Article
Understanding Manufacturing Organizational Charts
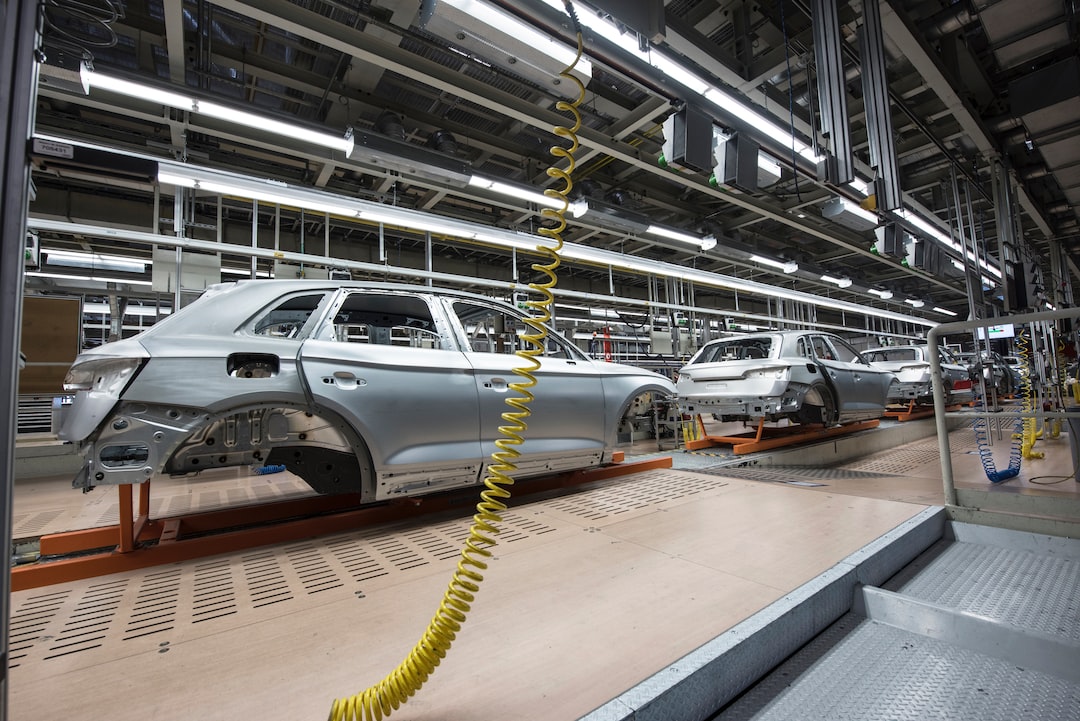
A manufacturing organizational chart is crucial for any manufacturing organization to streamline its operations and reduce costs. This blog post will examine the importance of organizational charts in manufacturing and how they can be used to create different types of structures, define roles, and optimize operational costs.
We'll discuss different types of manufacturing organizational charts commonly used in production departments, such as functional structures, product divisions, and assembly lines. You will also learn about key roles within a manufacturing organization, including plant managers, operations managers, production managers, and quality control personnel.
In addition, inventory control will be examined to see how it contributes significantly to the efficient running of daily operations. We'll also look at how product design impacts the overall success of any manufacturing strategy.
By understanding these essential components that make up a successful manufacturing organization's structure and strategy for reducing costs while increasing efficiency across all levels from production workers up through general management positions like CEOs or COOs alike — readers can gain valuable insights into what it takes to succeed in today's competitive marketplace.
Understanding Manufacturing Organizational Charts
Manufacturing organizational charts are an essential tool for any business operating in the manufacturing industry. By providing a visual representation of the company's hierarchy and how work flows through it, they make it easier to understand who reports to whom, identify communication channels, and streamline decision-making processes.
Organizational frameworks vary in configuration and scope, contingent upon your venture's size, the assembling procedure's multifaceted nature, items, divisions, and spending limitations. The most common types are functional structure (in which teams are organized by function), divisional structure (in which teams are divided into departments), and matrix structure (which combines both functional and divisional approaches).
