Article
Understanding the Cost of Quality
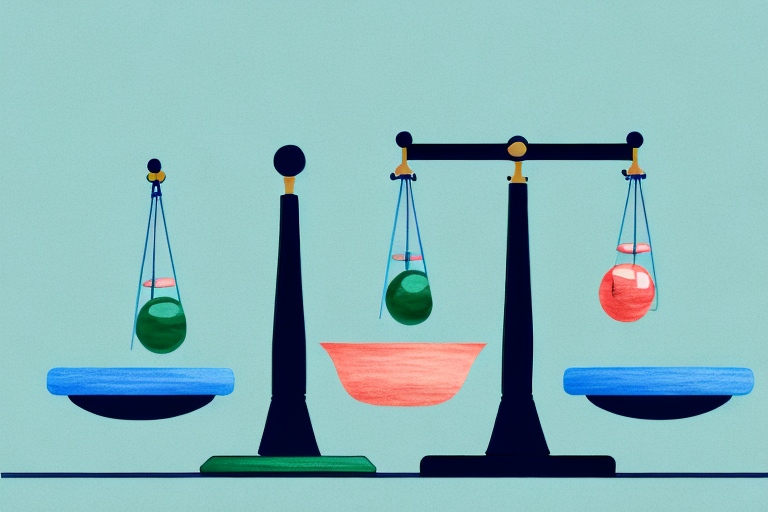
Quality is an integral aspect of any successful business. Ensuring that products and services consistently meet or exceed customer expectations is crucial for long-term growth and sustainability. However, achieving and maintaining high-quality standards comes at a cost. In this article, we will explore the various components and implications of the cost of quality in business.
Defining Quality in Business
Before delving into the intricacies of quality cost, let's first establish a clear definition of what quality means in a business context. Quality goes beyond simply meeting minimum requirements. It encompasses factors such as reliability, durability, performance, and customer satisfaction. Quality is about delivering products and services that exceed customer expectations and create value.
When businesses prioritize and consistently deliver high-quality products and services, they not only gain the trust and loyalty of customers but also enhance their reputation in the market. This can lead to increased customer retention, new business opportunities, and a competitive edge.
Let's explore further the role of quality in business success.
The Role of Quality in Business Success
Quality plays a pivotal role in the overall success of a business. It impacts customer satisfaction, brand reputation, and the bottom line. When businesses prioritize quality in their operations, they can achieve several benefits:
- Higher customer satisfaction: High-quality products and services meet customer needs and exceed expectations, leading to increased customer satisfaction and loyalty.
- Strong brand reputation: Consistently delivering quality products and services helps build a positive brand image, which can attract new customers and retain existing ones.
- Reduced costs: Investing in quality can help minimize defects, rework, and customer complaints, resulting in cost savings in the long run.
- Operational efficiency: By focusing on quality, businesses can streamline their processes, reduce waste, and improve overall efficiency.
These benefits highlight the importance of quality in driving business success and competitiveness. However, let's delve deeper into the key components of quality that contribute to overall excellence.
Key Components of Quality
Quality in business encompasses several key components that contribute to overall excellence. These include:
1. Product design and development: The process of creating products that meet customer requirements and adhere to quality standards.
Product design and development is a crucial component of quality in business. It involves understanding customer needs, conducting market research, and utilizing innovative techniques to create products that not only meet but exceed customer expectations. By investing in product design and development, businesses can ensure that their offerings are of the highest quality, setting them apart from competitors.
2. Process control: Implementing controls and measures to ensure consistency and reliability in the production process.
Process control is essential for maintaining quality throughout the production process. It involves implementing standardized procedures, monitoring key performance indicators, and conducting regular audits to identify and rectify any deviations. By having robust process control measures in place, businesses can ensure that their products consistently meet the desired quality standards.
