Article
Process Validation: A Guide to Ensuring Quality and Compliance
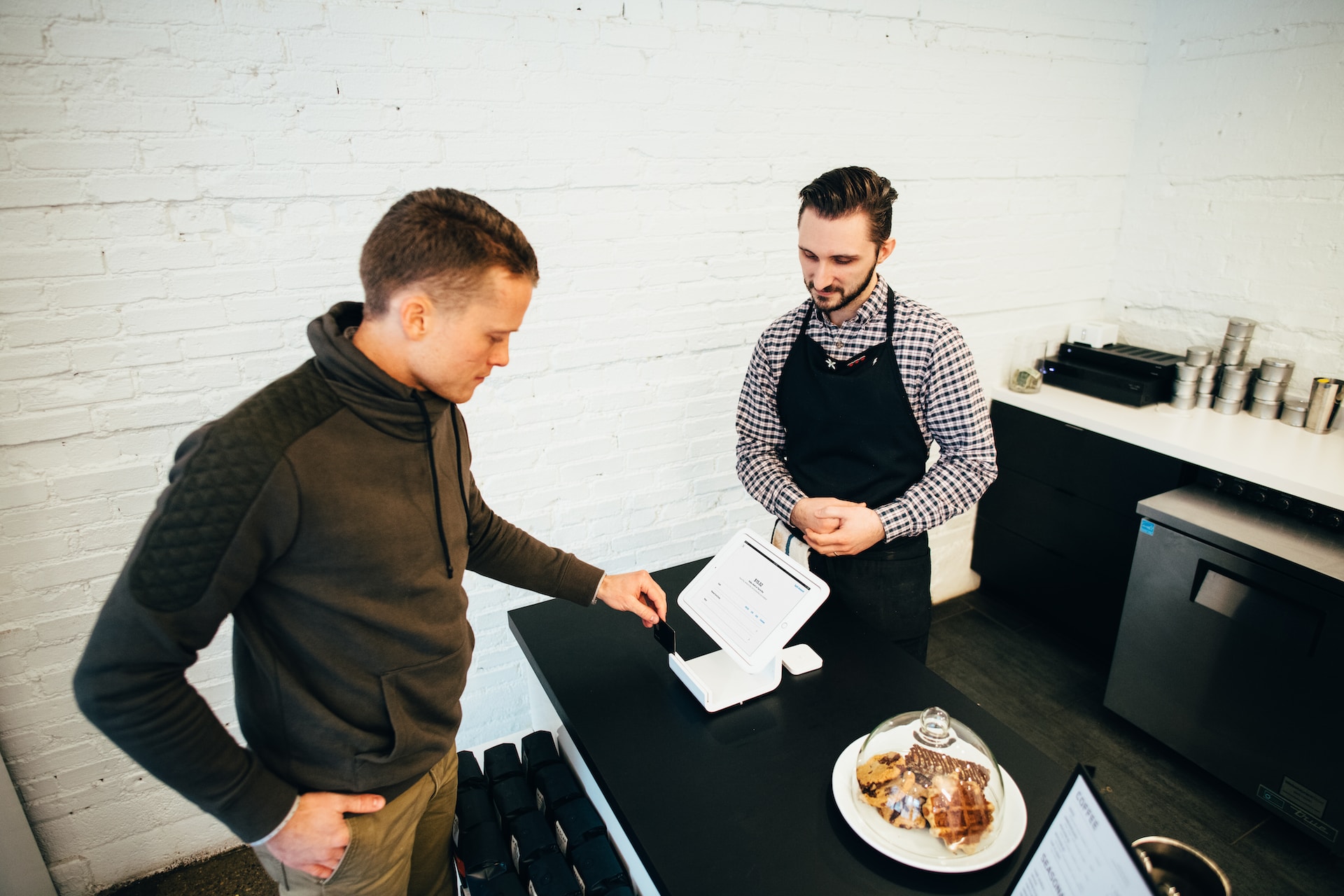
In the highly regulated and fast-paced world of manufacturing, quality control is of utmost importance. Companies must ensure that their processes are reliable, consistent, and capable of consistently producing products that meet the highest standards. This is where process validation comes into play. Process validation is a systematic approach to ensure that a manufacturing process consistently produces a product of predetermined quality. In this comprehensive guide, we will explore the importance of process validation, the key steps involved, regulatory requirements, as well as effective implementation strategies and the potential challenges that may arise.