No matter the type of organizational chart you select for your manufacturing business, there are some key principles to bear in mind when putting it together: taking a top-down or bottom-up approach; mapping out dependencies between departments; focusing on essential facilities & infrastructure categories such as production control, inventory control, and quality control. Assigning clear roles and responsibilities within each department, accurately titling jobs, and establishing effective communication channels among team members.
In addition to these basic steps for designing an ideal factory org chart, several other important factors need to be taken into consideration, such as human resources management strategies like skill development programs, turnover reduction strategies, and accident prevention measures.
These can help ensure that everyone involved is working towards achieving the same goals while also helping reduce costs associated with employee training and onboarding/offboarding processes. Having a clear view of the organization's interrelationships can facilitate collaboration among divisions, thus ensuring everyone agrees when it comes to making crucial decisions related to operations or product design.
Understanding manufacturing organizational charts is essential for any business looking to increase efficiency and optimize its operations. By understanding the different types of structures, businesses can better identify which structure best fits their needs.
Prioritizing Decisions into Facilities & Infrastructure Categories
Prioritizing decisions into facilities and infrastructure categories is essential to creating a successful manufacturing strategy. When designing an effective organizational structure for a manufacturing organization, three key areas — production control, inventory control, and quality control — must be taken into account.
Production Control entails the supervision of production processes, such as product lines, assembly personnel, manufacturing sections, and other staff involved in daily activities. It also includes developing strategies to reduce production costs while maintaining high-efficiency levels. Plant managers or general managers oversee this area of operations in order to ensure maximum productivity from their employees.
Inventory Control focuses on managing stock levels across all products manufactured by the company as well as tracking orders from customers and suppliers alike. The goal here is finding the right balance between having too much or too little inventory so that customer demands can be met without compromising profits through excessive spending on resources such as materials and labor costs associated with producing more than necessary items at any one time.
A successful manufacturing organization must prioritize decisions into facilities and infrastructure categories. Consequently, it is imperative to contemplate the personnel management components of such enterprises in order to guarantee their ongoing prosperity.
