Article
Comparing Push and Pull Manufacturing Strategies
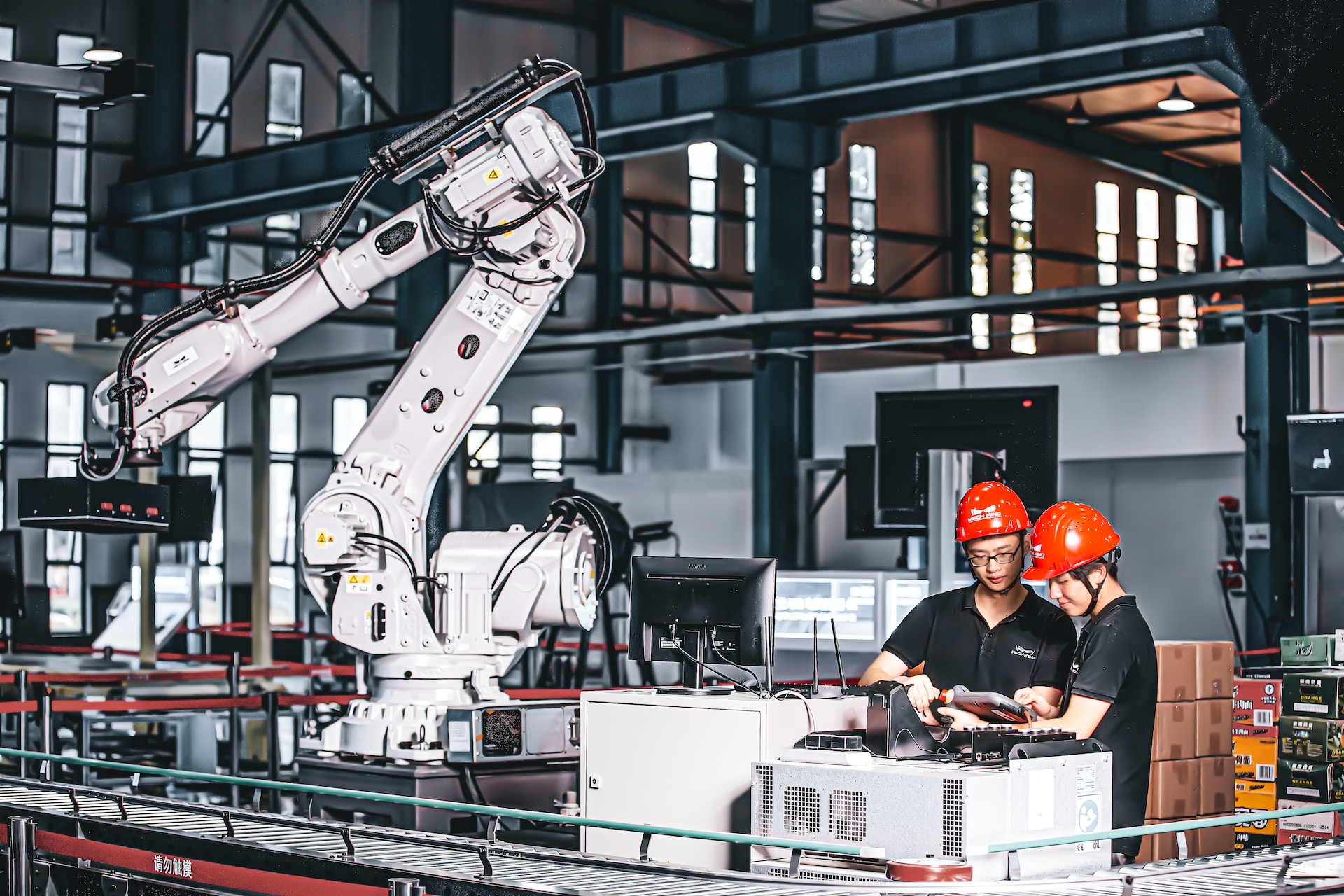
In the realm of manufacturing, there are two significant approaches: push and pull strategies. These strategies dictate how companies manage their production processes and respond to customer demand. Understanding the key differences between push and pull manufacturing is crucial for businesses aiming to optimize their supply chain efficiency and ultimately drive profitability.
Understanding Push Manufacturing Strategy
At its core, push manufacturing is a strategy driven by forecasts and predictions. In a push system, production is initiated based on estimated customer demand. The main goal is to manufacture goods in advance and have them ready for distribution.
