Article
Safety First: How Do You Measure Safety in the Workplace
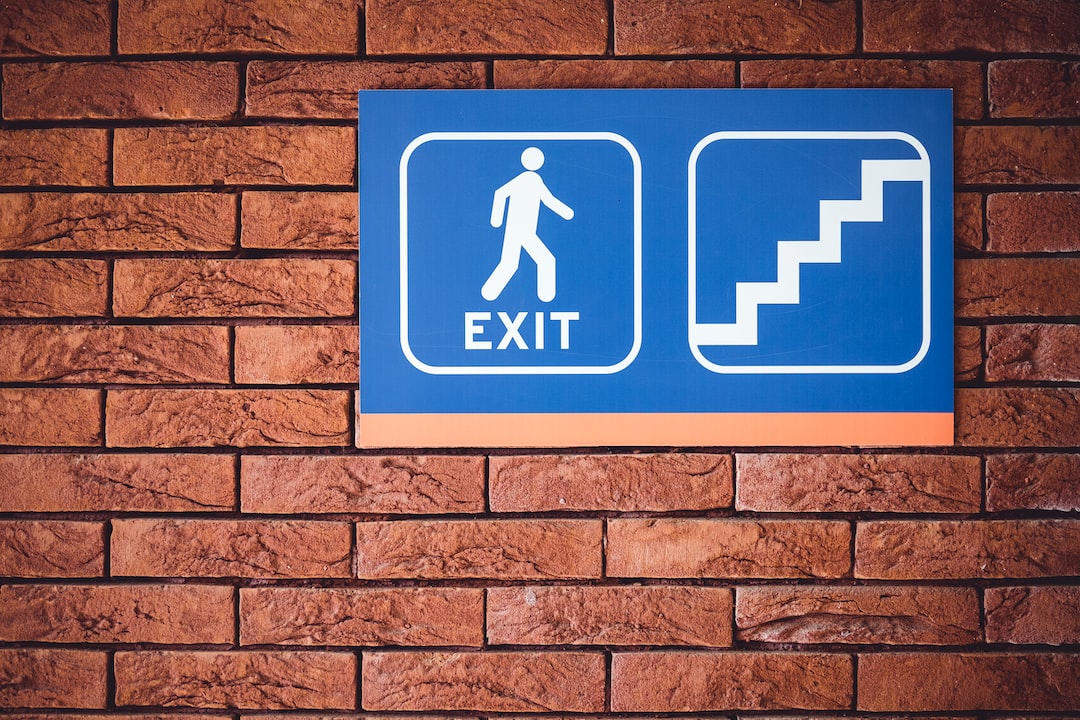
How do you measure safety in the workplace? Safety is an essential part of any successful business, yet it can be hard to quantify.
In this blog post, we'll explore why measuring safety should be on every entrepreneur's radar — from creating a safe work environment to leveraging technology for accurate measurement — so you can ensure your employees are as safe as possible while at work.
So how do you measure safety in the workplace? Let’s find out.
The Importance of Measuring Safety Performance in the Workplace
Knowing how to measure workplace safety performance can help businesses increase their efficiency and reduce their operating costs. By implementing safety protocols and procedures, companies can ensure that they are following all necessary regulations while also protecting their workers from potential harm. This will not only improve employee morale but also result in fewer sick days due to injury or illness caused by unsafe working conditions.
Furthermore, measuring a company’s safety performance can prevent costly lawsuits resulting from negligence or lack of proper training which could potentially bankrupt a business.
What Happens If You Don't Measure Safety Performance?
Failing to measure safety in the workplace puts both employers and employees at risk of serious injury or even death due to hazardous conditions.
In addition, not measuring safety increases the likelihood of expensive fines being levied against businesses that fail to comply with local laws regarding health and safety standards in the workplace.
So how do you measure safety in the workplace?
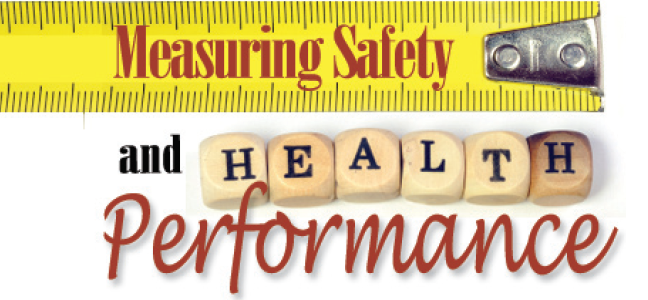
Creating a Safe Work Environment
Creating a safe work environment is essential for any business. Establishing clear policies and procedures is the first step in creating an effective safety protocol. Policies should be tailored to each business’s unique needs, taking into account their size, industry, and specific hazards that may exist in the workplace.