Creating an Ideal Factory Organizational Chart
Creating an ideal factory organizational chart is essential for any business owner looking to maximize efficiency and productivity. Knowing the fundamentals of constructing a successful org chart and what to consider when making one is critical.
The first step in designing an effective manufacturing organizational chart is understanding the top-down vs. bottom-up approach. The top-down strategy starts off with an overview of the departments and roles that are essential for success, followed by defining job titles and duties within each department.
This approach ensures personnel are cognizant of their duties and how they fit into the structure. On the other hand, a bottom-up approach starts from individual positions and builds up from there until departments are formed. This type of strategy can help create more efficient teams by focusing on how individual roles interact with each other rather than just relying on predetermined structures or hierarchies.
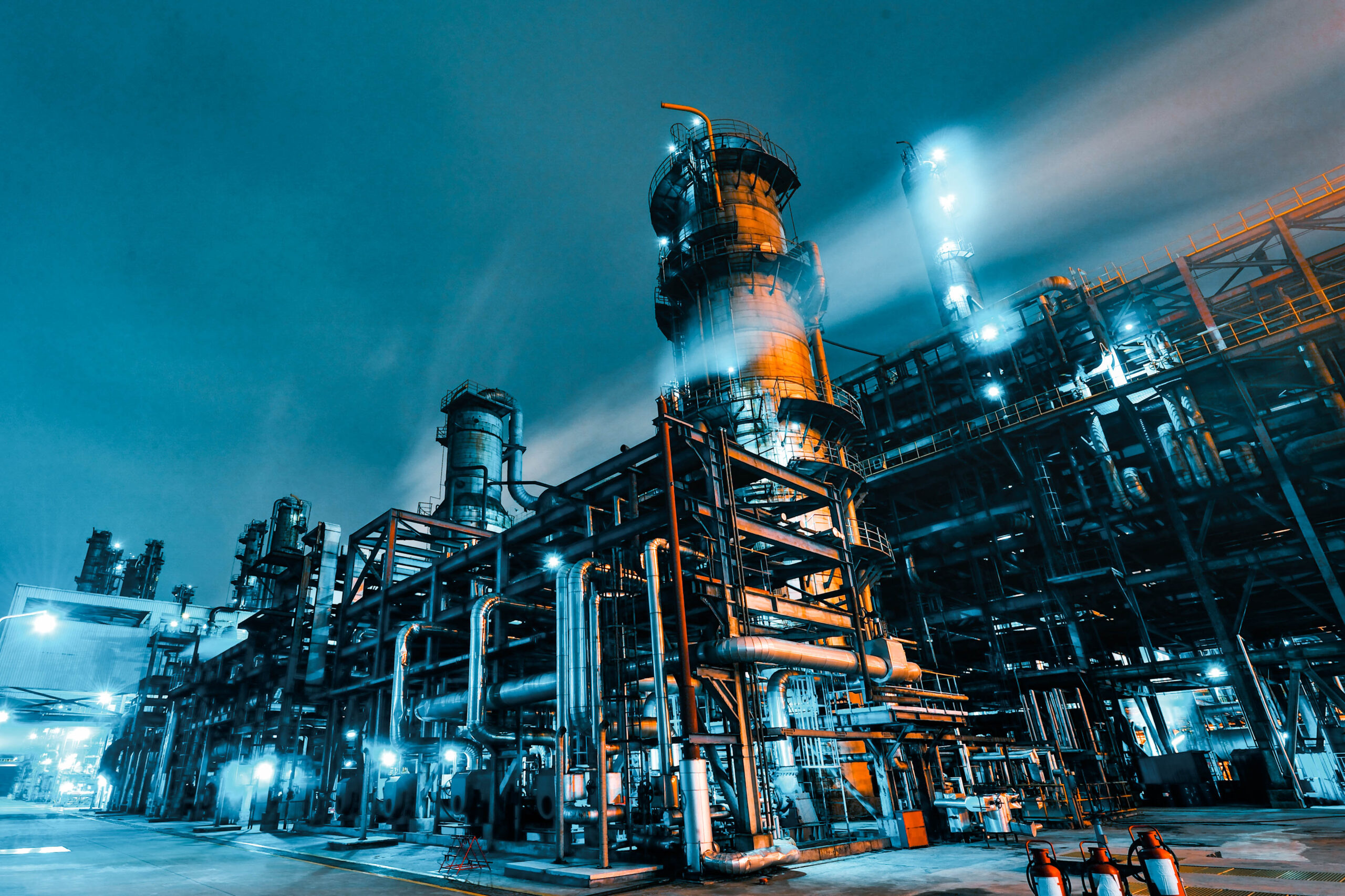
Production staff should be prioritized when constructing an organizational structure since they are responsible for managing daily activities within a factory or facility. Product lines should also be taken into account when creating your org chart since different products may require different levels of oversight or management depending on the complexity or cost associated with them.
Assembly line managers need to also be included in order to oversee production processes. At the same time, inventory control personnel must also be present in order to monitor supplies coming in and going out of warehouses or storage facilities throughout production cycles. Finally, quality control staff must also have representation so that defects can be quickly identified before a product reaches customers’ hands — this will help reduce costs associated with recalls or returns due to bad batches reaching consumers later down the line.
By adhering to key principles during the design phase, it is possible to create an organizational chart that provides clear visibility into tasks and roles, optimizing productivity in any scale of operation. Whether you are running small-scale operations like jewelry-making workshops or large-scale factories producing hundreds of thousands of units per month, having clear visibility over who does what will make sure everyone stays focused on their respective tasks without getting lost along the way.
FAQs in Relation to Manufacturing Organizational Chart
What is the organizational structure of a manufacturing industry?
The organizational structure of a manufacturing industry typically consists of several distinct layers, including top-level management, middle managers and supervisors, production workers, and support staff. Top-level management is responsible for setting the overall direction and making key decisions. Middle managers are responsible for coordinating activities between departments while supervising production workers in their daily tasks.
