Article
How to Write SOP for Equipment: A Step-by-Step Guide
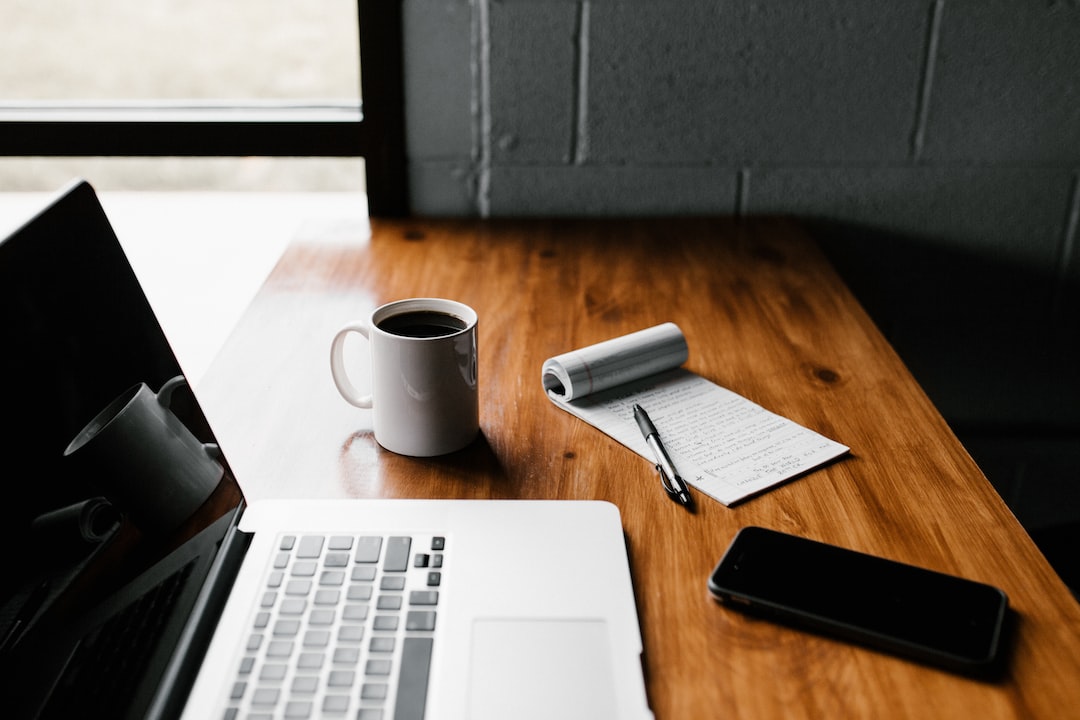
Learning how to write SOP for equipment that is efficient and effective is a must-have for any business leader striving to ensure their organization's success. But what does it take to write Standard Operating Procedures for equipment that's both efficient and effective?
In this blog post, we'll explore how to create comprehensive SOP documentation from scratch, implement it in your organization with ease, and leverage technology to streamline the process. From understanding best practices around to create SOPs through leveraging automation tools — figuring out how to write SOP for equipment doesn't have to be complicated or time-consuming.
How to Write SOP for Equipment
Having a clearly-defined SOP for managing equipment is key to ensuring proper use and maintenance, as well as having an accessible guide for troubleshooting any issues. A comprehensive SOP ensures that everyone involved understands the proper use and maintenance of equipment while also providing an easy reference guide for troubleshooting any issues that may arise.
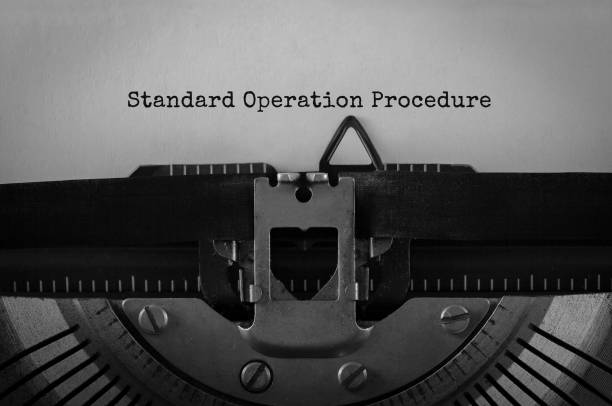
Defining the Scope of the SOP
The scope of your Standard Operating Procedures should include all relevant information related to your company’s specific equipment, including its purpose, usage guidelines, safety protocols, storage requirements, and repair/replacement procedures. This aids in guaranteeing that personnel are given the right instruction on how to use each apparatus securely and productively.