It’s important to make sure all employees are aware of these policies and understand them thoroughly.
Implementing training programs and resources is also key when it comes to promoting safety in the workplace. Training should include topics such as proper use of equipment, how to handle hazardous materials safely, emergency protocols, etc., depending on the type of work being done at your company.
Additionally, providing employees with access to additional resources like safety manuals or videos can help ensure everyone knows what steps need to be taken if something goes wrong.
How Do You Measure Safety in the Workplace?
Safety professionals are highly trained in analyzing safety issues. How do you measure safety in the workplace?
1. Centralize and Cleanse Your Data
Data is the foundation of any successful safety analytics program. To get started, you must first identify and collect all unused data in a single system, and ensure it is “clean” — meaning it’s complete and accurate. This includes both qualitative (e.g., incident reports) and quantitative (e.g., hazard exposure rates) data sources that are relevant to your organization’s safety performance goals.
Once you have collected this data, use business intelligence tools to visualize trends over time or compare different locations or teams within your organization. These visualizations can help you quickly identify potential risks impacting workplace safety so you can plan targeted interventions accordingly.
In addition to helping with risk identification, these tools also provide insights into how well current safety programs are working by providing key safety metrics such as near-misses per month or average time between incidents. This information can be used to evaluate the effectiveness of safety initiatives while allowing organizations to prioritize areas where more attention may be needed.
Finally, don't forget about the importance of integrating employee feedback into your analytics program. Surveys are an excellent way to gain insight into what employees think about your safety program from a health and safety perspective — something that cannot always be captured through traditional metrics alone.
2. Integrate Information
Data integration is the key to unlocking a comprehensive view of your safety program. By connecting information from different sources, you can start to build a picture of how all the pieces fit together and where potential risks may lie.
Integrating data from equipment maintenance systems can provide valuable insights into how well machinery is being maintained and serviced. This helps identify any issues before they become major problems, reducing downtime and improving efficiency.
Connecting enterprise resource planning (ERP) systems with EHS data gives you an overview of employee performance in relation to health and safety standards. It also allows for better tracking of safety training programs, ensuring that everyone has received appropriate instruction on safe working practices.
Third-party information such as weather reports can be used to help predict when hazardous conditions are likely to occur so that extra precautions can be taken ahead of time. Knowing what’s coming means you’re better prepared for whatever Mother Nature throws at you.
By combining all this data together, it becomes possible to use predictive modeling techniques which compare leading indicators against lagging ones in order to anticipate future outcomes. With this kind of insight at your fingertips, businesses will have the power to make smarter decisions about their operations and ensure greater levels of safety throughout their organization
3. Identify Metrics
When it comes to measuring safety performance, the key is to identify metrics that will provide you with an accurate representation of how your organization is performing. The best practice is to dedicate 60% of the key performance indicators (KPIs) to this function. Data points you can measure include employee engagement and satisfaction surveys, incident rates, near-miss reports, safety training completion rates, safety audits, and corrective action plans.
The next 30% should be dedicated to understanding how well employees are following procedures and policies related to safety protocols. This could include tracking compliance with PPE requirements or observing behaviors in hazardous areas such as machine shops or chemical storage rooms.
Finally, 10% of KPIs should focus on determining whether employees have a positive attitude toward safety culture by asking questions about their level of comfort in reporting incidents or participating in safety meetings.
By monitoring these data points regularly, you’ll gain insight into where your organization stands when it comes to creating a safe work environment for everyone involved.
Leveraging Technology for Improved Safety Culture
Technology has revolutionized the way businesses measure safety in the workplace. Automating processes with software solutions can help streamline operations and ensure compliance with regulations.
By integrating wearable devices, employers can monitor employee performance in real time and make adjustments to improve safety outcomes.
Artificial intelligence (AI) is also being used for predictive analysis, allowing companies to anticipate potential risks before they occur.
Automating Processes with Software Solutions
Businesses are increasingly turning to software solutions such as enterprise resource planning (ERP) systems or custom applications to automate their safety measurement processes. These tools allow organizations to track data more accurately and efficiently while ensuring compliance with industry standards and government regulations. Additionally, these solutions often come equipped with reporting capabilities that provide insight into key performance indicators (KPIs).
Integrating Wearable Devices to Measure Health and Safety
Wearable technology is becoming a popular tool to measure improved safety performance. Employers can use wearables such as smartwatches or fitness trackers to monitor employees’ activity levels throughout the day and identify any potential risks associated with fatigue or overwork. This data can then be used to adjust schedules or implement additional training programs if needed.