Production workers handle the actual work involved in producing goods or services, while support staff provides administrative assistance to other employees within the organization. All these functions must be collaboratively managed to ensure that all elements of the enterprise are functioning optimally.
What is the importance of an organizational structure in manufacturing?
Organizational structure is essential for manufacturing businesses as it helps to create a framework of responsibilities, roles, and processes that ensure efficient operations. An efficient organizational structure outlines who has the power to decide how tasks are assigned and handled, as well as what aims the business should strive for.
Additionally, an effective organizational structure allows manufacturers to identify potential areas of improvement or growth opportunities while providing clear communication between departments so they can work together efficiently.
What are the four types of organizational chart?
1. An Organizational Hierarchy Chart
An organizational hierarchy chart illustrates the various levels of a business, from top to bottom, and details who reports to whom as well as which departments are subordinate to others.
2. A Matrix Organizational Chart
A matrix organizational chart is a tool utilized to coordinate two or more functions between various people and teams with the purpose of achieving successful outcomes; it outlines roles, responsibilities, and relationships among those involved. It illustrates the relationships among those involved in a project and their responsibilities and roles within it.
3. Flat Organizational Chart
A flat organizational chart has few layers of management, with all employees having equal access to decision-making processes without any formal reporting structure in place. In this setup, communication tends to flow freely across teams allowing for quick decisions on projects and tasks while also giving everyone equal opportunities for input into decisions made by the team overall.
4. Functional Organizational Chart
This type of chart focuses on grouping individuals according to their skillset rather than by hierarchy or role title alone. An individual’s expertise will determine where they fit into the organization’s function-based structure. The functional organizational chart enables organizations to maximize efficiency through specialization while minimizing redundancies throughout the organization.
Why is an organizational chart important, especially in a large manufacturing organization?
An organizational chart is an essential tool for any large manufacturing organization. It clearly outlines the roles and responsibilities of each team member and how they are connected to one another. This assists in achieving tasks proficiently and successfully, as well as supplying a system for making decisions.
Additionally, it provides clarity on who has authority over which areas within the company, making it easier to delegate duties appropriately. Lastly, an organizational chart can also be used as a communication tool between teams in order to keep everyone informed about changes or updates throughout the business.
Conclusion
In conclusion, having a well-defined manufacturing organizational chart can be incredibly beneficial for small-to-medium-sized businesses. It helps to create clarity and structure within the organization by clearly outlining the roles and responsibilities of each team member.
By optimizing your manufacturing organizational chart, you can ensure that everyone works together efficiently towards common goals while making the most out of every available resource. With careful planning and execution, a comprehensive manufacturing organizational chart can help take your business operations to new heights.
Sign up now for a free 7-day with Trainual and scale your business!
Similar Blog Posts
Article
Understanding Manufacturing Organizational Charts
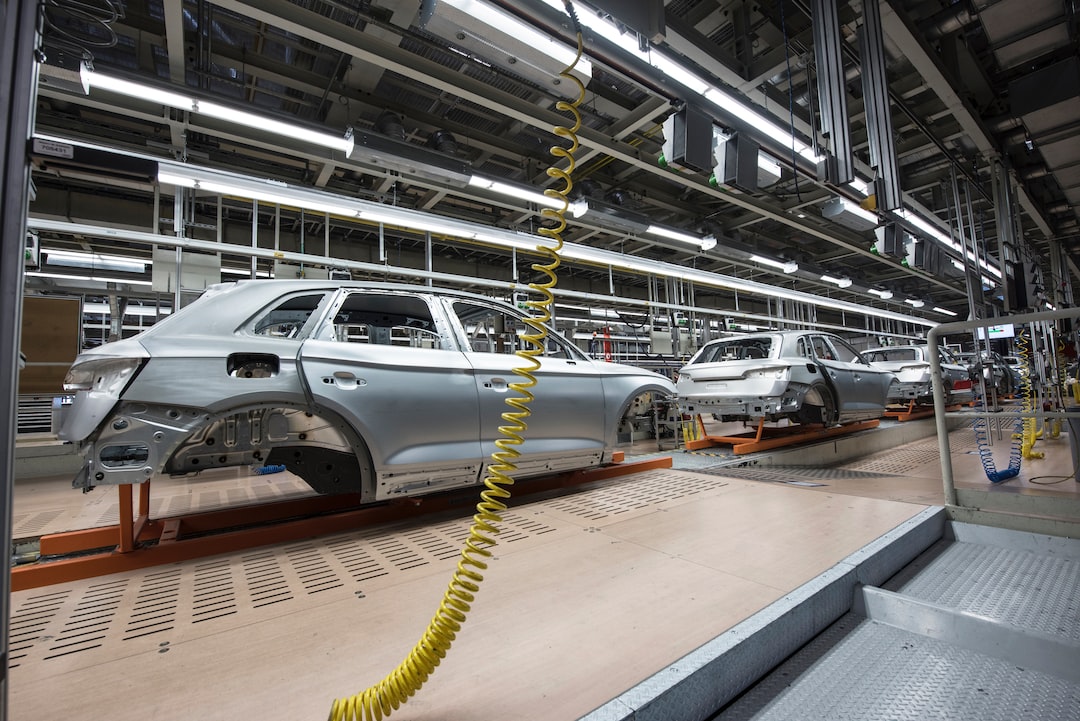