Push manufacturing is a widely used approach in various industries, including automotive, electronics, and consumer goods. It allows companies to streamline their production processes and ensure a steady supply of products to meet customer demand.
Defining Push Manufacturing
Push manufacturing revolves around a centralized planning system that coordinates the production activities across the entire supply chain. In this approach, production decisions are made based on forecasts and historical data, often resulting in mass production of goods.
The planning process in push manufacturing involves analyzing market trends, customer preferences, and historical sales data to estimate future demand. This information is then used to determine the quantity of products to be produced and the production schedule.
Key Features of Push Manufacturing
One of the main characteristics of push manufacturing is the emphasis on efficiency and cost reduction. By producing goods in large batches, companies can take advantage of economies of scale. This leads to lower production costs per unit and increased profitability.
Push manufacturing also allows for better resource utilization as production runs continuously, ensuring equipment and labor efficiency. By optimizing production processes and minimizing downtime, companies can maximize their productivity and output.
Another key feature of push manufacturing is the ability to respond quickly to sudden changes in demand. With a surplus of pre-manufactured goods, companies can quickly fulfill orders and minimize lead times, resulting in higher customer satisfaction.
Advantages and Disadvantages of Push Manufacturing
Push manufacturing offers several advantages, including faster production times and reduced lead times. By producing goods in advance, companies can shorten the time it takes to fulfill customer orders, leading to improved customer satisfaction and loyalty.
Furthermore, push manufacturing enables companies to take advantage of volume discounts from suppliers due to the predictability of production needs. By ordering materials and components in bulk, companies can negotiate better prices and reduce overall production costs.
However, one notable drawback of push manufacturing is the risk of overproduction. If demand does not meet the forecasted estimates, companies may end up with high inventories and potential waste. This can lead to increased storage costs and the need for clearance sales or discounts to sell excess inventory.
Additionally, push manufacturing may not be suitable for industries with rapidly changing customer preferences or unpredictable demand patterns. In such cases, a more flexible manufacturing approach, such as pull manufacturing, may be more appropriate.
In conclusion, push manufacturing is a strategy that focuses on producing goods in advance based on forecasts and historical data. It offers advantages such as faster production times and reduced lead times, but also carries the risk of overproduction. Understanding the key features and advantages and disadvantages of push manufacturing can help companies make informed decisions about their production strategies.
Understanding Pull Manufacturing Strategy
In contrast to push manufacturing, the pull strategy relies on actual customer demand to drive production. Rather than making goods in advance, companies using the pull strategy start manufacturing once an order is received.
Implementing a pull manufacturing strategy requires a deep understanding of customer demand patterns and the ability to quickly respond to fluctuations in the market. By aligning production with actual demand, companies can avoid the pitfalls of overproduction and reduce unnecessary inventory holding costs.
Defining Pull Manufacturing
Pull manufacturing is a demand-driven approach that aims to synchronize production with customer demand. This strategy requires companies to have an efficient system in place to monitor and respond to changes in demand promptly.
One of the key aspects of pull manufacturing is the concept of "just-in-time" production. This means that products are manufactured and delivered to customers exactly when they are needed, minimizing the need for excessive inventory and reducing the risk of obsolescence.
Key Features of Pull Manufacturing
The primary characteristic of pull manufacturing is its focus on reducing inventory and waste. By responding directly to customer demand, companies can minimize the risk of overproduction and costly inventory holding. Pull manufacturing also promotes flexibility and customization as products are made according to specific customer orders.
Another important feature of pull manufacturing is the emphasis on continuous improvement. By closely monitoring customer demand and production processes, companies can identify areas for optimization and make necessary adjustments to enhance efficiency and quality.
Advantages and Disadvantages of Pull Manufacturing
Pull manufacturing offers benefits such as lower inventory holding costs and reduced waste. This strategy allows for better customization and adaptation to changing market conditions.
However, challenges may arise in managing lead times, as production starts only when an order is received. This requires careful coordination and efficient communication between different departments and suppliers to ensure timely delivery to customers.
In addition, accurate demand forecasting becomes crucial in pull manufacturing. Companies must have reliable data and forecasting models to anticipate customer needs and adjust production accordingly. Without accurate forecasting, there is a risk of underproduction or delays in fulfilling customer orders.