3. Supplier management: Selecting and working with reliable suppliers who deliver high-quality materials and components.
Supplier management is a critical aspect of quality in business. By carefully selecting suppliers who share the same commitment to quality, businesses can ensure that they receive high-quality materials and components. Regular supplier evaluations, quality audits, and effective communication channels are essential for maintaining strong relationships with suppliers and ensuring the consistent delivery of quality inputs.
4. Quality assurance: Conducting inspections, tests, and checks to ensure that products and services meet specified quality standards.
Quality assurance is the process of systematically checking and verifying that products and services meet the specified quality standards. This involves conducting inspections, tests, and checks at various stages of the production process to identify any deviations or non-conformities. By implementing robust quality assurance measures, businesses can ensure that their products and services consistently meet the highest quality standards.
5. Customer feedback and support: Listening to customer feedback, addressing concerns, and providing excellent customer support to enhance satisfaction.
Customer feedback and support are integral to maintaining and improving quality in business. By actively listening to customer feedback, whether through surveys, reviews, or direct communication, businesses can gain valuable insights into areas for improvement. Addressing customer concerns promptly and providing excellent customer support not only enhances customer satisfaction but also demonstrates a commitment to quality and continuous improvement.
These key components of quality highlight the multifaceted nature of quality in business. By integrating these components into their operations, businesses can establish a strong foundation for delivering high-quality products and services, ultimately driving their success and growth.
The Concept of Quality Cost
Understanding the cost of quality is vital for businesses seeking to optimize their operations and financial performance. Quality costs refer to the expenses incurred during the various stages of delivering high-quality products and services. It includes both the visible and hidden costs associated with maintaining, improving, and monitoring quality.
Types of Quality Costs
Quality costs can be categorized into four main types:
- Prevention costs: These are the costs incurred to prevent defects or errors from occurring in the first place. It includes activities such as training employees, implementing quality management systems, and conducting preventive maintenance.
- Appraisal costs: These are the costs associated with inspecting, testing, and evaluating products and services to ensure they meet quality standards. Examples include equipment maintenance, inspection processes, and quality audits.
- Internal failure costs: These are the costs incurred when defects are detected before products or services reach the customer. It includes rework, scrap, equipment downtime, and loss of productivity.
- External failure costs: These are the costs incurred when defects are identified by customers. It includes warranty claims, product returns, customer complaints, and loss of reputation.
The Relationship Between Quality and Cost
There is a direct relationship between the level of quality and the cost incurred in delivering it. Poor quality leads to higher costs due to rework, scrap, warranty claims, and customer dissatisfaction. On the other hand, investing in prevention and quality assurance can lead to significant cost savings in the long run.
By adopting a proactive approach to quality, businesses can identify and address potential issues before they escalate. This not only reduces costs but also enhances customer satisfaction and overall business performance.
Measuring the Cost of Quality
Measuring the cost of quality is essential for businesses to gain insights into their quality performance and identify areas for improvement. Effective measurement provides valuable data that can be used to make informed decisions and allocate resources efficiently.
Tools for Measuring Quality Costs
There are various tools and techniques available to measure quality costs, such as:
- Cost of Quality (COQ) reports: These reports provide a breakdown of the different types of quality costs incurred by the business, allowing for analysis and comparison.
- Pareto analysis: This technique helps identify the most significant quality issues that contribute to the majority of quality costs.
- Statistical process control: Using statistical methods to monitor and control the quality of processes, ensuring that they operate within specified limits.
- Customer satisfaction surveys: Gathering feedback directly from customers to assess their satisfaction levels and identify areas for improvement.
The Importance of Accurate Measurement
Accurate measurement of quality costs provides businesses with a realistic picture of their quality performance. It allows them to evaluate the effectiveness of their current quality management practices and make data-driven decisions.
Moreover, accurate measurement enables businesses to allocate resources effectively, prioritize improvement initiatives, and demonstrate the impact of quality on the bottom line.