Identifying the key personnel responsible for equipment management is a must when developing SOPs. Depending on the size and complexity of your organization's operations, appointing a manager or team leader to oversee the implementation and address any questions or concerns from staff members regarding their usage of specific pieces of equipment may be necessary.
An SOP for Equipment can be set up by businesses to guarantee that all staff is aware of the same protocols concerning equipment control. Creating helpful SOP formats necessitates crafting clear and succinct directions, as well as adding visuals, checklists, and forms.
Creating an Effective SOP Document
Writing clear and concise instructions is key when creating an effective SOP document. It’s important to make sure that the language used is straightforward and easy to understand, so it should be written in plain English with minimal technical jargon.
When possible, provide examples or visual aids such as diagrams or flowcharts to help illustrate the process more clearly. Additionally, break up large blocks of text into smaller chunks for easier comprehension.
Utilizing visual aids can be a great way to clarify instructions within your SOP document. Diagrams are especially helpful when explaining complicated processes or procedures that involve multiple steps; they provide a quick overview of what needs to happen and how each step connects together.
Flowcharts are also useful for outlining sequential tasks while highlighting any decision points along the way. Additionally, visuals such as screenshots may be included to illustrate how something appears onscreen (e.g., when filling out a web-based form).
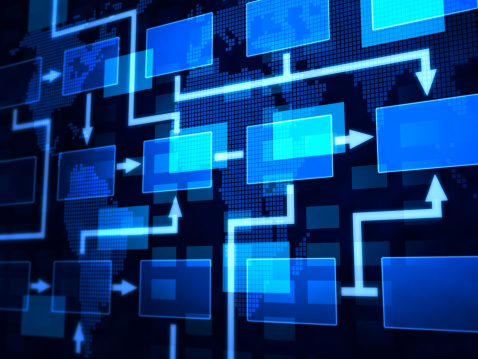
Incorporating checklists and forms into your SOP document will help ensure that employees follow all necessary steps during their workflows without missing anything important. Checklists should list out all required tasks in order of completion so users know exactly what needs doing before moving on to the next item on the list; this helps reduce errors due to human oversight or forgetfulness. Forms should include fields for collecting relevant information such as employee details, job descriptions, etc.; these can then be used later for tracking purposes or other reporting requirements (e.g., payroll processing).
Creating an effective SOP document is essential for any organization to ensure that equipment use and maintenance are performed safely and efficiently. To ensure compliance with the SOP, it's important to implement measures such as training employees on proper equipment use and maintenance, establishing accountability measures for adherence, and developing an ongoing evaluation system.
Implementing the SOP in Your Organization
Training employees on proper equipment use and maintenance is key to the successful implementation of a Standard Operating Procedure (SOP). It is essential that personnel understand their duties in terms of using, preserving, and storing equipment.
To do this, organizations should provide comprehensive training sessions that cover topics such as safety protocols, handling procedures, preventive maintenance techniques, and troubleshooting tips. Additionally, it’s wise to include refresher courses every few months or after any significant changes have been made to the SOP.
Establishing accountability measures for adherence to the SOP is essential for ensuring its effectiveness. Each employee should understand their role in relation to the SOP so they know what they need to do when something goes wrong or when there’s an issue with a particular piece of equipment. Additionally, organizations should consider implementing a system where employees must sign off on certain tasks before being allowed access or use of certain pieces of equipment.
Finally, developing an ongoing evaluation system is necessary for monitoring compliance with the SOP over time. Organizations should track usage data from each piece of equipment and review it regularly for signs that something isn’t functioning properly or needs attention due to excessive wear and tear from misuse or improper care.
By tracking usage data from each piece of equipment and reviewing it regularly, organizations can identify areas that require additional training or may lead to costly repairs due to improper use. Companies can ensure their employees are adhering closely to established guidelines while also avoiding unnecessary costs associated with poor management practices by having an effective evaluation process in place.
By establishing accountability measures and developing an ongoing evaluation system to monitor compliance with the SOP, organizations can ensure that their equipment is being used properly. Leveraging technology can streamline these processes even further by automating documentation and reporting requirements, integrating digital tools into existing workflows and systems, as well as utilizing mobile apps for remote accessibility.
