Article
Understanding the Benefits of a Process Flow Diagram
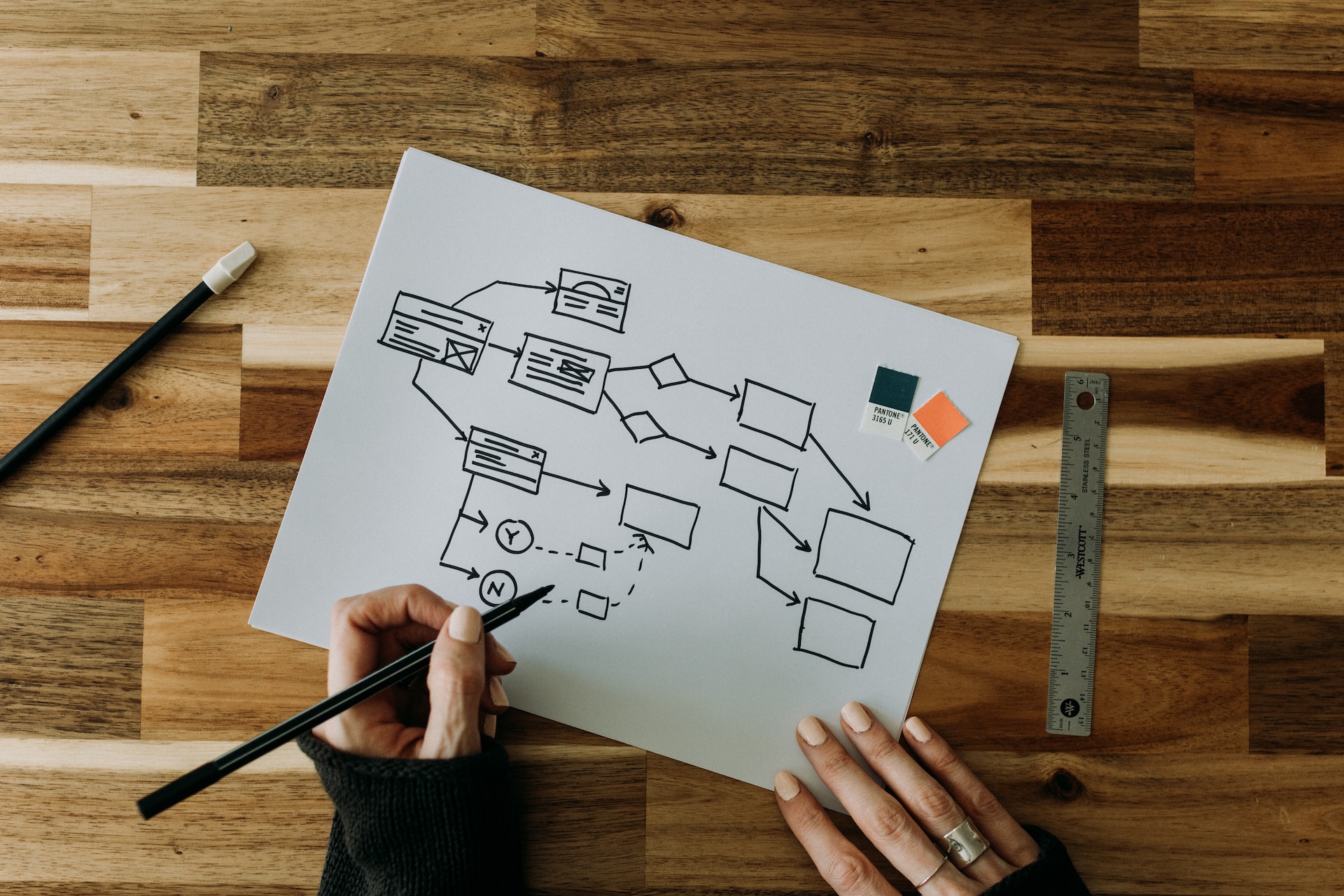
In today’s fast-paced business environment, efficiency and accuracy are more important than ever before. That’s why many organizations have started using process flow diagrams to visualize their workflows and identify opportunities for improvement.
What is a Process Flow Diagram?