Understanding Process Validation
Process validation is a critical part of quality assurance in the manufacturing industry. It involves the collection and analysis of data to ensure that a process consistently produces products that meet predetermined specifications and quality requirements. By validating the process, companies can have confidence in the consistency and reliability of their production methods, leading to improved product quality, increased customer satisfaction, and compliance with regulatory standards.
Process validation is a complex and multifaceted process that requires careful planning and execution. It encompasses various activities, including process design, process qualification, and continued process verification. Each of these stages plays a crucial role in ensuring that the manufacturing process is capable of consistently producing high-quality products.
Definition and Importance of Process Validation
Process validation can be defined as the documented evidence that establishes a high degree of assurance that a specific process will consistently produce a product that meets its predetermined specifications and quality characteristics.
When it comes to the importance of process validation, it cannot be overstated. It ensures that a process is capable of consistently producing products that meet the desired quality and performance standards. By validating a process, companies can reduce the risk of producing defective products, minimize the occurrence of deviations, and prevent costly recalls.
Moreover, process validation plays a crucial role in ensuring product safety. It helps identify potential risks and deviations that could compromise the safety of the end products. By addressing these risks and deviations, companies can ensure that their products are safe for consumers to use.
The Role of Process Validation in Quality Assurance
Process validation plays a crucial role in quality assurance by providing assurance that a manufacturing process is under control and capable of consistently producing products that meet customer requirements. It helps identify and mitigate potential risks and deviations, thereby ensuring that the end products are safe, effective, and of the highest quality.
Furthermore, process validation is essential in complying with regulatory requirements. Regulatory agencies, such as the Food and Drug Administration (FDA) and the European Medicines Agency (EMA), require companies to demonstrate that their manufacturing processes are well-controlled and capable of consistently producing high-quality products.
Process validation also contributes to continuous improvement efforts within an organization. By analyzing process data and identifying areas for improvement, companies can enhance their manufacturing processes, leading to increased efficiency, reduced waste, and improved overall performance.
In conclusion, process validation is a crucial component of quality assurance in the manufacturing industry. It ensures that manufacturing processes are capable of consistently producing high-quality products that meet customer requirements and regulatory standards. By validating the process, companies can minimize risks, prevent defects, and improve overall product quality.
Key Steps in Process Validation
The process validation lifecycle consists of three stages: process design, process qualification, and continued process verification. Let's take a closer look at each of these stages:
Stage 1: Process Design
In this stage, the process is designed and documented in detail. The critical process parameters and the corresponding operating ranges are identified. Other factors, such as equipment, facilities, and personnel, are also taken into consideration. The process is then evaluated using risk assessment tools to identify potential areas of concern.
During the process design stage, it is crucial to ensure that all aspects of the process are thoroughly understood and documented. This includes not only the technical specifications but also the potential impact of various factors on the process performance. By carefully designing the process, potential risks and challenges can be identified early on, allowing for appropriate mitigation strategies to be put in place.
Furthermore, process design involves the selection of suitable equipment and facilities that will be used in the production process. Factors such as capacity, reliability, and compatibility with the process requirements are taken into account to ensure smooth and efficient operations.
Additionally, the process design stage also considers the personnel involved in the process. Proper training and qualification of the operators are essential to ensure that they have the necessary skills and knowledge to carry out their tasks effectively and consistently.
Stage 2: Process Qualification
The second stage involves demonstrating that the process is capable of consistently producing products that meet the predetermined quality attributes. It includes the execution of validation protocols to verify the process performance and the collection of data to support the validation.