Leveraging Technology to Streamline Your SOP Processes
The incorporation of tech into SOP writing processes is an invaluable aid for any small-to-medium-sized enterprise. By automating documentation and reporting requirements with software solutions, integrating digital tools into existing workflows and systems, and utilizing mobile apps to facilitate remote accessibility, businesses can maximize efficiency while ensuring compliance with all applicable regulations.
When it comes to automating documentation and reporting requirements, the right software solution can make a world of difference. From tracking employee hours to managing inventory levels, having access to real-time data makes it easier than ever before for entrepreneurs and managers alike to stay on top of their operations. Customizable dashboards can be provided with such software, enabling users to quickly pinpoint any potential areas that need betterment for optimal functioning.
Integrating digital tools into existing workflows is another way businesses can leverage technology in order to achieve maximum efficiency when learning how to write SOP for equipment and implementing them.
By using cloud-based platforms like Google Drive or Dropbox Paper, teams are able to collaborate more effectively by sharing documents securely across multiple devices from anywhere at any time – making sure everyone has access to up-to-date information regardless of location or time zone differences.
This type of integration also helps reduce manual paperwork which allows employees more time to focus on other tasks that require greater attention such as training new hires or troubleshooting customer service issues.
FAQs in Relation to How to Write Sop for Equipment
How to Write Sop for Equipment Effectively?
Creating a Standard Operating Procedure (SOP) for equipment involves outlining the steps and processes necessary to ensure the safe, efficient use of any type of machinery or device. The SOP should include details on how to properly set up and operate the equipment, as well as safety protocols in case of malfunction.
Moreover, a strategy should be outlined for preserving the device's performance over time by outlining maintenance and storage instructions. Finally, all users should be trained on the proper usage of this equipment according to its specific SOP before they are allowed access.
What is SOP for equipment?
SOPs are important for ensuring the safety of personnel when using equipment by detailing how to use it correctly and outlining precautionary measures. They also include details on maintenance schedules, cleaning procedures, storage requirements, troubleshooting tips and other important information related to its proper functioning. SOPs are essential for ensuring safe and efficient operations.
How do you effectively write SOPs?
Creating SOPs that are effective necessitates providing succinct, easy-to-follow directives. Start by outlining the procedure step-by-step, ensuring each task is explained in detail with a logical order of operations.
Include visuals or diagrams if needed for clarification and use language that is easily understood by all users. Finally, be sure to test the SOP prior to implementation and revise it as necessary for accuracy.
Conclusion