A manufacturing organizational chart is crucial for any manufacturing organization to streamline its operations and reduce costs. This blog post will examine the importance of organizational charts in manufacturing and how they can be used to create different types of structures, define roles, and optimize operational costs.
We'll discuss different types of manufacturing organizational charts commonly used in production departments, such as functional structures, product divisions, and assembly lines. You will also learn about key roles within a manufacturing organization, including plant managers, operations managers, production managers, and quality control personnel.
In addition, inventory control will be examined to see how it contributes significantly to the efficient running of daily operations. We'll also look at how product design impacts the overall success of any manufacturing strategy.
By understanding these essential components that make up a successful manufacturing organization's structure and strategy for reducing costs while increasing efficiency across all levels from production workers up through general management positions like CEOs or COOs alike — readers can gain valuable insights into what it takes to succeed in today's competitive marketplace.
Understanding Manufacturing Organizational Charts
Manufacturing organizational charts are an essential tool for any business operating in the manufacturing industry. By providing a visual representation of the company's hierarchy and how work flows through it, they make it easier to understand who reports to whom, identify communication channels, and streamline decision-making processes.
Organizational frameworks vary in configuration and scope, contingent upon your venture's size, the assembling procedure's multifaceted nature, items, divisions, and spending limitations. The most common types are functional structure (in which teams are organized by function), divisional structure (in which teams are divided into departments), and matrix structure (which combines both functional and divisional approaches).
No matter the type of organizational chart you select for your manufacturing business, there are some key principles to bear in mind when putting it together: taking a top-down or bottom-up approach; mapping out dependencies between departments; focusing on essential facilities & infrastructure categories such as production control, inventory control, and quality control. Assigning clear roles and responsibilities within each department, accurately titling jobs, and establishing effective communication channels among team members.
In addition to these basic steps for designing an ideal factory org chart, several other important factors need to be taken into consideration, such as human resources management strategies like skill development programs, turnover reduction strategies, and accident prevention measures.
These can help ensure that everyone involved is working towards achieving the same goals while also helping reduce costs associated with employee training and onboarding/offboarding processes. Having a clear view of the organization's interrelationships can facilitate collaboration among divisions, thus ensuring everyone agrees when it comes to making crucial decisions related to operations or product design.
Understanding manufacturing organizational charts is essential for any business looking to increase efficiency and optimize its operations. By understanding the different types of structures, businesses can better identify which structure best fits their needs.
Prioritizing Decisions into Facilities & Infrastructure Categories
Prioritizing decisions into facilities and infrastructure categories is essential to creating a successful manufacturing strategy. When designing an effective organizational structure for a manufacturing organization, three key areas — production control, inventory control, and quality control — must be taken into account.