A process flow diagram is a graphical representation that illustrates the steps involved in a certain process. It allows you to see the sequence of activities and events that occur from the beginning to the end of the process. Essentially, it is a visual map of how work moves through an organization.
Process flow diagrams are an essential tool for businesses and organizations to improve their processes and increase efficiency. By creating a clear and concise visual representation of a process, it becomes easier to identify areas for improvement and optimize the process.
Key Components of a Process Flow Diagram
To create an effective process flow diagram, there are several key components you should include. These may vary depending on the type of process being diagrammed, but some common elements include:
- Start and End Points - Identify the beginning and end of the process. This helps to define the scope of the process and ensures that everyone involved understands the boundaries of the process.
- Activities - Outline the specific tasks or activities that occur during the process. This provides a detailed understanding of the steps involved and helps to identify areas for improvement.
- Decisions - Show how various decisions affect the process flow. This helps to identify decision points and ensure that the process is optimized for efficiency.
- Data - Indicate any inputs, outputs, or data that are necessary to complete the process. This helps to ensure that everyone involved in the process has access to the necessary information and resources.
By including these key components in a process flow diagram, businesses and organizations can create a clear and concise visual representation of their processes, making it easier to identify areas for improvement and optimize the process for efficiency.
Types of Process Flow Diagrams
There are several different types of process flow diagrams, each with its own unique purpose and benefits. Some common types include:
- Process Flowcharts - This type of diagram shows the flow of materials, people, equipment, or information through a process. It is commonly used in manufacturing and production processes to identify areas for improvement and increase efficiency.
- Value Stream Maps - This diagram identifies where value is added in a process and where waste is occurring. It is commonly used in lean manufacturing to identify areas for improvement and increase efficiency.
- Data Flow Diagrams - This type of diagram shows the flow of data through a system. It is commonly used in software development to identify areas for improvement and optimize the system for efficiency.
By using the appropriate type of process flow diagram for a specific process, businesses and organizations can gain a deeper understanding of the process and identify areas for improvement, ultimately leading to increased efficiency and productivity.
Benefits of Using a Process Flow Diagram
Using a process flow diagram offers numerous benefits for any organization, including:
Improved Communication and Collaboration
A process flow diagram clearly outlines the tasks and events involved in a process, making it easier for employees to understand and work together. It can also help identify where collaboration is needed or where communication breakdowns are occurring.
For example, imagine a manufacturing process where multiple departments are involved in the production of a single product. Without a process flow diagram, it can be difficult for each department to understand how their work fits into the overall process and where they need to collaborate with other departments. However, with a process flow diagram, each department can clearly see how their work impacts the work of other departments, leading to better communication and collaboration.
Enhanced Process Efficiency
By identifying the flow of work in a process, a process flow diagram can help you find ways to streamline and optimize workflows. This can lead to more efficient processes and faster completion times.
For instance, let's say a hospital wants to improve the efficiency of their patient admission process. By creating a process flow diagram, they can identify areas where bottlenecks occur and find ways to eliminate them. This can result in faster admission times, which can lead to improved patient satisfaction.
Simplified Problem Solving and Decision Making
When you have a visual map of the process, it is easier to identify problems and diagnose issues. This can help you find root causes and make informed decisions about process improvement initiatives.
For example, if a company's sales team is struggling to meet their targets, a process flow diagram can help identify where the problem is occurring. Perhaps there is a bottleneck in the sales process, or maybe the team is spending too much time on administrative tasks. By identifying the root cause of the problem, the company can make informed decisions about how to improve their sales process.
Streamlined Process Documentation and Training
A process flow diagram can serve as a useful reference tool for employees who need to learn or be trained on a new process. It can also help ensure that process documentation is accurate and up to date.
For instance, imagine a company is implementing a new software system. By creating a process flow diagram of the new system, they can provide employees with a visual representation of how the system works. This can make it easier for employees to understand and learn the new system, leading to a smoother transition. Additionally, the process flow diagram can serve as a reference tool for employees who need to refresh their knowledge of the system.
Creating a Process Flow Diagram
Creating a process flow diagram is an important step in understanding and improving a business process. A process flow diagram is a visual representation of the steps involved in a process, from start to finish. It can help identify areas for improvement, eliminate inefficiencies, and increase productivity.