In conclusion, a Standard Operating Procedure (SOP) for equipment is an essential document that should be implemented in any organization. By knowing how to write SOP for equipment effectively and leveraging technology to streamline the process, businesses can ensure their equipment remains safe and efficient while helping them save time and money. Writing an SOP for your business's specific needs may seem daunting at first but with the right guidance it can be done quickly and easily - so don't delay — start writing SOP for equipment today.
Sign up now for a free 7-day trial with Trainual and scale your business!
Similar Blog Posts
Article
How to Write SOP for Equipment: A Step-by-Step Guide
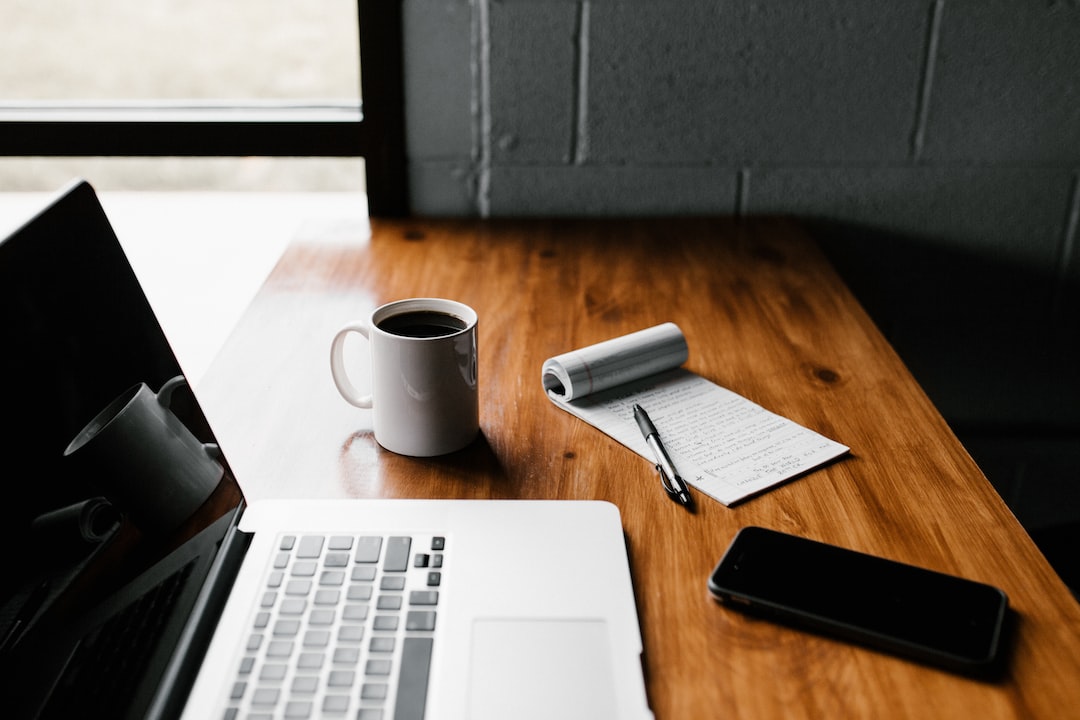
Learning how to write SOP for equipment that is efficient and effective is a must-have for any business leader striving to ensure their organization's success. But what does it take to write Standard Operating Procedures for equipment that's both efficient and effective?
In this blog post, we'll explore how to create comprehensive SOP documentation from scratch, implement it in your organization with ease, and leverage technology to streamline the process. From understanding best practices around to create SOPs through leveraging automation tools — figuring out how to write SOP for equipment doesn't have to be complicated or time-consuming.
How to Write SOP for Equipment
Having a clearly-defined SOP for managing equipment is key to ensuring proper use and maintenance, as well as having an accessible guide for troubleshooting any issues. A comprehensive SOP ensures that everyone involved understands the proper use and maintenance of equipment while also providing an easy reference guide for troubleshooting any issues that may arise.
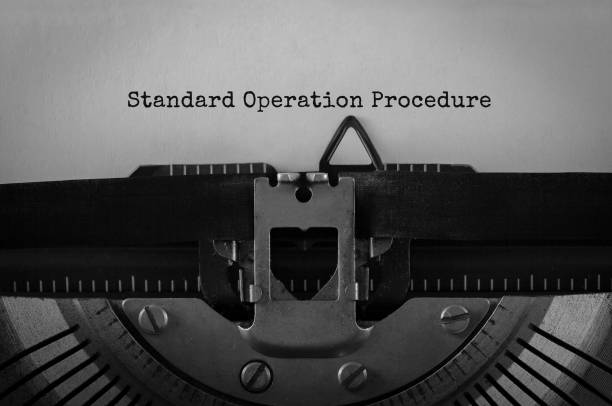
Defining the Scope of the SOP
The scope of your Standard Operating Procedures should include all relevant information related to your company’s specific equipment, including its purpose, usage guidelines, safety protocols, storage requirements, and repair/replacement procedures. This aids in guaranteeing that personnel are given the right instruction on how to use each apparatus securely and productively.
Identifying the key personnel responsible for equipment management is a must when developing SOPs. Depending on the size and complexity of your organization's operations, appointing a manager or team leader to oversee the implementation and address any questions or concerns from staff members regarding their usage of specific pieces of equipment may be necessary.
An SOP for Equipment can be set up by businesses to guarantee that all staff is aware of the same protocols concerning equipment control. Creating helpful SOP formats necessitates crafting clear and succinct directions, as well as adding visuals, checklists, and forms.
Creating an Effective SOP Document
Writing clear and concise instructions is key when creating an effective SOP document. It’s important to make sure that the language used is straightforward and easy to understand, so it should be written in plain English with minimal technical jargon.
When possible, provide examples or visual aids such as diagrams or flowcharts to help illustrate the process more clearly. Additionally, break up large blocks of text into smaller chunks for easier comprehension.
Utilizing visual aids can be a great way to clarify instructions within your SOP document. Diagrams are especially helpful when explaining complicated processes or procedures that involve multiple steps; they provide a quick overview of what needs to happen and how each step connects together.