Utilizing Artificial Intelligence for Predictive Analysis
AI-powered analytics are helping businesses stay ahead of potential risks by providing insights into future trends based on past behavior patterns. Companies can use this information to create proactive strategies that address issues before they become problems, resulting in improved overall safety outcomes across all areas of operation.
By leveraging technology, businesses have access to more accurate data to achieve their goal of improved safety performance.
Conclusion
How do you measure safety in the workplace? By understanding the importance of safety, creating a safe work environment, measuring safety, and leveraging technology for improved measurement, you can ensure that your business is doing its part to protect employees and customers alike.
Are you an entrepreneur, founder, manager, or operational leader looking to reduce safety incidents in your workplace? Trainual is the perfect solution for you! With our comprehensive documentation of processes and policies, as well as superior onboarding and offboarding experiences, we make it easy for business owners to maintain a safe environment.
Don't let unsafe practices take away from productivity — get on board with Trainual today!
Article
Safety First: How Do You Measure Safety in the Workplace
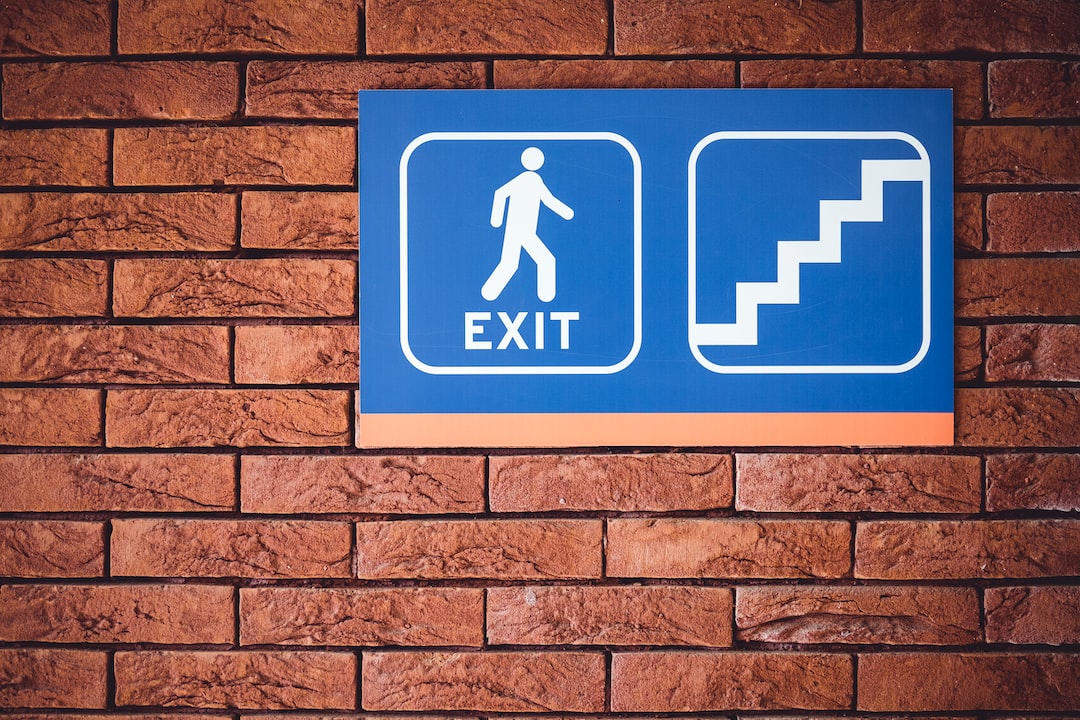
How do you measure safety in the workplace? Safety is an essential part of any successful business, yet it can be hard to quantify.
In this blog post, we'll explore why measuring safety should be on every entrepreneur's radar — from creating a safe work environment to leveraging technology for accurate measurement — so you can ensure your employees are as safe as possible while at work.
So how do you measure safety in the workplace? Let’s find out.
The Importance of Measuring Safety Performance in the Workplace
Knowing how to measure workplace safety performance can help businesses increase their efficiency and reduce their operating costs. By implementing safety protocols and procedures, companies can ensure that they are following all necessary regulations while also protecting their workers from potential harm. This will not only improve employee morale but also result in fewer sick days due to injury or illness caused by unsafe working conditions.
Furthermore, measuring a company’s safety performance can prevent costly lawsuits resulting from negligence or lack of proper training which could potentially bankrupt a business.
What Happens If You Don't Measure Safety Performance?
Failing to measure safety in the workplace puts both employers and employees at risk of serious injury or even death due to hazardous conditions.
