze the gathered data to identify potential design solutions.
- Design: Develop and optimize the new product or process design.
- Verify: Pilot-test the new design and verify its performance.
How Six Sigma Can Improve Your Business
Now that we've covered the fundamentals of Six Sigma, you might wonder how it can specifically benefit your business. Let's explore two key aspects: case studies of successful implementations and the overall benefits of implementing Six Sigma.
Case Studies of Six Sigma in Action
Across industries, numerous case studies have highlighted the transformative impact of Six Sigma. One such example is General Electric, where the methodology played a significant role in boosting quality and driving substantial cost savings. By embracing Six Sigma, GE was able to achieve remarkable improvements in product quality and customer satisfaction, ultimately leading to increased profitability.
Other companies that have successfully implemented Six Sigma include Motorola, Ford, Amazon, and Bank of America. These organizations have realized tangible benefits such as reduced defects, improved cycle times, increased productivity, and enhanced customer loyalty.
The Benefits of Implementing Six Sigma
The benefits of Six Sigma implementation are wide-ranging, impacting various aspects of the business. Here are some key benefits:
- Improved quality: Six Sigma helps organizations achieve higher levels of quality by reducing process variation and eliminating defects.
- Increased customer satisfaction: By consistently delivering high-quality products or services, businesses can enhance customer satisfaction and loyalty.
- Cost reduction: The reduction of process defects and waste translates into significant cost savings for organizations.
- Enhanced efficiency: Six Sigma identifies bottlenecks and streamlines processes, leading to improved operational efficiency.
- Empowering employees: By involving employees in the improvement process, Six Sigma fosters a culture of accountability, innovation, and continuous learning.
- Competitive advantage: With improved quality, customer satisfaction, and cost savings, organizations gain a competitive edge in the marketplace.
Implementing Six Sigma in Your Business
Now that you understand the concept, importance, and benefits of Six Sigma, you might be wondering how to implement it in your own organization. Let's explore the steps involved and some key challenges you may encounter along the way.
Steps to Implement Six Sigma
Implementing Six Sigma requires careful planning and execution. Here are the essential steps to get started:
- Define the project scope: Clearly define the problem or opportunity that will be addressed through Six Sigma.
- Form a team: Assemble a cross-functional team with diverse expertise to drive the implementation process.
- Provide training: Ensure that team members receive appropriate training in Six Sigma methodologies and tools.
- Collect data: Gather data related to the identified problem or opportunity, establishing a baseline for measurement.
- Analyze data: Analyze the collected data to identify root causes and potential improvement opportunities.
- Develop solutions: Generate innovative solutions and develop a plan for implementing the improvements.
- Implement improvements: Put the plan into action and monitor the results of the implemented changes.
- Maintain and sustain: Establish control measures to sustain the improvements and continuously monitor the process.
Challenges in Implementing Six Sigma and How to Overcome Them
While Six Sigma offers tremendous benefits, implementing it may come with certain challenges. Some common challenges include resistance to change, lack of commitment from top management, and difficulties in data collection and analysis. To overcome these challenges, it is crucial to:
- Create a strong change management plan to address resistance and ensure buy-in from employees.
- Gain support from top management and align Six Sigma goals with the overall business strategy.
- Invest in appropriate software and tools to facilitate data collection, analysis, and reporting.
- Provide ongoing training and support to employees at all levels, empowering them to embrace and utilize Six Sigma methodologies effectively.
In conclusion, Six Sigma is a powerful methodology that can significantly benefit businesses of all sizes and industries. By focusing on customer needs, utilizing data-driven decision making, and continuously improving processes, organizations can achieve higher levels of quality, efficiency, and customer satisfaction. If you're eager to enhance your business performance and stand out from the competition, Six Sigma is the way to go!
Similar Blog Posts
Article
What is Six Sigma and How Can It Help Your Business?