Furthermore, implementing a pull manufacturing strategy requires a well-established and reliable supply chain. Companies need to have strong relationships with suppliers and ensure a steady flow of raw materials to support production on-demand.
In conclusion, pull manufacturing is a demand-driven strategy that aims to align production with customer demand. By reducing inventory and waste, companies can achieve cost savings and enhance flexibility. However, effective coordination, accurate demand forecasting, and a robust supply chain are essential for successful implementation of pull manufacturing.
Differences Between Push and Pull Manufacturing Strategies
The disparities between push and pull manufacturing strategies go beyond their underlying philosophy. Let's explore some key differences in how these strategies impact various aspects of the manufacturing process.
Production Planning in Push vs Pull
In push manufacturing, production planning relies heavily on forecasts and historical data. The goal is to optimize efficiency and minimize idle time. However, this approach can sometimes lead to overproduction if the forecasts are inaccurate or if there are sudden changes in demand. On the other hand, pull manufacturing focuses on aligning production with actual customer demand. This approach involves constant monitoring of demand signals and adapting production accordingly. By producing only what is needed, companies using the pull strategy can reduce the risk of overproduction and minimize waste.
Furthermore, in push manufacturing, the emphasis is on maximizing the utilization of resources and achieving economies of scale. This often results in large batch sizes and longer production runs. In contrast, pull manufacturing aims to achieve smaller batch sizes and shorter production runs, allowing for more flexibility and responsiveness to changes in customer demand.
Inventory Management in Push vs Pull
Push manufacturing often leads to higher inventory levels to meet anticipated demand. Since production is based on forecasts, companies using this strategy may need to stockpile finished goods in warehouses or distribution centers. This can tie up a significant amount of capital and increase the risk of inventory obsolescence.
On the other hand, pull manufacturing strives to maintain minimal inventory levels by producing based on actual orders. By reducing inventory, companies using the pull strategy can minimize holding costs and the risk of obsolescence. This approach requires efficient supply chain management and close collaboration with suppliers to ensure timely delivery of raw materials and components.
Additionally, pull manufacturing allows for better visibility into the demand-supply chain, enabling companies to identify and address bottlenecks or disruptions more effectively. This can lead to improved overall supply chain performance and reduced lead times.
Customer Demand Response in Push vs Pull
In push manufacturing, customer demand response is predetermined through forecasts. This approach may lead to reduced flexibility in meeting unexpected demands or sudden shifts in market preferences. Companies using the push strategy may find it challenging to quickly adjust production levels or introduce new product variants.
In contrast, pull manufacturing allows companies to quickly respond to changes in customer demand, offering more agile and customer-centric operations. By closely monitoring demand signals and adjusting production accordingly, companies using the pull strategy can better meet customer expectations and reduce the risk of stockouts or excess inventory.
Furthermore, pull manufacturing enables companies to implement just-in-time (JIT) manufacturing principles, where products are produced and delivered to customers exactly when needed. This can result in shorter lead times, reduced order cycle times, and improved customer satisfaction.
Moreover, pull manufacturing encourages closer collaboration and communication between manufacturers and customers. By involving customers in the production process, companies can gain valuable insights and feedback, leading to continuous product improvement and innovation.
Choosing the Right Manufacturing Strategy
Deciding which manufacturing strategy to adopt requires careful consideration of various factors. Here are some key aspects to evaluate:
Manufacturing strategy plays a pivotal role in the success of a company. It determines how products are produced, how resources are allocated, and ultimately, how efficiently a company operates. By choosing the right manufacturing strategy, businesses can optimize their supply chain, meet customer demands, and drive profitability.
Factors to Consider
Consider factors like market volatility, product characteristics, and customer preferences. Assessing demand variability, lead times, and production capabilities will also help determine the most suitable manufacturing strategy.
Market volatility refers to the degree of uncertainty and fluctuations in the market. It is important to consider this factor because it can greatly impact the demand for products. For example, in a highly volatile market, a push manufacturing strategy may be more appropriate as it allows for a faster response to sudden changes in demand.
Product characteristics also play a significant role in choosing the right manufacturing strategy. Complex products with high customization requirements may benefit from a pull manufacturing strategy, as it allows for greater flexibility and customization. On the other hand, products with standardized features and high demand may be better suited for a push manufacturing strategy.