Identifying the Scope and Objectives
Before you begin creating a process flow diagram, it is important to identify the scope and objectives of the process being diagrammed. This will help you determine the appropriate level of detail and focus for the diagram. It is important to consider the purpose of the process, the stakeholders involved, and any constraints or limitations that may impact the process.
For example, if you are creating a process flow diagram for a manufacturing process, you may need to consider factors such as raw materials, equipment, and labor availability. Understanding the scope and objectives of the process will help ensure that your diagram accurately reflects the process being analyzed.
Gathering Necessary Information and Data
Next, you need to gather all the necessary information and data about the process. This may involve interviewing employees, reviewing documentation, and observing the process in action. It is important to gather as much information as possible to ensure that your diagram is accurate and complete.
When gathering information, it is important to keep an open mind and be willing to ask questions. This will help you gain a deeper understanding of the process and identify any areas for improvement.
Choosing the Right Diagramming Tool
Once you have all the information you need, you can choose the right diagramming tool for the job. There are many software tools available that can help you create clear and professional-looking process flow diagrams.
When choosing a diagramming tool, it is important to consider factors such as ease of use, functionality, and cost. Some popular diagramming tools include Microsoft Visio, Lucidchart, and Gliffy.
Constructing the Diagram Step by Step
With your tools and data in hand, it's time to start building your diagram. Start by sketching out the basic flow of the process and gradually add more detail. Remember to keep it clear and simple, focusing on the essential steps and components of the process.
As you construct your diagram, it may be helpful to collaborate with other stakeholders to ensure that the diagram accurately reflects the process. This can help identify any areas for improvement and ensure that all stakeholders are on the same page.
Once your diagram is complete, it can be used as a tool for process improvement. By analyzing the diagram, you can identify areas for improvement and implement changes to increase efficiency and productivity.
Real-World Examples of Process Flow Diagrams
Process flow diagrams are an essential tool in many industries, providing a visual representation of how a process works. They can be used to identify inefficiencies, bottlenecks, and waste, and to improve the overall efficiency of a system. Here are a few examples of how process flow diagrams are used in different industries.
Manufacturing Industry
The manufacturing industry is one of the most common users of process flow diagrams. These diagrams are used to show how materials and components move through the production process, from raw materials to finished products. By mapping out the entire process, manufacturers can identify areas where waste is being generated, where bottlenecks are occurring, and where improvements can be made to increase efficiency and reduce costs.
For example, a process flow diagram for a car manufacturing plant might show how raw materials like steel and plastic are transformed into car parts, how those parts are assembled into a car, and how the finished product is tested and shipped to dealerships. By analyzing this diagram, the manufacturer might identify that a particular machine is causing a bottleneck in the process, or that a certain step in the assembly process is generating a lot of waste.
Software Development
Process flow diagrams are also useful in the software development industry. In this context, they are used to illustrate how code, testing, and deployment processes work together to create a finished product. By mapping out the entire process, developers can identify areas where bugs are being introduced, where testing is taking too long, and where improvements can be made to increase efficiency and reduce costs.
For example, a process flow diagram for a software development project might show how code is written, how it is tested, and how it is deployed to production. By analyzing this diagram, the development team might identify that a particular piece of code is causing bugs in the system, or that the testing process is taking too long and delaying the release of the product.
Healthcare Sector
In the healthcare sector, process flow diagrams are often used to visualize patient care pathways or the flow of information through a hospital or clinic. By mapping out the entire process, healthcare providers can identify inefficiencies in the system and improve patient outcomes.
For example, a process flow diagram for a patient's journey through a hospital might show how they are admitted, how they are diagnosed, and how they receive treatment. By analyzing this diagram, healthcare providers might identify that patients are waiting too long to be seen by a doctor, or that certain treatments are not being administered in a timely manner.
Process flow diagrams are an invaluable tool in many industries, helping to identify inefficiencies, bottlenecks, and waste. By mapping out a process in detail, organizations can make informed decisions about how to improve their systems and increase efficiency.
Conclusion
Overall, process flow diagrams are a valuable tool for any organization looking to streamline their processes, improve communication and collaboration, and enhance overall efficiency. With the right tools and strategies, any organization can create effective process flow diagrams that lead to meaningful process improvements.