During the process qualification stage, several activities are carried out to ensure that the process meets the required standards. These activities include installation qualification (IQ), operational qualification (OQ), and performance qualification (PQ).
IQ involves verifying that the equipment is installed correctly and according to the manufacturer's specifications. This ensures that the equipment is in the proper condition to perform its intended functions. OQ, on the other hand, focuses on ensuring that the equipment operates as intended and meets the predefined operating parameters.
PQ is the final step in the process qualification stage and involves verifying that the process consistently produces products conforming to their predetermined specifications. This is achieved by collecting and analyzing data from multiple production runs to ensure that the process is stable and capable of meeting the required quality attributes.
The process qualification stage is critical in establishing confidence in the process's ability to consistently produce high-quality products. It provides evidence that the process is under control and capable of meeting the desired outcomes.
Stage 3: Continued Process Verification
Once the process has been qualified, the third stage focuses on ongoing monitoring and evaluation of the process performance to ensure that it remains in control. Continued process verification involves collecting and analyzing data from routine production runs and making necessary adjustments to maintain the validated state of the process.
During the continued process verification stage, various process performance indicators are monitored to ensure that the process is functioning within acceptable limits. These indicators may include yield, cycle time, process capability indices, and other relevant metrics.
The data collected during this stage provides valuable insights into the process's performance over time. It allows for the identification of any trends or deviations from the validated state, enabling timely corrective actions to be taken. By closely monitoring the process, potential issues can be addressed proactively, minimizing the risk of product non-conformities and ensuring consistent product quality.
Furthermore, the continued process verification stage also serves as an opportunity for continuous improvement. By analyzing the collected data, process optimization opportunities can be identified, leading to enhanced efficiency, reduced costs, and improved overall process performance.
By following these key steps in process validation, organizations can ensure that their processes are robust, reliable, and capable of consistently producing high-quality products. The thorough design, qualification, and ongoing verification of processes are essential in maintaining product quality and meeting regulatory requirements.
Regulatory Requirements for Process Validation
Meeting regulatory requirements is paramount when it comes to process validation. In order to ensure the safety and efficacy of pharmaceutical products, regulatory bodies such as the FDA and the EMA have established guidelines that must be followed. Let's explore these guidelines in more detail:
FDA Guidelines on Process Validation
The FDA's Process Validation Guidance provides a comprehensive framework for the validation of pharmaceutical processes. It outlines a risk-based approach that takes into consideration the potential impact on product quality and patient safety. This approach emphasizes the importance of a life cycle approach, which begins with process design and continues through process qualification and continued process verification.
One of the key aspects highlighted in the FDA guidelines is the need for a robust validation master plan. This plan serves as a roadmap for the validation activities and ensures that all necessary steps are taken to validate the process. It also emphasizes the importance of risk assessment, where potential risks associated with the process are identified and mitigated.
Documented evidence plays a crucial role in the FDA's process validation approach. The guidelines emphasize the need for thorough documentation to demonstrate process control and ensure repeatability and reproducibility. This includes documenting critical process parameters, process performance qualification, and ongoing process monitoring.
European Medicines Agency (EMA) Guidelines
The EMA, which regulates pharmaceutical products in the European Union, also provides guidelines for process validation. These guidelines align closely with the FDA guidelines, emphasizing the importance of a science-based and risk-based approach.
Similar to the FDA, the EMA highlights the need for a comprehensive validation plan. This plan should outline the validation strategy, including the scope, objectives, and acceptance criteria. It should also address the validation of critical process parameters and the validation of analytical methods used to assess product quality.
Data integrity is another critical aspect emphasized by the EMA. The guidelines stress the importance of maintaining accurate, complete, and reliable data throughout the validation process. This includes ensuring proper documentation practices, data traceability, and data integrity checks.
Ongoing process monitoring is also a key requirement outlined by the EMA. This involves the regular monitoring and analysis of process data to ensure that the process remains in a state of control. Any deviations or trends that could potentially impact product quality must be identified and addressed promptly.