Production Control entails the supervision of production processes, such as product lines, assembly personnel, manufacturing sections, and other staff involved in daily activities. It also includes developing strategies to reduce production costs while maintaining high-efficiency levels. Plant managers or general managers oversee this area of operations in order to ensure maximum productivity from their employees.
Inventory Control focuses on managing stock levels across all products manufactured by the company as well as tracking orders from customers and suppliers alike. The goal here is finding the right balance between having too much or too little inventory so that customer demands can be met without compromising profits through excessive spending on resources such as materials and labor costs associated with producing more than necessary items at any one time.
A successful manufacturing organization must prioritize decisions into facilities and infrastructure categories. Consequently, it is imperative to contemplate the personnel management components of such enterprises in order to guarantee their ongoing prosperity.
Creating an Ideal Factory Organizational Chart
Creating an ideal factory organizational chart is essential for any business owner looking to maximize efficiency and productivity. Knowing the fundamentals of constructing a successful org chart and what to consider when making one is critical.
The first step in designing an effective manufacturing organizational chart is understanding the top-down vs. bottom-up approach. The top-down strategy starts off with an overview of the departments and roles that are essential for success, followed by defining job titles and duties within each department.
This approach ensures personnel are cognizant of their duties and how they fit into the structure. On the other hand, a bottom-up approach starts from individual positions and builds up from there until departments are formed. This type of strategy can help create more efficient teams by focusing on how individual roles interact with each other rather than just relying on predetermined structures or hierarchies.
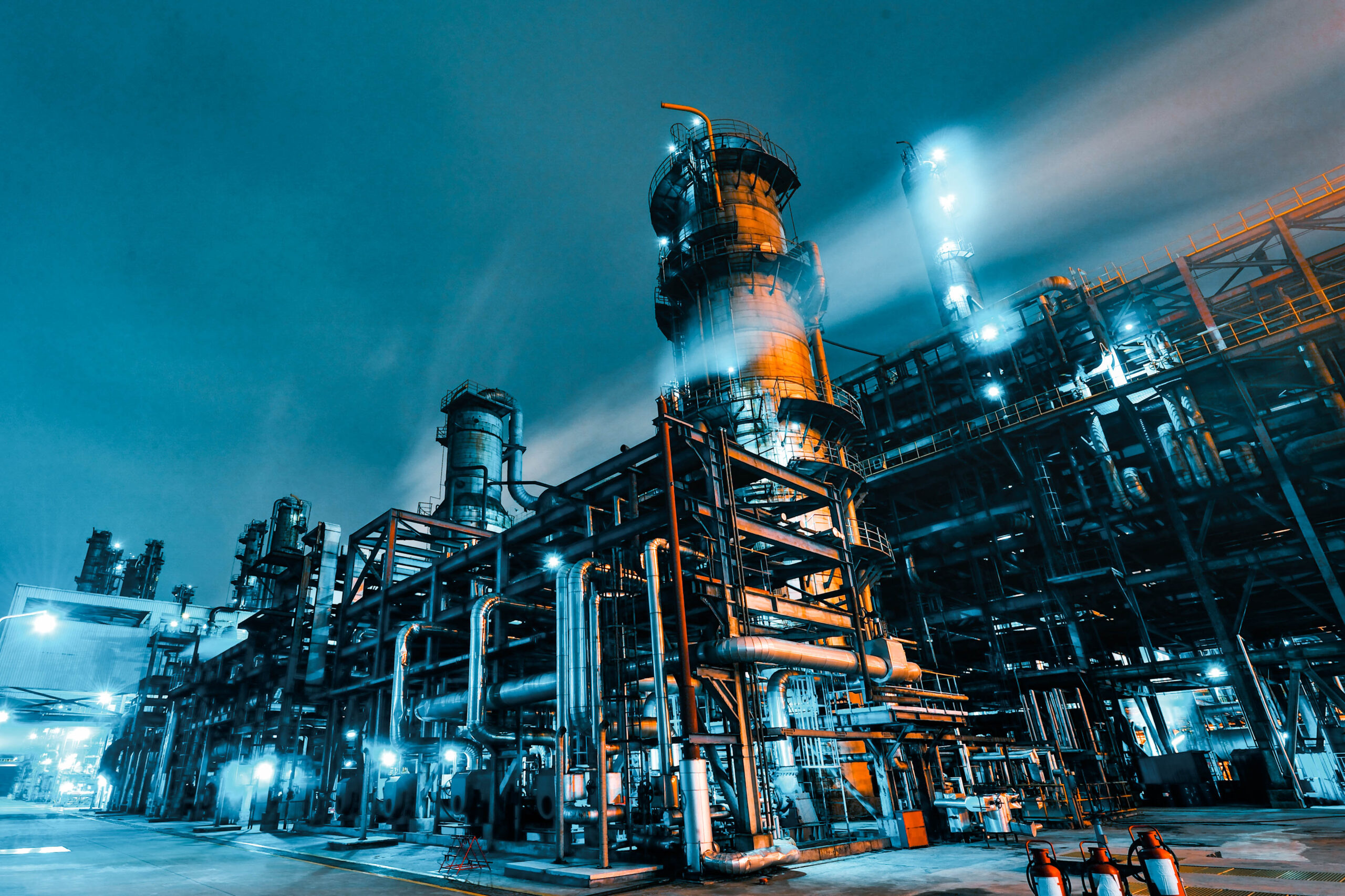
Production staff should be prioritized when constructing an organizational structure since they are responsible for managing daily activities within a factory or facility. Product lines should also be taken into account when creating your org chart since different products may require different levels of oversight or management depending on the complexity or cost associated with them.
Assembly line managers need to also be included in order to oversee production processes. At the same time, inventory control personnel must also be present in order to monitor supplies coming in and going out of warehouses or storage facilities throughout production cycles. Finally, quality control staff must also have representation so that defects can be quickly identified before a product reaches customers’ hands — this will help reduce costs associated with recalls or returns due to bad batches reaching consumers later down the line.