Customer preferences should not be overlooked when deciding on a manufacturing strategy. Understanding what customers value and how they prefer to receive products can help determine the most effective approach. For instance, if customers value quick delivery and customization, a pull manufacturing strategy that focuses on just-in-time production may be the best choice.
Impact on Supply Chain Efficiency
Push and pull strategies have different implications for supply chain efficiency. Push manufacturing can result in increased inventory and lead times, while pull manufacturing seeks to minimize both. Analyze the strengths and weaknesses of your supply chain and evaluate how each strategy aligns with your goals.
Push manufacturing involves producing goods based on forecasts and pushing them through the supply chain to meet anticipated demand. While this strategy can help ensure product availability, it can also lead to excess inventory and longer lead times. On the other hand, pull manufacturing relies on actual customer demand to trigger production, reducing the risk of excess inventory and minimizing lead times.
Assessing the efficiency of your supply chain is crucial when deciding between push and pull manufacturing strategies. Consider factors such as transportation costs, warehousing capabilities, and supplier relationships. A well-optimized supply chain can support a pull manufacturing strategy by enabling quick response times and minimizing waste.
Role in Business Growth and Profitability
Understanding the impact of manufacturing strategy on overall business growth and profitability is crucial. Consider how each strategy affects production costs, customer satisfaction, and competitiveness in the marketplace.
Production costs are a significant consideration when choosing a manufacturing strategy. Push manufacturing may require higher upfront investments in inventory and production capacity, while pull manufacturing can result in lower inventory costs but higher setup and changeover costs. Analyze your cost structure and evaluate which strategy aligns with your financial goals.
Customer satisfaction is another important factor to consider. A manufacturing strategy that enables quick response times, customization, and on-time delivery can greatly enhance customer satisfaction. By meeting customer demands effectively, businesses can build strong relationships and gain a competitive edge in the marketplace.
Competitiveness in the marketplace is closely tied to the chosen manufacturing strategy. Understanding how each strategy aligns with your competitors' approaches can help you differentiate yourself and stand out. Consider factors such as speed to market, product quality, and flexibility when evaluating the impact on competitiveness.
Choosing between push and pull manufacturing strategies is an important decision that can significantly impact a company's operations. By thoroughly evaluating their respective advantages, disadvantages, and suitability for specific contexts, businesses can enhance supply chain efficiency, meet customer demands, and ultimately drive profitability.
Similar Blog Posts
Article
Comparing Push and Pull Manufacturing Strategies