By following these guidelines, pharmaceutical manufacturers can ensure that their process validation activities meet the regulatory requirements set forth by the FDA and the EMA. This not only helps to ensure product quality and patient safety but also demonstrates compliance with regulatory standards.
Implementing Effective Process Validation
Now that we understand the importance of process validation and the key steps involved, let's explore some strategies for implementing effective process validation:
Developing a Validation Master Plan
A validation master plan is a comprehensive document that outlines the company's approach to process validation. It provides an overview of the validation activities, responsibilities, and timelines. By developing a validation master plan, companies can ensure that the validation activities are organized, well-documented, and executed in a timely manner.
Risk Assessment in Process Validation
Risk assessment plays a crucial role in process validation. By identifying potential risks and areas of concern, companies can focus their validation efforts on critical process parameters and steps. Risk assessment tools, such as Failure Mode and Effects Analysis (FMEA), can be used to prioritize validation activities and mitigate potential risks.
Challenges and Solutions in Process Validation
While process validation is critical, it is not without its challenges. Let's explore some common pitfalls and best practices for overcoming validation challenges:
Common Pitfalls in Process Validation
One common challenge is the lack of understanding of the regulatory requirements and guidelines. Companies may also struggle with inadequate resources, poor documentation practices, and insufficient training. These challenges can lead to non-compliance, deviations, and increased risks of product quality issues.
Best Practices for Overcoming Validation Challenges
To overcome validation challenges, it is essential to invest in training and education on regulatory requirements. Adequate resources should be allocated to ensure proper documentation and data integrity. Establishing a culture of quality and continuous improvement is also crucial for successful process validation.
Process validation is a critical aspect of ensuring quality and compliance in the manufacturing industry. By following the key steps, meeting regulatory requirements, and implementing effective strategies, companies can validate their processes, reduce risks, and consistently produce products of the highest quality. Remember, process validation is a continuous journey, and companies should strive for ongoing monitoring, evaluation, and improvement to maintain a validated state and remain compliant.
Similar Blog Posts
Article
Process Validation: A Guide to Ensuring Quality and Compliance
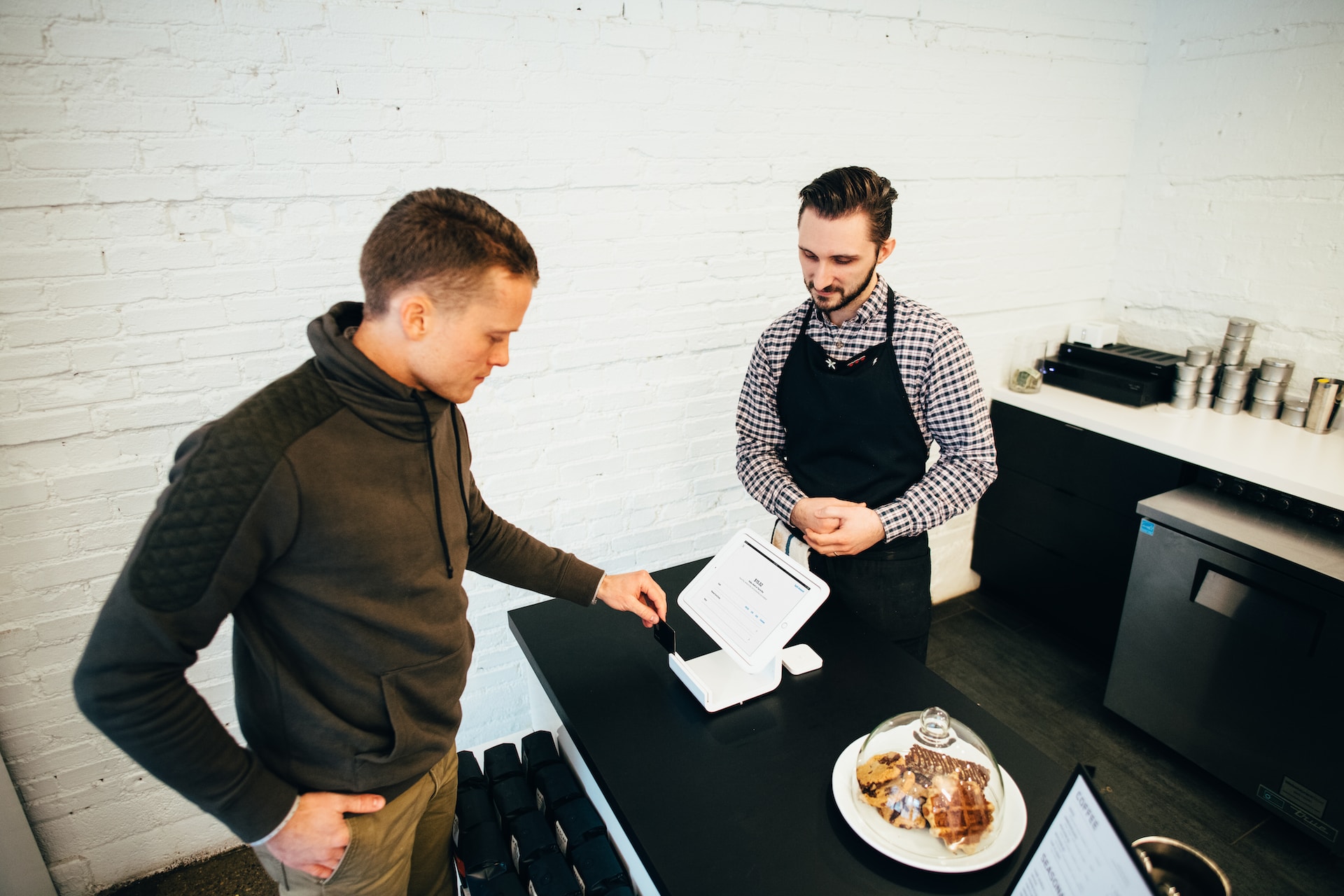