By adhering to key principles during the design phase, it is possible to create an organizational chart that provides clear visibility into tasks and roles, optimizing productivity in any scale of operation. Whether you are running small-scale operations like jewelry-making workshops or large-scale factories producing hundreds of thousands of units per month, having clear visibility over who does what will make sure everyone stays focused on their respective tasks without getting lost along the way.
FAQs in Relation to Manufacturing Organizational Chart
What is the organizational structure of a manufacturing industry?
The organizational structure of a manufacturing industry typically consists of several distinct layers, including top-level management, middle managers and supervisors, production workers, and support staff. Top-level management is responsible for setting the overall direction and making key decisions. Middle managers are responsible for coordinating activities between departments while supervising production workers in their daily tasks.
Production workers handle the actual work involved in producing goods or services, while support staff provides administrative assistance to other employees within the organization. All these functions must be collaboratively managed to ensure that all elements of the enterprise are functioning optimally.
What is the importance of an organizational structure in manufacturing?
Organizational structure is essential for manufacturing businesses as it helps to create a framework of responsibilities, roles, and processes that ensure efficient operations. An efficient organizational structure outlines who has the power to decide how tasks are assigned and handled, as well as what aims the business should strive for.
Additionally, an effective organizational structure allows manufacturers to identify potential areas of improvement or growth opportunities while providing clear communication between departments so they can work together efficiently.
What are the four types of organizational chart?
1. An Organizational Hierarchy Chart
An organizational hierarchy chart illustrates the various levels of a business, from top to bottom, and details who reports to whom as well as which departments are subordinate to others.
2. A Matrix Organizational Chart
A matrix organizational chart is a tool utilized to coordinate two or more functions between various people and teams with the purpose of achieving successful outcomes; it outlines roles, responsibilities, and relationships among those involved. It illustrates the relationships among those involved in a project and their responsibilities and roles within it.
3. Flat Organizational Chart
A flat organizational chart has few layers of management, with all employees having equal access to decision-making processes without any formal reporting structure in place. In this setup, communication tends to flow freely across teams allowing for quick decisions on projects and tasks while also giving everyone equal opportunities for input into decisions made by the team overall.
