Article
Standard Operating Procedure for Loading and Unloading Containers
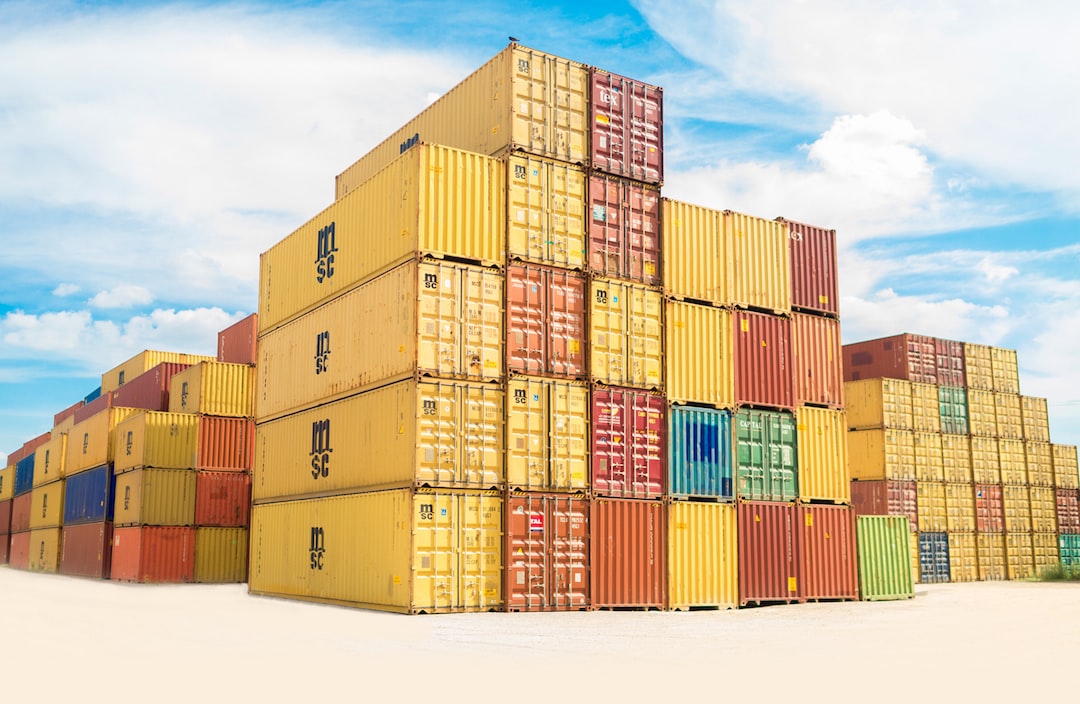
In the field of logistics, it is crucial to have a well-defined standard operating procedure for loading and unloading containers. In this article, we'll look at the complexities of unloading containers and strategies to improve productivity while reducing risk.
We'll begin by discussing why having a proper SOP is essential for any business that deals with containerized cargo. We'll then delve into the details of what should be incorporated in a standard operating procedure for loading and unloading containers and how to apply it proficiently.
Next, we'll take a closer look at the actual unloading process itself - from preparing for arrival to inspecting goods and handling damaged items. We'll examine best practices for organizing teams and equipment as well as strategies for dealing with unexpected challenges that may arise during unloading.
Finally, we will touch on some key considerations when loading containers back up after they've been unloaded. This often-overlooked aspect of container management can have significant implications down the line if not handled correctly.
By following these guidelines and implementing effective procedures throughout your organization's supply chain, you can ensure that your business runs smoothly while keeping costs low and minimizing risk.
Importance of Standard Operating Procedure for Loading and Unloading Containers
Having a standard operating procedure (SOP) in place is key for successful container loading and unloading, guaranteeing safety, compliance, and consistency. A standard operating procedure for loading and unloading containers ensures that everyone involved in the process understands their role and knows how to safely complete their tasks. It also allows supervisors to easily track employee performance and ensure all steps are completed correctly.
The first step of any successful standard operating procedure for loading and unloading containers is performing an inspection. This should include checking the cargo area for any potential hazards such as broken glass or sharp objects that could injure workers during the handling process. Additionally, staff members should be wearing appropriate protective gear such as hard hats and steel-toed boots when working around containers.