In the highly regulated and fast-paced world of manufacturing, quality control is of utmost importance. Companies must ensure that their processes are reliable, consistent, and capable of consistently producing products that meet the highest standards. This is where process validation comes into play. Process validation is a systematic approach to ensure that a manufacturing process consistently produces a product of predetermined quality. In this comprehensive guide, we will explore the importance of process validation, the key steps involved, regulatory requirements, as well as effective implementation strategies and the potential challenges that may arise.
Understanding Process Validation
Process validation is a critical part of quality assurance in the manufacturing industry. It involves the collection and analysis of data to ensure that a process consistently produces products that meet predetermined specifications and quality requirements. By validating the process, companies can have confidence in the consistency and reliability of their production methods, leading to improved product quality, increased customer satisfaction, and compliance with regulatory standards.
Process validation is a complex and multifaceted process that requires careful planning and execution. It encompasses various activities, including process design, process qualification, and continued process verification. Each of these stages plays a crucial role in ensuring that the manufacturing process is capable of consistently producing high-quality products.
Definition and Importance of Process Validation
Process validation can be defined as the documented evidence that establishes a high degree of assurance that a specific process will consistently produce a product that meets its predetermined specifications and quality characteristics.
When it comes to the importance of process validation, it cannot be overstated. It ensures that a process is capable of consistently producing products that meet the desired quality and performance standards. By validating a process, companies can reduce the risk of producing defective products, minimize the occurrence of deviations, and prevent costly recalls.
Moreover, process validation plays a crucial role in ensuring product safety. It helps identify potential risks and deviations that could compromise the safety of the end products. By addressing these risks and deviations, companies can ensure that their products are safe for consumers to use.
The Role of Process Validation in Quality Assurance
Process validation plays a crucial role in quality assurance by providing assurance that a manufacturing process is under control and capable of consistently producing products that meet customer requirements. It helps identify and mitigate potential risks and deviations, thereby ensuring that the end products are safe, effective, and of the highest quality.