Article
Understanding the Benefits of a Process Flow Diagram
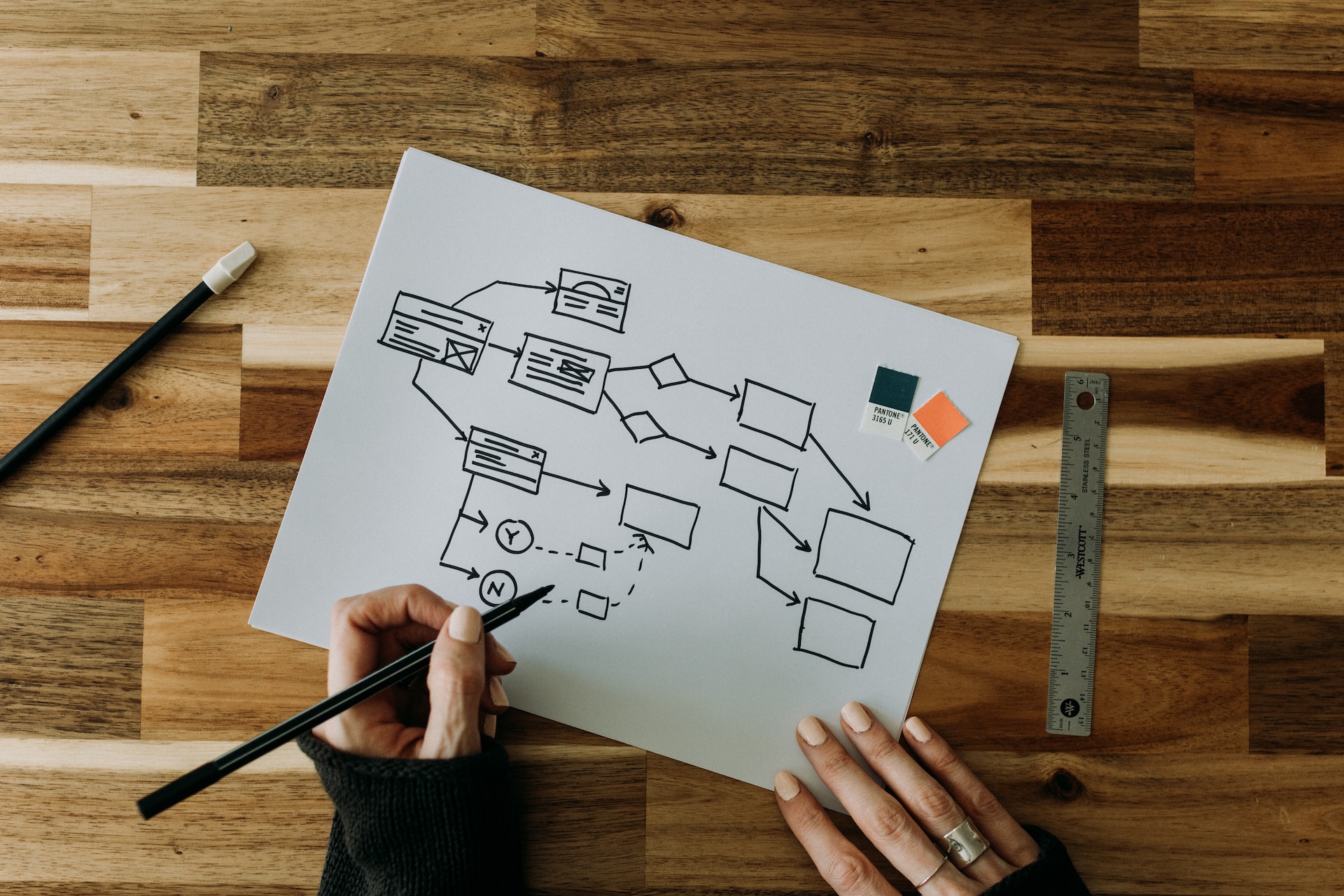
In today’s fast-paced business environment, efficiency and accuracy are more important than ever before. That’s why many organizations have started using process flow diagrams to visualize their workflows and identify opportunities for improvement.