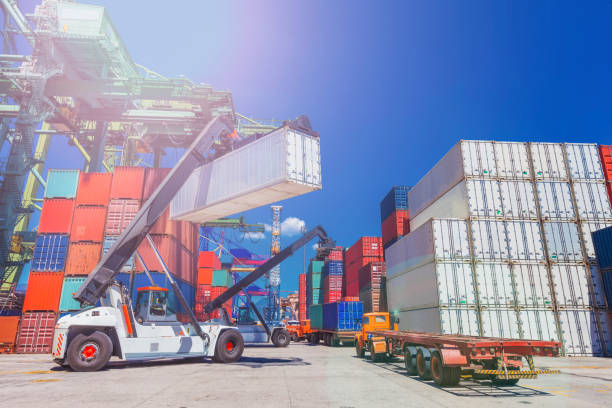
Another important factor to consider when creating a standard operating procedure for loading and unloading containers is chemical exposure risks associated with post-production off-gassing from certain types of cargo shipments like plastics or chemicals stored in tanks or drums. To mitigate this risk, employees must wear respirators approved by OSHA while working with these materials inside a containerized environment. Ventilation must be in place to allow for noxious fumes to exit the building, rather than lingering and potentially creating health issues over time.
Finally, supervisors need to make sure there are clear guidelines on how long containers may remain at a facility. Storage fees are imposed by port authorities if containers are left unattended for too long. Negligence or ignorance of regulations governing international shipping processes could lead companies into legal trouble down the road, so it is important for them to take these matters seriously from day one.
The significance of a set protocol for packing and unloading receptacles is paramount, as it ensures the safety of staff and machinery while also facilitating an effective workflow. As such, thorough inspection procedures should always take place before any containers are loaded or unloaded to guarantee their contents remain intact throughout the process.
Inspection Procedures Before Loading Containers
Ensuring the correct packaging of goods is integral to shipping. Before items are loaded onto a container, they must be inspected to ensure the right items have been shipped. To do this, it’s essential to have an SOP in place for inspecting goods.
Before any shipment is loaded, the packer should inspect all packaging and contents for damage. The packer should also keep an eye out for any hazardous material, such as gasoline, which could cause serious harm if not properly contained.
After receiving each shipment, you must physically verify its contents against the inventory sheet. Any discrepancies should be noted and reported to the shipping company immediately. Labels should also be inspected for accuracy and correct information as incorrectly labeled shipments can lead to hazardous mix-ups when being unloaded at your destination.
Inspectors must then ensure that the packing methods used comply with industry standards such as ISO 6346 (container identification). Mishaps in packing can result in damaged goods due to shifting during transit. This includes overloading containers without proper support or failing to secure loose objects in containers using straps, shrink wrap plastic sheets/bags for larger items like furniture and appliances, etc.
Prior to loading, it is critical to assess the container and its contents for any hazardous materials. Inspecting for any indications of harm or flaws that could potentially jeopardize personnel during the procedure is also important. To properly handle containers during loading/unloading operations, one must be aware of their weight limits and observe proper safety protocols.
Handling Procedures During Container Loading/Unloading Operations
When loading or unloading containers, it’s essential that safety is a top priority. All employees should be properly trained, and aware of all hazards. Forklifts should only be used by qualified individuals, and only in approved areas.
When packing items into vehicles or trailers, it is important to make sure that they do not exceed the load capacity and weight limits specified by the manufacturers. It is also essential that any hazardous items are properly labeled and marked as such prior to being loaded into the containers.
Operating heavy machinery, such as forklifts, requires a high degree of skill, especially when dealing with heavy loads. For this reason, employers often put strict safety protocols in place, such as mandating the use of protective equipment like helmets, and work shoes.
It is imperative for employees to receive proper training on the safe handling of hazardous materials found in freight containers before embarking on any tasks related to it. This will ensure any unforeseen situations are avoided, and that adequate preparations have been made beforehand.
It is critical to adhere to standard operating procedure for loading and unloading containers. To further enhance safety in this process, proper training for forklift drivers must be implemented before allowing them to operate machinery involved in container loading/unloading operations.
Forklift Driver Requirements for Safe Container Loading/Unloading
Forklift operators are essential to the safe and efficient loading/unloading of containers in warehouse settings. It is imperative that employers verify their drivers have valid licenses, as well as competency verification prior to operating a forklift or truck. Furthermore, it is important for supervisors to conduct regular consultations with drivers regarding proper un/loading procedures.