The Impact of Quality Cost on Business Performance
The cost of quality has a profound impact on business performance, both in the short and long term. Failing to manage quality costs effectively can result in financial losses, customer dissatisfaction, and a damaged reputation. On the other hand, taking proactive measures to reduce quality costs can yield significant benefits.
Case Studies of Quality Cost Impact
Several case studies highlight the impact of quality costs on business performance:
Company A, a manufacturing firm, experienced a significant increase in warranty claims due to a lack of preventive maintenance and poor quality control procedures. As a result, the company incurred substantial external failure costs, lost significant market share, and faced reputational damage. By implementing rigorous quality management practices, including preventive maintenance and thorough inspections, Company A was able to reduce warranty claims, improve customer satisfaction, and regain its competitive edge.
Company B, a service provider, faced recurring customer complaints related to the delivery of its services. After conducting a thorough analysis of quality costs, the company discovered that the majority of issues stemmed from inadequate training and inconsistent processes. By investing in employee training programs, implementing standardized operating procedures, and closely monitoring service quality, Company B was able to significantly reduce customer complaints, improve service delivery, and increase customer retention.
How to Minimize Quality Costs
Minimizing quality costs requires a systematic and proactive approach. Here are some strategies businesses can adopt:
- Invest in prevention: Allocate resources to activities that prevent defects and errors, such as employee training, quality management systems, and preventive maintenance.
- Implement continuous improvement: Foster a culture of continuous improvement, empowering employees to identify and address quality issues at every level of the organization.
- Strengthen supplier relationships: Work closely with suppliers to ensure they meet quality standards and deliver reliable materials and components.
- Listen to customers: Engage with customers, gather feedback, and use their insights to drive improvement initiatives and enhance customer satisfaction.
Strategies for Managing Quality Costs
Managing quality costs requires a comprehensive approach that encompasses the entire organization. Here are some strategies businesses can adopt:
Implementing Quality Management Systems
Quality management systems provide a framework for businesses to establish, monitor, and continuously improve their quality performance. Implementing internationally recognized standards such as ISO 9001 can help businesses streamline their quality processes and ensure consistent adherence to quality standards.
Features of effective quality management systems include:
- Clear quality policy and objectives that align with the organization's overall goals.
- Documented processes and procedures that guide employees in delivering consistent quality.
- Regular internal audits to assess compliance and identify areas for improvement.
- Continuous training and development programs to enhance employee skills and knowledge.
Continuous Improvement in Quality Management
Continuous improvement is a fundamental principle of quality management. By consistently striving for better quality, businesses can uncover inefficiencies, identify opportunities for improvement, and enhance their overall performance.
Key elements of continuous improvement in quality management include:
- Establishing a culture of continuous learning and improvement at all levels of the organization.
- Encouraging employee involvement and empowerment in identifying and addressing quality issues.
- Collecting and analyzing data to identify trends, patterns, and areas for improvement.
- Regularly reviewing and updating quality processes to adapt to changing customer needs and market dynamics.
In conclusion, understanding the cost of quality is essential for businesses seeking to thrive in today's competitive market. Quality is a strategic differentiator that can drive customer satisfaction, enhance brand reputation, and improve overall business performance. By investing in quality and effectively managing quality costs, businesses can position themselves for long-term success and sustainable growth.