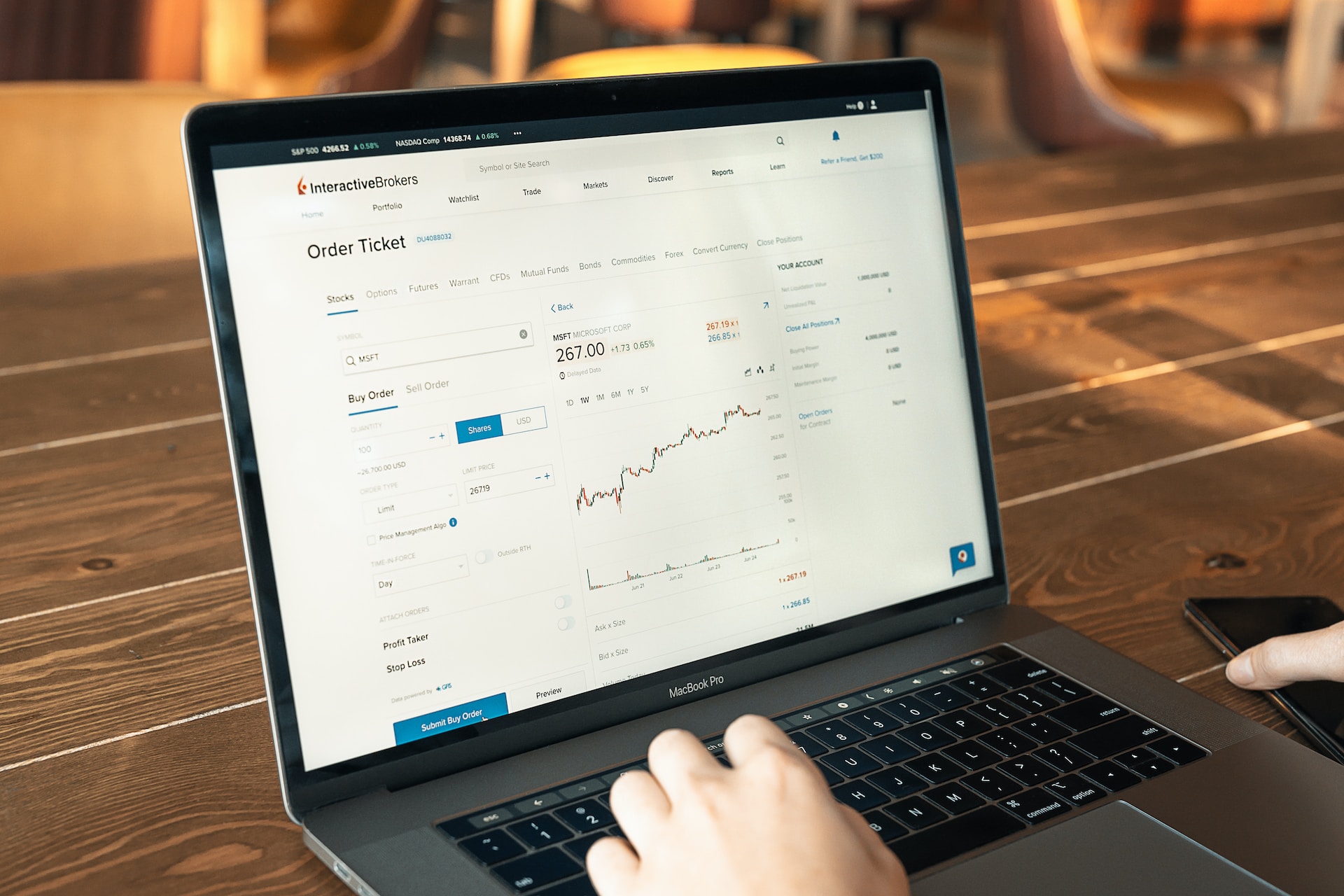
If you've been in the business world for any length of time, you may have heard the term "Six Sigma" thrown around. But what exactly does it mean, and how can it benefit your business? In this article, we will dive deep into the world of Six Sigma and explore its principles, methodologies, and real-world benefits.
Understanding the Concept of Six Sigma
Before we delve into the intricacies of Six Sigma, let's start with a brief overview. Six Sigma is a data-driven methodology that aims to improve business processes and reduce variation. It was developed in the 1980s by Motorola, a leading telecommunications company, and later popularized by Jack Welch during his tenure as CEO of General Electric.
Six Sigma is not just a passing trend; it has a rich history rooted in statistical quality control techniques. The concepts behind Six Sigma can be traced back to the work of process engineers and statisticians like William Edwards Deming and Joseph M. Juran. These pioneers laid the foundation for the methodology with their research and insights into quality management.
The History of Six Sigma
However, it wasn't until the 1980s that Motorola recognized the potential of these concepts and started using them to streamline their manufacturing processes. Motorola's success with Six Sigma attracted the attention of other major corporations, including General Electric, which adopted the methodology under the leadership of Jack Welch.