When using a forklift to load a container onto the back of a truck, it's important to make sure the weight is evenly distributed throughout the four sides of the box. This ensures that the container won't tip over during transport. It's also important to check both sides of the box for clearance before putting it onto the back of the vehicle.
Always be aware of your surroundings when operating heavy machinery in small spaces. This includes always being aware of your blind spot when backing, and never exceeding the speed limit in areas where there are people present.
Forklift drivers must ensure that all safety protocols are followed when loading and unloading containers, to prevent any potential accidents. It is equally important for workers to wear the proper protective gear while working around containers in order to maintain a safe environment.
Protective Gear Requirements When Working Around Containers
When working in or around a container, it’s important to wear the proper safety gear. This should include a hard hat and steel-toe work boot to protect from any potential hazards or injuries.
A hard hat is essential to protect against falling objects and hazardous materials. A sturdy pair of steel-toe boots are recommended for extra protection when loading or unloading freight.
Businesses should adhere strictly to inspection procedures and standard operating procedure for loading and unloading containers. Workers must also be equipped with specialized respiratory equipment before handling any chemicals that may be found in shipping container cargo. This will help safeguard employees from potential hazards associated with working around containers.
Wearing protective equipment is imperative when in the vicinity of containers, and it's essential to be aware of potential post-production emissions risks to guarantee safety. Therefore, understanding chemical exposure risks should be a priority for any business involved in loading or unloading containers.
Chemical Exposure Risks Associated With Post-Production Off-Gassing
When offloading shipping containers, the hazards of post-production off-gassing must be considered. This is especially the case when handling the empty container on the site as high concentrations of fumes can pose a threat to the environment and to employees. To mitigate this risk, you should have an SOP for safely removing the shipping container.
Before entering the shipping container, inspect the outside for damage, such as dents or holes, and measure the air quality. Wear appropriate PPE, such as facemasks and gloves, and limit access to the only people who need it.
In addition to the SOP for safe container offloading, there are other steps your company should take to minimize exposure to hazardous chemicals. These include ensuring all ventilation and exhaust systems are functioning properly, and conducting regular inspections of all loading and unloading machinery. Also, be sure to train your employees in how to appropriately handle and dispose of dangerous materials.
Finally, if possible they should use alternatives such as dry ice blasting instead of fumigation whenever possible due to its lower environmental impact compared with traditional methods like using pesticides or insecticides inside shipping containers.
Conclusion
Creating a standard operating procedure for loading and unloading containers is vital to guarantee the security of all personnel involved in container operations. These processes help companies avoid mistakes, keep workers safe, and protect their materials from damage. Taking the time to develop and document an effective SOP can help your business stay organized and ensure everyone follows safe practices when dealing with containers on-site.