Article
Understanding the Cost of Quality
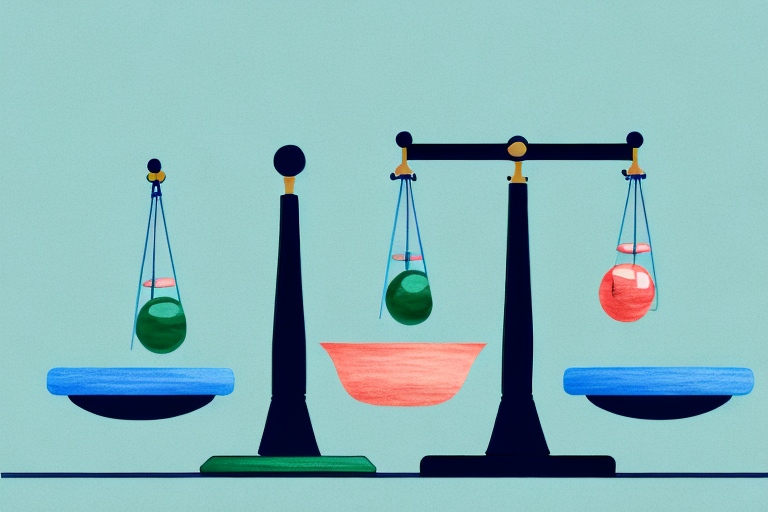
Quality is an integral aspect of any successful business. Ensuring that products and services consistently meet or exceed customer expectations is crucial for long-term growth and sustainability. However, achieving and maintaining high-quality standards comes at a cost. In this article, we will explore the various components and implications of the cost of quality in business.
Defining Quality in Business
Before delving into the intricacies of quality cost, let's first establish a clear definition of what quality means in a business context. Quality goes beyond simply meeting minimum requirements. It encompasses factors such as reliability, durability, performance, and customer satisfaction. Quality is about delivering products and services that exceed customer expectations and create value.
When businesses prioritize and consistently deliver high-quality products and services, they not only gain the trust and loyalty of customers but also enhance their reputation in the market. This can lead to increased customer retention, new business opportunities, and a competitive edge.
Let's explore further the role of quality in business success.
The Role of Quality in Business Success
Quality plays a pivotal role in the overall success of a business. It impacts customer satisfaction, brand reputation, and the bottom line. When businesses prioritize quality in their operations, they can achieve several benefits:
- Higher customer satisfaction: High-quality products and services meet customer needs and exceed expectations, leading to increased customer satisfaction and loyalty.
- Strong brand reputation: Consistently delivering quality products and services helps build a positive brand image, which can attract new customers and retain existing ones.
- Reduced costs: Investing in quality can help minimize defects, rework, and customer complaints, resulting in cost savings in the long run.
- Operational efficiency: By focusing on quality, businesses can streamline their processes, reduce waste, and improve overall efficiency.
These benefits highlight the importance of quality in driving business success and competitiveness. However, let's delve deeper into the key components of quality that contribute to overall excellence.
Key Components of Quality
Quality in business encompasses several key components that contribute to overall excellence. These include:
1. Product design and development: The process of creating products that meet customer requirements and adhere to quality standards.
Product design and development is a crucial component of quality in business. It involves understanding customer needs, conducting market research, and utilizing innovative techniques to create products that not only meet but exceed customer expectations. By investing in product design and development, businesses can ensure that their offerings are of the highest quality, setting them apart from competitors.
2. Process control: Implementing controls and measures to ensure consistency and reliability in the production process.
Process control is essential for maintaining quality throughout the production process. It involves implementing standardized procedures, monitoring key performance indicators, and conducting regular audits to identify and rectify any deviations. By having robust process control measures in place, businesses can ensure that their products consistently meet the desired quality standards.
3. Supplier management: Selecting and working with reliable suppliers who deliver high-quality materials and components.
Supplier management is a critical aspect of quality in business. By carefully selecting suppliers who share the same commitment to quality, businesses can ensure that they receive high-quality materials and components. Regular supplier evaluations, quality audits, and effective communication channels are essential for maintaining strong relationships with suppliers and ensuring the consistent delivery of quality inputs.
4. Quality assurance: Conducting inspections, tests, and checks to ensure that products and services meet specified quality standards.
Quality assurance is the process of systematically checking and verifying that products and services meet the specified quality standards. This involves conducting inspections, tests, and checks at various stages of the production process to identify any deviations or non-conformities. By implementing robust quality assurance measures, businesses can ensure that their products and services consistently meet the highest quality standards.