Furthermore, process validation is essential in complying with regulatory requirements. Regulatory agencies, such as the Food and Drug Administration (FDA) and the European Medicines Agency (EMA), require companies to demonstrate that their manufacturing processes are well-controlled and capable of consistently producing high-quality products.
Process validation also contributes to continuous improvement efforts within an organization. By analyzing process data and identifying areas for improvement, companies can enhance their manufacturing processes, leading to increased efficiency, reduced waste, and improved overall performance.
In conclusion, process validation is a crucial component of quality assurance in the manufacturing industry. It ensures that manufacturing processes are capable of consistently producing high-quality products that meet customer requirements and regulatory standards. By validating the process, companies can minimize risks, prevent defects, and improve overall product quality.
Key Steps in Process Validation
The process validation lifecycle consists of three stages: process design, process qualification, and continued process verification. Let's take a closer look at each of these stages:
Stage 1: Process Design
In this stage, the process is designed and documented in detail. The critical process parameters and the corresponding operating ranges are identified. Other factors, such as equipment, facilities, and personnel, are also taken into consideration. The process is then evaluated using risk assessment tools to identify potential areas of concern.
During the process design stage, it is crucial to ensure that all aspects of the process are thoroughly understood and documented. This includes not only the technical specifications but also the potential impact of various factors on the process performance. By carefully designing the process, potential risks and challenges can be identified early on, allowing for appropriate mitigation strategies to be put in place.
Furthermore, process design involves the selection of suitable equipment and facilities that will be used in the production process. Factors such as capacity, reliability, and compatibility with the process requirements are taken into account to ensure smooth and efficient operations.
Additionally, the process design stage also considers the personnel involved in the process. Proper training and qualification of the operators are essential to ensure that they have the necessary skills and knowledge to carry out their tasks effectively and consistently.
Stage 2: Process Qualification
The second stage involves demonstrating that the process is capable of consistently producing products that meet the predetermined quality attributes. It includes the execution of validation protocols to verify the process performance and the collection of data to support the validation.
During the process qualification stage, several activities are carried out to ensure that the process meets the required standards. These activities include installation qualification (IQ), operational qualification (OQ), and performance qualification (PQ).
IQ involves verifying that the equipment is installed correctly and according to the manufacturer's specifications. This ensures that the equipment is in the proper condition to perform its intended functions. OQ, on the other hand, focuses on ensuring that the equipment operates as intended and meets the predefined operating parameters.
PQ is the final step in the process qualification stage and involves verifying that the process consistently produces products conforming to their predetermined specifications. This is achieved by collecting and analyzing data from multiple production runs to ensure that the process is stable and capable of meeting the required quality attributes.
The process qualification stage is critical in establishing confidence in the process's ability to consistently produce high-quality products. It provides evidence that the process is under control and capable of meeting the desired outcomes.
Stage 3: Continued Process Verification
Once the process has been qualified, the third stage focuses on ongoing monitoring and evaluation of the process performance to ensure that it remains in control. Continued process verification involves collecting and analyzing data from routine production runs and making necessary adjustments to maintain the validated state of the process.
During the continued process verification stage, various process performance indicators are monitored to ensure that the process is functioning within acceptable limits. These indicators may include yield, cycle time, process capability indices, and other relevant metrics.
The data collected during this stage provides valuable insights into the process's performance over time. It allows for the identification of any trends or deviations from the validated state, enabling timely corrective actions to be taken. By closely monitoring the process, potential issues can be addressed proactively, minimizing the risk of product non-conformities and ensuring consistent product quality.
Furthermore, the continued process verification stage also serves as an opportunity for continuous improvement. By analyzing the collected data, process optimization opportunities can be identified, leading to enhanced efficiency, reduced costs, and improved overall process performance.
By following these key steps in process validation, organizations can ensure that their processes are robust, reliable, and capable of consistently producing high-quality products. The thorough design, qualification, and ongoing verification of processes are essential in maintaining product quality and meeting regulatory requirements.