What is a Process Flow Diagram?
A process flow diagram is a graphical representation that illustrates the steps involved in a certain process. It allows you to see the sequence of activities and events that occur from the beginning to the end of the process. Essentially, it is a visual map of how work moves through an organization.
Process flow diagrams are an essential tool for businesses and organizations to improve their processes and increase efficiency. By creating a clear and concise visual representation of a process, it becomes easier to identify areas for improvement and optimize the process.
Key Components of a Process Flow Diagram
To create an effective process flow diagram, there are several key components you should include. These may vary depending on the type of process being diagrammed, but some common elements include:
- Start and End Points - Identify the beginning and end of the process. This helps to define the scope of the process and ensures that everyone involved understands the boundaries of the process.
- Activities - Outline the specific tasks or activities that occur during the process. This provides a detailed understanding of the steps involved and helps to identify areas for improvement.
- Decisions - Show how various decisions affect the process flow. This helps to identify decision points and ensure that the process is optimized for efficiency.
- Data - Indicate any inputs, outputs, or data that are necessary to complete the process. This helps to ensure that everyone involved in the process has access to the necessary information and resources.
By including these key components in a process flow diagram, businesses and organizations can create a clear and concise visual representation of their processes, making it easier to identify areas for improvement and optimize the process for efficiency.
Types of Process Flow Diagrams
There are several different types of process flow diagrams, each with its own unique purpose and benefits. Some common types include:
- Process Flowcharts - This type of diagram shows the flow of materials, people, equipment, or information through a process. It is commonly used in manufacturing and production processes to identify areas for improvement and increase efficiency.
- Value Stream Maps - This diagram identifies where value is added in a process and where waste is occurring. It is commonly used in lean manufacturing to identify areas for improvement and increase efficiency.
- Data Flow Diagrams - This type of diagram shows the flow of data through a system. It is commonly used in software development to identify areas for improvement and optimize the system for efficiency.
By using the appropriate type of process flow diagram for a specific process, businesses and organizations can gain a deeper understanding of the process and identify areas for improvement, ultimately leading to increased efficiency and productivity.
Benefits of Using a Process Flow Diagram
Using a process flow diagram offers numerous benefits for any organization, including:
Improved Communication and Collaboration
A process flow diagram clearly outlines the tasks and events involved in a process, making it easier for employees to understand and work together. It can also help identify where collaboration is needed or where communication breakdowns are occurring.
For example, imagine a manufacturing process where multiple departments are involved in the production of a single product. Without a process flow diagram, it can be difficult for each department to understand how their work fits into the overall process and where they need to collaborate with other departments. However, with a process flow diagram, each department can clearly see how their work impacts the work of other departments, leading to better communication and collaboration.
Enhanced Process Efficiency
By identifying the flow of work in a process, a process flow diagram can help you find ways to streamline and optimize workflows. This can lead to more efficient processes and faster completion times.
For instance, let's say a hospital wants to improve the efficiency of their patient admission process. By creating a process flow diagram, they can identify areas where bottlenecks occur and find ways to eliminate them. This can result in faster admission times, which can lead to improved patient satisfaction.
Simplified Problem Solving and Decision Making
When you have a visual map of the process, it is easier to identify problems and diagnose issues. This can help you find root causes and make informed decisions about process improvement initiatives.
For example, if a company's sales team is struggling to meet their targets, a process flow diagram can help identify where the problem is occurring. Perhaps there is a bottleneck in the sales process, or maybe the team is spending too much time on administrative tasks. By identifying the root cause of the problem, the company can make informed decisions about how to improve their sales process.
Streamlined Process Documentation and Training
A process flow diagram can serve as a useful reference tool for employees who need to learn or be trained on a new process. It can also help ensure that process documentation is accurate and up to date.
For instance, imagine a company is implementing a new software system. By creating a process flow diagram of the new system, they can provide employees with a visual representation of how the system works. This can make it easier for employees to understand and learn the new system, leading to a smoother transition. Additionally, the process flow diagram can serve as a reference tool for employees who need to refresh their knowledge of the system.