Under Welch's guidance, General Electric became synonymous with Six Sigma excellence. The company achieved remarkable results by implementing the methodology across its various business units. This success story further propelled Six Sigma into the mainstream, making it a widely adopted practice in industries ranging from manufacturing to healthcare, finance, and beyond.
The Principles of Six Sigma
The foundation of Six Sigma lies in its principles, which guide its implementation in organizations. These principles serve as the pillars of the methodology, ensuring that its core values are upheld. Let's take a closer look at these principles:
- Focus on the customer: Six Sigma emphasizes the importance of understanding customer needs and delivering products or services that meet or exceed their expectations. By putting the customer at the center of the improvement process, organizations can ensure their offerings are truly valuable and relevant.
- Data-driven decision making: The methodology relies on data and statistical analysis to drive decision making. It ensures that changes are based on objective evidence rather than guesswork. By using data to identify patterns, trends, and root causes of problems, organizations can make informed decisions that lead to meaningful improvements.
- Process improvement: Six Sigma aims to identify and eliminate process defects, reduce variability, and continuously improve business processes to achieve better outcomes. By analyzing processes, organizations can identify bottlenecks, inefficiencies, and areas for improvement, leading to increased productivity and customer satisfaction.
- Employee involvement: Six Sigma encourages active engagement from employees at all levels of the organization. By empowering employees to contribute to process improvement efforts, organizations tap into a wealth of knowledge and creativity. This involvement fosters a culture of continuous improvement and ownership, driving sustainable change.
- Management commitment: Successful implementation of Six Sigma requires strong leadership support and commitment to the methodology's goals. Management plays a crucial role in setting the direction, providing resources, and creating an environment conducive to Six Sigma success. Their commitment sets the tone for the entire organization and ensures that Six Sigma becomes ingrained in the company's DNA.
These principles, when applied effectively, can transform organizations by driving operational excellence, improving customer satisfaction, and achieving sustainable growth. Six Sigma is not just a set of tools and techniques; it is a mindset that fosters a culture of continuous improvement and data-driven decision making.
The Importance of Six Sigma in Business
In today's competitive business landscape, organizations strive for excellence in all aspects of their operations. Six Sigma offers a proven framework to achieve this, helping businesses enhance their processes and drive continuous improvement.
But what exactly is Six Sigma and why is it so important in the business world? Six Sigma is a data-driven methodology that focuses on reducing process variation and eliminating defects or non-value-added activities. By systematically identifying and addressing these issues, organizations can streamline their operations, improve quality, lower costs, and ultimately increase customer satisfaction.
Enhancing Business Processes with Six Sigma
One of the primary goals of Six Sigma is to reduce process variation, which in turn leads to improved quality, lower costs, and increased customer satisfaction. By systematically identifying and eliminating defects or non-value-added activities, organizations can streamline their operations and deliver products or services that consistently meet or exceed customer expectations.
Implementing Six Sigma involves a rigorous methodology that includes defining, measuring, analyzing, improving, and controlling processes. This structured approach ensures that organizations not only identify areas for improvement but also implement sustainable solutions that drive continuous improvement.
Furthermore, Six Sigma empowers organizations to identify and prioritize improvement opportunities based on data analysis. This analytical approach ensures that resources are allocated to the most critical areas, leading to tangible and measurable results.
By embracing Six Sigma, businesses can foster a culture of continuous improvement, where every employee is encouraged to identify and solve problems, leading to increased efficiency and effectiveness across the organization.
The Role of Six Sigma in Quality Management
Quality management is a crucial aspect of Six Sigma. The methodology provides organizations with a systematic approach to quality improvement, aiming to reduce process variation and eliminate defects. By implementing robust quality control procedures and continuously monitoring key performance indicators, businesses can achieve higher levels of quality and customer satisfaction.
One of the key tools used in Six Sigma for quality management is the DMAIC (Define, Measure, Analyze, Improve, Control) process. This process allows organizations to define the problem, measure the current state, analyze the root causes, implement improvements, and establish control measures to sustain the improvements.
By following the DMAIC process, organizations can effectively identify and address quality issues, leading to improved product or service quality, reduced waste, and increased customer loyalty. Six Sigma also emphasizes the importance of involving employees at all levels in the quality improvement process, fostering a sense of ownership and accountability.
Moreover, Six Sigma provides businesses with a set of statistical tools and techniques that help in analyzing data, identifying trends, and making data-driven decisions. These tools enable organizations to identify areas of improvement, validate the effectiveness of implemented solutions, and monitor ongoing performance.