Regulatory Requirements for Process Validation
Meeting regulatory requirements is paramount when it comes to process validation. In order to ensure the safety and efficacy of pharmaceutical products, regulatory bodies such as the FDA and the EMA have established guidelines that must be followed. Let's explore these guidelines in more detail:
FDA Guidelines on Process Validation
The FDA's Process Validation Guidance provides a comprehensive framework for the validation of pharmaceutical processes. It outlines a risk-based approach that takes into consideration the potential impact on product quality and patient safety. This approach emphasizes the importance of a life cycle approach, which begins with process design and continues through process qualification and continued process verification.
One of the key aspects highlighted in the FDA guidelines is the need for a robust validation master plan. This plan serves as a roadmap for the validation activities and ensures that all necessary steps are taken to validate the process. It also emphasizes the importance of risk assessment, where potential risks associated with the process are identified and mitigated.
Documented evidence plays a crucial role in the FDA's process validation approach. The guidelines emphasize the need for thorough documentation to demonstrate process control and ensure repeatability and reproducibility. This includes documenting critical process parameters, process performance qualification, and ongoing process monitoring.
European Medicines Agency (EMA) Guidelines
The EMA, which regulates pharmaceutical products in the European Union, also provides guidelines for process validation. These guidelines align closely with the FDA guidelines, emphasizing the importance of a science-based and risk-based approach.
Similar to the FDA, the EMA highlights the need for a comprehensive validation plan. This plan should outline the validation strategy, including the scope, objectives, and acceptance criteria. It should also address the validation of critical process parameters and the validation of analytical methods used to assess product quality.
Data integrity is another critical aspect emphasized by the EMA. The guidelines stress the importance of maintaining accurate, complete, and reliable data throughout the validation process. This includes ensuring proper documentation practices, data traceability, and data integrity checks.
Ongoing process monitoring is also a key requirement outlined by the EMA. This involves the regular monitoring and analysis of process data to ensure that the process remains in a state of control. Any deviations or trends that could potentially impact product quality must be identified and addressed promptly.
By following these guidelines, pharmaceutical manufacturers can ensure that their process validation activities meet the regulatory requirements set forth by the FDA and the EMA. This not only helps to ensure product quality and patient safety but also demonstrates compliance with regulatory standards.
Implementing Effective Process Validation
Now that we understand the importance of process validation and the key steps involved, let's explore some strategies for implementing effective process validation:
Developing a Validation Master Plan
A validation master plan is a comprehensive document that outlines the company's approach to process validation. It provides an overview of the validation activities, responsibilities, and timelines. By developing a validation master plan, companies can ensure that the validation activities are organized, well-documented, and executed in a timely manner.
Risk Assessment in Process Validation
Risk assessment plays a crucial role in process validation. By identifying potential risks and areas of concern, companies can focus their validation efforts on critical process parameters and steps. Risk assessment tools, such as Failure Mode and Effects Analysis (FMEA), can be used to prioritize validation activities and mitigate potential risks.
Challenges and Solutions in Process Validation
While process validation is critical, it is not without its challenges. Let's explore some common pitfalls and best practices for overcoming validation challenges:
Common Pitfalls in Process Validation
One common challenge is the lack of understanding of the regulatory requirements and guidelines. Companies may also struggle with inadequate resources, poor documentation practices, and insufficient training. These challenges can lead to non-compliance, deviations, and increased risks of product quality issues.
Best Practices for Overcoming Validation Challenges
To overcome validation challenges, it is essential to invest in training and education on regulatory requirements. Adequate resources should be allocated to ensure proper documentation and data integrity. Establishing a culture of quality and continuous improvement is also crucial for successful process validation.
Process validation is a critical aspect of ensuring quality and compliance in the manufacturing industry. By following the key steps, meeting regulatory requirements, and implementing effective strategies, companies can validate their processes, reduce risks, and consistently produce products of the highest quality. Remember, process validation is a continuous journey, and companies should strive for ongoing monitoring, evaluation, and improvement to maintain a validated state and remain compliant.