Creating a Process Flow Diagram
Creating a process flow diagram is an important step in understanding and improving a business process. A process flow diagram is a visual representation of the steps involved in a process, from start to finish. It can help identify areas for improvement, eliminate inefficiencies, and increase productivity.
Identifying the Scope and Objectives
Before you begin creating a process flow diagram, it is important to identify the scope and objectives of the process being diagrammed. This will help you determine the appropriate level of detail and focus for the diagram. It is important to consider the purpose of the process, the stakeholders involved, and any constraints or limitations that may impact the process.
For example, if you are creating a process flow diagram for a manufacturing process, you may need to consider factors such as raw materials, equipment, and labor availability. Understanding the scope and objectives of the process will help ensure that your diagram accurately reflects the process being analyzed.
Gathering Necessary Information and Data
Next, you need to gather all the necessary information and data about the process. This may involve interviewing employees, reviewing documentation, and observing the process in action. It is important to gather as much information as possible to ensure that your diagram is accurate and complete.
When gathering information, it is important to keep an open mind and be willing to ask questions. This will help you gain a deeper understanding of the process and identify any areas for improvement.
Choosing the Right Diagramming Tool
Once you have all the information you need, you can choose the right diagramming tool for the job. There are many software tools available that can help you create clear and professional-looking process flow diagrams.
When choosing a diagramming tool, it is important to consider factors such as ease of use, functionality, and cost. Some popular diagramming tools include Microsoft Visio, Lucidchart, and Gliffy.
Constructing the Diagram Step by Step
With your tools and data in hand, it's time to start building your diagram. Start by sketching out the basic flow of the process and gradually add more detail. Remember to keep it clear and simple, focusing on the essential steps and components of the process.
As you construct your diagram, it may be helpful to collaborate with other stakeholders to ensure that the diagram accurately reflects the process. This can help identify any areas for improvement and ensure that all stakeholders are on the same page.
Once your diagram is complete, it can be used as a tool for process improvement. By analyzing the diagram, you can identify areas for improvement and implement changes to increase efficiency and productivity.
Real-World Examples of Process Flow Diagrams
Process flow diagrams are an essential tool in many industries, providing a visual representation of how a process works. They can be used to identify inefficiencies, bottlenecks, and waste, and to improve the overall efficiency of a system. Here are a few examples of how process flow diagrams are used in different industries.
Manufacturing Industry
The manufacturing industry is one of the most common users of process flow diagrams. These diagrams are used to show how materials and components move through the production process, from raw materials to finished products. By mapping out the entire process, manufacturers can identify areas where waste is being generated, where bottlenecks are occurring, and where improvements can be made to increase efficiency and reduce costs.
For example, a process flow diagram for a car manufacturing plant might show how raw materials like steel and plastic are transformed into car parts, how those parts are assembled into a car, and how the finished product is tested and shipped to dealerships. By analyzing this diagram, the manufacturer might identify that a particular machine is causing a bottleneck in the process, or that a certain step in the assembly process is generating a lot of waste.
Software Development
Process flow diagrams are also useful in the software development industry. In this context, they are used to illustrate how code, testing, and deployment processes work together to create a finished product. By mapping out the entire process, developers can identify areas where bugs are being introduced, where testing is taking too long, and where improvements can be made to increase efficiency and reduce costs.
For example, a process flow diagram for a software development project might show how code is written, how it is tested, and how it is deployed to production. By analyzing this diagram, the development team might identify that a particular piece of code is causing bugs in the system, or that the testing process is taking too long and delaying the release of the product.
Healthcare Sector
In the healthcare sector, process flow diagrams are often used to visualize patient care pathways or the flow of information through a hospital or clinic. By mapping out the entire process, healthcare providers can identify inefficiencies in the system and improve patient outcomes.
For example, a process flow diagram for a patient's journey through a hospital might show how they are admitted, how they are diagnosed, and how they receive treatment. By analyzing this diagram, healthcare providers might identify that patients are waiting too long to be seen by a doctor, or that certain treatments are not being administered in a timely manner.
Process flow diagrams are an invaluable tool in many industries, helping to identify inefficiencies, bottlenecks, and waste. By mapping out a process in detail, organizations can make informed decisions about how to improve their systems and increase efficiency.