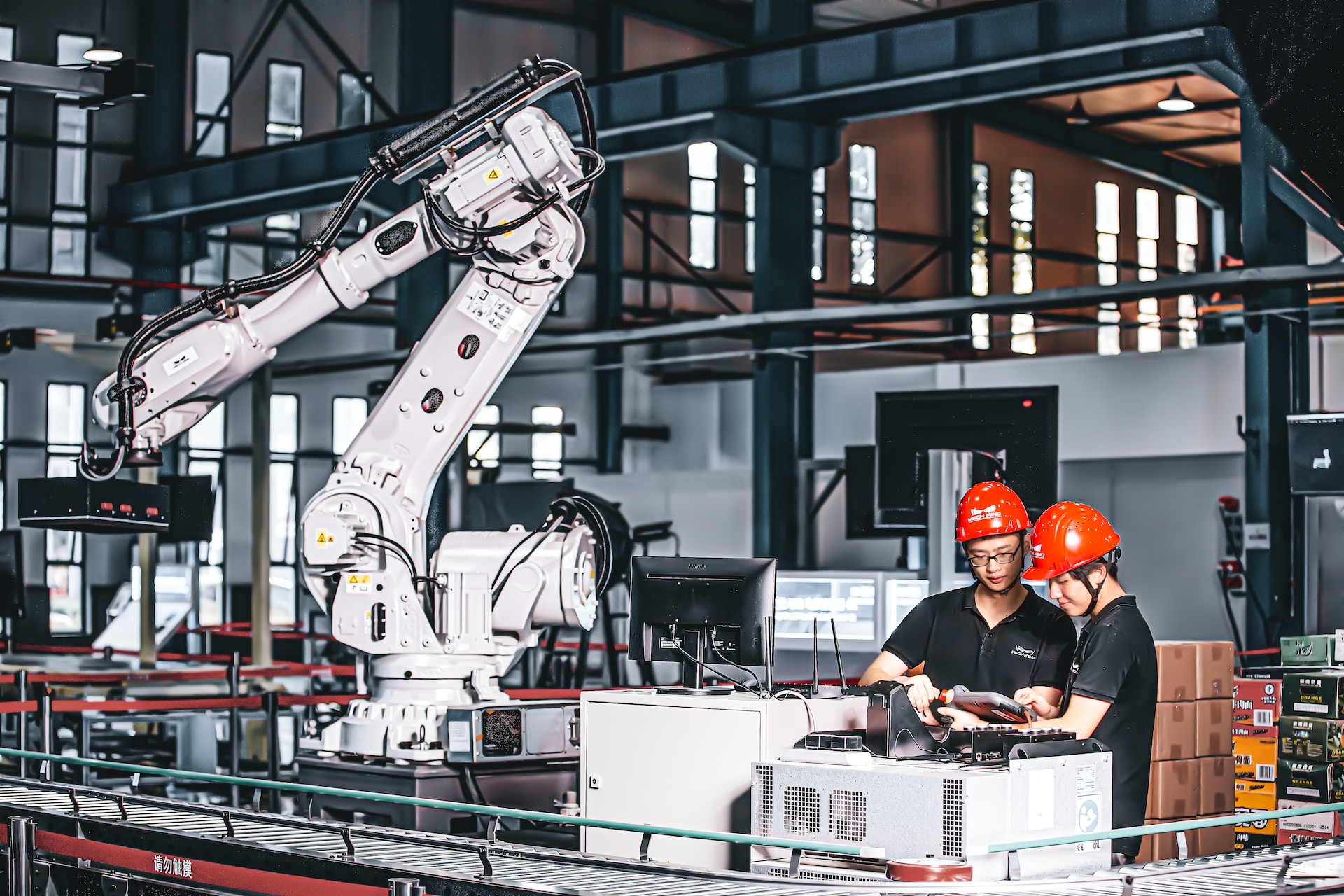
In the realm of manufacturing, there are two significant approaches: push and pull strategies. These strategies dictate how companies manage their production processes and respond to customer demand. Understanding the key differences between push and pull manufacturing is crucial for businesses aiming to optimize their supply chain efficiency and ultimately drive profitability.
Understanding Push Manufacturing Strategy
At its core, push manufacturing is a strategy driven by forecasts and predictions. In a push system, production is initiated based on estimated customer demand. The main goal is to manufacture goods in advance and have them ready for distribution.
Push manufacturing is a widely used approach in various industries, including automotive, electronics, and consumer goods. It allows companies to streamline their production processes and ensure a steady supply of products to meet customer demand.
Defining Push Manufacturing
Push manufacturing revolves around a centralized planning system that coordinates the production activities across the entire supply chain. In this approach, production decisions are made based on forecasts and historical data, often resulting in mass production of goods.
The planning process in push manufacturing involves analyzing market trends, customer preferences, and historical sales data to estimate future demand. This information is then used to determine the quantity of products to be produced and the production schedule.
Key Features of Push Manufacturing
One of the main characteristics of push manufacturing is the emphasis on efficiency and cost reduction. By producing goods in large batches, companies can take advantage of economies of scale. This leads to lower production costs per unit and increased profitability.
Push manufacturing also allows for better resource utilization as production runs continuously, ensuring equipment and labor efficiency. By optimizing production processes and minimizing downtime, companies can maximize their productivity and output.
Another key feature of push manufacturing is the ability to respond quickly to sudden changes in demand. With a surplus of pre-manufactured goods, companies can quickly fulfill orders and minimize lead times, resulting in higher customer satisfaction.
Advantages and Disadvantages of Push Manufacturing
Push manufacturing offers several advantages, including faster production times and reduced lead times. By producing goods in advance, companies can shorten the time it takes to fulfill customer orders, leading to improved customer satisfaction and loyalty.
Furthermore, push manufacturing enables companies to take advantage of volume discounts from suppliers due to the predictability of production needs. By ordering materials and components in bulk, companies can negotiate better prices and reduce overall production costs.
However, one notable drawback of push manufacturing is the risk of overproduction. If demand does not meet the forecasted estimates, companies may end up with high inventories and potential waste. This can lead to increased storage costs and the need for clearance sales or discounts to sell excess inventory.