Ultimately, Six Sigma helps organizations achieve a competitive edge by consistently delivering high-quality products or services that meet or exceed customer expectations. By focusing on process improvement and data-driven decision-making, businesses can drive continuous improvement, foster innovation, and stay ahead in today's dynamic business environment.
The Six Sigma Methodology
The Six Sigma methodology consists of two primary processes: DMAIC and DMADV. Let's explore each process in detail.
The DMAIC Process
DMAIC, which stands for Define, Measure, Analyze, Improve, and Control, is a problem-solving approach widely used in Six Sigma. This process enables organizations to tackle existing process issues and ensure sustained improvements. Let's break down each step:
- Define: Clearly define the problem, project goals, and customer requirements.
- Measure: Collect data and measure process performance to establish a baseline.
- Analyze: Analyze the collected data to identify the root causes of process variation and performance issues.
- Improve: Develop and implement solutions to address the identified root causes.
- Control: Implement control measures to sustain the improvements and monitor ongoing performance.
The DMADV Process
The DMADV process, short for Define, Measure, Analyze, Design, and Verify, is used when a new product or process is being developed. This process aims to ensure that the final product or process meets or exceeds customer expectations. Let's explore each step:
- Define: Clearly define customer requirements and project goals.
- Measure: Measure and analyze customer needs and competitive benchmarks.
- Analyze: Analyze the gathered data to identify potential design solutions.
- Design: Develop and optimize the new product or process design.
- Verify: Pilot-test the new design and verify its performance.
How Six Sigma Can Improve Your Business
Now that we've covered the fundamentals of Six Sigma, you might wonder how it can specifically benefit your business. Let's explore two key aspects: case studies of successful implementations and the overall benefits of implementing Six Sigma.
Case Studies of Six Sigma in Action
Across industries, numerous case studies have highlighted the transformative impact of Six Sigma. One such example is General Electric, where the methodology played a significant role in boosting quality and driving substantial cost savings. By embracing Six Sigma, GE was able to achieve remarkable improvements in product quality and customer satisfaction, ultimately leading to increased profitability.
Other companies that have successfully implemented Six Sigma include Motorola, Ford, Amazon, and Bank of America. These organizations have realized tangible benefits such as reduced defects, improved cycle times, increased productivity, and enhanced customer loyalty.
The Benefits of Implementing Six Sigma
The benefits of Six Sigma implementation are wide-ranging, impacting various aspects of the business. Here are some key benefits:
- Improved quality: Six Sigma helps organizations achieve higher levels of quality by reducing process variation and eliminating defects.
- Increased customer satisfaction: By consistently delivering high-quality products or services, businesses can enhance customer satisfaction and loyalty.
- Cost reduction: The reduction of process defects and waste translates into significant cost savings for organizations.
- Enhanced efficiency: Six Sigma identifies bottlenecks and streamlines processes, leading to improved operational efficiency.
- Empowering employees: By involving employees in the improvement process, Six Sigma fosters a culture of accountability, innovation, and continuous learning.
- Competitive advantage: With improved quality, customer satisfaction, and cost savings, organizations gain a competitive edge in the marketplace.
Implementing Six Sigma in Your Business
Now that you understand the concept, importance, and benefits of Six Sigma, you might be wondering how to implement it in your own organization. Let's explore the steps involved and some key challenges you may encounter along the way.
Steps to Implement Six Sigma
Implementing Six Sigma requires careful planning and execution. Here are the essential steps to get started:
- Define the project scope: Clearly define the problem or opportunity that will be addressed through Six Sigma.
- Form a team: Assemble a cross-functional team with diverse expertise to drive the implementation process.
- Provide training: Ensure that team members receive appropriate training in Six Sigma methodologies and tools.
- Collect data: Gather data related to the identified problem or opportunity, establishing a baseline for measurement.
- Analyze data: Analyze the collected data to identify root causes and potential improvement opportunities.
- Develop solutions: Generate innovative solutions and develop a plan for implementing the improvements.
- Implement improvements: Put the plan into action and monitor the results of the implemented changes.
- Maintain and sustain: Establish control measures to sustain the improvements and continuously monitor the process.
Challenges in Implementing Six Sigma and How to Overcome Them
While Six Sigma offers tremendous benefits, implementing it may come with certain challenges. Some common challenges include resistance to change, lack of commitment from top management, and difficulties in data collection and analysis. To overcome these challenges, it is crucial to:
- Create a strong change management plan to address resistance and ensure buy-in from employees.
- Gain support from top management and align Six Sigma goals with the overall business strategy.