Sign up now for a free 7-day trial with Trainual and scale your business!
Article
Standard Operating Procedure for Loading and Unloading Containers
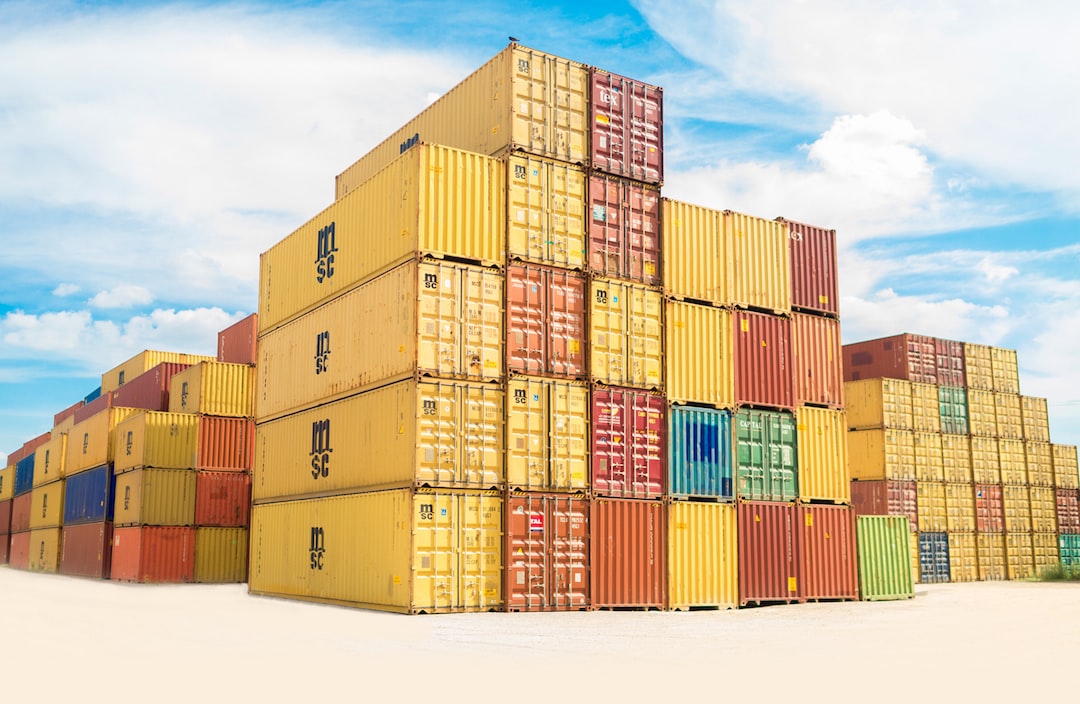
Jump to a section
- Importance of Standard Operating Procedure for Loading and Unloading Containers
- Inspection Procedures Before Loading Containers
- Handling Procedures During Container Loading/Unloading Operations
- Forklift Driver Requirements for Safe Container Loading/Unloading
- Protective Gear Requirements When Working Around Containers
- Chemical Exposure Risks Associated With Post-Production Off-Gassing
- Conclusion
In the field of logistics, it is crucial to have a well-defined standard operating procedure for loading and unloading containers. In this article, we'll look at the complexities of unloading containers and strategies to improve productivity while reducing risk.
We'll begin by discussing why having a proper SOP is essential for any business that deals with containerized cargo. We'll then delve into the details of what should be incorporated in a standard operating procedure for loading and unloading containers and how to apply it proficiently.
Next, we'll take a closer look at the actual unloading process itself - from preparing for arrival to inspecting goods and handling damaged items. We'll examine best practices for organizing teams and equipment as well as strategies for dealing with unexpected challenges that may arise during unloading.
Finally, we will touch on some key considerations when loading containers back up after they've been unloaded. This often-overlooked aspect of container management can have significant implications down the line if not handled correctly.
By following these guidelines and implementing effective procedures throughout your organization's supply chain, you can ensure that your business runs smoothly while keeping costs low and minimizing risk.
Importance of Standard Operating Procedure for Loading and Unloading Containers
Having a standard operating procedure (SOP) in place is key for successful container loading and unloading, guaranteeing safety, compliance, and consistency. A standard operating procedure for loading and unloading containers ensures that everyone involved in the process understands their role and knows how to safely complete their tasks. It also allows supervisors to easily track employee performance and ensure all steps are completed correctly.
The first step of any successful standard operating procedure for loading and unloading containers is performing an inspection. This should include checking the cargo area for any potential hazards such as broken glass or sharp objects that could injure workers during the handling process. Additionally, staff members should be wearing appropriate protective gear such as hard hats and steel-toed boots when working around containers.
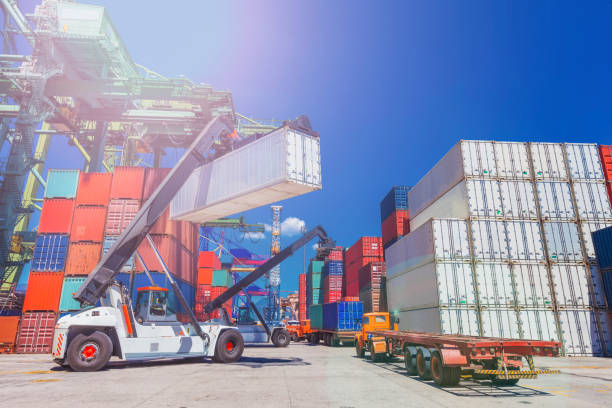
Another important factor to consider when creating a standard operating procedure for loading and unloading containers is chemical exposure risks associated with post-production off-gassing from certain types of cargo shipments like plastics or chemicals stored in tanks or drums. To mitigate this risk, employees must wear respirators approved by OSHA while working with these materials inside a containerized environment. Ventilation must be in place to allow for noxious fumes to exit the building, rather than lingering and potentially creating health issues over time.