Article
Process Validation: A Guide to Ensuring Quality and Compliance
•
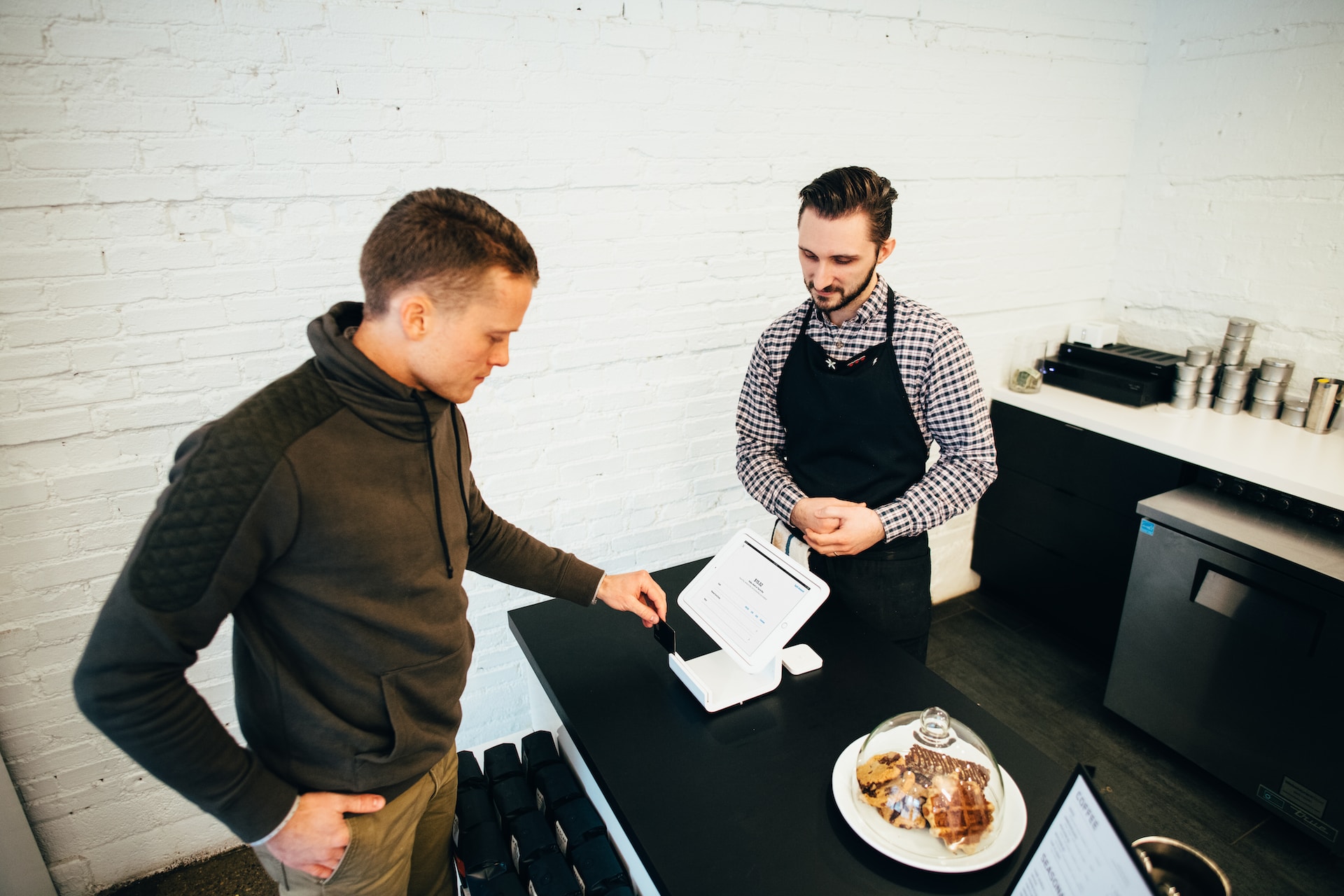