Additionally, push manufacturing may not be suitable for industries with rapidly changing customer preferences or unpredictable demand patterns. In such cases, a more flexible manufacturing approach, such as pull manufacturing, may be more appropriate.
In conclusion, push manufacturing is a strategy that focuses on producing goods in advance based on forecasts and historical data. It offers advantages such as faster production times and reduced lead times, but also carries the risk of overproduction. Understanding the key features and advantages and disadvantages of push manufacturing can help companies make informed decisions about their production strategies.
Understanding Pull Manufacturing Strategy
In contrast to push manufacturing, the pull strategy relies on actual customer demand to drive production. Rather than making goods in advance, companies using the pull strategy start manufacturing once an order is received.
Implementing a pull manufacturing strategy requires a deep understanding of customer demand patterns and the ability to quickly respond to fluctuations in the market. By aligning production with actual demand, companies can avoid the pitfalls of overproduction and reduce unnecessary inventory holding costs.
Defining Pull Manufacturing
Pull manufacturing is a demand-driven approach that aims to synchronize production with customer demand. This strategy requires companies to have an efficient system in place to monitor and respond to changes in demand promptly.
One of the key aspects of pull manufacturing is the concept of "just-in-time" production. This means that products are manufactured and delivered to customers exactly when they are needed, minimizing the need for excessive inventory and reducing the risk of obsolescence.
Key Features of Pull Manufacturing
The primary characteristic of pull manufacturing is its focus on reducing inventory and waste. By responding directly to customer demand, companies can minimize the risk of overproduction and costly inventory holding. Pull manufacturing also promotes flexibility and customization as products are made according to specific customer orders.
Another important feature of pull manufacturing is the emphasis on continuous improvement. By closely monitoring customer demand and production processes, companies can identify areas for optimization and make necessary adjustments to enhance efficiency and quality.
Advantages and Disadvantages of Pull Manufacturing
Pull manufacturing offers benefits such as lower inventory holding costs and reduced waste. This strategy allows for better customization and adaptation to changing market conditions.
However, challenges may arise in managing lead times, as production starts only when an order is received. This requires careful coordination and efficient communication between different departments and suppliers to ensure timely delivery to customers.
In addition, accurate demand forecasting becomes crucial in pull manufacturing. Companies must have reliable data and forecasting models to anticipate customer needs and adjust production accordingly. Without accurate forecasting, there is a risk of underproduction or delays in fulfilling customer orders.
Furthermore, implementing a pull manufacturing strategy requires a well-established and reliable supply chain. Companies need to have strong relationships with suppliers and ensure a steady flow of raw materials to support production on-demand.
In conclusion, pull manufacturing is a demand-driven strategy that aims to align production with customer demand. By reducing inventory and waste, companies can achieve cost savings and enhance flexibility. However, effective coordination, accurate demand forecasting, and a robust supply chain are essential for successful implementation of pull manufacturing.
Differences Between Push and Pull Manufacturing Strategies
The disparities between push and pull manufacturing strategies go beyond their underlying philosophy. Let's explore some key differences in how these strategies impact various aspects of the manufacturing process.
Production Planning in Push vs Pull
In push manufacturing, production planning relies heavily on forecasts and historical data. The goal is to optimize efficiency and minimize idle time. However, this approach can sometimes lead to overproduction if the forecasts are inaccurate or if there are sudden changes in demand. On the other hand, pull manufacturing focuses on aligning production with actual customer demand. This approach involves constant monitoring of demand signals and adapting production accordingly. By producing only what is needed, companies using the pull strategy can reduce the risk of overproduction and minimize waste.
Furthermore, in push manufacturing, the emphasis is on maximizing the utilization of resources and achieving economies of scale. This often results in large batch sizes and longer production runs. In contrast, pull manufacturing aims to achieve smaller batch sizes and shorter production runs, allowing for more flexibility and responsiveness to changes in customer demand.
Inventory Management in Push vs Pull
Push manufacturing often leads to higher inventory levels to meet anticipated demand. Since production is based on forecasts, companies using this strategy may need to stockpile finished goods in warehouses or distribution centers. This can tie up a significant amount of capital and increase the risk of inventory obsolescence.
On the other hand, pull manufacturing strives to maintain minimal inventory levels by producing based on actual orders. By reducing inventory, companies using the pull strategy can minimize holding costs and the risk of obsolescence. This approach requires efficient supply chain management and close collaboration with suppliers to ensure timely delivery of raw materials and components.