4. Functional Organizational Chart
This type of chart focuses on grouping individuals according to their skillset rather than by hierarchy or role title alone. An individual’s expertise will determine where they fit into the organization’s function-based structure. The functional organizational chart enables organizations to maximize efficiency through specialization while minimizing redundancies throughout the organization.
Why is an organizational chart important, especially in a large manufacturing organization?
An organizational chart is an essential tool for any large manufacturing organization. It clearly outlines the roles and responsibilities of each team member and how they are connected to one another. This assists in achieving tasks proficiently and successfully, as well as supplying a system for making decisions.
Additionally, it provides clarity on who has authority over which areas within the company, making it easier to delegate duties appropriately. Lastly, an organizational chart can also be used as a communication tool between teams in order to keep everyone informed about changes or updates throughout the business.
Conclusion
In conclusion, having a well-defined manufacturing organizational chart can be incredibly beneficial for small-to-medium-sized businesses. It helps to create clarity and structure within the organization by clearly outlining the roles and responsibilities of each team member.
By optimizing your manufacturing organizational chart, you can ensure that everyone works together efficiently towards common goals while making the most out of every available resource. With careful planning and execution, a comprehensive manufacturing organizational chart can help take your business operations to new heights.
Sign up now for a free 7-day with Trainual and scale your business!
Article
Understanding Manufacturing Organizational Charts
•
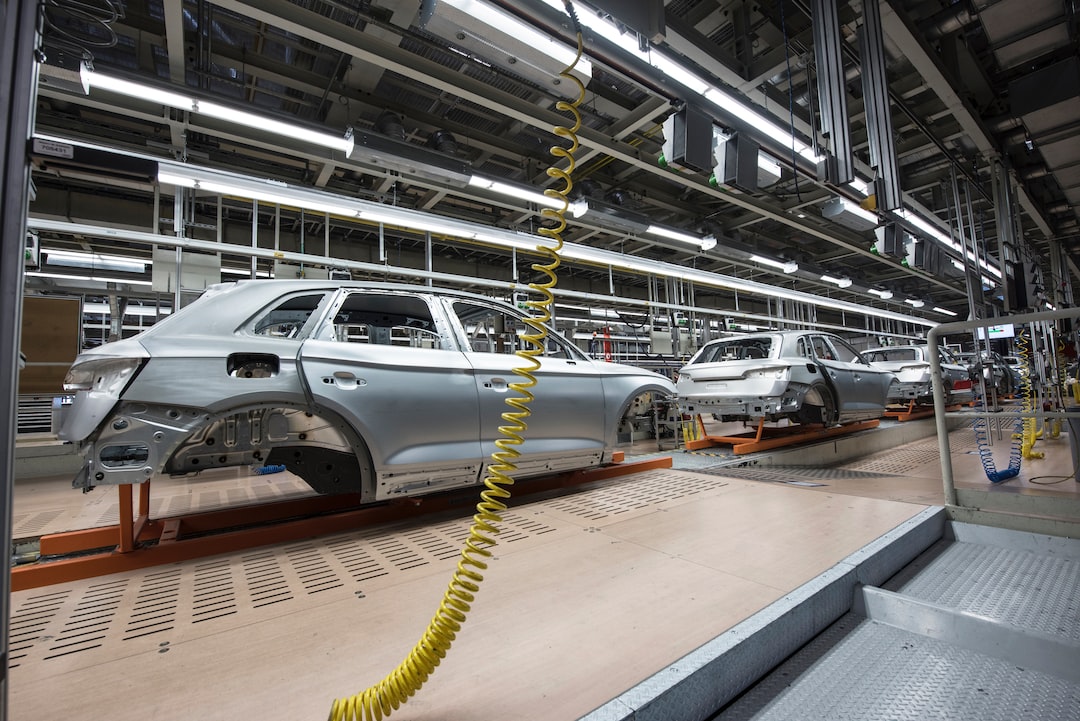