- Invest in appropriate software and tools to facilitate data collection, analysis, and reporting.
- Provide ongoing training and support to employees at all levels, empowering them to embrace and utilize Six Sigma methodologies effectively.
In conclusion, Six Sigma is a powerful methodology that can significantly benefit businesses of all sizes and industries. By focusing on customer needs, utilizing data-driven decision making, and continuously improving processes, organizations can achieve higher levels of quality, efficiency, and customer satisfaction. If you're eager to enhance your business performance and stand out from the competition, Six Sigma is the way to go!
Article
What is Six Sigma and How Can It Help Your Business?
•
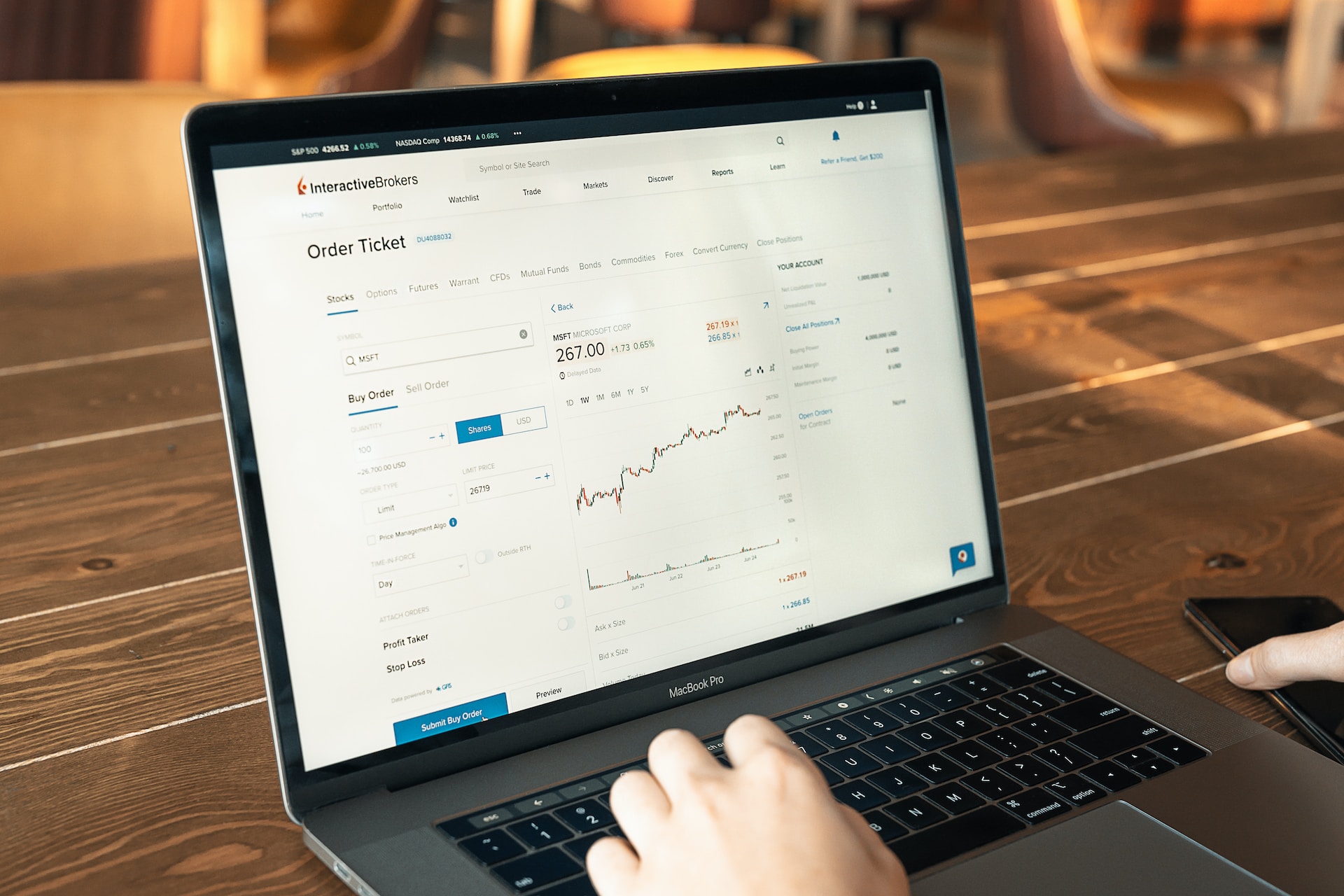