In addition, not measuring safety increases the likelihood of expensive fines being levied against businesses that fail to comply with local laws regarding health and safety standards in the workplace.
So how do you measure safety in the workplace?
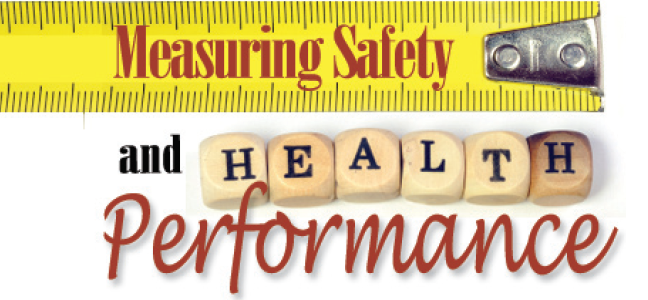
Creating a Safe Work Environment
Creating a safe work environment is essential for any business. Establishing clear policies and procedures is the first step in creating an effective safety protocol. Policies should be tailored to each business’s unique needs, taking into account their size, industry, and specific hazards that may exist in the workplace.
It’s important to make sure all employees are aware of these policies and understand them thoroughly.
Implementing training programs and resources is also key when it comes to promoting safety in the workplace. Training should include topics such as proper use of equipment, how to handle hazardous materials safely, emergency protocols, etc., depending on the type of work being done at your company.
Additionally, providing employees with access to additional resources like safety manuals or videos can help ensure everyone knows what steps need to be taken if something goes wrong.
How Do You Measure Safety in the Workplace?
Safety professionals are highly trained in analyzing safety issues. How do you measure safety in the workplace?
1. Centralize and Cleanse Your Data
Data is the foundation of any successful safety analytics program. To get started, you must first identify and collect all unused data in a single system, and ensure it is “clean” — meaning it’s complete and accurate. This includes both qualitative (e.g., incident reports) and quantitative (e.g., hazard exposure rates) data sources that are relevant to your organization’s safety performance goals.
Once you have collected this data, use business intelligence tools to visualize trends over time or compare different locations or teams within your organization. These visualizations can help you quickly identify potential risks impacting workplace safety so you can plan targeted interventions accordingly.
In addition to helping with risk identification, these tools also provide insights into how well current safety programs are working by providing key safety metrics such as near-misses per month or average time between incidents. This information can be used to evaluate the effectiveness of safety initiatives while allowing organizations to prioritize areas where more attention may be needed.
Finally, don't forget about the importance of integrating employee feedback into your analytics program. Surveys are an excellent way to gain insight into what employees think about your safety program from a health and safety perspective — something that cannot always be captured through traditional metrics alone.
2. Integrate Information
Data integration is the key to unlocking a comprehensive view of your safety program. By connecting information from different sources, you can start to build a picture of how all the pieces fit together and where potential risks may lie.
Integrating data from equipment maintenance systems can provide valuable insights into how well machinery is being maintained and serviced. This helps identify any issues before they become major problems, reducing downtime and improving efficiency.
Connecting enterprise resource planning (ERP) systems with EHS data gives you an overview of employee performance in relation to health and safety standards. It also allows for better tracking of safety training programs, ensuring that everyone has received appropriate instruction on safe working practices.
Third-party information such as weather reports can be used to help predict when hazardous conditions are likely to occur so that extra precautions can be taken ahead of time. Knowing what’s coming means you’re better prepared for whatever Mother Nature throws at you.
By combining all this data together, it becomes possible to use predictive modeling techniques which compare leading indicators against lagging ones in order to anticipate future outcomes. With this kind of insight at your fingertips, businesses will have the power to make smarter decisions about their operations and ensure greater levels of safety throughout their organization
3. Identify Metrics
When it comes to measuring safety performance, the key is to identify metrics that will provide you with an accurate representation of how your organization is performing. The best practice is to dedicate 60% of the key performance indicators (KPIs) to this function. Data points you can measure include employee engagement and satisfaction surveys, incident rates, near-miss reports, safety training completion rates, safety audits, and corrective action plans.
The next 30% should be dedicated to understanding how well employees are following procedures and policies related to safety protocols. This could include tracking compliance with PPE requirements or observing behaviors in hazardous areas such as machine shops or chemical storage rooms.
Finally, 10% of KPIs should focus on determining whether employees have a positive attitude toward safety culture by asking questions about their level of comfort in reporting incidents or participating in safety meetings.
By monitoring these data points regularly, you’ll gain insight into where your organization stands when it comes to creating a safe work environment for everyone involved.