Finally, supervisors need to make sure there are clear guidelines on how long containers may remain at a facility. Storage fees are imposed by port authorities if containers are left unattended for too long. Negligence or ignorance of regulations governing international shipping processes could lead companies into legal trouble down the road, so it is important for them to take these matters seriously from day one.
The significance of a set protocol for packing and unloading receptacles is paramount, as it ensures the safety of staff and machinery while also facilitating an effective workflow. As such, thorough inspection procedures should always take place before any containers are loaded or unloaded to guarantee their contents remain intact throughout the process.
Inspection Procedures Before Loading Containers
Ensuring the correct packaging of goods is integral to shipping. Before items are loaded onto a container, they must be inspected to ensure the right items have been shipped. To do this, it’s essential to have an SOP in place for inspecting goods.
Before any shipment is loaded, the packer should inspect all packaging and contents for damage. The packer should also keep an eye out for any hazardous material, such as gasoline, which could cause serious harm if not properly contained.
After receiving each shipment, you must physically verify its contents against the inventory sheet. Any discrepancies should be noted and reported to the shipping company immediately. Labels should also be inspected for accuracy and correct information as incorrectly labeled shipments can lead to hazardous mix-ups when being unloaded at your destination.
Inspectors must then ensure that the packing methods used comply with industry standards such as ISO 6346 (container identification). Mishaps in packing can result in damaged goods due to shifting during transit. This includes overloading containers without proper support or failing to secure loose objects in containers using straps, shrink wrap plastic sheets/bags for larger items like furniture and appliances, etc.
Prior to loading, it is critical to assess the container and its contents for any hazardous materials. Inspecting for any indications of harm or flaws that could potentially jeopardize personnel during the procedure is also important. To properly handle containers during loading/unloading operations, one must be aware of their weight limits and observe proper safety protocols.
Handling Procedures During Container Loading/Unloading Operations
When loading or unloading containers, it’s essential that safety is a top priority. All employees should be properly trained, and aware of all hazards. Forklifts should only be used by qualified individuals, and only in approved areas.
When packing items into vehicles or trailers, it is important to make sure that they do not exceed the load capacity and weight limits specified by the manufacturers. It is also essential that any hazardous items are properly labeled and marked as such prior to being loaded into the containers.
Operating heavy machinery, such as forklifts, requires a high degree of skill, especially when dealing with heavy loads. For this reason, employers often put strict safety protocols in place, such as mandating the use of protective equipment like helmets, and work shoes.
It is imperative for employees to receive proper training on the safe handling of hazardous materials found in freight containers before embarking on any tasks related to it. This will ensure any unforeseen situations are avoided, and that adequate preparations have been made beforehand.
It is critical to adhere to standard operating procedure for loading and unloading containers. To further enhance safety in this process, proper training for forklift drivers must be implemented before allowing them to operate machinery involved in container loading/unloading operations.
Forklift Driver Requirements for Safe Container Loading/Unloading
Forklift operators are essential to the safe and efficient loading/unloading of containers in warehouse settings. It is imperative that employers verify their drivers have valid licenses, as well as competency verification prior to operating a forklift or truck. Furthermore, it is important for supervisors to conduct regular consultations with drivers regarding proper un/loading procedures.
When using a forklift to load a container onto the back of a truck, it's important to make sure the weight is evenly distributed throughout the four sides of the box. This ensures that the container won't tip over during transport. It's also important to check both sides of the box for clearance before putting it onto the back of the vehicle.
Always be aware of your surroundings when operating heavy machinery in small spaces. This includes always being aware of your blind spot when backing, and never exceeding the speed limit in areas where there are people present.
Forklift drivers must ensure that all safety protocols are followed when loading and unloading containers, to prevent any potential accidents. It is equally important for workers to wear the proper protective gear while working around containers in order to maintain a safe environment.
Protective Gear Requirements When Working Around Containers
When working in or around a container, it’s important to wear the proper safety gear. This should include a hard hat and steel-toe work boot to protect from any potential hazards or injuries.
A hard hat is essential to protect against falling objects and hazardous materials. A sturdy pair of steel-toe boots are recommended for extra protection when loading or unloading freight.
Businesses should adhere strictly to inspection procedures and standard operating procedure for loading and unloading containers. Workers must also be equipped with specialized respiratory equipment before handling any chemicals that may be found in shipping container cargo. This will help safeguard employees from potential hazards associated with working around containers.