Additionally, pull manufacturing allows for better visibility into the demand-supply chain, enabling companies to identify and address bottlenecks or disruptions more effectively. This can lead to improved overall supply chain performance and reduced lead times.
Customer Demand Response in Push vs Pull
In push manufacturing, customer demand response is predetermined through forecasts. This approach may lead to reduced flexibility in meeting unexpected demands or sudden shifts in market preferences. Companies using the push strategy may find it challenging to quickly adjust production levels or introduce new product variants.
In contrast, pull manufacturing allows companies to quickly respond to changes in customer demand, offering more agile and customer-centric operations. By closely monitoring demand signals and adjusting production accordingly, companies using the pull strategy can better meet customer expectations and reduce the risk of stockouts or excess inventory.
Furthermore, pull manufacturing enables companies to implement just-in-time (JIT) manufacturing principles, where products are produced and delivered to customers exactly when needed. This can result in shorter lead times, reduced order cycle times, and improved customer satisfaction.
Moreover, pull manufacturing encourages closer collaboration and communication between manufacturers and customers. By involving customers in the production process, companies can gain valuable insights and feedback, leading to continuous product improvement and innovation.
Choosing the Right Manufacturing Strategy
Deciding which manufacturing strategy to adopt requires careful consideration of various factors. Here are some key aspects to evaluate:
Manufacturing strategy plays a pivotal role in the success of a company. It determines how products are produced, how resources are allocated, and ultimately, how efficiently a company operates. By choosing the right manufacturing strategy, businesses can optimize their supply chain, meet customer demands, and drive profitability.
Factors to Consider
Consider factors like market volatility, product characteristics, and customer preferences. Assessing demand variability, lead times, and production capabilities will also help determine the most suitable manufacturing strategy.
Market volatility refers to the degree of uncertainty and fluctuations in the market. It is important to consider this factor because it can greatly impact the demand for products. For example, in a highly volatile market, a push manufacturing strategy may be more appropriate as it allows for a faster response to sudden changes in demand.
Product characteristics also play a significant role in choosing the right manufacturing strategy. Complex products with high customization requirements may benefit from a pull manufacturing strategy, as it allows for greater flexibility and customization. On the other hand, products with standardized features and high demand may be better suited for a push manufacturing strategy.
Customer preferences should not be overlooked when deciding on a manufacturing strategy. Understanding what customers value and how they prefer to receive products can help determine the most effective approach. For instance, if customers value quick delivery and customization, a pull manufacturing strategy that focuses on just-in-time production may be the best choice.
Impact on Supply Chain Efficiency
Push and pull strategies have different implications for supply chain efficiency. Push manufacturing can result in increased inventory and lead times, while pull manufacturing seeks to minimize both. Analyze the strengths and weaknesses of your supply chain and evaluate how each strategy aligns with your goals.
Push manufacturing involves producing goods based on forecasts and pushing them through the supply chain to meet anticipated demand. While this strategy can help ensure product availability, it can also lead to excess inventory and longer lead times. On the other hand, pull manufacturing relies on actual customer demand to trigger production, reducing the risk of excess inventory and minimizing lead times.
Assessing the efficiency of your supply chain is crucial when deciding between push and pull manufacturing strategies. Consider factors such as transportation costs, warehousing capabilities, and supplier relationships. A well-optimized supply chain can support a pull manufacturing strategy by enabling quick response times and minimizing waste.
Role in Business Growth and Profitability
Understanding the impact of manufacturing strategy on overall business growth and profitability is crucial. Consider how each strategy affects production costs, customer satisfaction, and competitiveness in the marketplace.
Production costs are a significant consideration when choosing a manufacturing strategy. Push manufacturing may require higher upfront investments in inventory and production capacity, while pull manufacturing can result in lower inventory costs but higher setup and changeover costs. Analyze your cost structure and evaluate which strategy aligns with your financial goals.
Customer satisfaction is another important factor to consider. A manufacturing strategy that enables quick response times, customization, and on-time delivery can greatly enhance customer satisfaction. By meeting customer demands effectively, businesses can build strong relationships and gain a competitive edge in the marketplace.