Conclusion
Overall, process flow diagrams are a valuable tool for any organization looking to streamline their processes, improve communication and collaboration, and enhance overall efficiency. With the right tools and strategies, any organization can create effective process flow diagrams that lead to meaningful process improvements.
Article
Understanding the Benefits of a Process Flow Diagram
•
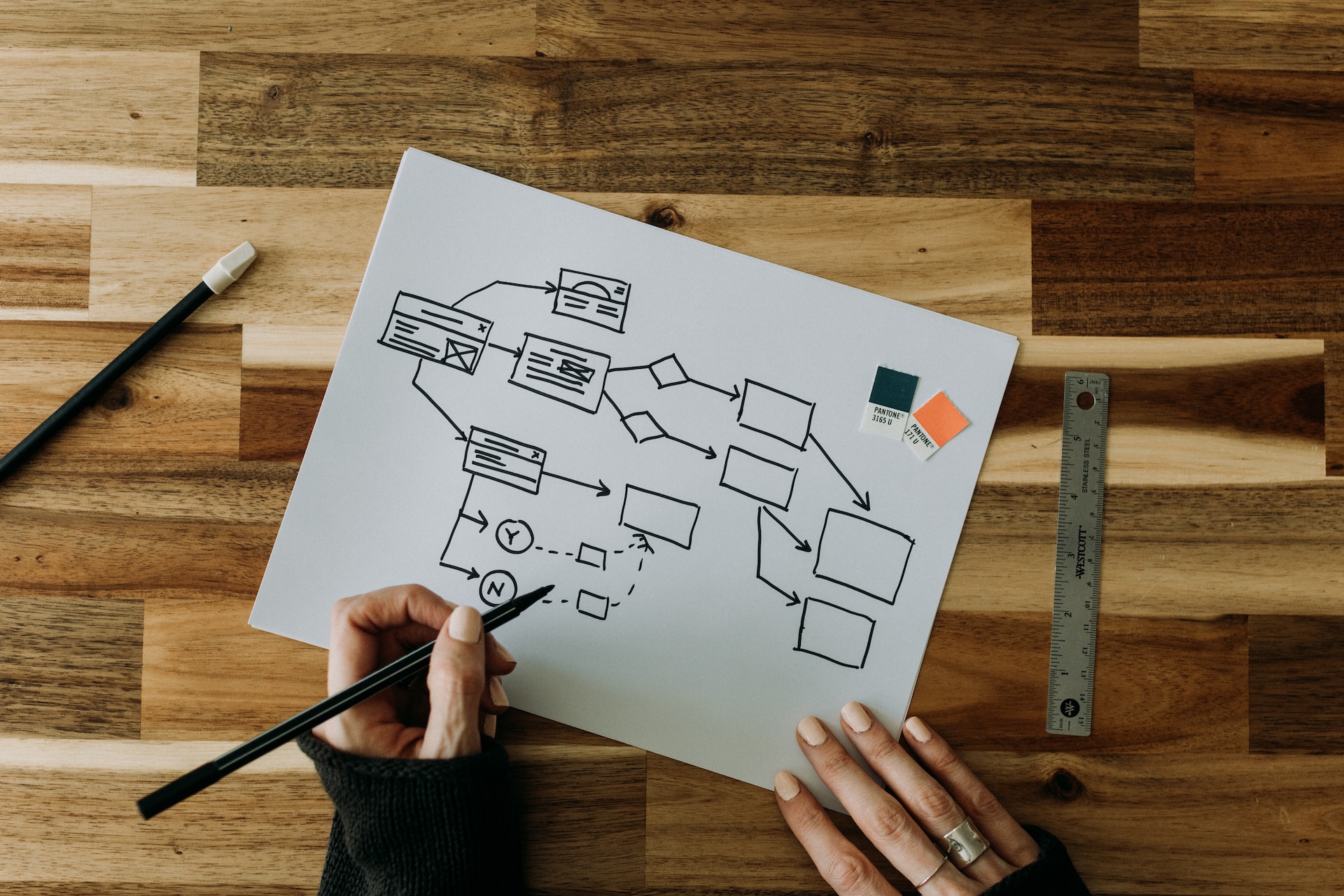