5. Customer feedback and support: Listening to customer feedback, addressing concerns, and providing excellent customer support to enhance satisfaction.
Customer feedback and support are integral to maintaining and improving quality in business. By actively listening to customer feedback, whether through surveys, reviews, or direct communication, businesses can gain valuable insights into areas for improvement. Addressing customer concerns promptly and providing excellent customer support not only enhances customer satisfaction but also demonstrates a commitment to quality and continuous improvement.
These key components of quality highlight the multifaceted nature of quality in business. By integrating these components into their operations, businesses can establish a strong foundation for delivering high-quality products and services, ultimately driving their success and growth.
The Concept of Quality Cost
Understanding the cost of quality is vital for businesses seeking to optimize their operations and financial performance. Quality costs refer to the expenses incurred during the various stages of delivering high-quality products and services. It includes both the visible and hidden costs associated with maintaining, improving, and monitoring quality.
Types of Quality Costs
Quality costs can be categorized into four main types:
- Prevention costs: These are the costs incurred to prevent defects or errors from occurring in the first place. It includes activities such as training employees, implementing quality management systems, and conducting preventive maintenance.
- Appraisal costs: These are the costs associated with inspecting, testing, and evaluating products and services to ensure they meet quality standards. Examples include equipment maintenance, inspection processes, and quality audits.
- Internal failure costs: These are the costs incurred when defects are detected before products or services reach the customer. It includes rework, scrap, equipment downtime, and loss of productivity.
- External failure costs: These are the costs incurred when defects are identified by customers. It includes warranty claims, product returns, customer complaints, and loss of reputation.
The Relationship Between Quality and Cost
There is a direct relationship between the level of quality and the cost incurred in delivering it. Poor quality leads to higher costs due to rework, scrap, warranty claims, and customer dissatisfaction. On the other hand, investing in prevention and quality assurance can lead to significant cost savings in the long run.
By adopting a proactive approach to quality, businesses can identify and address potential issues before they escalate. This not only reduces costs but also enhances customer satisfaction and overall business performance.
Measuring the Cost of Quality
Measuring the cost of quality is essential for businesses to gain insights into their quality performance and identify areas for improvement. Effective measurement provides valuable data that can be used to make informed decisions and allocate resources efficiently.
Tools for Measuring Quality Costs
There are various tools and techniques available to measure quality costs, such as:
- Cost of Quality (COQ) reports: These reports provide a breakdown of the different types of quality costs incurred by the business, allowing for analysis and comparison.
- Pareto analysis: This technique helps identify the most significant quality issues that contribute to the majority of quality costs.
- Statistical process control: Using statistical methods to monitor and control the quality of processes, ensuring that they operate within specified limits.
- Customer satisfaction surveys: Gathering feedback directly from customers to assess their satisfaction levels and identify areas for improvement.
The Importance of Accurate Measurement
Accurate measurement of quality costs provides businesses with a realistic picture of their quality performance. It allows them to evaluate the effectiveness of their current quality management practices and make data-driven decisions.
Moreover, accurate measurement enables businesses to allocate resources effectively, prioritize improvement initiatives, and demonstrate the impact of quality on the bottom line.
The Impact of Quality Cost on Business Performance
The cost of quality has a profound impact on business performance, both in the short and long term. Failing to manage quality costs effectively can result in financial losses, customer dissatisfaction, and a damaged reputation. On the other hand, taking proactive measures to reduce quality costs can yield significant benefits.
Case Studies of Quality Cost Impact
Several case studies highlight the impact of quality costs on business performance:
Company A, a manufacturing firm, experienced a significant increase in warranty claims due to a lack of preventive maintenance and poor quality control procedures. As a result, the company incurred substantial external failure costs, lost significant market share, and faced reputational damage. By implementing rigorous quality management practices, including preventive maintenance and thorough inspections, Company A was able to reduce warranty claims, improve customer satisfaction, and regain its competitive edge.