Competitiveness in the marketplace is closely tied to the chosen manufacturing strategy. Understanding how each strategy aligns with your competitors' approaches can help you differentiate yourself and stand out. Consider factors such as speed to market, product quality, and flexibility when evaluating the impact on competitiveness.
Choosing between push and pull manufacturing strategies is an important decision that can significantly impact a company's operations. By thoroughly evaluating their respective advantages, disadvantages, and suitability for specific contexts, businesses can enhance supply chain efficiency, meet customer demands, and ultimately drive profitability.
Article
Comparing Push and Pull Manufacturing Strategies
•
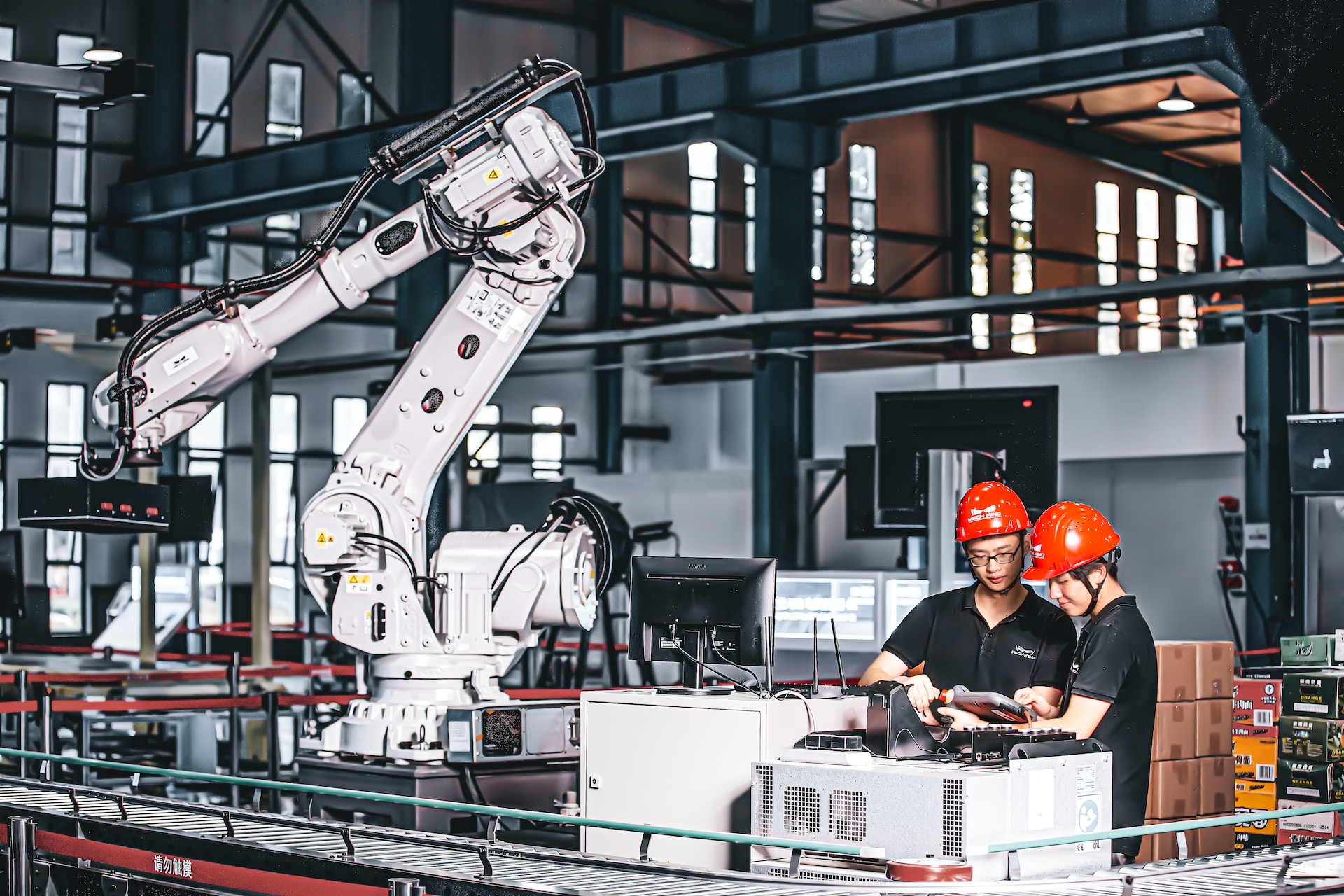