Wearing protective equipment is imperative when in the vicinity of containers, and it's essential to be aware of potential post-production emissions risks to guarantee safety. Therefore, understanding chemical exposure risks should be a priority for any business involved in loading or unloading containers.
Chemical Exposure Risks Associated With Post-Production Off-Gassing
When offloading shipping containers, the hazards of post-production off-gassing must be considered. This is especially the case when handling the empty container on the site as high concentrations of fumes can pose a threat to the environment and to employees. To mitigate this risk, you should have an SOP for safely removing the shipping container.
Before entering the shipping container, inspect the outside for damage, such as dents or holes, and measure the air quality. Wear appropriate PPE, such as facemasks and gloves, and limit access to the only people who need it.
In addition to the SOP for safe container offloading, there are other steps your company should take to minimize exposure to hazardous chemicals. These include ensuring all ventilation and exhaust systems are functioning properly, and conducting regular inspections of all loading and unloading machinery. Also, be sure to train your employees in how to appropriately handle and dispose of dangerous materials.
Finally, if possible they should use alternatives such as dry ice blasting instead of fumigation whenever possible due to its lower environmental impact compared with traditional methods like using pesticides or insecticides inside shipping containers.
Conclusion
Creating a standard operating procedure for loading and unloading containers is vital to guarantee the security of all personnel involved in container operations. These processes help companies avoid mistakes, keep workers safe, and protect their materials from damage. Taking the time to develop and document an effective SOP can help your business stay organized and ensure everyone follows safe practices when dealing with containers on-site.
Sign up now for a free 7-day trial with Trainual and scale your business!
Article
Standard Operating Procedure for Loading and Unloading Containers
•
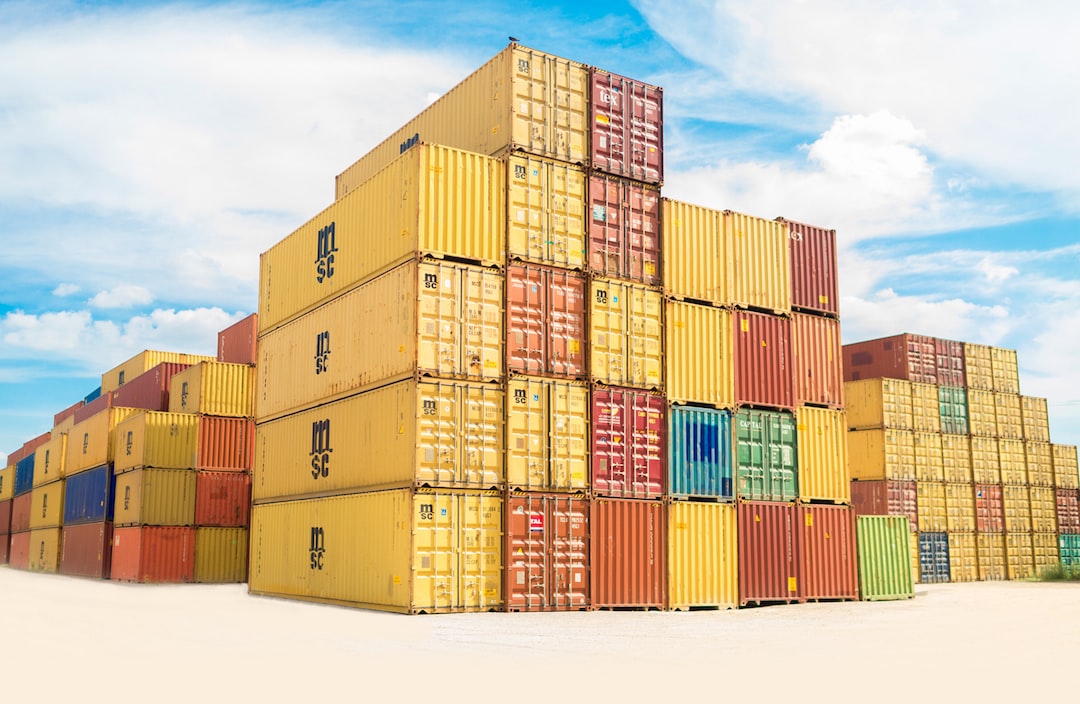