Flowcharts are also useful for outlining sequential tasks while highlighting any decision points along the way. Additionally, visuals such as screenshots may be included to illustrate how something appears onscreen (e.g., when filling out a web-based form).
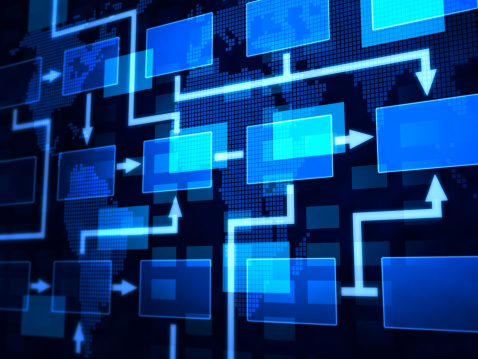
Incorporating checklists and forms into your SOP document will help ensure that employees follow all necessary steps during their workflows without missing anything important. Checklists should list out all required tasks in order of completion so users know exactly what needs doing before moving on to the next item on the list; this helps reduce errors due to human oversight or forgetfulness. Forms should include fields for collecting relevant information such as employee details, job descriptions, etc.; these can then be used later for tracking purposes or other reporting requirements (e.g., payroll processing).
Creating an effective SOP document is essential for any organization to ensure that equipment use and maintenance are performed safely and efficiently. To ensure compliance with the SOP, it's important to implement measures such as training employees on proper equipment use and maintenance, establishing accountability measures for adherence, and developing an ongoing evaluation system.
Implementing the SOP in Your Organization
Training employees on proper equipment use and maintenance is key to the successful implementation of a Standard Operating Procedure (SOP). It is essential that personnel understand their duties in terms of using, preserving, and storing equipment.
To do this, organizations should provide comprehensive training sessions that cover topics such as safety protocols, handling procedures, preventive maintenance techniques, and troubleshooting tips. Additionally, it’s wise to include refresher courses every few months or after any significant changes have been made to the SOP.
Establishing accountability measures for adherence to the SOP is essential for ensuring its effectiveness. Each employee should understand their role in relation to the SOP so they know what they need to do when something goes wrong or when there’s an issue with a particular piece of equipment. Additionally, organizations should consider implementing a system where employees must sign off on certain tasks before being allowed access or use of certain pieces of equipment.
Finally, developing an ongoing evaluation system is necessary for monitoring compliance with the SOP over time. Organizations should track usage data from each piece of equipment and review it regularly for signs that something isn’t functioning properly or needs attention due to excessive wear and tear from misuse or improper care.
By tracking usage data from each piece of equipment and reviewing it regularly, organizations can identify areas that require additional training or may lead to costly repairs due to improper use. Companies can ensure their employees are adhering closely to established guidelines while also avoiding unnecessary costs associated with poor management practices by having an effective evaluation process in place.
By establishing accountability measures and developing an ongoing evaluation system to monitor compliance with the SOP, organizations can ensure that their equipment is being used properly. Leveraging technology can streamline these processes even further by automating documentation and reporting requirements, integrating digital tools into existing workflows and systems, as well as utilizing mobile apps for remote accessibility.
Leveraging Technology to Streamline Your SOP Processes
The incorporation of tech into SOP writing processes is an invaluable aid for any small-to-medium-sized enterprise. By automating documentation and reporting requirements with software solutions, integrating digital tools into existing workflows and systems, and utilizing mobile apps to facilitate remote accessibility, businesses can maximize efficiency while ensuring compliance with all applicable regulations.
When it comes to automating documentation and reporting requirements, the right software solution can make a world of difference. From tracking employee hours to managing inventory levels, having access to real-time data makes it easier than ever before for entrepreneurs and managers alike to stay on top of their operations. Customizable dashboards can be provided with such software, enabling users to quickly pinpoint any potential areas that need betterment for optimal functioning.
Integrating digital tools into existing workflows is another way businesses can leverage technology in order to achieve maximum efficiency when learning how to write SOP for equipment and implementing them.
By using cloud-based platforms like Google Drive or Dropbox Paper, teams are able to collaborate more effectively by sharing documents securely across multiple devices from anywhere at any time – making sure everyone has access to up-to-date information regardless of location or time zone differences.
This type of integration also helps reduce manual paperwork which allows employees more time to focus on other tasks that require greater attention such as training new hires or troubleshooting customer service issues.