Leveraging Technology for Improved Safety Culture
Technology has revolutionized the way businesses measure safety in the workplace. Automating processes with software solutions can help streamline operations and ensure compliance with regulations.
By integrating wearable devices, employers can monitor employee performance in real time and make adjustments to improve safety outcomes.
Artificial intelligence (AI) is also being used for predictive analysis, allowing companies to anticipate potential risks before they occur.
Automating Processes with Software Solutions
Businesses are increasingly turning to software solutions such as enterprise resource planning (ERP) systems or custom applications to automate their safety measurement processes. These tools allow organizations to track data more accurately and efficiently while ensuring compliance with industry standards and government regulations. Additionally, these solutions often come equipped with reporting capabilities that provide insight into key performance indicators (KPIs).
Integrating Wearable Devices to Measure Health and Safety
Wearable technology is becoming a popular tool to measure improved safety performance. Employers can use wearables such as smartwatches or fitness trackers to monitor employees’ activity levels throughout the day and identify any potential risks associated with fatigue or overwork. This data can then be used to adjust schedules or implement additional training programs if needed.
Utilizing Artificial Intelligence for Predictive Analysis
AI-powered analytics are helping businesses stay ahead of potential risks by providing insights into future trends based on past behavior patterns. Companies can use this information to create proactive strategies that address issues before they become problems, resulting in improved overall safety outcomes across all areas of operation.
By leveraging technology, businesses have access to more accurate data to achieve their goal of improved safety performance.
Conclusion
How do you measure safety in the workplace? By understanding the importance of safety, creating a safe work environment, measuring safety, and leveraging technology for improved measurement, you can ensure that your business is doing its part to protect employees and customers alike.
Are you an entrepreneur, founder, manager, or operational leader looking to reduce safety incidents in your workplace? Trainual is the perfect solution for you! With our comprehensive documentation of processes and policies, as well as superior onboarding and offboarding experiences, we make it easy for business owners to maintain a safe environment.
Don't let unsafe practices take away from productivity — get on board with Trainual today!
Article
Safety First: How Do You Measure Safety in the Workplace
•
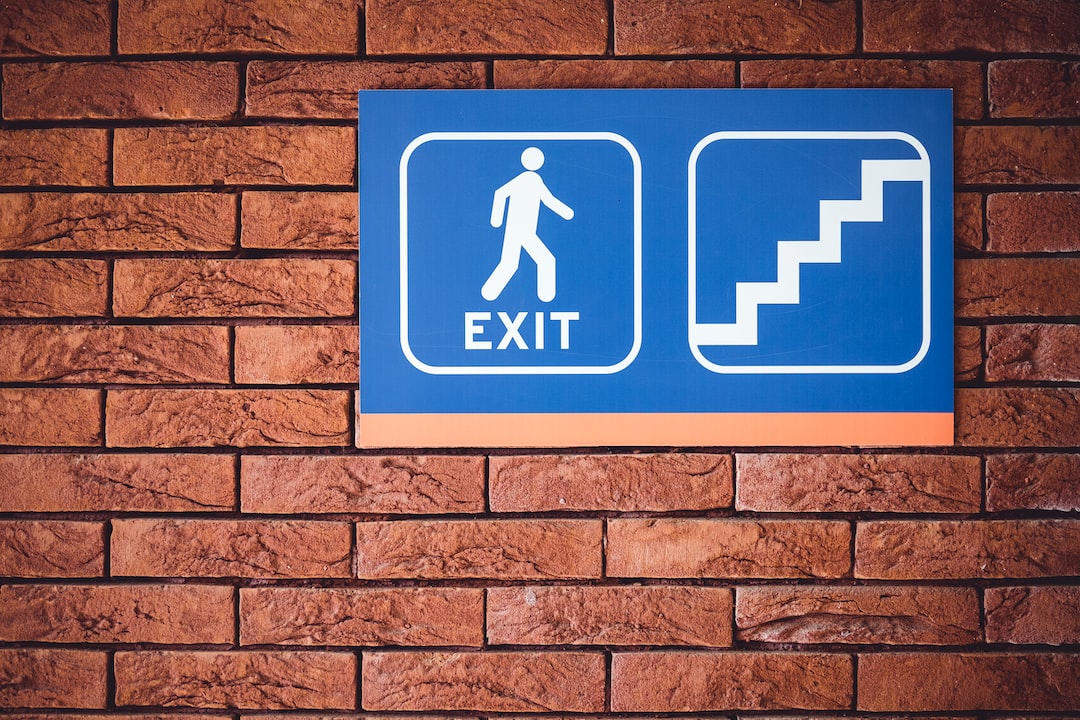