Company B, a service provider, faced recurring customer complaints related to the delivery of its services. After conducting a thorough analysis of quality costs, the company discovered that the majority of issues stemmed from inadequate training and inconsistent processes. By investing in employee training programs, implementing standardized operating procedures, and closely monitoring service quality, Company B was able to significantly reduce customer complaints, improve service delivery, and increase customer retention.
How to Minimize Quality Costs
Minimizing quality costs requires a systematic and proactive approach. Here are some strategies businesses can adopt:
- Invest in prevention: Allocate resources to activities that prevent defects and errors, such as employee training, quality management systems, and preventive maintenance.
- Implement continuous improvement: Foster a culture of continuous improvement, empowering employees to identify and address quality issues at every level of the organization.
- Strengthen supplier relationships: Work closely with suppliers to ensure they meet quality standards and deliver reliable materials and components.
- Listen to customers: Engage with customers, gather feedback, and use their insights to drive improvement initiatives and enhance customer satisfaction.
Strategies for Managing Quality Costs
Managing quality costs requires a comprehensive approach that encompasses the entire organization. Here are some strategies businesses can adopt:
Implementing Quality Management Systems
Quality management systems provide a framework for businesses to establish, monitor, and continuously improve their quality performance. Implementing internationally recognized standards such as ISO 9001 can help businesses streamline their quality processes and ensure consistent adherence to quality standards.
Features of effective quality management systems include:
- Clear quality policy and objectives that align with the organization's overall goals.
- Documented processes and procedures that guide employees in delivering consistent quality.
- Regular internal audits to assess compliance and identify areas for improvement.
- Continuous training and development programs to enhance employee skills and knowledge.
Continuous Improvement in Quality Management
Continuous improvement is a fundamental principle of quality management. By consistently striving for better quality, businesses can uncover inefficiencies, identify opportunities for improvement, and enhance their overall performance.
Key elements of continuous improvement in quality management include:
- Establishing a culture of continuous learning and improvement at all levels of the organization.
- Encouraging employee involvement and empowerment in identifying and addressing quality issues.
- Collecting and analyzing data to identify trends, patterns, and areas for improvement.
- Regularly reviewing and updating quality processes to adapt to changing customer needs and market dynamics.
In conclusion, understanding the cost of quality is essential for businesses seeking to thrive in today's competitive market. Quality is a strategic differentiator that can drive customer satisfaction, enhance brand reputation, and improve overall business performance. By investing in quality and effectively managing quality costs, businesses can position themselves for long-term success and sustainable growth.
Article
Understanding the Cost of Quality
•
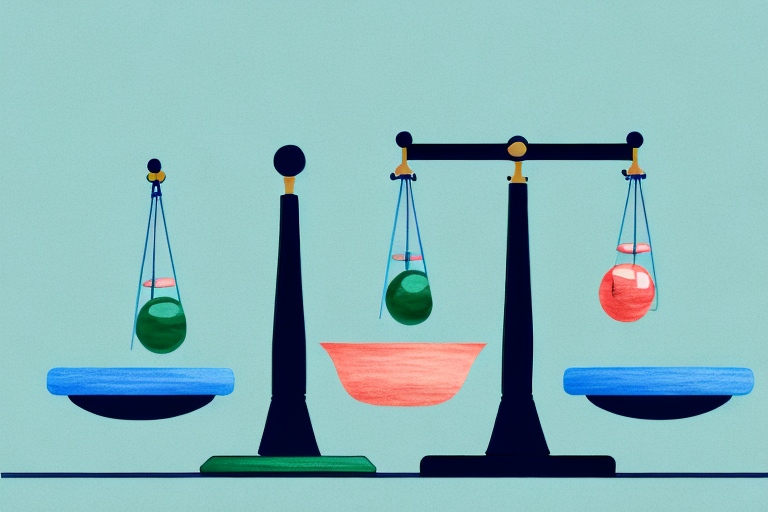