FAQs in Relation to How to Write Sop for Equipment
How to Write Sop for Equipment Effectively?
Creating a Standard Operating Procedure (SOP) for equipment involves outlining the steps and processes necessary to ensure the safe, efficient use of any type of machinery or device. The SOP should include details on how to properly set up and operate the equipment, as well as safety protocols in case of malfunction.
Moreover, a strategy should be outlined for preserving the device's performance over time by outlining maintenance and storage instructions. Finally, all users should be trained on the proper usage of this equipment according to its specific SOP before they are allowed access.
What is SOP for equipment?
SOPs are important for ensuring the safety of personnel when using equipment by detailing how to use it correctly and outlining precautionary measures. They also include details on maintenance schedules, cleaning procedures, storage requirements, troubleshooting tips and other important information related to its proper functioning. SOPs are essential for ensuring safe and efficient operations.
How do you effectively write SOPs?
Creating SOPs that are effective necessitates providing succinct, easy-to-follow directives. Start by outlining the procedure step-by-step, ensuring each task is explained in detail with a logical order of operations.
Include visuals or diagrams if needed for clarification and use language that is easily understood by all users. Finally, be sure to test the SOP prior to implementation and revise it as necessary for accuracy.
Conclusion
In conclusion, a Standard Operating Procedure (SOP) for equipment is an essential document that should be implemented in any organization. By knowing how to write SOP for equipment effectively and leveraging technology to streamline the process, businesses can ensure their equipment remains safe and efficient while helping them save time and money. Writing an SOP for your business's specific needs may seem daunting at first but with the right guidance it can be done quickly and easily - so don't delay — start writing SOP for equipment today.
Sign up now for a free 7-day trial with Trainual and scale your business!
Article
How to Write SOP for Equipment: A Step-by-Step Guide
•
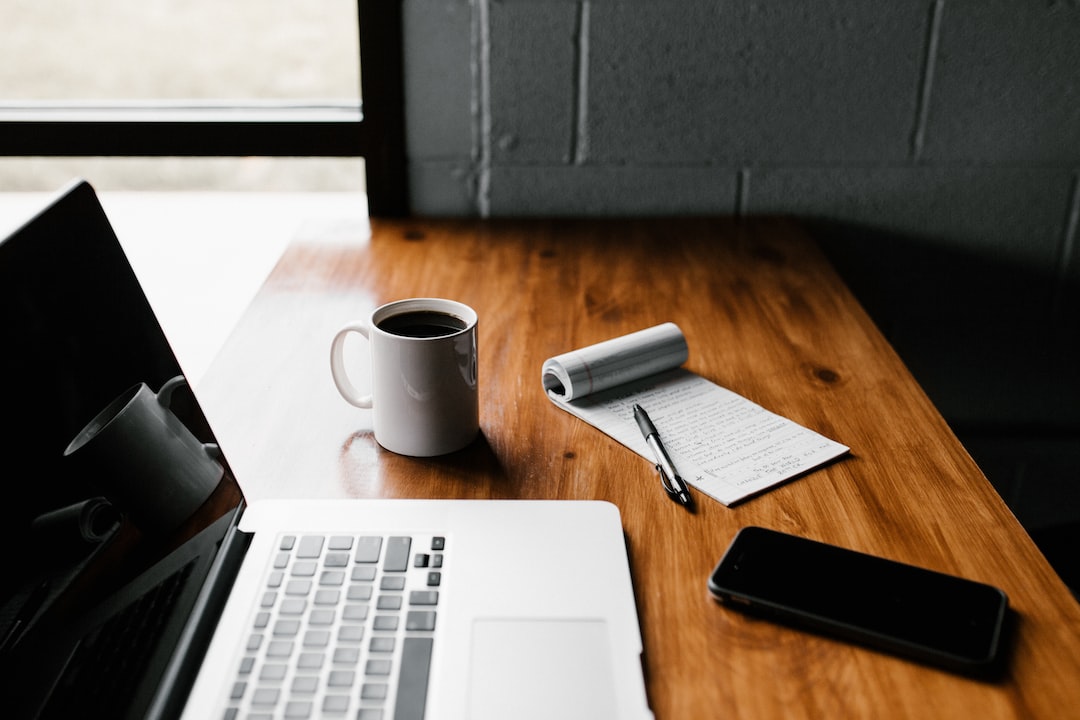